Engineering the Past: Junkers Reviving the Junkers Ju 52 with Danny Wadewitz
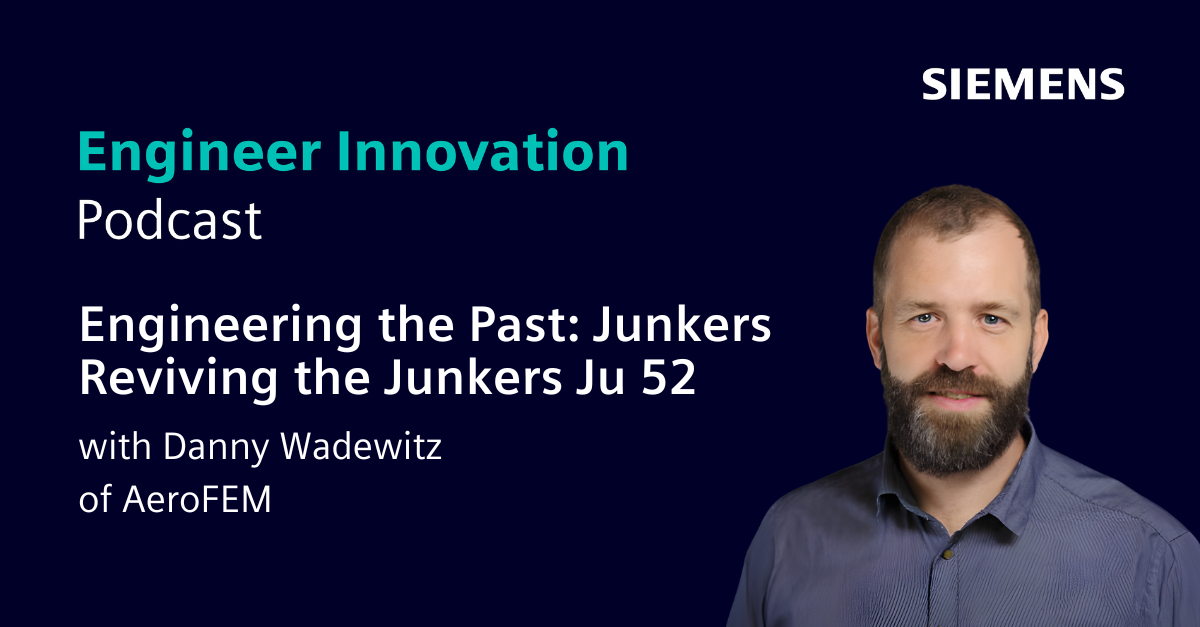
Listen to the Engineer Innovation podcast on
In this episode, we welcome Danny Wadewitz, Calculation Engineer and Member of the Executive Board at AeroFEM, to talk about the use of cutting-edge engineering to restore the iconic Junkers Ju 52 aircraft.
Danny highlights the innovative use of 3D scanning for replication and provides fascinating insights into how modern technology aids in reviving and preserving significant pieces of aviation history.
Key Takeaways:
- Introduction to the Junkers Ju 52’s historical significance.
- The enthusiast-led initiative to bring these aircraft back to the skies.
- Challenges faced in reconstructing the aircraft from scratch.
- Observations on the asymmetry and wear of the old aircraft.
- Using Siemens tools for simulation and analysis in the aircraft restoration project.
- Changes in materials used for the aircraft rebuild.
- The status of the airworthiness certification for the rebuilt aircraft.
- Overview of AeroFEM’s work in the aerospace industry and its unique capabilities.
- AeroFEM’s involvement in the Solar Impulse solar aircraft project.
- AeroFEM’s diverse engineering projects, from historical aircraft to future innovations.
Resources Mentioned:
Siemens NX Reverse Engineering Tool
AeroFEM’s Aerospace Industry Work
This episode of the Engineer Innovation podcast is brought to you by Siemens Digital Industries Software — bringing electronics, engineering and manufacturing together to build a better digital future.
If you enjoyed this episode, please leave a 5-star review to help get the word out about the show.
