From Skyward Dreams to Groundbreaking Turbines
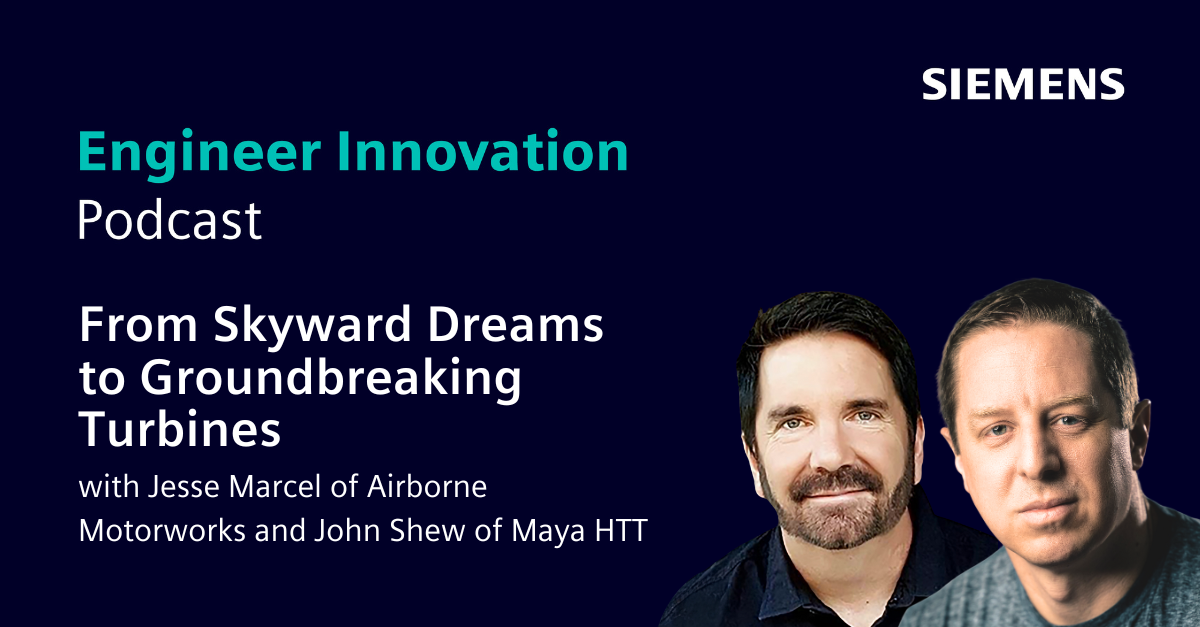
Guests Jesse Marcel (Airborne Motorworks) & John Shew (Maya HTT)
Listen on Apple
Listen on Spotify
Show Notes
In this episode, we’re joined by Jesse Marcel, Co-Founder and Chief Design Officer of Airborne Motorworks, and John Shew, Simulation Services Director of Maya HTT. They delve into the development of innovative wind turbines that could revolutionize local power generation.
Key Takeaways:
- Shifting from propulsion to power-generation technology. (06:24)
- Scaling up the design challenges. (10:35)
- Unique aspects of their wind turbine. (12:26)
- Collaborating on electromagnetics and mechanical design. (15:44)
- Design evolution and efficiency improvements. (19:17)
- The role in addressing climate issues. (29:28)
Resources Mentioned:
https://airbornemotorworks.com/energy-production
This episode of the Engineer Innovation podcast is brought to you by Siemens Digital Industries Software — bringing electronics, engineering and manufacturing together to build a better digital future.
If you enjoyed this episode, please leave a 5-star review to help get the word out about the show and subscribe on Apple or Spotify so you never miss an episode.
Watch on YouTube
Guest biographies and episode transcript
- Shifting from propulsion to power-generation technology. (06:24)
- Scaling up the design challenges. (10:35)
- Unique aspects of their wind turbine. (12:26)
- Collaborating on electromagnetics and mechanical design. (15:44)
- Design evolution and efficiency improvements. (19:17)
- The role in addressing climate issues. (29:28)
Speaker 1:
It’s beautiful to see an idea become and go through the stages. So for me, the most exciting thing is starting with a clean sheet of paper that wasn’t that clean by the time it got to the design and through our iterative processes and finding out that although we’re not wrong in the design we were doing, but how well it fits into this new adaptive architecture. Being able to get it to where it’s at right now, and we’re still at the beginning of this product. There’s lots of little tricks that can be done with the current design, but you got to start somewhere. But as the saying goes, it’s pretty common, your first design is going to be its worst. I think our first design is going to be mind-blowing compared to what’s out there.
Speaker 2:
Hello and welcome to the Engineer Innovation podcast. My name is Chad Ghalamzan. I’m joined today by two special guests, Jesse Marcel, who is the co-founder and chief design officer at Airborne Motorworks and John Shew, simulation service director at Maya HTT. They’re here to talk about a project they’ve recently worked on, which might completely change how we think about local power generation and wind turbines. Jesse and John, why don’t you introduce yourselves to our listeners?
Speaker 1:
I’m Jesse Marcel, and as Chad mentioned, I was one of the original founders of Airborne Motorworks and we originally started out as a propulsion company and engineering and eventually evolved to where we’re today.
Speaker 3:
And I’m John Shew. I’m the simulation services director for Maya HTT. Maya does a lot of things to help people with software-driven digital engineering solutions. But my group specifically does a lot of the simulation, structural, thermal, CFD, EMAG for companies.
Speaker 2:
So Jesse, can you tell our listeners a little bit more about Airborne Motorworks? What does your company do?
Speaker 1:
Airborne Motorworks, it started as a concept like a lot of small companies do, a number of years ago. Just formulation of different ideas, concepts. Back in the day when the idea of flying cars and eVTOL wasn’t really a common term, it was personal air vehicle back then. And I had this idea, kind of a design knack to draw attractive vehicles. I grew up with sports cars and that kind of thing. I used to race some different cars. And in that process I thought it would be fun to combine a sports car that could fly-
Speaker 2:
So that’s where Airborne comes from, is that the Airborne-
Speaker 1:
Yeah.
