Podcast: “What it Takes to Build a Supersonic Aircraft”
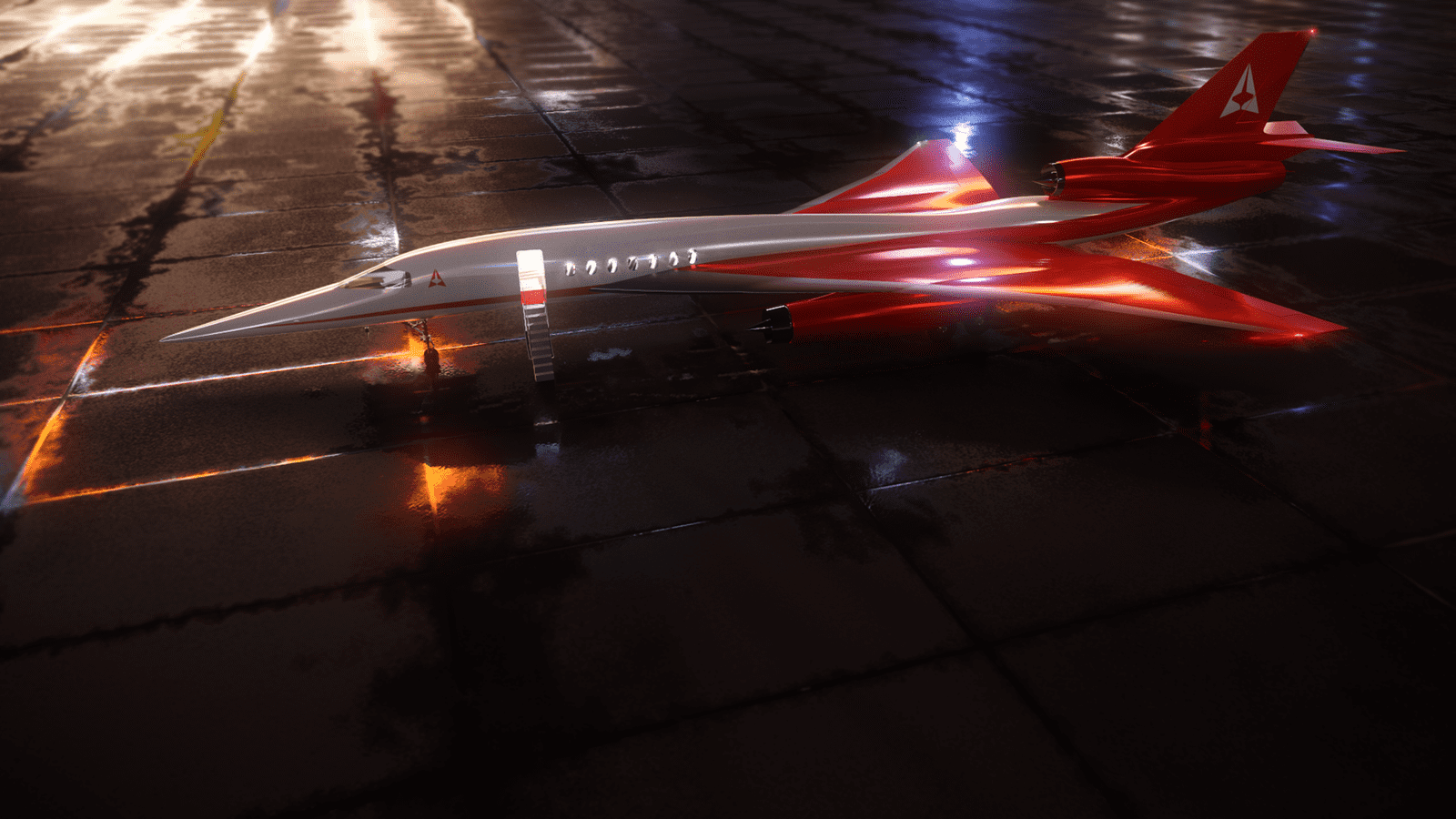
Can you believe we’re talking about supersonic flight again? It’s true. Fueled by the digital transformation, OEMs are energized to introduce the next generation of supersonic flight.
Listen to this episode now.
This is episode #4 of a four-part series. (A special episode for us. Durrell Rittenberg, Director of Aerospace & Defense for Siemens Simcenter, and Thierry Olbrechts, Director of Simcenter Aerospace Solutions, join the conversation for a fascinating discussion.)
Listen to all episodes from Talking Aerospace Today – Season 1:
Episode #1 – “An Integrated Approach: Program Planning and Execution”
Episode #2 – “The Future of Aerospace”
Episode #3 – “Aerospace Compliance in the Digital Age”
Raise your hand if you remember the Concorde SST?
Man, even to do this day that plane is seen as an engineering marvel. So ahead of its time. And of course, that sonic boom is hard to forget.
With the advancement of technology and the desire to decrease travel time, the concept of supersonic travel – even hypersonic travel – is being revisited once again. With so much innovation and the arrival of the digital transformation, things are destined to get very interesting this time around. (For example, one supersonic manufacturer has figured out the sonic boom. Instead of bouncing it off the ground, the boom is aimed upward bouncing it off the upper atmosphere. Wow.)
Today, in our final episode in the series – the conclusion of season one, we’ll be talking to some industry experts who are quite familiar with designing and building of a modern supersonic using today’s connected tools.