For more unique insights on all kinds of cutting-edge topics, tune in to siemens.com/simcenter-podcast.
- (00:16) Introduction to the Junkers Ju 52’s historical significance.
- (03:31) The enthusiast-led initiative to bring these aircraft back to the skies.
- (04:17) Challenges faced in reconstructing the aircraft from scratch.
- (06:30) Observations on the asymmetry and wear of the old aircraft.
- (08:26) Using Siemens tools for simulation and analysis in the aircraft restoration project.
- (10:32) Changes in materials used for the aircraft rebuild.
- (13:17) The status of the airworthiness certification for the rebuilt aircraft.
- (15:55) Overview of AeroFEM’s work in the aerospace industry and its unique capabilities.
- (17:59) AeroFEM’s involvement in the Solar Impulse solar aircraft project.
- (19:12) AeroFEM’s diverse engineering projects, from historical aircraft to future innovations.
Danny Wadewitz:
… thousands of hours. It’s been a process that you could keep on doing. Fortunately, as I already said, the engineering art at the time was impressive, so they used a lot of standard profiles, standard parts in the aircraft, which you scan once and digitalize them, and then you try to basically build your structure from this catalogue of standard parts that you have, like you would do today. So it’s not been necessary to scan everything extensively. Also, you have symmetry in the aircraft, which you can make use of, and a lot of basic engineering principles, which were quite advanced at the time as well, which you could take into account.
Stephen:
Regular listeners will know that this podcast is unashamedly about the future of engineering, but sometimes it’s fun to speculate about what would happen if we applied modern day engineering simulation tools to some of the great projects of yesteryear. In today’s episode, I interview Danny Wadewitz from AeroFEM about a project to get the iconic Junkers Ju 52 aircraft back in the air. The Ju 52 had its maiden flight in October 1930, but all of the remaining aircraft had been grounded since an accident in 2018. The aim of this project was to demonstrate the airworthiness of an entirely new replica Ju 52 that has been built from 3D scans of the original aircraft.
As you’ll hear, one of the biggest challenges faced by Danny and the team was to try and reduce the takeoff weight of the aircraft to a level which is acceptable to modern regulations. What really struck me about this interview is just how difficult it is for modern engineers armed with an array of fantastic engineering simulation tools to improve on the designs of an aircraft that was first built like 94 years ago, using not much more than paper, pencils and slide rules. Danny was an extremely interesting and very charming guest, and I hope you enjoy listening to this episode of the Engineer Innovation Podcast.
Hello and welcome to a special episode of the Engineer Innovation Podcast. Now, if you listen regularly, you’ll know that this podcast is normally about the future of engineering. Today we’re going to take a dip into the past as I talk to Danny Wadewitz from Swiss Engineering Company, AeroFEM about how they use simulation and tests to get an iconic 90-year-old aircraft back into the air or almost back into the air. Danny, so the aircraft in question is Junkers Ju 52. Could you tell us about why that aircraft is so iconic?
Danny Wadewitz:
Yes, hello Stephen. Thanks for having me. The Junkers 52 aircraft, it’s one of the iconic aircraft because, in a way, just due to the sheer number of aircraft that have been built, and then also it’s throughout the years when it was built, it was a workhorse for the German airlines and also many other airlines. So it’s also been quite a long-lasting aircraft, as well. It’s been reliable, it’s been robust, and apparently from what the pilots were saying, it’s quite pleasant to fly really, and I think that’s most things. The other thing is probably the appearance of the aircraft. It looks quite mighty with its three engines and the sheer size of it, and also it, from modern perspective, doesn’t really look like something that is able to fly.
Stephen:
Which makes it an interesting engineering project, doesn’t it? Because actually the aircraft industry has evolved away from lots of the features of this design. We can talk about that in a minute. If I look at Wikipedia, which we can sometimes trust, it says that it was in production between 1931 and 1952, and that 4,835 of them were built. According to Wikipedia, there’s three that remain airworthy. Are any of those still flying, do you know?
Danny Wadewitz:
Not in Europe anymore, as far as I’m aware. I think in South Africa there is one that’s flying, last time I checked, but the last three that were flying in Switzerland have been grounded following the accident in 2018.
