How Does Siemens Enable Industry Manufacturers to Become Leaders?
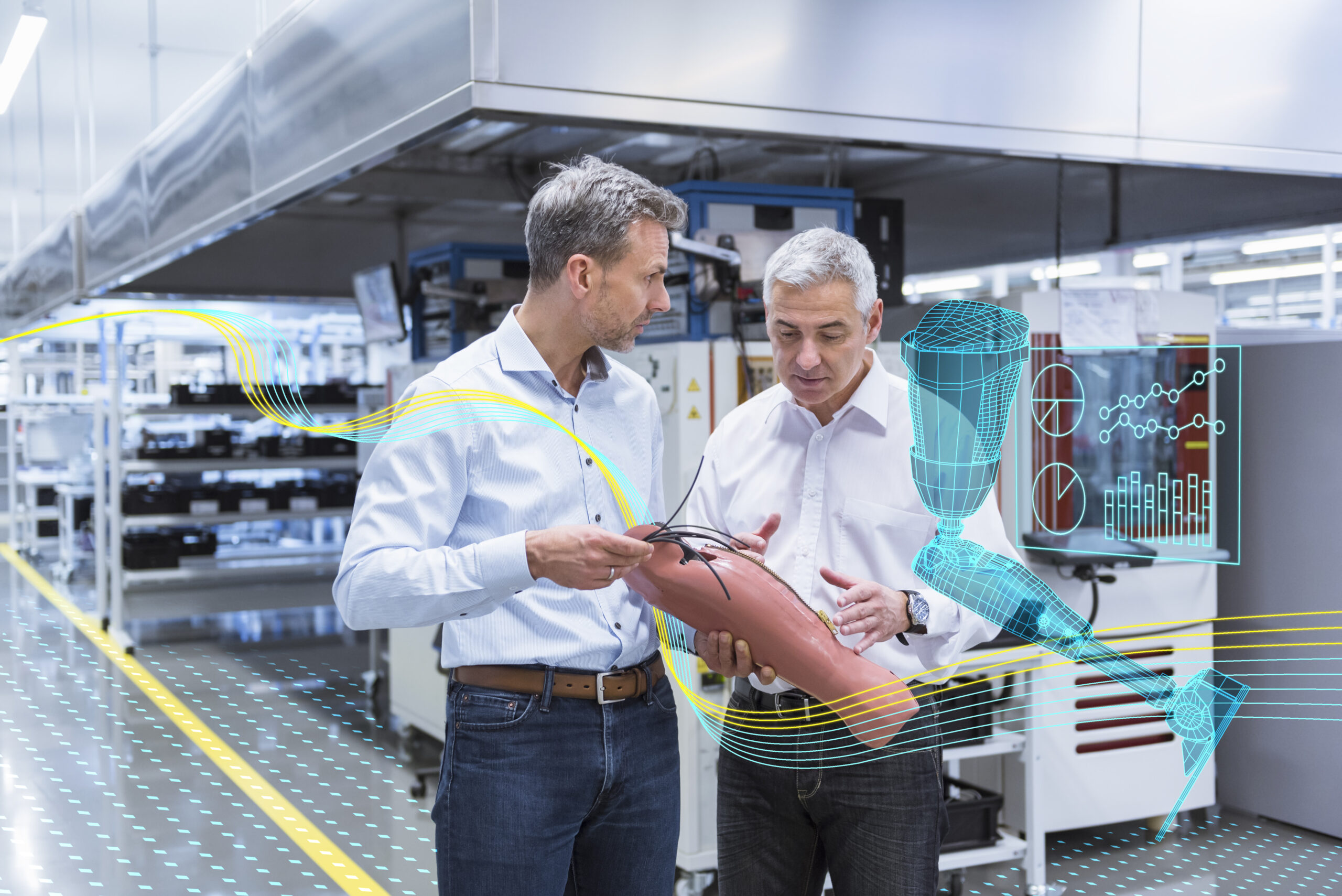
Digitalization is helping companies leverage the data that is already available to them to create better products and become more agile. It is expected to play a bigger role in the future as companies seek new ways to gain a competitive advantage and unlock new opportunities. With the right roadmap to digital transformation, businesses that embrace it will be able to maximize the output from assets that are already available to them.
