“Productivity” podcast series (Ep. #5): Intelligent Manufacturing – Delivering Quality Products Faster
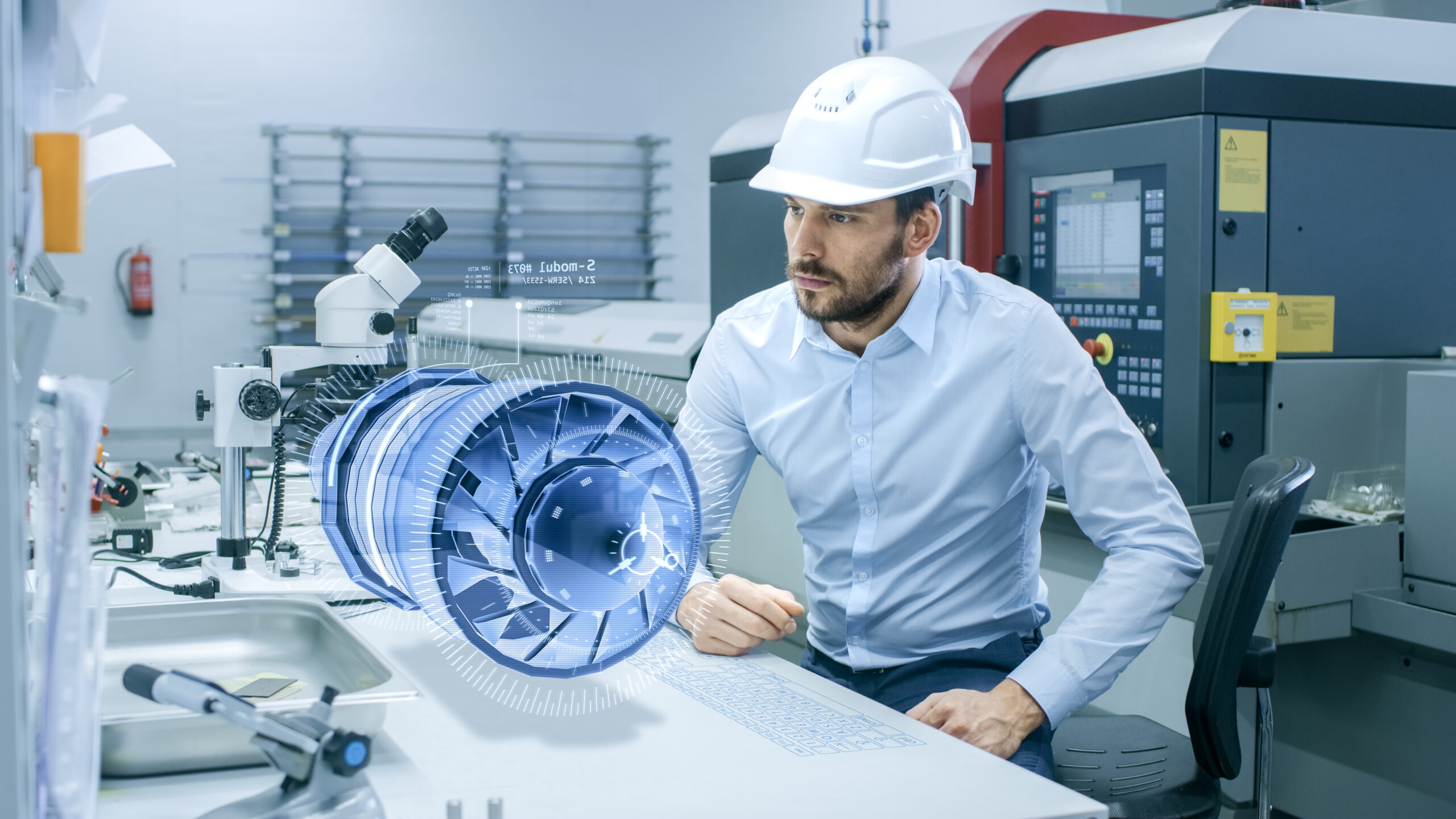
Quick… What comes to mind when you hear “Intelligent Manufacturing?” It’s a term with special meaning these days especially when you consider all the innovation that’s going on. You might think of the digital factory. And yes, you would be correct.