Stephen:
That aircraft accident, which tragically killed 20 people, I think was mainly put down to pilot error, but there were some maintenance issues with those aircraft as well, which meant that they’re grounded. So 4,835 of them have been built so far. There are plans to build a 4,836th aircraft, which is what we’re talking about today. Can you tell us about this project to get that aeroplane back in the sky?
Danny Wadewitz:
Yes. The Swiss company that was operating these last three remaining flying Junkers aircraft in Europe basically stopped with this tragic accident, and in the aftermath of that, the whole fleet’s been grounded to what you say. Eventually it’s been put down to pilot error, but there were other issues that were found, basically leading to a complete grounding of the fleet. And then basically, as this aircraft with all its history, and there was one enthusiast who had enough money to be able to put that dream into reality to bring that aircraft back into the air. He’s been flying with the aircraft for years and he’s been quite impressed with it and also with the sight of it, with the sound of it, and one of his big dreams was to bring that aircraft back into the air. But he’s also been the one who founded the F 13 Project that made it back into the air, and I think for him it was a logical step to try that.
Stephen:
So what’s involved then in basically reconstructing a classic aircraft from scratch? I don’t suppose back in the 1930s there was many CAD models you could rely on, so you must’ve been working from drawings. How did you get the data to start constructing the models for this aircraft?
Danny Wadewitz:
Yeah, it was basically starting from scratch again. All that was available was an old aircraft that we could look at, the two aircraft that were left with the company, which we could use to scan and basically get digitised this data. Junkers were quite advanced for their time. There were drawings of everything. They had a system almost like a PLM system. They were under version control and everything. It was all analogue, but it was all there but unfortunately it got all destroyed with the bombing of the Junkers Flugzeugwerke in the Second World War, and there were no drawings available whatsoever. Basically we had to redo everything from scratch, and as you can imagine with the sheer size and complexity of this aircraft, it would’ve been a nightmare to do it by hand measurement or anything.
The idea that we had was to 3D-scan the aircraft, which we essentially did twice. We did it once from the outside and we did it again from the inside and then in different stages of disassembling the aircraft, if you like. The first step was to scan the entire aircraft as it was assembled and then disassembling the different individual components and scanning them again, scanning them from the inside, removing the skins and scanning the truss framework on the inside of the wings and scanning the inside of the fuselage and all that sort of stuff.
Stephen:
That sounds like a really detailed and time-intensive process. How long did it take? Have you got an estimate of how long it took?
Danny Wadewitz:
Thousands of hours. It’s been a process that you could keep on doing. Fortunately, as I already said, the engineering art at the time was impressive, so they used a lot of standard profiles, standard parts in the aircraft, which you scan once and digitalize them, and then you trying to basically build your structure from this catalogue of standard parts that you have, like you would do today. So it’s not been necessary to scan everything extensively. Also, you have symmetry in the aircraft, which you can make use of, and a lot of basic engineering principles, which were quite advanced at the time as well, which you could take into account as well. Basically this all goes hand in hand and reduces your labourers’ scanning essentially.
Stephen:
So you mentioned symmetry there. These are quite old aircraft, which you’re seeing lots of operation again. Are they still symmetric or is there some signs of wear and tear and bending of parts?
Danny Wadewitz:
It’s definitely not been symmetric anymore. It had quite a lot of incidents and repairs and all that sort of things. A lot of material deformations that come with time and creep, if you like, and all that sort of thing. Yeah, as you said, with 80 years of age, can’t expect someone to be symmetric anymore.
Stephen:
And so the output of all that effort was what? Is it a 3D model or is it a triangulated surface file? What did you use as the input to the CAE models?
Danny Wadewitz:
Yes, the output from the scanning was a triangulated surface file or basically just a gigantic cloud of points. The real work comes after that, that it’s making surfaces, creating parts from all these points. Fortunately, Siemens has quite advanced the NX reverse engineering tool boxes, really advanced and really intuitive also. So basically with all our engineers working on that and never done that before, they picked up on that really fast and almost perfected the work on that. It was impressive how these points could be transformed back into surfaces, into parts, into assemblies, and essentially into the full aircraft again.