Speaker 2:
Okay.
Speaker 1:
That’s where Airborne came from. Exactly. And then as it evolved, I come up with something that looks attractive. I’m a big Porsche nut, and it looked like a flying Porsche in a way. And as it evolved, it came to the idea of… To make this thing actually work, you can’t have the more typical propulsion system with props and motors without changing the configuration and the way it looks, that kind of thing. So I thought if we designed a electromagnetic system that maybe is a little more powerful and intensive and directive and stabilising, then that’d be a place to start. So that’s how it started. I got the designs, put them into a vehicle, and then obviously started learning how to write patents and I was able to rough them together. Was lucky enough to get together with a very good patent attorney, Mr. Lau in Seattle, Washington, and kind of went from there.
And so we went through this process of developing the propulsion system. Additional founders came along as we were developing it. From the early stages, you’re raising money and you’re developing, you’re trying to pick a course and it was all developing fairly well. We had some really good numbers, some very strong, very efficient numbers coming out when applied. But then as the company evolved, we came along and we put together an advisory board, that sort of thing. And one of the gentlemen there was well versed in FAA and the regulations and “Have you guys realised what it’s going to take to get your concept, your ideas into something you can fly, that’s going to be legal and accepted?” And we realised we were actually a lot longer from that junction than we thought we were.
Speaker 2:
But how far did you get in your process? Because you said you put some ideas together. Had you built any kind of prototypes or was this still all on paper or digital paper?
Speaker 1:
No, prototypical propulsion systems. It wasn’t so much the pressure that the pumps could generate, but can we do it and stabilise it, so the propulsion system not only provides your lift and your vector direction, those kind of things, but can actually stabilise the vehicle? So in essence, you’re not relying on the typical where you vary the pressures of the different fans to keep things level in a quadcopter, what-have-you. We wanted each system to develop its own mechanical stability. So we were able to do that and we did in our small shops. We built a number of prototypes and tested them and it actually worked out fairly well. The concepts, the science behind them worked well. As we were delving into the engineering component that brought us some very good people, some their founders, that helped us develop into a more of a workable prototype. As the company went to the point where we had developed some simple propulsion systems, now what’s it going to take to make them powerful enough to lift the vehicle and do all those kinds of things?
And we were progressing. We actually worked with a number of companies, building some prototypes of the propulsion system. And as we were going along, just like I said, that was the junction where it came along, now you have a workable propulsion, or direction, our propulsion system. Now you’re working at the airframe. I had a big tubular carbon fibre airframe put together in our shop and we’re going a house all come together. And as it was developing, we were realising that we didn’t have all the expertise we needed to take it to the next level. And when we brought in that expertise, which is through our current CEO, Hugh McElroy, and a number of other people, it became very obvious that again, the resources to take it to the next level would involve a partnership or some kind of a next level mechanism to get where now we have a workable prototype. Because again, we weren’t pulling pieces off of the shelf to make it work, we were having to develop each individual part.
It was exciting work, but we realised that the numbers it would take to get to that level were a little out of our realm and we haven’t stopped that work, we’re still going that direction. But when we hit that, and again when Hugh McElroy came along, we looked at what’s the low hanging fruit out there with our engineering or our science or propulsion, that kind of thing. And while we were doing patents on propulsion and the uses, and we did a number of them out there, we have quite a number, about a half dozen patents locally, about 30 that are working around the world. It was just a ripe opportunity when we came along because we were innovators at the beginning before the big craze hit with eVTOLs, that kind of thing. Alongside that, we always thought we’re creating a very efficient propulsion system, a very stabilised, somewhat quiet, a balanced system. And we started looking into power generation, flipping it inside out. Instead of powering it, let the wind power is where we’re going with it.
Speaker 2:
But before you were working on this, it sounds like it got pretty far along because flying cars or flying vehicles, that’s the stuff from 1930s science fiction. But it sounds like this wasn’t just an idea you were toying with, you developed a pretty stable prototype, but why didn’t you pursue other propulsions? Why did you look at power generation? Why did that switch come about? Has it granted a motor and a generator [inaudible] as the same device, but you did go into a very different area. What was the rationale behind that?
Speaker 1:
We prototyped basically mock-ups of motorcycles to fly, platforms, all that kind of thing. As we evolved into, okay, what are we going to do next? It’s going to take a lot of finance, quite honestly, a good partnership to develop to the next level. And as we’re looking at the numbers, we thought if we could look at this thing as a generator rather than propulsion system, it just made sense. I did a brief study, and honestly this is not my expertise, of what the market is out there as far as what are the good things going on out there, what are the problems that are going on out there and wind generation. And some of those issues can be solved through the same science that we’re using in our propulsion system. So it was almost a natural fit. It wasn’t a big leap, other than you were looking at diameters of our propulsion system of 15 inches.
And then as we look at power generation, which is looked at differently, it’s basically, it’s not so much what percentage of the kinetic energy can you pull out of the wind at the end of it. Efficiently and quietly and bounce, all those little items. So when we came and were introduced to John and his team, we were kind of base level. We had a design for a 15-inch propulsion system and we came to these guys and said, “Hey, let’s blow this thing out,” just because there’s some easy numbers to get a hold of it on a 12 foot diameter wind turbine, although we’re nothing like what’s out there. We thought, let’s do that so we can compare some. Are we going down the right path? How do we look like compared to what’s out there at 12 feet diameter? That was where we started with John.
Speaker 2:
And were you aware, John, that you had been working on what was once supposed to be a flying propulsion motor or is this new to you?
Speaker 3:
They told us that upfront when we joined on, they explained, “Hey, here’s where we’re at. We were designing something for a motor, for a flying vehicle. But yeah, we want to switch directions. We think we can get to market quicker with wind turbine and oh by the way, we want to scale this up to 12 feet.”