But really, it’s more about connecting the engineering world to the manufacturing world. It’s about using the comprehensive digital twin and tapping into a digital thread. It’s about introducing flexible automation into your process.
In this final podcast of the Talking Aerospace Today “Productivity” series, Dale Tutt and I discuss intelligent manufacturing and the important role it plays in both engineering and manufacturing. We’ll be discussing how to accelerate production ramp-up and how to deliver complex and more highly integrated quality products faster.
Listen to the podcast now.
This is episode #5 in a five-part series.
Welcome to Talking Aerospace Today – a podcast for the Aerospace and Defense industry. A place that brings the promise of tomorrow’s technology to the ears of our listeners today.
Everyone’s talking about the factory of the future as something that’s years away or a concept that needs to be realized, but the truth is – the factory of the future is here now because the technology of tomorrow exists today.
Today, in the final podcast of our “Productivity” series, we’ll be talking about intelligent manufacturing and how aerospace companies can be more productive throughout their engineering and manufacturing processes and ultimately deliver complex and highly integrated quality products faster. We’ll be talking about ways to accelerate production ramp-up using intelligent manufacturing and how to introduce flexible automation throughout the product lifecycle process.
I’m your host, Scott Salzwedel, and I hope you’ll join me and Dale Tutt, Vice President of Aerospace & Defense at Siemens Digital Industries Software, in our final episode of the series.
Learn the many ways intelligent manufacturing can assist aerospace companies involved in urban air mobility, electric propulsion, supersonic flight, or any of the other promising areas going on right now.
In this episode, you’ll learn:
- The common challenges manufacturers face today. (04:08)
- How manufacturing has changed in the traditional factory and what that means to the digital factory. (05:34)
- How companies can make the digital transition smoother. (09:04)
- The role Siemens plays when it comes to intelligent manufacturing. (11:02)
- A real-world example of how Siemens is helping customers today. (14:05)
Connect with Dale:
Connect with Scott:
For more information, please visit the Siemens Aerospace & Defense website.
Podcast transcript:
Scott Salzwedel: Hello, this is Talking Aerospace Today, a podcast for the Aerospace and Defense Industry. A place that brings the promise of tomorrow’s technology to the ears of our listeners today.
I’m your host, Scott Salzwedel. Welcome to our five-part series “Accelerating Productivity through Digital Transformation.” As you might imagine, maximizing productivity throughout the A&D product lifecycle is key to success and significant profits.
Today, in our final podcast, we’ll be discussing how to accelerate production ramp-up. Before we get started, to recap our last episode, we talked about program execution excellence – program management using a digital thread. If you missed it, I urge you to chase that one down.
In this podcast, we’re talking about ways to accelerate production ramp-up using intelligent manufacturing. Now, this is one area that’s evolving fast. We’re talking about advanced visualization using augmented and virtual realities, the digital factory and so much more.
So, let’s get started. I’m pleased to introduce my special guest, Dale Tutt, who is the Vice President of Aerospace and Defense at Siemens Digital Industries Software. Welcome Dale, thanks for stopping by to talk about productivity and the digital transformation in Aerospace and Defense. Before we dive in, could you please share with our listeners, your background, and your role at Siemens?
Dale Tutt: Hello, Scott. I’m very happy to be here, today. So, before I joined Siemens, I worked in the Aerospace and Defense industry for about 30 years in various engineering and program leadership roles. In my most recent position, I was the Vice President of Engineering at The Spaceship Company. We were working with Virgin Galactic in developing spaceships for commercial space tourism. Before that, I was at Textron Aviation or Cessna Aircraft Company for about 18 years, and a number of engineering and program management roles there, as well. In my last real big program, before I left there, I was the Chief Engineering Program Director for the Textron AirLand Scorpion Jet. We went from a concept sketch to first flight of an all-new tactical aircraft in about 23 months, which was pretty fast for the industry. And, before that, I had some time as well at Bombardier Learjet and General Dynamics Space Systems Division, so a mix of space and aircraft in my career. But now, at Siemens, I’m the Vice President of the Aerospace and Defense Industry. And we do a lot of the industry’s strategy development, and work on developing product solutions for the aerospace and defense industry and for our customers in the industry, so that we can provide solutions that meet our customer’s needs. So, I get to work with all of our product lines and our global sales teams, and it’s a lot of fun in this role.