Stephen:
And I guess we’ll talk about how you use that for simulation and for working on airworthiness, but actually that’s a historical record now for the aircraft, isn’t it? It’s the defacto record of what that aircraft looked and probably will exist beyond the lifespan of any of the existing aircrafts.
Danny Wadewitz:
I guess you could see it like that. It’s just quite an interesting view, but yeah, you’re right. It’s the oldest aircraft now in PLM probably.
Stephen:
So looking back at the history of this aircraft, and again relying a bit on Wikipedia, it said that the first develop on this aircraft started in 1930. It doesn’t say when, but it flew for the first time in October 1931. So it looks like it was a really… If you think about how long it takes to get a modern aircraft in the air, this was a really rapid development process, and so they got this thing flying and, as you said, with quite advanced technology. What simulation tools did you use and what sort of simulation did you use on this model?
Danny Wadewitz:
We used the whole bandwidth of Siemens tools that we have available. We historically used the Siemens tools because we’re also reseller for Siemens, but we started with the reverse engineering, which we did in NX, then we put the geometry that we obtained from the reverse engineering into CFD analysis, which we did with Simcenter STAR-CCM+, and the results from the CFD analysis then went into DFE analysis, which we did with Simcenter Femap. So that gave us the internal loads on every truss of the aircraft, if you want.
Stephen:
Were there any surprises in that process? We know that the aircraft works because it flew for a very long time. So were there any surprises when you were looking at the results from the simulations?
Danny Wadewitz:
One of the surprises was that there was little room for optimization really. With the certification requirements, we had to reduce the weight of the aircraft quite dramatically. So it’s been flying with a takeoff weight of 10 and a half tonnes. Now, the limit on CS23, which this aircraft was supposed to be categorised as, is at 8,600 kilogrammes. Now that’s a huge weight reduction, especially in the aircraft industry. That’s almost like an impossible task. Now, our idea was with modern simulation tools and everything that you would find a lot of places for improvement if you want, but then I think it’s a mixture of both. The requirements are more stringent now than they were at the time, and also engineers at the time, they knew what they were doing, so there was really not much room for weight savings on the structural side.
Stephen:
I love the fact that we’re attacking this with the best tools that industry has to offer and actually we find out that those guys 90 years ago were doing a brilliant job without any of these tools as well, which goes to show you just how great engineers are. So I described this aircraft before as being iconic and legendary, but perhaps a better adjective would be groovy because it’s quite famous for being a grooved aircraft. It’s made from, I think, a copper-aluminium alloy, the original aircraft, but the modern aircraft is going to be built or might be built out of aluminium, isn’t it? Why did they change the materials? Was that a weight-saving thing or was that just because of corrosion?
Danny Wadewitz:
No, we had to change the material… You mean we changed the material for the rebuild or?
Stephen:
Yeah, for the rebuild, yeah.
Danny Wadewitz:
You have to use what’s commercially available now, and I think if you compare the chemical composition of the materials, they’re quite similar. Now we had to choose a material that is similar in strengths and similar in durability, but is commercially available. Because when we did the project, there were problems with supply chains all over the world and also in the aircraft, especially in the aircraft industry. Now, if you were to choose an exotic material, then you would have no chance to get that through certification and make it work or build it at all. So the material that we used is, for and large, the same as Junkers used.
Stephen:
And so the corrugated kind of shape of the airplane’s exterior, which was almost classic of the Junkers aircraft because the F 13 which you’ve also worked on also had that. Why was it corrugated? Certainly not for aerodynamics, I would think.
Danny Wadewitz:
No, certainly not. It’s simply for stability. The Junkers F 13, that was the first full-metal aircraft that were built, and to overcome some of the problems that you have switching from wooden material to metal material is obviously weight. And then to overcome that, you need to go as soon as possible. And at the time, the modern design principles of an aircraft wing, they weren’t applied at the time. It’s like a framework structure, so it’s not like the wings carry any of the load or something, at least not in compression with the corrugations and stuff. So you had to provide some kind of out-of-plane stiffness for the metal sheet, and that was done with the corrugation. So I think that’s just plain and simple.