Speaker 2:
So just a little bit bigger.
Speaker 3:
It’s just a bit bigger, little bit.
Speaker 2:
Do you have any experience working on either propulsion or wind turbines before this?
Speaker 3:
Yeah, actually both. And I should say too, I’m speaking for my team as well. I didn’t do all the analysis on this. Both myself, I’ve done some analysis on wind turbines before, primarily structural on my side, and then also a lot of aircraft experience as well. But Maya as a whole, we have experience with that. And my understanding, and Jesse step in and correct me if I’m wrong, but they definitely came to us with a design. They came to us with a kind of novel sort of patent, something a little bit different where the electromagnetics are on the outside versus the inside, wanted to scale that up to 12 feet. So it was an interesting idea and an interesting project.
And when they came to us, it’s also a little bit undefined because it’s very early in the process. Oftentimes when you do a typical analysis services project, you’re given a package that’s very well-defined. Here’s the inputs, here’s the outputs we want. This is a little open-ended. I have some experience. I was in the startup world for six years prior to joining Maya, so I at least have some experience with that sort of open-ended, working on everything at once, trying to define everything at once world. So I really felt we could do it and yeah, I think we were able to come to a pretty cool feasible design in the end.
Speaker 2:
So I know there’s some unique features about this wind turbine that we’ll get to, but maybe we could start with this question. What did it take to scale up from 15 inches to 12 feet?
Speaker 3:
We started first with the electromagnetics and I laid out the process that I saw for Airborne, talked with them. We were very collaborative through the whole thing and I got to say they’re a great company to work with. We’ll start with the electromagnetics and we’ll design that motor and you can’t just scale that linearly. So they already had a design at 15 inches. We had our EMAG team scale that up to 12, adjust for anything they needed to adjust for. We were using the Simcenter E-Machine Design tools. We also ended up using HEEDS as well, to do some optimization studies. Just run some different trades for working on the sizing of the motors, the sizing of the magnets and the steel in the motor as well.
Speaker 2:
Did you have to change any of the materials because you were working on such a bigger scale?
Speaker 3:
We did. We actually looked at different types of materials. So we did a bit of looking at types of materials. We also ended up switching to a Halbach array. Because it’s bigger, I come more from the structural side, so my concern was always like how much mass is spinning and at what speed, because I know with structurally that’s always going to be a problem. So we were trying to minimise the mass we could while still get the power output that they needed. So primarily from our EMAG design, we were trying to hit the power numbers they needed, but keep that in a reasonably low RPM and keep that in a reasonably low mass as well. So a lot of our design using the E-Machine Design tools and HEEDS was to try and reduce that mass.
Speaker 2:
That was the issues when you were trying to scale up, but the wind turbine itself isn’t just like every other wind turbine that people may be familiar with. There’s a couple of things about this one that’s unique. Maybe you could both talk to that point. What’s so different about the wind turbine that Airborne Motorworks has worked with Maya HTT on developing here?
Speaker 1:
Initially, and again, I’m looking through the eyes of more science than engineering, and there are certain principles that make sense that if you could align multiple rotors that could extract energy that’s not being extracted by a first rotor by a second or a third, whatever that is. And then as you rotate air over the first one and that it makes sense to rotate the other one in the opposite direction and then doing a little bit of side-studying into jet turbines and those kinds of things, how that assembly looks, how that whole thing comes together. And it worked out really well by, I like to say it was all because we thought it all out, and it’s not exactly the truth…
Speaker 2:
When is that ever the truth though? When can you ever think it all out?
Speaker 1:
It makes sense to put in some kind of, we’re going to have the field rails, etc. They’re going to be on the outer edge. You’re going to have something to hold this together. It’s going to probably be some kind of a tube of some kind. Okay, now that becomes a duct. Now heat can be dissipated through that duct. Now the air direction can be brought to that duct. Now you can use diffusers, etc., etc., that are going to create that pressure that’s going to be able to extend the efficiency. So it was more like just a step-by-step. It’s really propulsion, jet turbine, wind turbine, and it’s just the mating of those three as it went through. We were bare-bones and we came to Maya and said, “This is it. These are our ideas.” And the first run-through is, “Yeah, if you scale this thing, it’s going to be crazy.” It took a lot of work to get it from just a simple, see what we can do with this thing, to actually having it be feasible.
Speaker 3:
It was a fun project, honestly, it was more open-ended than we usually get to do. So as a primarily analysis services, we got to put some of our design chops up to the test as well. And the biggest thing throughout this I think was us taking a look at, hey, here’s the design they have. It’s definitely different for a wind turbine, so what are the pros and cons of that and how do we take advantage of that? How can we think outside of the box? Because if you look at normal wind turbines, there are usually three blades, a single rotor, usually try and make them as big as they can. They don’t have ducts or anything. But with the way this works, having the electromagnetic motor on the outside, it really did lead us down a different path and we were able to take some of the advantages of that or take advantage of that to try some different things.
So obviously then a duct makes sense. Having two turbine blades inside there instead of one and being able to counter rotate them because you don’t have to have a mechanical transmission and gearing all connected and have all the maintenance issues with that. It doesn’t matter if they’re counter-rotating in different directions in this purpose, ’cause you’re just tying them in electronically basically, not tying them mechanically to each other. So there were really some interesting things that kind of led us… even down to the blade shape because of how we have the stability on the tips because we’re connecting to the… You’ve got the duct, the shroud out there, you’ve got the electromagnetics out there. It allowed us to explore blade shapes that I think is fair to say, they look more like blade shapes you would see in a turbine, in a jet engine than they do with a typical wind turbine. So it was really interesting project and really let us, I think, come up with some really cool ideas and explore that design space that hadn’t really been explored too much yet for wind turbines.