My first guest is Dale Tutt, Vice President of the Aerospace and Defense Industry. He’s been my regular guest on all Talking Aerospace Today episodes.
Joining us will be two Siemens heavyweights who will break down some of the specifics of supersonic aircraft design and simulation. Durrell Rittenberg is the Director of Aerospace & Defense for Simcenter, and Thierry Olbrechts is the Director of Simcenter Aerospace Solutions.
We’ll be discussing the specific challenges of modern supersonic aircraft design, and how the models of today are evolving towards sustainability. Will you be boarding a supersonic plane in the near future? Maybe. Today’s episode has the answers!
Some questions we ask:
- What is the business case for developing supersonic aircraft? (3:59)
- How can supersonic aircraft be produced and stay cost-effective? (5:56)
- What are the environmental implications of this type of aircraft? (7:00)
- What are the toughest challenges facing aerospace manufacturers? (9:55)
- What are some of the primary design concepts and challenges behind solving aerodynamics in these modern supersonic aircraft? (12:47)
- How are we helping customers with an integrated solution to solve these problems? (26:40)
- How are these technologies helping customers design, simulate, and build high-speed aircraft? (31:20)
In this episode, you will learn:
- Aerospace industry solutions that address carbon neutrality and sustainability (7:40)
- The problem with the sonic boom (8:42)
- How access to computational resources is changing the game (14:38)
- How building expertise in fluid dynamics helps companies better manage risk (17:03)
- The three challenges dominating supersonic aircraft (18:53)
- How the heat accumulation of greater computer integration can be managed in flight (23:44)
Connect with Dale Tutt:
Connect with Durrell Rittenberg:
Connect with Thierry Olbrechts:
Podcast transcript:
Scott Salzwedel: Hello… and welcome. This is Talking Aerospace Today – the podcast for the aerospace and defense industry and the trends that drive the digital enterprise. A place that brings the promise of tomorrow’s technology to the ears of our listeners today.
And I’m your host, Scott Salzwedel. Welcome to episode four – our final episode in the series.
In this episode, we’ll be talking about what it takes to design and build a supersonic aircraft. Pretty cool, huh? Before we dive in, a reminder that our first episode covered aerospace program planning and execution. Episode two touched on the future of aerospace. And episode three covered aerospace verification, management, and certification. I urge you to give those previous episodes a listen. You’ll find our podcasts on iTunes, Spotify, Stitcher, and Google Podcasts, or wherever you go and listen to your favorite podcast.
Okay, I’m excited to get started.
So supersonic flight. I cannot believe we’re even having this conversation. But it’s true, there’s a handful of new supersonic jet companies out there, there’s new technology for sure, and there’s an appetite for better, faster travel. This could be the dawning of a new age and high-speed transport. During this time of innovation and digital transformation, the sky’s the limit when it comes to supersonic flight literally. Okay, well, maybe up to 60,000 feet. Now, we all remember the Concorde from 15 years ago, still an engineering marvel, and very much ahead of its time. But let’s be real, the Concorde had its detractors, primarily people were against the noise (the sonic boom) and the emissions. Would today’s supersonic aircraft address those issues? The short answer is, yes. And we’ll be talking about that on our podcast today.
Our episode today “What it Takes to Build a Supersonic Aircraft” will touch on some of the key drivers, technology enablers that are allowing supersonic flight to reignite. What about external aerodynamics, thermal systems? Of course, propulsion is key. There’s also huge issues around thermal dynamics and structural integrity. We’ll talk about those issues and more. I’m happy to have a collection of highly talented experts with me today to discuss what it takes to build a supersonic aircraft in the year 2020. Joining me first is Dale Tutt from Siemens Digital Industries Software. At Siemens, Dale is known as the go-to guy for all things aerospace and defense. Welcome back to the show, Dale, it’s great to have you.
Dale Tutt: Hey, thanks, Scott. It’s really great to be with you for our final episode in this podcast series. We’ve had a couple of good discussions, as you mentioned in the previous podcast. In the last episode, we talked about verification management and how it really can help you manage that process. And certification is critical for every company that wants to sell commercial aircraft, and it’s a major cost and schedule driver for these programs. And as aircraft have become more complex, the certification requirements have also become more rigorous. And having a solid process in place is the key to navigating through all the complexities of certification so that you can show compliance that you’ve adequately analyzed and tested your product, and have met all the requirements. And so it’s a great topic, but today, I’m going to really enjoy today’s topic. It’s a fun topic. So, thank you for having me today.
Scott: It’s nice to have you, Dale. I really appreciate you stopping by. So, a little bit more about Dale. Dale is the VP of Aerospace & Defense at Siemens. He has over 30 years of experience in engineering, design, development, and program leadership within the aerospace industry. He specializes in building highly effective cross-functional teams to achieve complex operations when building today’s aircraft. Before Siemens, Dale worked at The Spaceship company, which is now part of Virgin Galactic, Textron Aviation, and Bombardier Aerospace. So, Dale, I’m curious, what is the business case for developing supersonic aircraft?