Stephen:
Which is one of the reasons why it’s so iconic because you don’t see many aircraft like that, do you? Not even historically. So we talked a second ago about the tragic crash that ended the flight-worthiness of these aircraft, but if you look back in the history of the aircraft, one of the prototypes, one of the first prototypes also crashed. Because when the aircraft were designed, it was designed as a single-engine aircraft. One of the prototypes crashed and they decided to upgrade it. It felt that it was under power and upgraded to a triple-engine aircraft. Was there any evidence to you? Did it seem like it was designed as a triple-engineered aircraft or was any evidence that maybe they just stuck two extra engines on it? Did it look very elegant, I guess is the question?
Danny Wadewitz:
Well, that’s in the eye of the individual, I believe. I think it’s part of why it’s such an iconic aircraft is the really mighty three radial engines on the front. It’s the sound and it’s the sheer size of these engines, and it looks like it’s a very powerful aircraft. If you look at the pictures of the one-engine ones, it’s certainly, I would say, less impressive.
Stephen:
And perhaps we wouldn’t be talking about it today if it was a single-engine aircraft. So how far through the kind of airworthiness certification process did you get?
Danny Wadewitz:
With authorities, we didn’t get very far. We got to the point where we applied for type certificate and the concept was shown on the arrow and pretty shortly after that the project was cancelled. So I think we basically did all the preparations, we had the process laid out for ourselves and never really got to show compliance to the authorities, unfortunately.
Stephen:
Which is slightly disappointing because I guess, would you have flown on the aircraft if it had been flown again?
Danny Wadewitz:
Oh yeah…
Stephen:
Is that something you would’ve risked? You trusted your calculations that much?
Danny Wadewitz:
Definitely. Yeah, it’s been flying before and then with all the changes we made, it’s been made safer, essentially. So one of the major points was the reliability of the engines. Because you had countless of little levers in the aircraft and you had massive console where all the levers for all three engines were placed and which you constantly had to monitor during the flight. And then the way these engines were controlled, it was very easy to make errors on that or have them not running on an optimal regime. So basically it’s changing that, the reliability of the aircraft has improved dramatically.
Stephen:
The intention was to build the aircraft with more modern engines, modern avionics as well, so it would be a lot safer…
Danny Wadewitz:
Yes.
Stephen:
… if it ever got flying again. So this aircraft hasn’t flown yet and might not fly. But a previous project worked on by AeroFEM is one of the precursors to this aircraft, which is the Junkers F 3, which I think is probably one of the world’s first all-metal aircraft. I think it was built in 1919, so it was not very long after the Wright brothers, it was one of the first commercial airliner almost. It carried about four passengers, as well. And that actually did fly, didn’t it? Because I was watching the YouTube videos of that first flight last night. AeroFEM were also involved in that work, as well. And I could just imagine if I was an engineer working on that project, standing on the airfield on a grass runway as well, it wasn’t like a nice tarmac runway, I would be absolutely scared that my calculations hadn’t worked. So it’s fantastic to see that this process does work and these planes do end up in the sky eventually, sometimes.
Danny Wadewitz:
Yeah, it is fantastic to see. It’s a great feeling to see them eventually fly, but it’s a process that is well monitored throughout by the authorities. It’s a good process. So it’s complicated, but it’s well monitored throughout.
Stephen:
I guess it’s really effective, which is good news, as well. So I guess, Danny, that you don’t get paid your salary to work on 90-year-old, 80-year-old aircraft all the time. So AeroFEM’s been around for, I think it was the 21st anniversary of the founding of the company last year. I think you’ve worked there, according to your LinkedIn profile, for about 11 years. What is your day-to-day work? What sort of projects does AeroFEM work on day-to-day?