Scott: Great… Thank you, Dale! Since this podcast series is on productivity, why don’t we first take a minute and discuss the many ways in which an OEM or a supplier can increase productivity?
Dale: The four main areas that we’ve been talking about are Model Based Systems Engineering (MBSE). Really, this ability to orchestrate your technical program and it’s a digital thread that connects a lot of these other engineering supply chain program management and manufacturing activities. We then talked a lot about accelerating product design and how companies can use digital thread in their PLM system to really support an agile product development process. The heart of all of it, I guess, sometimes, is improving program management with our Integrated Program Planning and Execution (IPP&E) solution. And today, we want to talk about accelerating your production ramp-up. And this will be a good story, a good discussion around intelligent manufacturing and flexible automation, and how a digital factory can really help a company ramp-up their production rate faster and deliver their product to their customers faster. So, it’s often where the rubber hits the road with a lot of these development programs.
Scott: Okay, so, accelerating production ramp-up through intelligent manufacturing. There are so many facets here: AR/VR, the digital factory, additive manufacturing, the IIoT – all of these, by themselves, or even better, working nicely together, can vastly improve A&D productivity. So, Dale, let’s begin by first discussing the common challenges manufacturers face today.
Dale: The manufacturing process is always kind of at the end of the process, and everything flows down to them. And so, they suffer from late design changes and it’s impacting their ability to produce a product. They’ve got to be able to bring in new materials and technologies and sometimes do it very quickly. I think one of the questions, especially when you’re setting up a new factory, or maybe you’re modifying an existing factory line, is how do you set it up to be the most efficient? You have so many moving parts bringing today’s complex aerospace products together. And the topic today is how do you incorporate automation into your production line while managing your investment? This is a big topic as companies look at more efficient ways of producing products. And then, finally, how do you deliver your final product? How can you verify that, with all of these customizations that might happen on your product that actually, your “as-built” matches your “as-designed,” as it’s coming off the production line? So, those are the big challenges a lot of these guys have to deal with.
Scott: How is manufacturing changing in the traditional factory?
Dale: As you look at a lot of their factories over the last 20 to 30 years, I was talking to a guy that was from one of the automotive companies where we were doing some benchmarking, when I was at Textron they were kind of surprised because they were used to seeing a lot of automation, and they were surprised at how much hand labor there still was in building a lot of airplanes. And this is 10 or 15 years ago. But they still use very conservative manufacturing concepts. Sometimes, the state of the art hasn’t changed that much. They still rely a lot on assembly labor to build these products. So, you have a lot of tooling associated with that, and you have a lot of people associated with it, and there’s a cost of training and making sure you keep your people safe in these assembly lines.
And really, you know, the cost of automation has been deemed to be too expensive. First of the production rate that a lot of these aerospace companies are asked for this. There’s always this trade-off of automation versus labor hours. So, as I was talking earlier, they’re using a lot of assembly labor but the challenge has been that automation has been seen as something for an automotive company because they might produce 300 to 400,000 cars a year and so, they can implement automation. But an airplane manufacturer might go, “Well, I’m going to produce 60 a year, so why would I want to invest all that money?” So, it’s been a challenge. And then, finally, there’s still a lot of paper processes out there. You see books traveling around with parts, and you see a lot of paper, and everything’s just kind of a paper trail. And sometimes it’s hard to keep track of it and brings the factory to a halt when there’s a part that shows up and there’s no piece of paper hanging off of it. So, it really does bring a lot of challenges to the factories today.
Scott: Yeah, it sounds like they still have a long way to go. Wow… But there’s the digital factory and we are seeing manufacturing changes in the digital factory as well.
Dale: We’re starting to see a lot of state-of-the-art manufacturing facilities bringing in some of this advanced technology. So, you want your factories to be smarter and more connected to bring that intelligence to the factory floor so that you can start to automate managing some of your process controls. You want it to be easy to adapt to these changes either changes in your product or maybe demand fluctuations. And so, there’s always a lot of demand to have different customization. Say you’re an aircraft manufacturer for commercial aircraft, each one coming off the line might be different; you have different customer demands. And you want to be more flexible to do that. But you also see today’s environment where you’re starting to see big changes in demand and how companies accommodate that.