In this 10-part series, we’ll focus on the impact smart digital manufacturing is having and what to expect from it in the future. We’ll invite experts from different industries to share their experiences with digitalization. This series will shine a light on the road ahead for industries that are willing to embrace change brought on by digital transformation.
I’m your host, Bettina Pruemper, with Siemens Global Marketing and, in this first episode, I’m joined by Dr. Raffaello Lepratti, he is the Global Vice President of Industrial Manufacturing Cloud at Mendix and former Global Vice President of Manufacturing Operations Management, Business Development, Segment Marketing at Siemens Digital Industry Software. In this episode, we’ll discuss smart digital manufacturing and cases where it has been successfully applied.
Tune in to learn more about the role digitalization is playing in helping companies solve problems and unlock opportunities, as well as the resources used by manufacturers to gain a competitive advantage and become leaders in their industries.
Bettina Pruemper: Hello and welcome to the first episode of The Voice Of Smart Digital Manufacturing; a 10-part industry podcast dedicated to the industries of tomorrow and how they can be enablers of fundamental innovation and disruption; a place that brings the promises to allow today’s listeners to meet tomorrow’s innovation. I’m Bettina Pruemper, and I’m your host with Siemens Global Marketing. Today in our first episode, we start our journey by discussing how Siemens enable industry manufacturers to become leaders. We will be introducing you to the idea of the smart digital manufacturing. As you might imagine, the digital transformation is one of the most fundamental drivers of disruption ever, and at the same time, a unique opportunity to shape our future in this age of rapid changes and unprecedented innovation. So, what does smart manufacturing mean in the industry 4.0? With increased complexity everywhere, what does it mean to provide your First Time Right innovation to market? Some of these questions will be answered in today’s episode. But first, let me introduce you to today’s special guest, Raffaello Lepratti. He is the Global Vice President of Manufacturing Operations Management, Business Development, and Segment Marketing at Siemens Digital Industries Software. And he recently joined the manufacturing industry cloud team. Welcome Raffaello, thanks for taking the time to talk to us about smart digital manufacturing and its application to the industries of the future.
Raffaello Lepratti: Hi, Bettina. Thanks for having me here.
Bettina Pruemper: Before we dive in, could you please share a little bit about your background and role at Siemens?
Raffaello Lepratti: I come actually from the industry background. And after the academics and, actually, the engineering degree that I achieved, I was spending the first years in the automotive industry. And actually, that was my first experience in the industry that I got. And I joined the company, Siemens, actually, 15 years ago, which is quite a long time, I have to say. Still having a great motivation because I was rotating in different responsibilities and jobs across different countries. So, I was actually making experience in R&D but also in Product Management. And then afterwards, I basically saw that most of my motivation was more in the sales, marketing, business development kind of roles. Here, I was starting working more close to the automation business, and then when the software and all the discussion around digitalization came up, I got an opportunity to join the software business within Siemens. Now, since 2014, I’m working there and I’m quite glad that we could build some of the cool things that we’re now having in the market.
Bettina Pruemper: Sounds like you have a lot of experience. So, before we shift onto how industry manufacturers can become leaders through smart manufacturing, I think it makes sense to first define digitalization by clarifying its role.
Raffaello Lepratti: That’s a good question. It’s a so-called $1 million question. It’s not easy to answer. So, in a nutshell, digitalization means a lot of things, but I think in the center is the way we’re smartly connecting data from anywhere, any domain of company to another domain. What I mean by that is, whatever is happening in the product lifecycle – from the idea of a new product to its design to the delivery to the market – there is a lot of things happening, and there is a lot of data created, a lot of transactions, events, also alarms if you look at the manufacturing really where the production is taking place. So, it’s all about whenever we have something happening, how smartly I can identify whether this created data is of a direct-indirect impact for anyone else in the ecosystem? Is it kind of an intelligent mechanism allowing to link something which is happening somewhere in some stage, in some part of the organization of a company to having a relevant job that might be impacted by that data? So, that’s what I see digitalization; making a company more agile, much more able to cope with challenges as we are experiencing with the unprecedented time that we’re going through, making to make the company much more agile and able to react to those events.