Danny Wadewitz:
We’re mainly doing our work in the aircraft industry or in the aerospace industry. That’s 60%, I would say, of our daily business. We are service providers, so we basically work for TC holders. We work for other aircraft companies that require changes or repairs on aircraft, which we are allowed to do from the authorities’ point of view. We have design organisation approval that we hold since 2019, and that allows us under our own authority do, as I said, do changes and repairs on certified aircraft. Which is quite a unique feature that we have for a service provider because that’s normally something that the TC holder or just companies that have type certificates for aircraft would do, but we can provide that as a service and that’s a big part of what we do. Another field that we also work for in general, mechanical engineering, big customer of us designs rollercoasters. There’re quite some similarities, but it’s mainly a fatigue and durability analysis that we do on these.
But these structures, they are quite sophisticated as well because they’re always trying to break records, get faster and higher and more, I don’t know, thrilling and then all this sort of things. And we were quite heavily involved in the development of some of those rollercoasters as well, which is a huge part of our business. We do aeroelastics and that’s something where we specialise. We have Arne Vollan, who’s over 80 years now, 81 I think he turned, still coming to work on a regular basis. So basically do aeroelastics, aerodynamics. And recently, five years ago, we have started a branch CFD, like computational fluid dynamics, which is psychological extension to the structural analysis.
Stephen:
So with regards to aeroelasticity, another kind of iconic project that AeroFEM worked on, and we talked a bit before this interview and you’re quite new to AeroFEM, is the solar impulse solar aircraft, which I think set a lot of records for being the first solar aircraft to circumnavigate the world with some quite outstanding flight times, as well. Again, Wikipedia’s doing quite a lot of heavy lifting today, but according to Wikipedia, it flew one stage for 117 hours or five days and five nights from Japan to Hawaii. So that’s an incredible, very unusual project as well, which kind of challenges the norms of usual engineering. And it’s got big wings, it has to be very lightweight. I think it’s got an engine which delivers about the same power as the Wright brothers’ engine. Do you have any recollections from that project?
Danny Wadewitz:
Yes, as we started getting involved because we were tasked to do the aeroelastics on that aircraft. Now you might think with an aircraft that flies that slow, plotter would not be an issue, but with the massive wingspan of this aircraft and the very, very lightweight construction, it’s a lot less steep than a conventional aircraft. So that even with this low velocity or low velocities, you would have to consider the aeroelastic problems. And Arne, he did quite a lot of work or we had quite a hard time to make that actually work. Quite proud of that project as well. And then from there, as it normally happens, one thing leads to another and we got involved in more and more structural work as well. So we had quite good insight into that project as well. And we’re happy to accompany the engineers that way to that flight around the world.
Stephen:
Which I think is probably a good place to end this podcast because we’ve gone from 80-year-old aircraft to perhaps ideas for some of the aircrafts of the future, as well. It’s fantastic to see that you’re applying Simcenter tools to almost all of these projects, and it’s really interesting to see how your expertise is so recognised that the AeroFEM is a company that ends up with all these really strange and unusual challenges in engineering. So thank you very much, Danny. You’ve been an excellent guest and thank you for listening to the Engineer Innovation Podcast.
Danny Wadewitz:
Thank you, Stephen. It’s been a pleasure talking to you.
Speaker 4:
This episode of the Engineer Innovation Podcast is powered by Simcenter, turn product complexity into a competitive advantage with Simcenter solutions that empower your engineering teams to push the boundaries, solve the toughest problems and bring innovations to market faster.