You want to bring in flexible automation. How do you bring in automation smartly? And maybe, when I talk about flexible automation, sometimes you’re replacing tooling with some automation or with some robots, but because of the production rates, you’re not going to have a robot just sitting there doing the same thing over and over again. You maybe need to have that robot do four or five different things. And so, a different environment, additive manufacturing is changing how everyone is looking at building parts. I think in ten years, you’ll start to see this really come online. And then, finally, how do you present the information to the technicians so that you have advanced work instructions that can be on any device? You move away from paper, maybe you start moving into augmented reality.
Scott: So, Dale, how would our customers survive and even thrive in this kind of environment?
Dale: With the Xcelerator portfolio that really connects your engineering to your production and service environments, the key there is that having a digital twin that enables you to truly achieve this true concurrent engineering and be able to shift some of these processes to the left, so that you’re able to evaluate your manufacturing processes at the same time that you’re designing your products. And so, that brings that voice of manufacturing further to the left in your design processes. We’re seeing advanced automation where you can bring more automation, and more importantly, you can bring it faster into your factory line. You do this through your plant simulation, your simulation of your automation, and then you’re able to verify it with virtual commissioning. So, when you think about how much investment you make in tools and you make into your automation, and even just setting up a place and tens of millions or maybe $100 million, if you can utilize virtual commissioning, you can identify any issues early on and you can design those out early in the process. You don’t run into a problem when you are standing up your line doing the physical commissioning, you reduce the risk of changes that come out of there. And then, you’re able with the flexible, open environment, with our toolsets, with our full lifecycle management system, you’re able to incorporate new materials and technology faster because it’s easier to connect to it with this open environment. And then, really, with IoT, and all the tools that are now available, you’re able to leverage more data to close the loop on your production processes and provide insights into both how your product is designed and how your production process is designed, and really optimized. So we bring a lot of tools together to help companies make this digital transition into their factory.
Scott: Great! So yeah, that was going to be my next question: how specifically do we help our customers along the lines of intelligent manufacturing?
Dale: As I mentioned, and I’ll go into a little more detail, the comprehensive digital twin of your product and your production processes. And the key here is that the physical environment is going to be a clone of the virtual environment. So, you’ve designed everything in the virtual environment, and now the physical environment is really intended to be a clone of that. And, as I mentioned, it really helps you identify early identification of any design and tooling issues, again, before you start investing a lot of money in your manufacturing facility or even just committing to your product design. Something I didn’t mention about having the twin is really this ability to rapidly evaluate different concepts to how to build a part and how to understand the tradeoffs. This is really a key element of design for manufacturability and automation. And so, the ability to quickly look at these different concepts through good simulation you’re not building physical mockups, you’re doing this in the digital twin. It can really transform how you’re looking at your manufacturing processes, and it can help you go a lot faster and standing up your production line. We’re able to offer closed-loop manufacturing, so you’re connecting your PLM system to your MES or your Manufacturing Execution System. You’re managing this very complex aerospace and defense product with this full digital thread that connects from your engineering all the way into all of your manufacturing processes. And this improves your first-pass yield.
I mentioned flexible automation. So you can bring robots online faster, and be able to apply them and have them do more than one task. Plant simulations – as you start to layout a new factory, you’re looking at different configurations of your factory. You’re able to simulate all this. And then, as I mentioned, with virtual commissioning of your automation and your simulation, you get to test everything out and verify it. So, I think, really, as I said, we have this complete digital thread, it connects from the engineering all the way in your manufacturing. And then, you bring in your IoT as you have data coming off of your production line, your real production processes, you’re able to use those insights and improve your production processes with the digital twin and with the digital thread.
And then, finally, we’re starting to bring a lot more new technology in with advanced visualization, with augmented reality, and how you do work instructions, how you help with solid parts, how you locate parts. And then also virtual reality. It plays a role as you’re setting up your factory and looking at it at the beginning. So, a lot of aspects to intelligent manufacturing, a lot going on. I guess, if I would summarize it, it’s looking at the manufacturing environment, the tools, and processes that you’re using. It’s also looking at the people, how you empower the people that really interact now with this more digital environment.