Bettina Pruemper: Now, as we all have a common definition of the role of digitalization, I would like to focus on the trends and challenges. Raffaello, what are the major trends and challenges which are shaping the manufacturing industry today?
Raffaello Lepratti: Thanks, Bettina. It’s not an easy answer but I’ll try to cut to the point. Maybe allow me to start with a more tangible example that is about the disruptive events. And I think we have been experienced in the last 18 months one of the most disruptive times we had. You can think about few examples and I believe every one of us knows about the ventilator story – ventilator shortage devices that were required in the hospitals and clinics. You probably recall that was a big discussion around how to produce more of those devices. And we had also, in some cases, not a request to the medical device company to produce more but also other companies outside of that industry, to start producing those devices, the ventilators. So, what that means is basically that you need to have a big level of agility in place in your organization, in order to either produce more, but even more to change the way you produce from a typical product to a new one. This impacts the way you’re organized — of course, your systems and your flow of information — because it comprises different departments, different domains from the design of the product, to the validations of your design, then everything around the product itself. So, what is the planning about capacity — the material flow, logistics — and then, of course, now on to the operational part, where you produce your product, and you have equipments you need probably to reconfigure equipment and your programs, or you need to even add or change some of the equipment. This shows the complexity that we have if we need to change quickly, rapidly, and that was definitely the example that we have out of an unprecedented time – we had experienced, again, in the recent times. And this is not an issue about the company itself; it’s an issue that is impacting the networked economy. So it’s the company and the supply chain that’s attached to this. And so, it’s about not only being able to redesign and re-engineer and produce new products; it’s about how can you get to implement a good strategy and the right strategy from a supply chain point of view? How can you inform ahead your supplier, how can you check that you’re getting the right material, the right quantity, and you identify any kind of potential quality issues that are coming along through the supply chain. Because here, we have a caveat as we’re talking about a medical device in the diagnostic industry or a medical device product, which is, of course, exposed to a lot of regulations. And I’m not saying our industry doesn’t have those regulations but it’s one of the industry with definitely a lot of regulations around the product, which has to be safe and there is zero tolerance for mistakes. So, how you’re suddenly making sure you’re pulling all your data and structure in a way that in a very effective time you’re able to produce the documents you’re required from the authority for the audit and to be successful, to pass the audit and to be able to really bring your product to market at the end. So this is, I believe, the example that might be quite tangible for every one of us. This is definitely one big challenge. So, how can we adopt to those disruptive events? And we have a lot of them. I was using probably a prominent example but there are a lot different ones. And this is the biggest challenge probably at the moment.
Raffaello Lepratti: And this is coming not as the only challenge – as the networked economy and the expectation from being a global player implies also a kind of a high complexity in the design of a product itself. Think about, on the one side, we have the expectation to have products becoming much more smarter and connected; on the other side, the expectation from people to get products that are matching to specific individual expectations. So, we’re talking about mass customization, so it’s going really to be more and more an individual product or at least to give the opportunity to everyone to order that is matching your own expectations. And this is reflecting the higher complexity in the design. So you need to take into consideration all these variables and make sure that you have a description of the product that is considering that. So, definitely one additional challenge is the complexity in design.