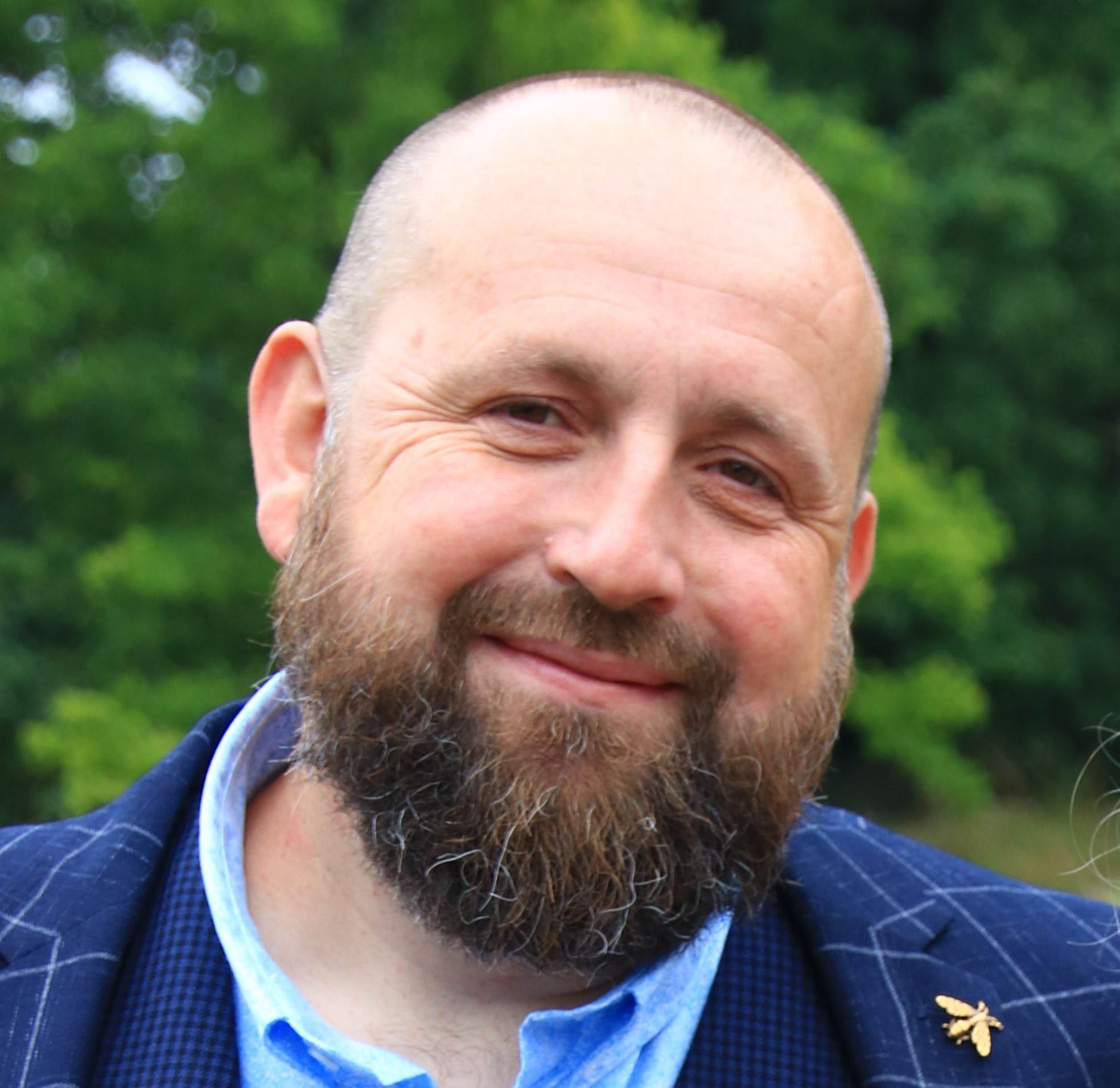
Stephen Ferguson – Host
Stephen Ferguson is a fluid-dynamicist with more than 30 years of experience in applying advanced simulation to the most challenging problems that engineering has to offer for companies such as WS Atkins, BMW and CD-adapco and Siemens.
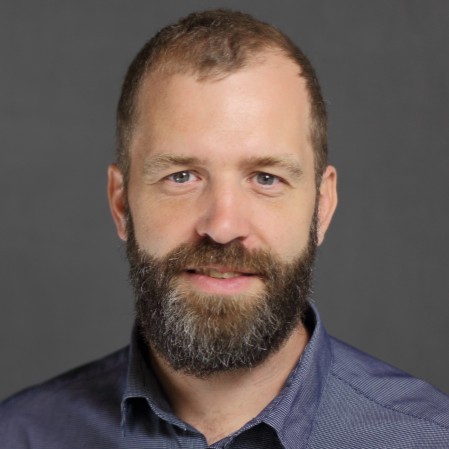
Danny Wadewitz
Danny Wadewitz, is a structural engineer with over sixteen years of experience solving difficult problems in the aircraft industry and elsewhere. He began his career as a stress engineer at Rolls Royce, and is currently a calculation Engineer and Member of the Executive Board at a Swiss engineering consultancy AeroFEM.