Dale: You know the old saying: time is money? And if you’re an executive of a business, time is very critical for you. And if you have to fly across the USA from New York to Los Angeles, or going overseas, it might take normally six hours or eight hours. And most of the airliners and businesses today really top out around Mach 0.8, about 550 miles per hour. And there are some business jets out there, like the Citation 10 or the Gulfstream 650, that they increase the speed to just over Mach 0.9, but this has really been kind of an upper limit for a lot of these aircraft today. So, there is only a limited amount of time savings. But if you can push speed to higher speed, like where Aerion is planning for up to Mach 1.4. And some of the other programs out there, they’re pushing up to Mach 1.8. You can really reduce the duration of that cross-country trip, maybe 40 to 50% and that’s saving valuable time. So instead of spending two or three days out of the office, now you can start looking at a much shorter trip and maybe even doing one of these trips in just over a day. And so if you’re going overseas, this time savings is an even greater benefit. And so when you think about the hundreds of airliners that are built each year for all these long haul routes going, you know, these international routes are also just going cross country across the US. And then there’s a hundred or so these long-range business jets that are being produced every year. There’s an attractive market for supersonic airliners and these business jets. So, it’s really not about just having a super-fast sports car as a jet. It’s really about companies being much more efficient and effective with their time. And that’s the business case.
Scott: Yeah, that makes a lot of sense. But won’t supersonic flights be heavy on maintenance due to the economies of scale? How can an aircraft be produced and stay cost-effective? How do you square that up?
Dale: Yeah, it’s certainly a consideration. But when you think about the new design and manufacturing capabilities that are available now, versus what was available 40 to 50 years ago, when the Concorde was first developed, we’re really in a much better situation to be able to manage these costs. And so when you apply a comprehensive digital twin for your product, and your production, and your product support, it really is a difference maker. Having this digitalization and this virtual product, it really helps you design your product faster, and better. And apply new manufacturing techniques and automation to optimize the production line. So, you can really look at more effective ways to support the product once it’s in the field. Across the entire product lifecycle. You’re able to get it right the first time, and you’re able to effectively bring those economies of scale down to a number that’s well within the production rates and usage of what a supersonic aircraft would see.
Scott: I have to ask: what about the environmental concerns? We’re moving towards a carbon-neutral economy, at least we’re trying anyway. How does this fit in?
Dale: Yeah, again, the world really has changed a lot in the last 50 years. And it’s much more feasible now to design and target more carbon-neutral supersonic solutions, or certainly much more efficient solutions. One of the things I find attractive about working with a company like Aerion is that they’re developing a sustainable carbon-neutral aircraft, and it’s their goal. And this is if you talk to the – all of the companies that are out there working on it, that’s their goal is to be more carbon neutral. And it’s a very ambitious goal, but it addresses a major concern for their customers, the regulators, the governments, and quite frankly, the general public. What’s really changed in the design? Engines are a lot more efficient than they used to be. There’s been new design solutions, new materials that have brought significant advancements in the amount of fuel that’s needed for this mission. Right off the top you use less carbon. The aircraft systems themselves are becoming much more efficient, and many have switched from mechanical systems to electrical systems. And when you do this change, you get significant improvements in the power efficiency of these systems. These electrical systems are very efficient from a power standpoint. So if your systems are 30% more efficient, you burn less fuel to power them. So again, you get savings. And then finally, I think the aerodynamics, there’s a lot of new CFD analysis solutions that have made it a lot easier for companies to find more efficient aerodynamic designs for supersonic operations.
Scott: The new designs of these high-speed aircraft are just beautiful. They’re just gorgeous. Let’s get to the heart of the matter. Why is a supersonic aircraft so challenging to build? And I first want to address that pesky sonic boom.
Dale: Yeah, it was definitely a challenge for the Concorde. And that’s the reason it was largely limited to overseas routes. It could only be supersonic when it was over the water. And so whenever it was overland, it had to stay subsonic, so that it would not create a sonic boom and create unnecessary noise. When you think about just limited to being over water, it’s not very efficient, and you don’t get the full-time savings that you could. So, there have been a lot of studies over the years since the Concord around making quiet booms and boom-less aircraft. CFD and acoustic simulations have really helped companies understand what drives a boom. They’ve looked at different aircraft shapes, they’re looking at altitudes, speeds, really kind of a little bit of everything. And as a result, engineers are finding that they can now fly at supersonic speeds and be effectively boom-less even when they’re flying over land in populated areas. So it’s a much different situation now than when the Concorde first came out.
Scott: I like the term “boom-less.” I’m sure that’ll catch on. So, let’s talk a little bit more in-depth about the challenges. What are the toughest challenges facing aerospace manufacturers?
Dale: It starts with, I think, the aerodynamics. It’s making sure that you find the right balance in the shapes that are very efficient from an aerodynamic standpoint. You’re maybe relying more on your CFD analysis than just using wind tunnels and flight testing. And you’re balancing that with finding efficient designs that work well at both supersonic and subsonic speeds because you still want to be efficient even when you’re at subsonic speeds because you’re coming in and landing in an area, or you’re taking off and flying through an area where you need to be subsonic. And then finally, the aircraft designs themselves that help shape the shockwave that creates the boom. That’s one of the challenges. The systems development is also challenging, and it’s about finding some efficient solutions for more efficient systems. Sometimes you have thin wings and so you need to be able to make the systems fit. But this really this concept of transitioning to more electric solutions that tend to be more complex and contain software. So that adds a systems development challenge. And then with the airframe and with the systems, and you also have thermal management. I think about thermal heating of the airframe, and how do you manage this during flight? There’s been aircraft out there that they grow several inches in flight, just due to the aerodynamic heating. And so it’s a very real problem that these aircraft have to deal with. And then rejecting heat from the aircraft systems themselves. And so there’s a complexity of that problem. And finally, I think just the engines, needing to be able to design these inlets, and nozzles, and the blades with new materials. Bringing all those together with aerodynamics, your systems, and your thermal management really does create an interesting set of challenges that companies have to work with.