Scott: It’d be great if you could give our listeners a real-world example of how Siemens is helping the customer right now, today.
Dale: I think it’s a really cool example… We are working with the NAVSEA Shipyards – such as Pearl Harbor – to build a digital twin of their maintenance operations for their aircraft carriers, submarines and surface ships. This digital twin will be used to evaluate new construction and modernization efforts at the shipyards as they are transforming to meet modern mission requirements. Basically, they apply simulation to quantify their investments and to evaluate the impact on their sustainment operations before breaking ground on a new project. We use a model to determine things like optimal travel routes for personnel and material or we look at new design alternatives for production facilities that support improving the maintenance of those vessels. We can also model constraints, such as cranes, that would be a potential bottleneck and consider how to optimize their usage and evaluate potential future placement of new cranes. Beyond current maintenance operations, the same digital twin will then be used in perpetuity to provide a digital representation for any process or facility modernizations in the future. People tend to think of a factory when you talk about manufacturing simulation. But when a large surface ship comes in for maintenance, you basically set the factory up around the whole ship. Simulation is playing a big role in improving these operations and the Navy is currently seeing a lot of benefits from these tools.
Scott: Well, that’s an interesting example. We’re nearing the end. And before we finish, I wanted to ask you the take-aways, what would you like to leave with our listeners?
Dale: Everyone talks about the factory of the future, and everyone’s always talking about the factory of the future it’s something way out in the future. But I’m going to tell you right now, you can set up your factory of the future today. When we talk about “Where today meets tomorrow” tomorrow’s technology is available today. And I look at it as also setting the foundation for where we’re headed in the future. When we talk about this simulation. When we’re talking about the automation. When we’re talking about how do we help the technicians be more productive? And how do we help them interact with the digital environment better? We’re really setting the stage for the future.