Take a listen to a previous episode of the Engineer Innovation Podcast: Engineer Innovation: Engineering Simulation: What’s Hot in 2024? on Apple Podcasts
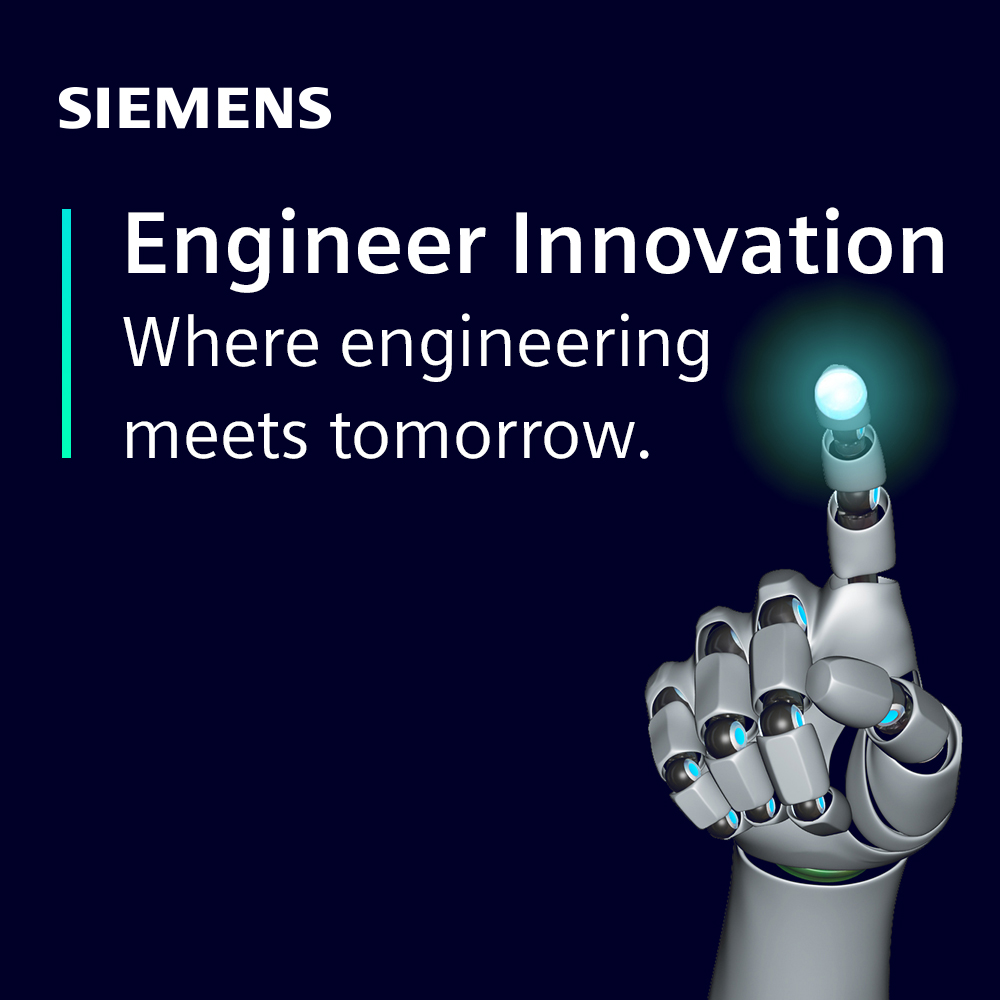
Engineer Innovation Podcast
A podcast series for engineers by engineers, Engineer Innovation focuses on how simulation and testing can help you drive innovation into your products and deliver the products of tomorrow, today.