Scott: It’s time now to bring in some heavyweights who specialize in the areas you just mentioned. With us is Durrell Rittenberg. He’s the Director of Aerospace & Defense for Simcenter at Siemens. And Thierry Olbrechts, Director of Simcenter Aerospace Solutions, also from Siemens. Guys, welcome to Talking Aerospace Today.
Durrell Rittenberg: Very good to be with you and Dale today. Thanks for having me.
Thierry Olbrechts Thanks, Scott. I can’t wait to get started. I’m honored to be here.
Scott: Oh, thanks, guys. It’s really nice to have you here. So, what I’m going to do now is something rather unusual, I’m going to hand over the yoke to Dale. I think I can trust him at this speed and altitude. Plus, he can be much harder on you guys.
Dale: Thanks Scott. Nothing better than sitting and chatting about designing and building supersonic aircraft. The pleasure is all mine. Durrell and Thierry, looking forward to the discussion. I’m very excited to start talking about supersonic design and simulation and the engineering that goes into it. And so I’ll start with you, Durrell. What are some of the primary design concepts and challenges behind solving aerodynamics in these modern supersonic aircraft?
Durrell Rittenberg: It’s interesting because aerodynamics, as you might think, obviously, it’s all around efficiencies, and how can we reduce drag so that we can increase range, and that all feeds into while reducing the sonic boom. Actually, fortunate enough to be part of an organization that looks at sonic boom, and AIAA actually has a workshop called the Sonic Boom Prediction Workshop, which actually increases the fidelity of the type of simulations that are used to predict that kind of noise. And we’ve done a fair amount of work as an organization with companies like Spike aerospace and Aerion around how to leverage computational methods to reduce the sonic boom. And at the same time, look for aerodynamic efficiencies. That is really looking at how do you decrease the drag so you can ultimately increase the range? And there’s probably one other thing in the context of aerodynamics that often gets overlooked, and that is: what’s the overall environment inside the cabin? Because aircraft noise, airframe noise is something that can propagate into the cabin. And you talk about these business people wanting to get across the ocean as fast as possible. If they did that in an environment that’s uncomfortable, that’s noisy, it’s not going to be as productive for them. So, you really have to think about all of these things in the context of aerodynamics. It’s more than just the shape. It’s really looking at all of those components: the noise, the shape, the environment within the cabin.
Dale: Yeah, it’s pretty cool. So, what are customers doing to solve this? I know that they can do wind tunnel, and there’s some amount of flight testing they can do, but how are they really solving all of those challenges today?
Durrell Rittenberg: Well, it’s interesting. When it comes to wind tunnels, and supersonic wind tunnels, in particular, there are very few options out there, NASA has a few, DLR has a few, but there’s just aren’t as many facilities. So, the industry has really relied on computational methods. And there’s some great news in that endeavor because, over the last ten years, the availability of large computational resources has fundamentally changed the game. People are now applying computational fluid dynamics calculations early in the design process. And throughout the entire operating envelope. You talked about having to fly subsonic and supersonic, now they can actually look at that entire mission profile and start to develop databases of, let’s say, the aerodynamics of a vehicle and the control systems requirements for a vehicle across that entire mission profile. And that’s only really something that’s been available to organizations that I would say, small, mid-size, and large organizations in the last ten years. This is something truly unique. And actually, there were a number of workshops recently that talked about what are those enabling technologies. And if we start to think about supersonic, but you know, there are people out there like Hermeus, who are trying to build a hypersonic commercial jet, which is, you know, now we’re talking Mach 3.5 to 5, boy, none of that’s even possible without fluid dynamics calculations. And of course, that supplements what you do in the wind tunnel because at the end of the day, no organization is going to certify an aircraft purely on CFD, they’re going to require some wind tunnel and flight test to basically build out that means of compliance. So, it’s a very exciting time and fluid dynamics to be frank.
Dale: When you think about the challenges and the investment that you’re making in the design of an airplane like this, or actually I think hypersonic even better, the amount of investments that you have to make, and anything that we can do to help minimize that risk is going into flight test, and then, as you said, both from an aerodynamic standpoint but also the cabin interior being able to manage that noise; you’re banking a lot on the results of those CFD tools. So how are we helping our customers with this? I mean, how we’re helping them manage that risk and use those tools?
Durrell Rittenberg: Well, today, we’re lucky enough to work with a number of aircraft programs that are trying to bring these vehicles to market. Aerion, I think you’ve already talked about. Spike Aerospace is another, and there’s several others that we could talk to as well. But we’re actually working with them to bring both expertise in the area of fluid dynamics and how you can use computational methods beyond aerodynamics, looking at structural dynamics, looking at systems integration, systems simulation, we kind of bring our competencies to an organization, our experience. And the other thing that we’re helping them with is how to tie that into the overall digital thread, which is a critical component here. It’s one thing to do a simulation, it’s another thing to bring that simulation into the design process and be able to trace that back to a requirement, and ultimately, how that requirement goes to certification. That’s kind of our vision, and the way that we work with customers is to help bring together the technical competencies, the tools within the portfolio to provide accurate simulation results, and of course, bringing that into the digital thread as a way to kind of help them accelerate that certification process.