Speaker 2:
So it sounds like you guys collaborated quite a bit here. Is it a process between the two? Like you said, this wasn’t just a simple, “Can you please run the analysis?” How much influence did you have on each other’s process?
Speaker 1:
It was exciting because they ran numbers of numbers of variations and I was looking at it one way and thinking that… Just a specific item, air gap, you got to squeeze that down. You got to this, that and the other. And then to the evolution electromagnetics, he was actually fairly broad with what could be done, which is great, a little wider tolerances, that kind of thing. Structurally it was easier to put together a mechanical design. So significant changes, thought processes changed as we were going along. And honestly what I loved in working with Maya, one of the most exciting things is because I’m not an engineer. I do have a background in more science, but when we’re talking about this and I hear the people working on the actual blade design and the skies, one of them staying up all night, they’re trying to figure out a problem.
So it’s more than just a tick off the boxes on a piece of paper. It’s actually a certain level of interest or excitement in our project. It was almost a team-time relationship making this all work, and that was just so much more efficient. We were able to solve so many more problems faster and effectively, I think, as we moved along. Because we’re not “Hold, no, this is it, you can’t go out of this area.” We wanted freedom of expression. We wanted to have everybody collaborate and come up with best ideas. Examples of how do we slow it down, expertise in different areas were brought in that we were unaware of. Just all those different things. Like I said, it was a very team effort. It wasn’t so much an A and B that worked together. It was very exciting and it still is exciting as we go forward.
Speaker 3:
Yeah, I mean that’s part of the fun of it was the collaboration. And again, Airborne was great to work with. And upfront, I said, “Hey, I understand this is very open-ended. This isn’t your standard services, like, here’s the geometry, come back to us with the results.” So upfront we knew from the beginning we’d have to touch base frequently. From our side, we started with the EMAG and we would come back and give updates to Airborne. We would look at the options, give them a menu of directions we could go. And say our recommendation, here’s where we think we get the most bang for the buck because obviously we could iterate on this design and this analysis forever, but at the end of the day, we want to get you to be able to do a prototype quickly. So we’re always keeping that in mind and trying to get as efficient as possible, as quickly as possible, with a feasible design.
So we collaborated with them all throughout the process and then internally, as well, we had the teams collaborating because we started with the EMAG design. We had to put a stake in the ground somewhere on that design. Once we had a feasible design there, we shifted to our CFD team, they’re using STAR-CCM and NX to come up with the blade design and the duct design, run those analyses. Then we would iterate back and forth. We’d go back and check with our EMAG team. We did some final iteration checks to make sure, okay, we got the CFD, now let’s go back and check, make sure we’re still on the right balance with the EMAG. So this collaboration both between Maya and Airborne, it was a really cool project because of that.
Speaker 2:
So besides scaling the size, how much did the design change by virtue of it changing its end usage here?
Speaker 3:
They’d had this 15-inch motor design, they’d had some rough CAD of a turbine design as well. There were definitely changes to it. I think it was a lot of…
Speaker 2:
If you had them side by side, would they be recognisable beside each other, or would you say, oh, you could only see how this evolved with a lot of…?
Speaker 3:
Yeah, I think you can see that one is more preliminary and one’s more detailed. Obviously our blade designs now, you can tell there’s a lot of work in the shaping of the blades, which is height of the blades and stuff, the turbines. So it just continued improvement on the detail of the design.
Speaker 1:
If I could say something, I mean, it is an idea, efficiency-wise, what percentage of kinetic energy we pull out of the air. With our rough designs, we were in the low teens. By the time these guys were done, by the time they’d worked out — and we’re not done yet — but to the point where we’re at right now, we’re pushing 70.
Speaker 2:
Wow, okay, that’s a big jump.
Speaker 1:
So you figure that if you look at where we started, by the low teens, and now we’re up to 70, that’s a big deal. We’re well beyond what current technology produces. So now we not only took a concept, a very rough concept, and that switch over and with Maya and their teams being able to develop a viable project, and now, to our delight, would be a light way to put it, is that we actually have something here that can really change the marketplace in the way that… Especially our turbines are more compact, they’re smaller. We can game them together and they become used for micro grids, where instead of having to have the larger ones that are miles out in the field, they can be proximate to the location of the micro grid. That’s becoming a standard. Even worldwide, we have a lot more micro grids. There’s been a lot of fear of, well, what happens if you have a huge micro grid then somebody takes it out, the Eastern Seaboard goes out? Micro grids get rid of that.
And then of course you have a bonus to us, you’re local, you’re not shipping power across lives for miles to get to your location. You’re proximate to the need. As an example, we have a site in Texas right now that we’ll be putting out our first units. And our intention is to go from where we’re at on the design and we’re just working through our mechanical design ready to go through the prototype process, which we hope to deploy sometime next year in several models, and then it’d be full production in the following year. It’s really been a growth process, but it’s been actually incredibly fast. Being able to take something and completely… Our original designs, I did put in there that we could be using them for power generation in wind terms. The idea was that you can bridge it, but they were… Again, we were a long ways from getting something that was a mere idea.
It’s a lot easier to write a patent that has a lot of ideas behind it than it is to actually have the engineering behind it to make it work as you go along. I’m pretty good about coming up with some crazy ideas, some ideas, putting them down on paper, getting some intellectual project behind them. But then you’ve got to have a really smart engineering team to back those up and see, is this actually viable or are you just off your rocker? Can you actually make something like this work? And then the intersection of Airborne Motorworks and Maya HTT was able to make that happen.
Speaker 2:
Well, this doesn’t sound like that crazy of an idea. It sounds like you were able to actually get closer to what you would like to achieve here. You’ve talked a little bit about how the micro grid is one of the reasons why this particular wind turbine and its size and less noise makes it different in its deployment. What about maintenance? Is there any maintenance issues that come with this design versus a standard wind turbine topology?