We can keep talking about the factory of the future, but a lot of that is available today and it’s the foundation for where we’re going. So, that’s the big thing. We really want to help your programs be on time, to execute them on time and on budget, and most importantly, while accelerating your production ramp-up. And then, I think, just the ability with this digital thread and with the information that’s available with a digital twin, the whole portfolio is able to help you capture and reuse your manufacturing best practices and knowledge and be more effective as you go forward.
Scott: Well, Dale, I’m sorry. But, once again, we’ve run out of time. But I do thank you for a wonderful discussion on intelligent manufacturing…
Dale: Yeah, no problem, Scott. And thanks again for having me. We really had a lot of fun talking about all these topics in this series. And manufacturing is always a great one to talk about, as well.
Scott: We’re honored to have you. Of course, I’d like to extend my many thanks to our listeners. I’m glad you tuned into this podcast. Thank you, listeners.
So this concludes our five-part series on A&D productivity. Please check out our previous episodes wherever you go to get your podcast downloads. And for more information, you can visit us online at siemens.com/PLM/AerospaceDefense.
This is Talking Aerospace Today and I hope you’ve enjoyed this five-part productivity series. Bye for now…
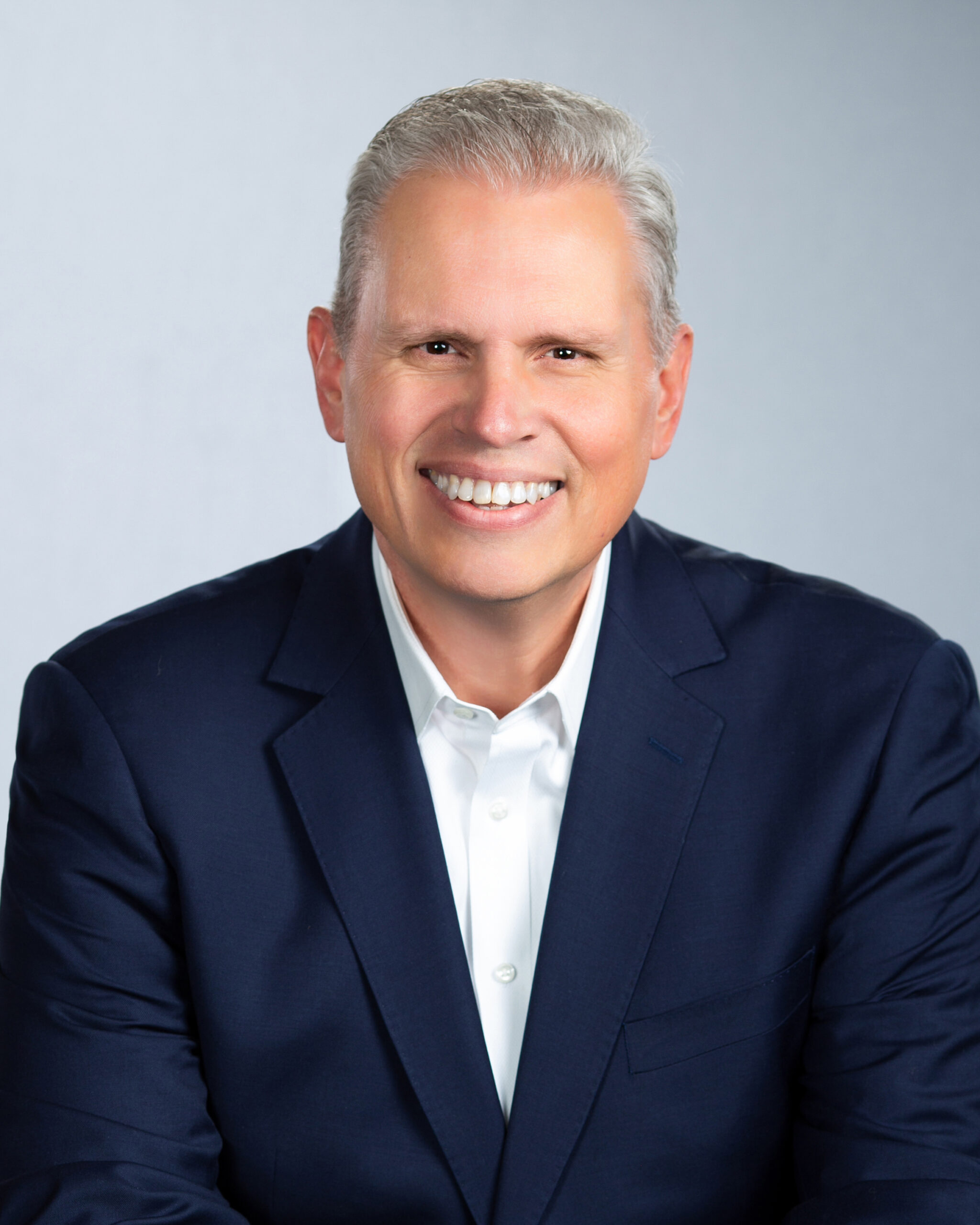
Dale Tutt – Vice President of Industry Strategy at Siemens Digital Industries Software
Dale Tutt is Vice President of Industry Strategy at Siemens Digital Industries Software. Dale leads a team of experts to develop and execute industry-specific product and marketing strategies in collaboration with the global product, sales, and business development teams. With over 5 years of experience in this role combined with extensive experience in the aerospace and defense industry, Dale has a deep understanding of the challenges and opportunities facing companies as they embark on their digital transformation journeys.
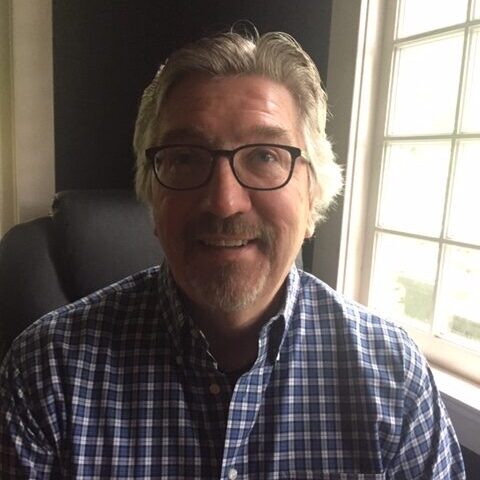
Scott Salzwedel – Host
Scott Salzwedel is senior technical writer and corporate communications writer involved in the Siemens Aerospace & Defense Industry and Siemens Capital. In addition to writer/host of Talking Aerospace Today, Scott is the writer of white papers, articles, blogs, videos and websites at Siemens.