Dale: Well, moving on… Another big piece of that puzzle, as I mentioned earlier, is the engine design and the propulsion and the dynamics. And I think about some of the older designs where they had movable or adjustable inlets and even adjustable nozzles, and how they’ve looked at some of the new inlets designs or looking at new shapes and maybe looking at in a bump in the inlets. As we’re looking at the engine and the propulsion side of things, what are some of the things that companies are doing? What are some of their challenges and what are they doing to solve those today?
Durrell Rittenberg: It’s interesting, there’s actually three challenges that I’ve seen as kind of the dominant challenges, especially in the context of aerodynamics. You hit on the first one which is inlet design, and boy, let me tell you, inlet design for a transonic aircraft where you basically don’t have much of an inlet, you have a cowling going directly into the fan and into the engine, and that kind of design is a little easier. But when you get into supersonic, if you have supersonic flow going into an engine, you can choke it. You basically stop the efficiency of the engine. And in the worst-case scenario you can stall. And so when you think about inlet design, and I’m actually part of a technical committee with AIAA called Inlets, Nozzles, and Propulsion System Integration. We are looking at furthering the state of the art in inlet design for supersonic and subsonic vehicles alike. We look at those challenges and say, you know, how can we help organizations help to design an inlet? It’s an interesting aside but kind of funny. At the most recent conference, which actually about two weeks ago for Propulsion and Energy, there was a whole section on inlet design related to the Concorde. Here we are, years and years later, that was designed in the 60s and 70s, and we’re still trying to understand how those engineers were able to design such an efficient inlet design without all these computational methods. But we’re learning from that, we’re applying those strategies, and really helping organizations push the state of the art. And the last thing that we’re seeing is around engine integration. You talked about these new engines, they are more efficient, but they’re more efficient by running hotter. They run a little leaner, and so you have a tremendous amount of heat that’s going into that cowling. And how do you make sure that you have adequate cooling? How do you make sure that you have adequate flow-through so that your engine and maintain its durability across being able to be in service over several decades, which is often what you see for these aircraft. So between inlet design, between engine integration, and then really, trying to drive the efficiencies, you know how do you make those inlets work within that mission profile when they’re in cruise? You want the absolute best aerodynamics, while still maintaining good clean air into the engine. So it’s a difficult problem, but we’ve been working with many organizations to help, again, move the state of the art.
Dale: That’s excellent stuff. It is amazing what they were able to design with the Concorde, your story about how they’re trying to sort that out is just fascinating. So, what are we doing to help out with some of these customers? Are we doing anything, in addition to what you’re doing with AIAA? Do we have other things that we’re working on with some of our customers in these areas?
Durrell Rittenberg: It’s interesting because we’re actually working with both the engine manufacturers. So we’re working with several of the big engine manufacturers who are going to be providing the engines for the supersonic aircraft. In that case, we’re working more on the efficiencies, on the thermal balance, on the durability. And at the same time, we’re working with the integrators on inlet design, and we’re actually bringing to that discussion both our experience and again, our portfolio of tools. We have kind of a wide array of mixed fidelity solutions that can really be helpful, especially early in the process. Again, all of this is supported by having access to this digital thread. You can really tie back the design, the work that you’re doing, and simulation back to that requirement. And really try to push that all the way through once you get into testing and ultimately certification. So, we’ve been very fortunate and working with a lot of these organizations very early in their design process. We can help guide them in terms of some industry best practices, as well as obviously some simulation best practices that really help them move the state of the art.
Dale: Thank you, Durrell. Outstanding. Thierry, I’ll turn to you now. Durrell was mentioning some of the work that we’re doing with engines and we’re running those engines hotter. And there’s some new challenges with thermal but can you talk about some of the other challenges, in addition to that that customers are facing when they’re designing the supersonic aircraft.
Thierry Olbrechts I believe, we already touched upon it with Dale and Durrell, let’s say, the heating that the supersonic aircraft is basically subjected to, and it’s basically connected to the aerodynamic heating, but also you have a performance engine that is basically integrated in the aircraft that needs to be ventilated, that needs to be cooled on one side. But on the other side, you also have new systems being integrated. I’m quite sure that the future supersonic aircraft will have much more electrical and computer hardware integrated that also needs to be cooled. So typically, when you integrate these electrical systems, they might be more reliable and more performant, but one of the problems that you have is that they create quite a lot of heat, and also that heat needs to be rejected. And there’s a lot of new ways to look into how you can basically reject that heat. You might use a fuel tank, for instance, to dump the heat into the fuel tank. But that poses, of course, a lot of problems related to, for instance, when you are at the end of the mission when your fuel quantity is low, maybe rejecting a lot of heat in the fuel might create flammability problems inside your fuel tanks. You absolutely want to avoid that. When you look into the current aircraft development, you want to understand the thermal behavior, the thermal balance of the integrated aircraft throughout the mission. You basically are going to ask the different departments this is the hydraulic department, the environmental control system department, the engine integration department, you’re going to ask them, how much heat do you generate? How much heat needs to be rejected in a certain way? When you want to understand the thermal balance of the aircraft, you actually need that integrated view of the heat exchanges between the systems. That’s often a problem. We see that the different departments like the hydraulic department, avionics department, etc., they do a perfect job in doing the thermal analysis of their individual department but when it comes to bringing all these heat exchanges together at integrated aircraft level, which is typically not done because all the tools that are being used cannot be integrated. We see quite a lot of problems that the integrated thermal balance analysis.