Speaker 1:
Because there are no generators, it’s more magnetics that’s holding everything in place and together, there’s a big difference. It’s very low maintenance. And just because of the size, the needs to keep this thing held together are a big component of that. And because the work Maya did in being able to keep us at a very low RPM, but still being able to extract that much energy out of the wind, now we have a unicorn wind turbine. There’s a lot of talk about wind turbines out there right now and it’s not all good. And we’d like to reframe what a wind turbine can be. A lot of it’s compact, low maintenance, the dual counter-turning rotors, you can balance far much, you can eliminate a lot of vibration, noise and those kinds of things, which are just a byproduct of what we’re trying to do here.
And then again, being able to put it locally. Another item is, at the end of the day, the duct is a big windsock. And if you’re familiar with the windsock, they direct themselves into the wind and ours is going to have that natural… It’s going to want to be as direct into the wind. There isn’t going to be any thought behind it, it’s going to want to be in its most efficient state all the time as far as the wind direction goes. So all these pieces really came together. And again, now that we can, instead of being some very large wind turbine, they’re going to look somewhat unique. There isn’t really anything out there that looks like what we’re doing, but when you put them out there, they’re going to be again, much smaller. You could turn a building into a micro grid, those kind of things. So it has a lot of applications that you just have a more difficult time if you have a more contemporary wind turbine design.
Speaker 2:
Have you been able to test this design with actual weather patterns to see if there’s any difference in its performance or has it just been mainly prototyping for the electromagnetics and CFD structural stuff?
Speaker 1:
One of our engineering team, the teams basically on Airborne Motorworks, went through and they looked at, okay, if we’re going to be putting this, our first one, it’s going to be in Texas. How high? What’s the average wind speed? Temperatures? So those were all taken into consideration and those were all brought to Maya. It’s a starting point. Now, we expect those to change as we go along, but there’s an iteration or iterative process in this wind turbine design that allows us a lot of modularity. So perhaps a wind turbine that works great in Houston, a variation of that is going to work great in Tunisia or whatever. But it all builds itself. It’s very modular and the components are somewhat… They’re smaller, they’re lighter, you don’t need large cranes and big crews and the dangers you can run into and those kinds of things. So there’s a lot of things that play into it. And again, just the compact size, the really high efficiency and being able to look at approximate to the need really helps as far as making it a viable project.
Speaker 3:
Yeah, I was going to say that’s one thing we knew and tried to design for along the way, is we knew that they were looking for, one of the benefits of this design was low maintenance compared to other wind turbines. So we tried to keep that in mind as we designed this. And also removing as many mechanical mechanisms as parts as possible, like really limiting that, take that into account every aspect of the design. Even the idea of maybe we can get away with not having pitch control on blades because we do use a blade design that doesn’t have just one sweet spot and doesn’t work anywhere else, but it’s a wide-band. You’re not going to stall out the blade if you’re off nominal on the wind speed because obviously the wind is not constant. It’s always changing. So we try to keep that in mind and really focus on what are the key benefits of this design and make sure that we took that into account when we were doing the EMAG and the CFP design, as well.
Speaker 2:
And just for the benefit of those who don’t know off the top of their heads, when you say this is much more smaller and compact, can you give us a sense of the proportions we’re talking about here?
Speaker 1:
Our design was originally just to put a stake in the ground, was 12 feet. Realistically, the micro grids are going to need about a hundred thousand plus watts. How many numbers is it going to take of these? So realistically, you’re looking more at about probably a 20 to 25 foot design, by the time we’re all said and done, somewhere in that neighbourhood. And getting together, there might be three of them together. When you look at it as a strict ROI, it makes a lot of sense. It’s much cheaper and more useful. The energy that can be drawn out of the air as a percentage is so much greater when you take into consideration of losses and those kinds of things.
It just becomes a very efficient… Well, economically, it makes a lot of sense. It removes a lot of those things that people have a bad taste in their mouth, so they don’t want to see a big spinning wind turbine in the neighbourhood, that kind of thing. So it eliminates that. But our focus at this point is now moving to ROI because of its compact size and that we’re estimating costs and those kinds of things, but we can deliver energy more efficiently at a lower cost than it would take to bring it in from a field, basically.
Speaker 2:
Would this be a fair statement, this was really a simulation-driven design process?
Speaker 1:
Yes.
Speaker 3:
Yeah, definitely.
Speaker 2:
Could you see you achieving this without using… Obviously everyone uses simulation to test, but would you see yourself being able to achieve the objectives here without using tools like that to hit the objectives put forth to you by Airborne Motorworks, John?
Speaker 3:
I’d say not as efficiently. You could get to a design, but being in simulation-driven design, obviously Maya is a very simulation-driven company, but being a simulation-driven design using tools that we were able to use in the Siemens portfolio, really helped us keep focus on the end goal of that efficiency. But you can CAD up anything, but we didn’t start by making CAD. We started by doing some literature review actually first, looking at designs and technology and stuff that’s out there, but from our end it was almost entirely simulation-driven. We did start on the EMAG with their initial design. We scaled it up, but then we’re focusing on the simulation to get the power output that we need. And then from the CFD side, we didn’t start by just making CAD, we started by looking at, okay, what are the blade shapes we need to get the power output that we need?
Kind of thinking about that end goal, the efficiency, drawing power out of the wind, taking the wind, turning it into rotational energy to get that power out. And we’ve just let simulation drive our design the whole way. I think Jesse talked about, we went from about 10% to 70% efficiency and we did multiple iterations of that where we would do a design and run the simulations, see where we’re at, look at what we think the next best change is based on what we saw previously on the analysis and make those changes and re-run. So we did multiple iterations, even some optimization in there as well, parametric designs and optimizations to be able to drive up that efficiency as much as possible. Honestly, it became a game for our CFD team. They were enjoying coming back each meeting, be like, “Hey, we’re up to this percent now,” or “We’re up to this percent now.” Amazed me sometimes where they were up to with the next iteration.