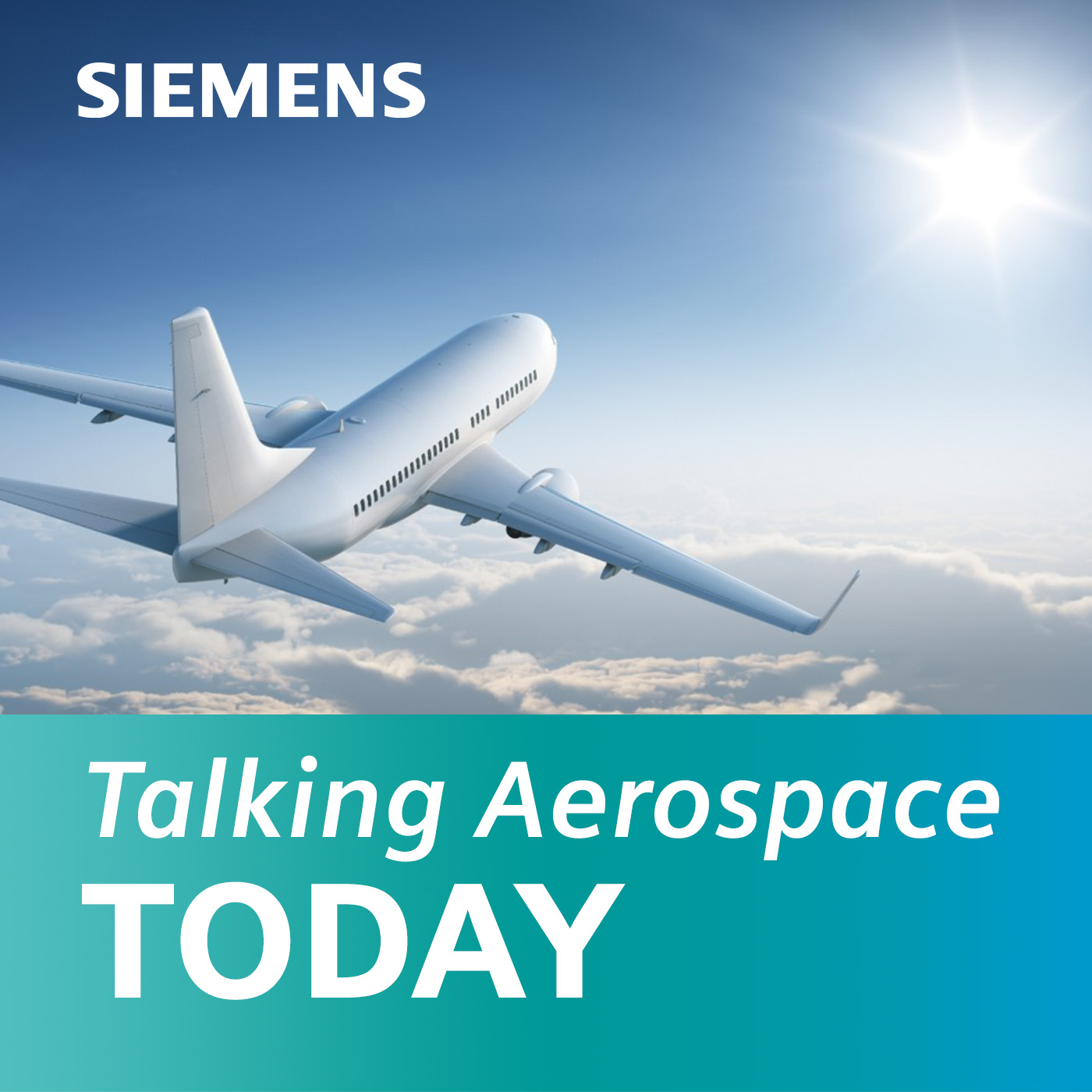
Talking Aerospace Today Podcast
The A&D Industry is at a serious inflection point. Transformation to the digital enterprise has opened up a new era in innovation and technological breakthroughs. However, complexity and compliance continue to hamper the best of efforts.
Join us as we explore how Siemens is turning complexity into a competitive advantage for many of our customers – today and well into tomorrow.