Dale: Yeah, that’s a great point. I was thinking about some of the stories I’ve heard in the past. And some of the early supersonic aircraft, you know, they struggled with, like, on the XP70, and even the thermal heating that the SR-71 goes through when it’s flying. But a great point that on subsonic aircraft it’s not uncommon to take the heat from these mechanical systems and reject that heat to the side of the aircraft which is usually cold. Now a different problem when you’re supersonic, and so it’s a little harder to reject heat to a warmer surface. So, as you say, you talked about the balance, the integrated solution, so how are we helping with this problem? It sounds like a pretty complex problem.
Thierry Olbrechts: Indeed… So, when you want to understand the thermal balance of the integrated aircraft throughout its complete mission, you need to understand the thermal balance of each of the individual systems. That’s where we typically advise our customers to implement a virtual integrated aircraft analysis capability where you basically do, for each individual department, your thermal analysis, but where we also allow to basically bring all that data, all these models together at an integrated level. And allow the customers to even in very early phases of the aircraft development, look into what might be the best system architecture. What might be the best location in the avionic base to put the avionics? Should you basically distribute your electrical systems and avionics systems in a different avionic base? Or do you concentrate in only a few of them? What does it mean with respect to the connection to the environmental control system? Are you going to use an electrical system? Or are you going to use the more classical bleeder system to cool your systems, etc.? So, we allow the customers in our modeling capabilities to create a dynamic thermal model that is capable of looking into that thermal balance. It’s not only thermal balance, it’s also energy balance in a more integrated and model-based way.
Dale: That’s a great concept on the virtual integrated aircraft and using it with the thermal heating. But I remember going through several development programs, and we built these massive systems integration test rigs, where we basically put all those systems hardware in the loop, our customers being able to… Are they solving that problem? Are they still need to build big systems test rigs? Or are they being able to show more and more of this with the vertically integrated aircraft?
Thierry Olbrechts: A very good question, Dale. As you know, in the context of the integration that testing of an aircraft, you create an iron bird, maybe you create a copper bird in context of a more electrical aircraft. But I guess creating a thermal iron bird would certainly be a bridge too far, isn’t it? So, what we actually want to provide to our customers is to create this virtual integrated aircraft models very early in the development phase to basically do the trade-off studies and to look for the right architecture for the specific aircraft and for its specific mission, but also basically use these kind of models in the context of the integration testing of the systems. And that’s where we basically connect the virtual integrated aircraft to the virtual iron bird. We have been working with Airbus on creating a virtual iron bird model that basically allows us to speed up to a shift-left integration testing big time. Typically, you have the flight test. You have the first flight. Typically one year before the first flight, you have a physical iron bird that is being powered on. And we believe that actually three years before that we can actually power on a virtual iron bird, which is giving you quite a lot of insight of how all these systems are going to talk to each other in an energetic way, thermal way, etc. So, we have quite a lot of customers using our simulation capabilities in context of that kind of integration testing, model in a loop, software in a loop, hardware in a loop, pilot in loop type of testing, etc. And related to the thermal management, we strongly believe that simulation can avoid the need to create that thermal iron bird, which would be a very expensive form, isn’t it?
Dale: Definitely. So what’s amazing is how much things have changed since the early days when I was involved with a lot of these systems development and these big iron birds and test rigs, and now being able to do that virtually. It’s just pretty amazing stuff. So, thank you, Thierry. And thank you, Durrell.
Thierry Olbrechts: You’re welcome.
Scott: Great conversation. Before we land this plane, Dale, I want to turn this back to you and ask you to please reemphasize some of these important topics around the digital twin, the digital thread, and even Siemens Xcelerator, how these technologies are helping customers design, simulate, and build high-speed aircraft?
Dale: As I mentioned earlier, a lot of what we’ve talked about today with the simulation and virtual integrated aircraft and the CFD analysis are examples of how applying a comprehensive digital twin and thread is really a difference maker now for designing, and producing, and supporting these commercial supersonic aircraft. And so it’s this rich understanding of your product design. It’s really helped create these “boom-less” designs, help you understand the cabin noise, help you be more aerodynamically efficient. And it’s being used to develop more efficient engines and systems, you know, the inlets as Durrell, and the systems as Thierry was talking about. So, the digital thread is connecting all of these elements of the aircraft together really create this virtual integrated aircraft that can be used to support your certification and as well as reducing risk as you move into your flight testing and build. There’s a lot of investment in these programs, and the ability to help manage that with the digital twin is pretty huge. Simulating and then virtually commissioning your production lines as you move into manufacturing as well as your support processes, within this digital twin will also enable new manufacturing and sustainment methods as you go forward. So, it can really help manage your production rates and lower the cost of your operations. This is all through the digital threads – tying it all together from initial requirements into design, and then into your manufacturing, your product support, so that you can see it transition seamlessly from one phase into the next and kind of simulating every step of the way, and really using your twin to the fullest of its potential there.
And this is all within the Xcelerator portfolio that we have at Siemens. It’s really providing that truly comprehensive digital twin to help enable these solutions. And we’re partnering with companies of all sizes and organizations of all types to help develop some of these exciting new and complex processes and products. So, pretty well ties it all together.
Scott: Wow. I think what we’ve learned is Siemens Digital Industries Software is ahead of the curve in aerospace, there’s just no question. It’s no surprise, we’re bringing the technology of tomorrow to our customers today in a number of real and very innovative ways. So, thank you for visiting with us today, Dale. My sincere thanks to you.