Speaker 2:
It sounds like you enjoyed the project. That’s pretty clear and very interesting work that was done. And like you said, you had a lot more maybe chance to put your thumbprint on this one compared to your other work. Jesse, just something that occurs to me. We’re recording this at the end of 2023. By most people’s standards of recording, this was one of the hottest temperatures on record. For those even who have been sceptical, climate change is becoming more and more a thing that everyone is accepting. Is this one of the solutions maybe perhaps reducing carbon emissions, especially when it comes to power generation?
Speaker 1:
Absolutely. It kind of ticks off all the boxes across the row on as far as a climate change or looking at a great energy source. I really don’t know what you could do to top it, what we have… Or perhaps even retrofitting some of the existing technology out there with some of our devices and those kind of things. It all goes together very well, with an eye towards… ESG is thrown around there…out a lot, and that kind of thing. So any company that’s trying to define themselves on the ESG component, we would definitely be a great partner for them in helping them achieve those goals through our design work. And as we’re talking about through the simulations now, we’re going through all the mechanical work to get them out there. It’s a good time to be where we’re at. That would be a fair statement.
Speaker 2:
Going to ask you both this question and whoever wants to be brave and answer first, go ahead. Biggest lesson learned while working on this project?
Speaker 1:
Let me start from the high level. It’s beautiful to see an idea become and go through the stages. So for me, the most exciting thing is literally from starting with a clean sheet of paper that wasn’t that clean by the time it got to the design and through our iterative processes, and finding out that although we’re not wrong in the design we were doing, but how well it fits into this new adaptive architecture. And we couldn’t be more excited about the direction of the company and with Maya HTT being able to get it to where it’s at right now. And we’re still at the beginning of this product, there’s lots of little tricks that can be done with the current design, but you got to start somewhere. But as we move into variable error gaps and it’s all kinds of different concepts, there’s so much more to go. And as the saying goes, pretty common, your first design is going to be its worst. I think our first design is going to be mind-blowing compared to what’s out there, so.
Speaker 2:
John?
Speaker 3:
Yeah, I think when you asked that question, I was thinking it’s maybe not so much lesson learned, but lesson validated that I’ve been learning over my 18-year career — is just the more collaborative and the more integrated the design and the analysis is upfront, the better the design ends up being in the end. I’ve learned that the hard way in previous projects when that wasn’t the case. This case we really integrated the design and analysis and were very collaborative across the board. And even with that, there were times where I found like, oh man, we should have had the EMAG and the CFD team talk just a few days prior or something. Things like that. I’ve constantly been learning just the more you can integrate that, the more you can have the design analysis coming together, the better result you’re going to get in the end.
Speaker 2:
So it sounds like this is still something that you’re developing. What’s next for Airborne Motorworks and Maya HTT when it comes to this wind turbine, but also other projects that you might have?
Speaker 1:
We’re in a mechanical design. We’re going to be starting the prototypes at beginning of next year, so it’s going to be fun to start deploying those and then working in a production factory and all those kind of things to actually get that business going. In the meantime, we’re still working on all of the aerospace area though. What’s good for the goose is good for the gander. We’re learning from the wind turbine side, better parts, they’re going to work on the propulsion side now, so it’s going backwards. So we’re still developing that area, that atmosphere, that business unit if you want to call it that. But in the aerospace, it’s now only looking better as we go along with the rest of it. And it’s a time thing too. It’s like, we’ve been writing patents for years and years and now they’re all starting to come…
We have a number have come through and they’re start coming more and more. So the whole project, the whole company has really come together and now we’re looking for partners. We’re working with investment banks and investors and looking for building out that end. But we’re making those connections. Business journals are starting to look at us and starting to want to publish us. And so it’s starting to really get out there. So it’s getting to be that steep rise component of a company. So like I said, we’re very excited about this place.
Speaker 2:
John, anything to add?
Speaker 3:
From that standpoint, we’re just continuing to support them as they need and excited to work with them. We’ve done a lot of great work already and we’re just continuing to work-
Speaker 4:
This episode of the Engineer Innovation podcast is powered by Simcenter.
Speaker 3:
… with them, provide the engineering services they need when they need them.
Speaker 4:
Turn product complexity into a competitive advantage with Simcenter solutions that empower your engineering teams to push the boundaries, solve the toughest problems and bring innovations to market faster.
Speaker 2:
It sounds like a fascinating project. I think it’s not atypical in engineering to start up with one idea and end up somewhere completely different. But it’s always important to remember that the sky’s the limit. Thank you both for joining me today. It was a pleasure talking to both of you. And thank you for listening to this episode of the Engineer Innovation podcast. If you enjoyed today’s episode, please make sure to leave a review and follow us so you never miss a new episode when they drop. My name is Chad Ghalamzan and thank you for listening.