Raffaello Lepratti: Coming along with this is also the cost factor we have attached to the product. So, although we are expecting to get high quality and premium products, which are more and more individually produced for everyone’s need, the expectation at the same time is to get this product with an affordable cost level. So the cost pressure is getting higher and higher and cost pressure implies a lot of different aspects. The one, of course, is about efficiency — internal efficiency of products — how can I make sure that I don’t waste time, I don’t waste resources and I get to a point that my infrastructure is helping me understand quickly where I need to act and how to act and even helping collaborating in parallel different things carried out in parallel without losing time. That’s one thing. So, efficiency internally, but also the material costs. And everyone was attached to a better supply chain strategy, in the fact that you should know, depending on the seasonal facts, depending on other facts, where you can ensure you get to the high quality material or part for your products applied at the best price. So, this is definitely one of the challenges that I see in all the industry. And this is coming on top to disruptive events, and agility, and complexity of design.
Bettina Pruemper: Thanks for these three great examples, I have to say. It sounds like manufacturers have already a lot on their plate. So, the impact of the COVID-19 pandemic has created a new face on manufacturing, could you further explain that impact?
Raffaello Lepratti: Believing that manufacturing is back again, I think this was also an interview that was even, I don’t recall that the resurgence of manufacturing because manufacturing is the key of, at the end of the day, realizing what you think is the right product and is an innovative product. There is a lot to say around that. But in manufacturing, there is now a big shift in the culture. A big shift also in the way that manufacturing is perceived. I believe that COVID has given a clarity that maybe manufacture is not the commodity you need to have to realize something but it’s the central point of where the supply chain is coming where innovation needs to be realized, and therefore, is taking a much bigger and higher role now going forward again.
Bettina Pruemper: It looks like this new phase of manufacturing is forcing industry manufacturers to innovate their processes, but also they’re embracing a new normal in order to succeed in this age of industry 4.0 and digital transformation. So, I’m wondering how they can gain competitive advantage and become leaders?
Raffaello Lepratti: Well, we have learned from this experience we are doing how important is to be able to run manufacturing, to run processes also from remote. How to be sure you can not only take the control, monitor what’s going on in your production? And understand where to take a certain decision because there is a bottleneck, there is an issue that you need to solve. And imagine you’re not in a factory, you’re not in a plant, so you need to take the decision. So, how important is that you have the right data on your device, and you have the right distillation of all this big data into, what I call, smart data and into what drives the actionable insights for you? So, it’s very important. This is the new normal. The new normal is, I think, that people are much more clear that, first of all, the work from remote is a good opportunity, and that what has been developed in order to support this remote work is definitely also an advantage in terms of technology but in terms of approach for the future going forward when we will be back with the new normal. There is a set of other things that are attached to the fact that fluctuation has become much the challenge now. You cannot plan anymore to have certain people in the plant because of all the regulations, the distance they need to keep, and all that what happened recently. With that said, you need to have a smart way of combining this way of planning and scheduling your operations depending on the condition you have outside. So, there is also a year of an explosion of intelligence that happened in some of the tools that are used to plan your activities, to dispatch your activities. This is definitely one of the major aspects that I see. As well as the sense of urgency for digitalization. So, I have to say that the new normal is something that is where people are not only understanding anymore what the digitalization is important, I think people are now – and decision-makers, in particular – are having a clear sense of urgency now. They are feeling the sense of urgency to implement digitalization. There is maybe an imperative for some of them because we know that some of the industry, unfortunately, although we’re talking about digitalization in maybe 10 years, that some of the industry are, unfortunately, far behind. There is a lot of paper used, which is still fine and you can run that, but it’s representing a big constraint going forward.
Bettina Pruemper: To be honest, that reminds me of a great quote from – I think it was – Henry Ford about collaboration. Do you remember that one?
Raffaello Lepratti: Oh, yes. It was about coming together is a beginning, then keeping together is progress, and then working together is success. Well, that’s definitely valid. I mean, collaboration is what I said before; how you link the data. But what is the rule of digitalization now, that’s different. Digitalization should create a foundational enablement to have a different collaboration. I mean Henry Ford, at that time it was about mass production – how you’re producing a serialized assembly plant, for example, where people were collaborating and everything was organized differently, that was on-site, side by side. Hre’s about enabling collaboration in a totally different way. But what Henry Ford was saying is definitely still valid.