Dale: Hey, no problem, Scott. And thank you for having me. It’s been a lot of fun working with you on this podcast series and look forward to the next series.
Scott: Indeed. Durrell, Thierry, thank you. Such a fascinating and detailed discussion. Thanks, guys.
Durrell Rittenberg: Yeah, thank you.
Thierry Olbrechts: Yeah, great, Scott. And thanks a lot for giving me the opportunity to be in this podcast.
Scott: And of course, I’d like to extend my deepest thanks to our listeners. I’m glad you tuned in to the podcast. Thanks, listeners.
Now at the top of the show, I mentioned this is a four-part series. If you enjoyed this episode and you want to dive into previous episodes, please check out the links in the podcast description. Be sure to subscribe to Talking Aerospace Today on iTunes, Spotify, or wherever you go for your favorite podcast. That way you won’t miss a single episode. Talking Aerospace Today will be releasing new podcasts in the future, so you don’t want to miss out.
My name is Scott Salzwedel, and this is Siemens’ Talking Aerospace Today. I hope you’ll join us again for our next podcast. Until then, bye for now…
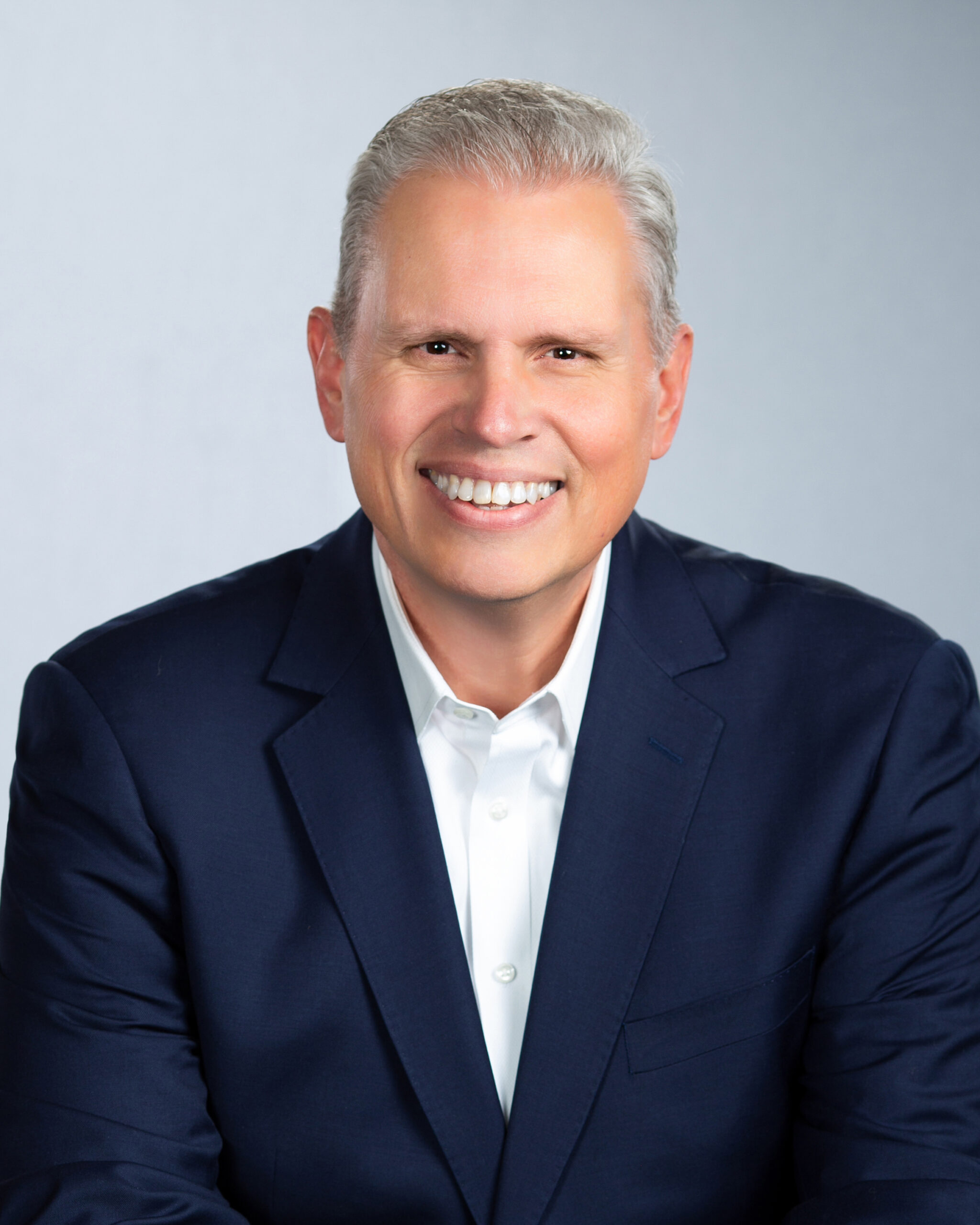
Dale Tutt – Vice President of Industry Strategy at Siemens Digital Industries Software
Dale Tutt is Vice President of Industry Strategy at Siemens Digital Industries Software. Dale leads a team of experts to develop and execute industry-specific product and marketing strategies in collaboration with the global product, sales, and business development teams. With over 5 years of experience in this role combined with extensive experience in the aerospace and defense industry, Dale has a deep understanding of the challenges and opportunities facing companies as they embark on their digital transformation journeys.