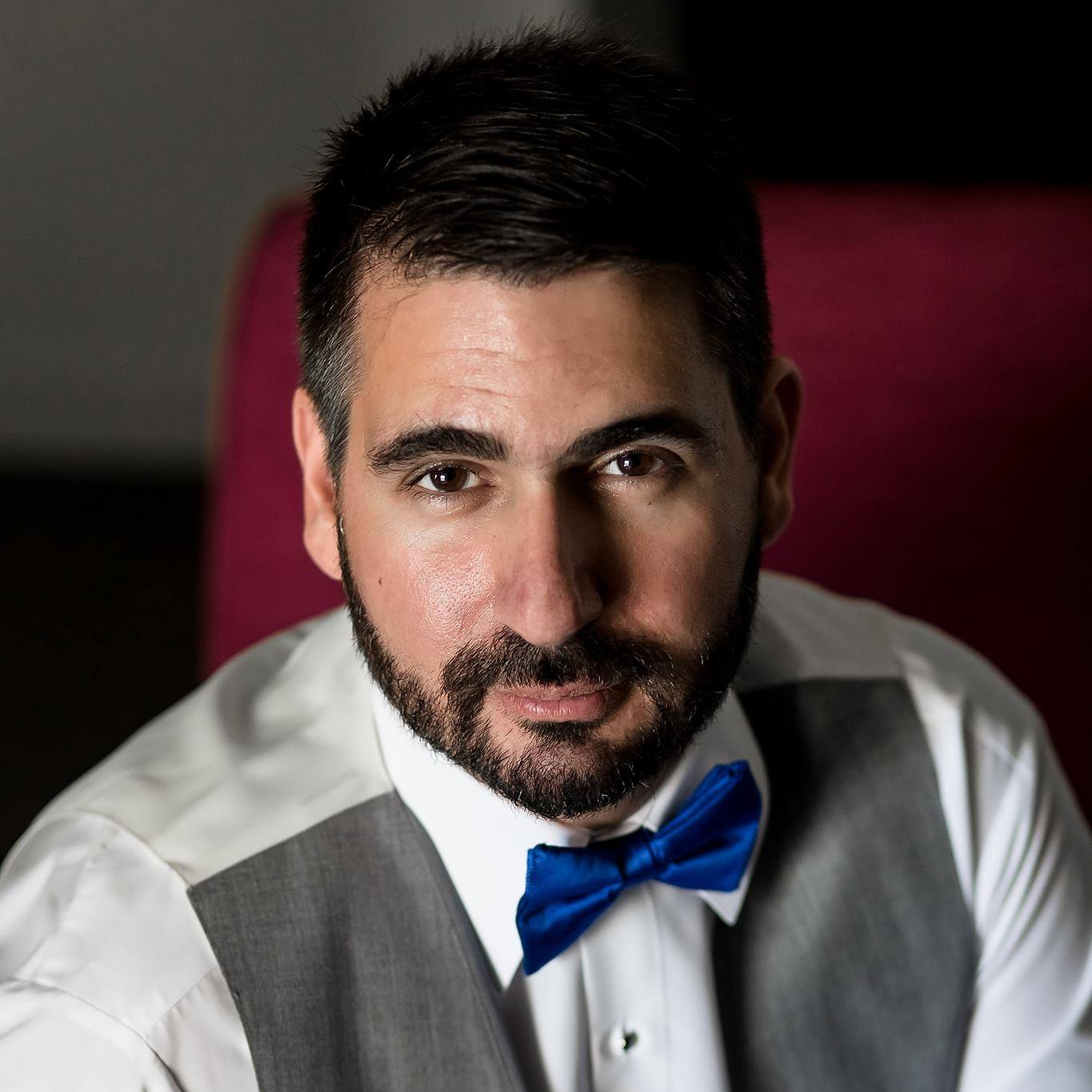
Chad Ghalamzan – Host
Chad Ghalamzan is a computer engineer with over two decades of experience in sales and marketing for the simulation and test industry. He co-hosts the Engineer Innovation podcast and creates content for Siemens Digital Industries Software. He’s tired of people calling him ChadGPT.
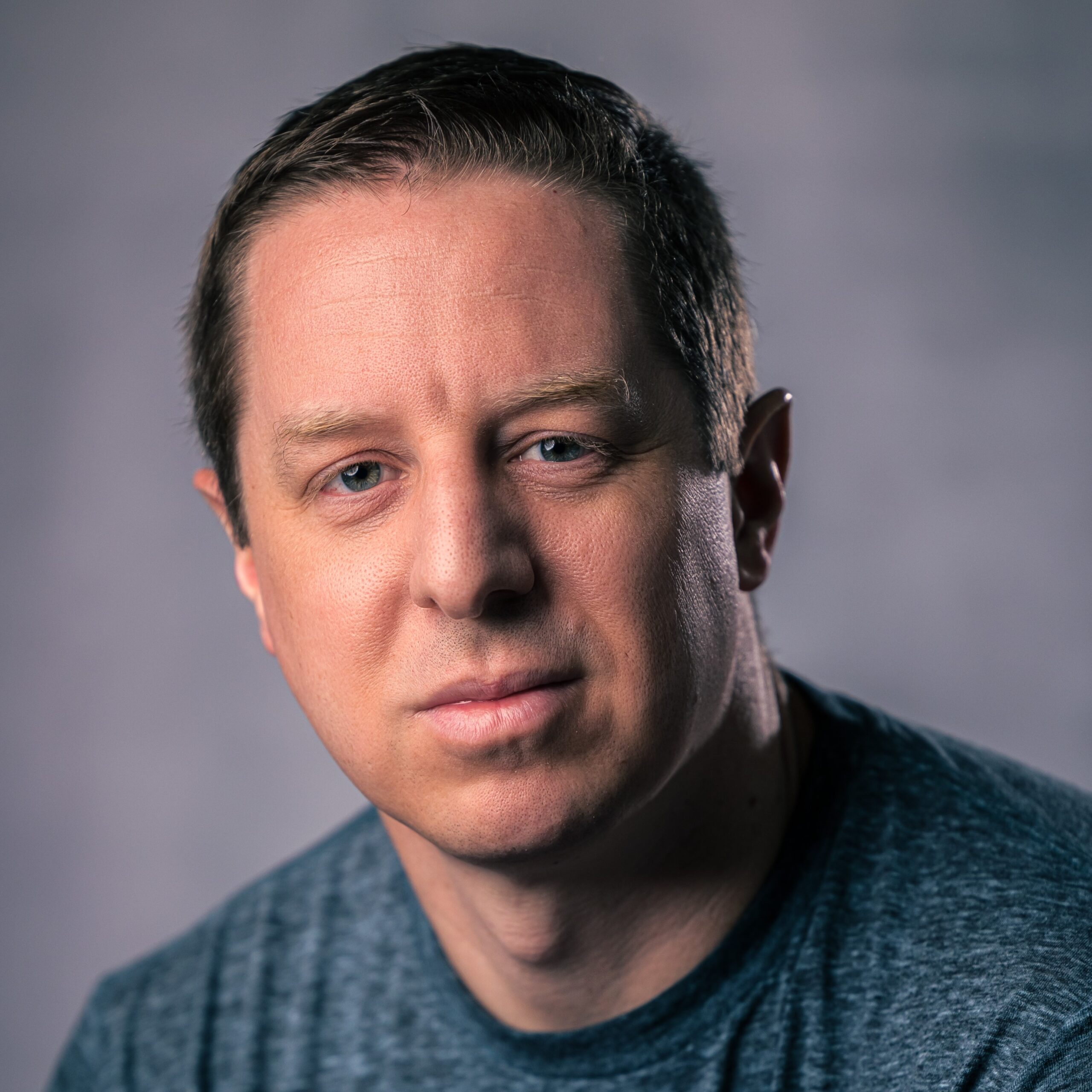
John Shew
John Shew brings nearly two decades of expertise in solving complex engineering challenges through physics-based tools. Specializing in shifting product design curves leftward, he accelerates project timelines by leveraging advanced simulation technologies. With a diverse background spanning aerospace, ride entertainment, transportation, aviation, and renewable energy, John is a versatile leader, offering CAE expertise, design knowledge, and effective project management.