Bettina Pruemper: Exactly. So, unfortunately, we are already nearing the end of today’s episode, but I can promise there are many more to come, Raffaello. What can our listeners expect in our upcoming episodes?
Raffaello Lepratti: It’s important – and I’ve been touching this while talking to you – that digitalization is an approach, is an evolution of the industries but what matters more and where the questions are coming up is how is really the value of the digitalization in different industries or sub-industries. So, we’re gonna see, we’re gonna have some experts talking about our experiences and our developer position and what we’re doing for specific industries. So, one of them will be the medical device and diagnostic, but machinery is another one and electronics, and we will have a number of those podcasts that will allow also specific audience to understand maybe their needs of a specific industry or, again, sub-industry. Then we will also talk about more technologies as where, of course, we are coming from and how this technology can help more enable and implement the digitalization or a digital transformation in those industries. We are going also to talk about some new approaches that we’re taking about how you combine and making sure that the collaboration is also being enabled. One of the typical examples is how you collaborate between engineering design and manufacturing design. So, we are going to focus on what we call closed-loop manufacturing, which is the way of basically exchanging data from engineering to manufacturing and back in order to better address change requests, better address any kind of issue deviation that we need to change because designing a product is one thing, realizing the product you, are going to experience maybe some deviation and you need to capture this depending on the industry, the frequency of the request are higher or lower but the tools need to talk to each other, they need to allow to this collaboration despite there is a wall and there is a geo difference between a fab and an engineering design department. Lastly, of course, what I’d like to mention is the rule of low-code/no-code technologies with Mendix within Siemens, since two years, a powerful mean in order to accelerate a lot of those transformation roadmaps industry have, the customers and manufacturer has. This is about really smartly linking existing assets with new assets with our software assets is about personalized a lot the way you assess data and to take decisions creating apps. But in particular, this is also the way to expose everyone’s experience in the daily job through an app to all the rest of organization, because as soon as you’re creating an app, you have it ready for sharing with our community. That’s why with Mendix we’re looking forward not only to help accelerate the digital transformation roadmap of our customers and manufacturers, but also a way of bringing the specific knowledge and exposing this into a broader developers community. And we are looking at increasing there more and more going forward.
Bettina Pruemper: Thank you so much, Raffaello, for taking the time to talk to us.
Raffaello Lepratti: You’re welcome. It was a pleasure for me to have spent some time with you, and it’s important we talk about these things and we talk about the experience we’re doing. So, thanks for inviting me here.
Bettina Pruemper: And of course, I’d like to thank all of our listeners. Thank you so much for listening to this episode. If you enjoyed it and you want to stay up to date with the latest digital industry stories, click the subscribe button and leave us a review and rating to help us spread the message of these extraordinary visionaries. We have recorded over 10 episodes and we want to bring you more exciting content just like this. In the meantime, we will be working hard on putting together episodes for your auditory pleasure. Also, for further information, you can visit us online@siemens.com and use the contact section to reach out to us. This is The Voice of Smart Digital Manufacturing. And I hope you will join us again for our next podcast episode.