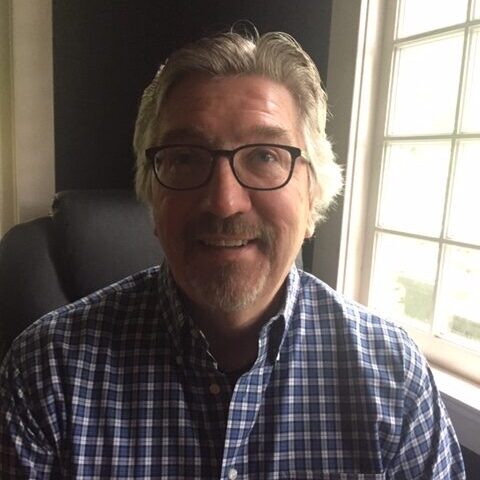
Scott Salzwedel – Host
Scott Salzwedel is senior technical writer and corporate communications writer involved in the Siemens Aerospace & Defense Industry and Siemens Capital. In addition to writer/host of Talking Aerospace Today, Scott is the writer of white papers, articles, blogs, videos and websites at Siemens.
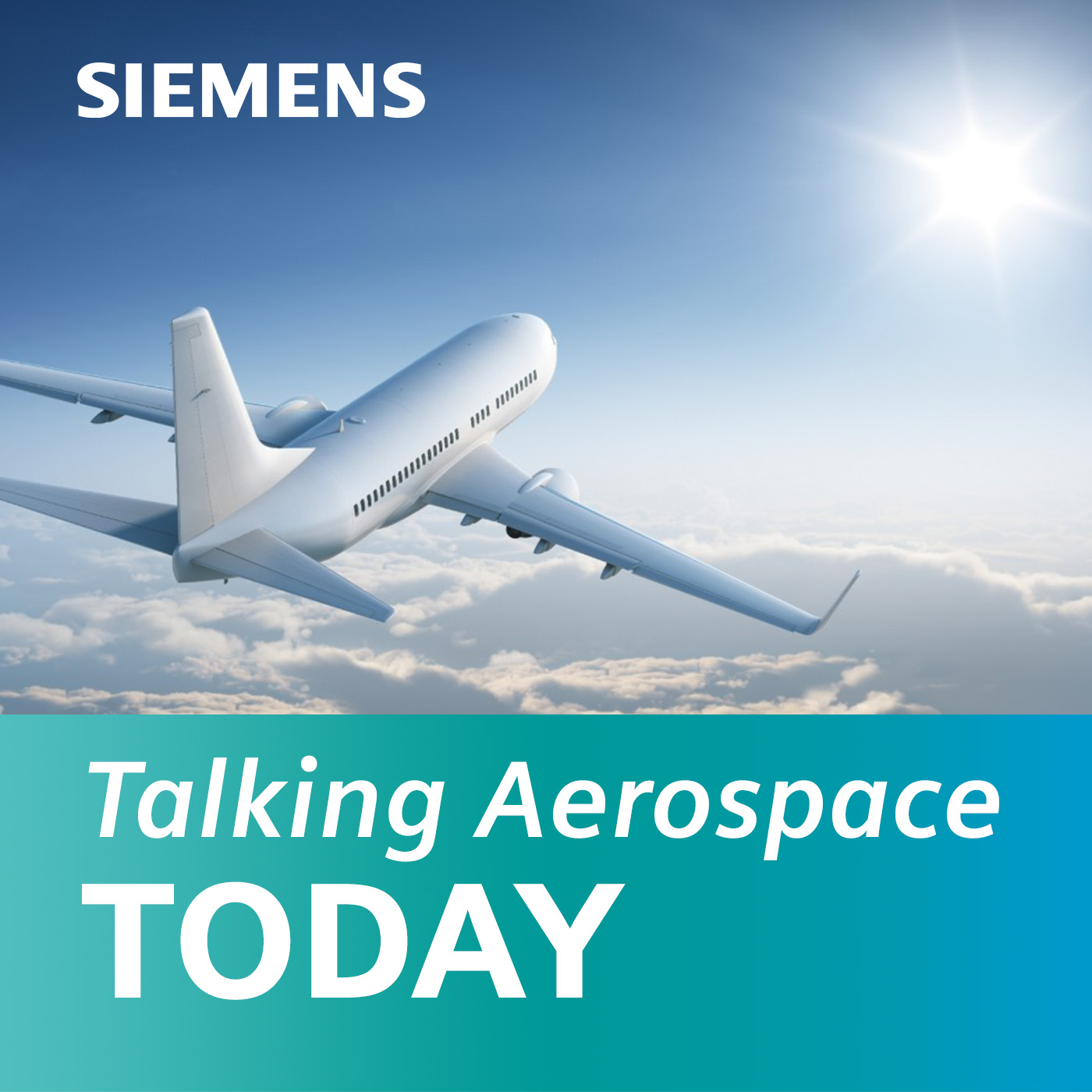
Talking Aerospace Today Podcast
The A&D Industry is at a serious inflection point. Transformation to the digital enterprise has opened up a new era in innovation and technological breakthroughs. However, complexity and compliance continue to hamper the best of efforts.
Join us as we explore how Siemens is turning complexity into a competitive advantage for many of our customers – today and well into tomorrow.