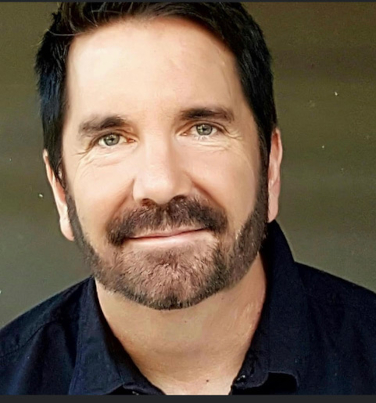
Jesse Marcel
Jesse Marcel is Co-founder of AMW, Technology inventor and designer of vehicles in transportation. Understudy at laboratories of Jeff Holter, the creator of the Holter Monitor. Studied physics, chemistry, and biology. Bachelor’s degree University of Montana in economics and finance. Studied Aerospace Engineering at Montana State University. Is a published author, filmmaker, and executive producer.
Take a listen to a previous episode of the Engineer Innovation Podcast: Engineer Innovation: Reinventing the Wheel: Cycling Innovation with Frederic Poppenhäger on Apple Podcasts
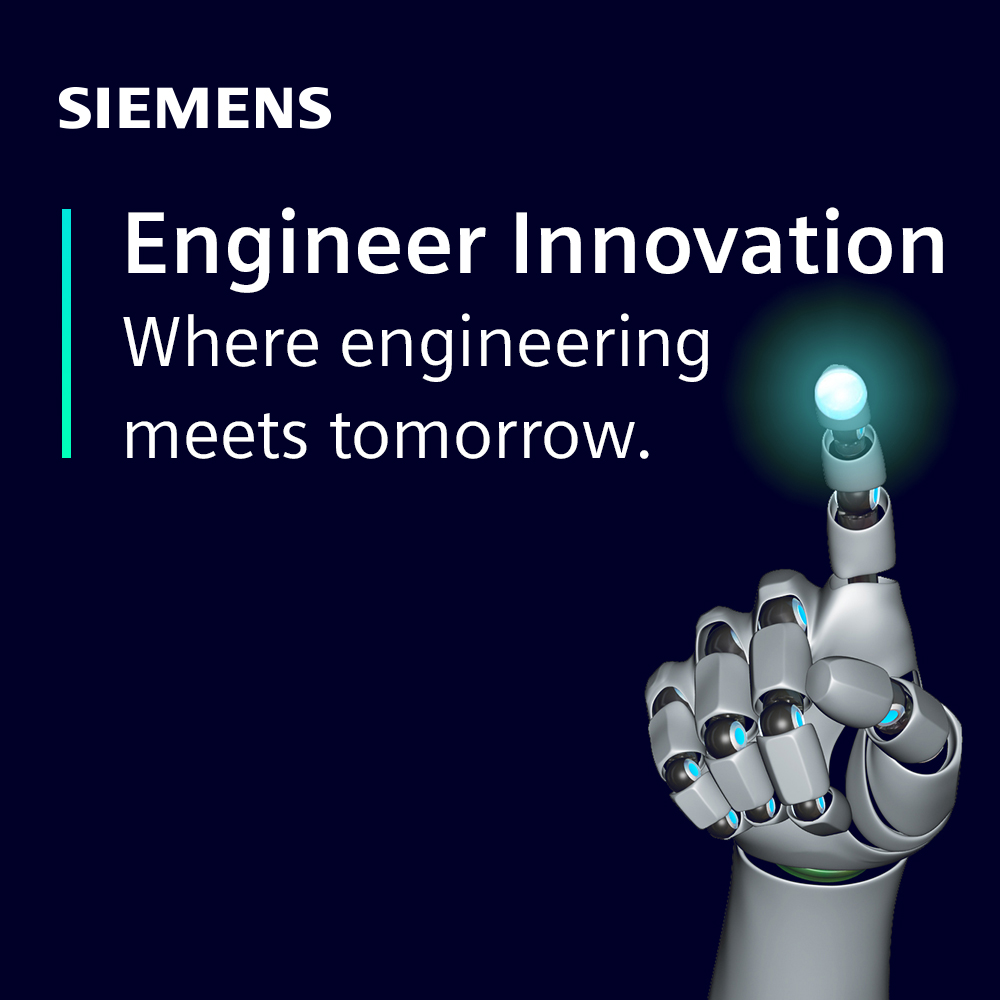
Engineer Innovation Podcast
A podcast series for engineers by engineers, Engineer Innovation focuses on how simulation and testing can help you drive innovation into your products and deliver the products of tomorrow, today.