In this episode, you will learn:
- The role of digitalization (02:56)
- The major trends and challenges shaping the manufacturing industry today (04:44)
- The impact of the COVID-19 pandemic on the manufacturing industry (11:38)
- How can manufacturers gain competitive advantage and become leaders in their industries (12:38)
- A quote from Henry Ford, still valid today (15:41)
- What to expect in the upcoming episodes. (16:47)
Connect with Dr. Raffaello Lepratti:
Connect with Bettina Pruemper:
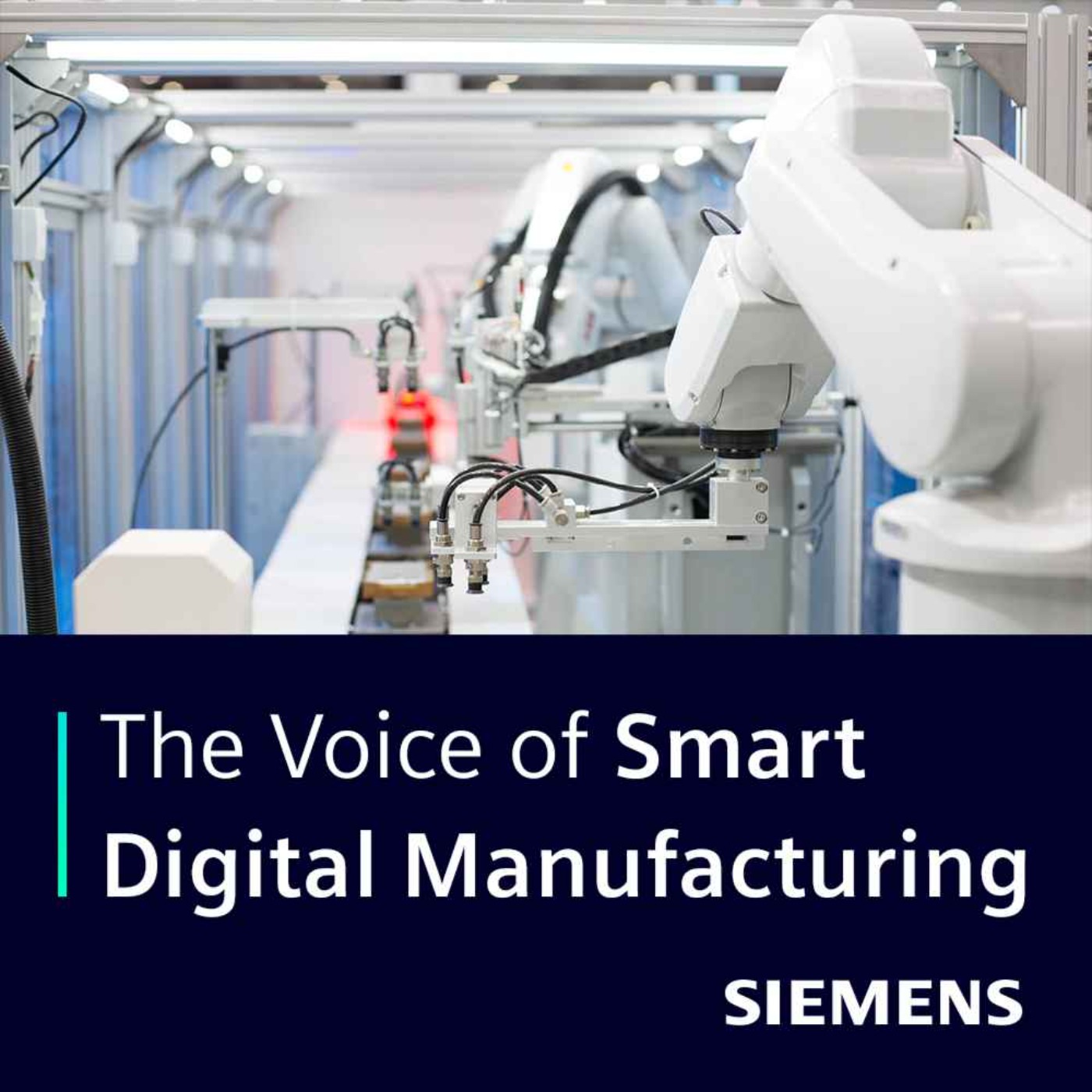
The Voice of Smart Digital Manufacturing Podcast
The Voice of Smart Digital Manufacturing is a podcast dedicated to the industries of tomorrow. Throughout 10 episodes, we will invite industry experts to share their experiences on how Siemens enables industry manufacturers – from Medical to Electronics – to become leaders, by leveraging the digital infrastructure to accelerate growth and innovation to market while lowering the cost. This series will shine a light on the road ahead for industries that are willing to embrace change brought on by digital transformation. Hosted on Acast. See acast.com/privacy for more information.