Advanced Planning and Scheduling for Industry 4.0
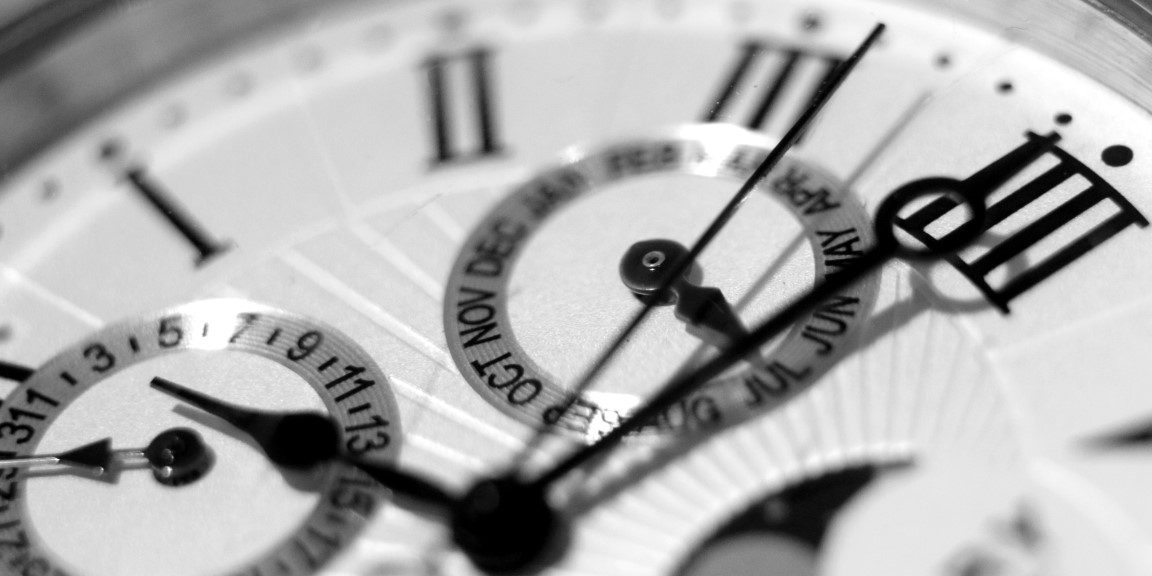
Industry 4.0 initiatives are pushing manufacturers to enhance overall production processes and deploy a multitude of cloud-based solutions. And with new manufacturing and supply chain challenges brought on by COVID-19, forward-thinking executives are turning to Advanced Planning and Scheduling (APS) software to lower costs, increase productivity and gain cash flow. For early APS software adopters, this represents a substantial opportunity to rise above the competition and realize the benefits before APS software adoption doubles the market to $2.9M by 2028.
Common supply chain challenges
As a Siemens Digital Industries Software partner since 2013, NEO Engenharia de Produção (NEO) helps clients address pressing supply chain challenges with Siemens Opcenter™ APS technology, including delays in material deliveries and stockouts, long production setup and waiting times, and high inventories due to long lead times in sourcing and processing raw materials. Our team finds that while management is aware of the challenges, it’s typically the supply chain analysts and process and production control coordinators that rely on legacy or inadequate solutions who suffer the most without access to APS software. In particular, we have seen many of them struggle to overcome gaps and limitations within legacy manufacturing resource planning (MRP) solutions.
MRP/MRPII solution limitations
MRP was developed in the 1960s before computers dominated the industry and was followed in the 1980s by MRPII as a software solution. Designed for inventory control, bill of material processing and elementary scheduling with an objective of maintaining low inventory levels throughout the planning, purchasing and delivery, it’s still in use today. MRP solutions lack functionality that APS offers such as taking capacity into account for calculations. As such, desired results can be impossible to achieve due to data integrity, built-in manual assumptions on lead times, and unrecognized challenges with manpower as well as machine and supplier constraints. Simply put, Opcenter APS is a superior solution for manufacturers — especially those in consumer goods where sequencing based on attributes are critical. A common situation when processing allergens, where cleanouts and washdowns are required between processing. But also, when producing low-volume, high customization products such as those made-to-order.
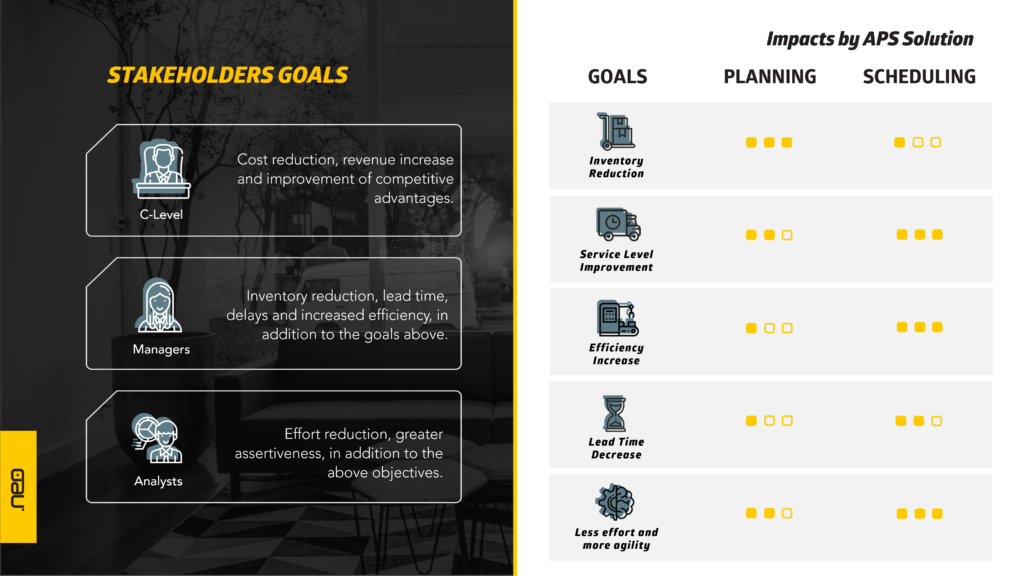
The importance of historical data for production planning
In traditional manufacturing processes, production decisions are made the planning stage. This is where choices are made about which items to produce and how often based on knowing which products will be impacted by capacity issues and mitigating any impact of potential overstocks and disruptions to the release of the product. When this detailed step is missed, the most common result is higher inventories of some products and a lack of inventory for others. With APS in place, planning takes capacity into consideration to generate healthy stock levels and mitigates lost income from back-ordered, out-of-stock items.
APS also allows seamless capacity adjustments for near and long-term cost reductions while continuing to meet demand by leveraging historical information about demand and influencers such as seasonal changes in the product mix, variations and shifts, and changes in production processes that impact decision making. With APS supplying information, better decisions can be made about capital investments in machines before they end up sitting idle, or unintentionally purchasing fewer supplies than needed to fulfill demand. In essence, capacity planning functions drive better decision-making that leads to significant cost savings across the supply chain.
Synchronization improves production scheduling
Advanced programming rules set within APS create better synchronization between production and operations that results in reduced setup, wait, and production times. As a rule of thumb, a 30 percent reduction in lead-time represents up to a 22 percent reduction in safety stock levels. It’s a correlation that makes sense considering faster and more streamlined restock production schedules result in more efficiency and reduces the need to keep large volumes of stock on hand.
APS for production scheduling provides visibility weeks or months into the future with great accuracy whereby teams can see current production that is running late alongside any at risk of being late which allows time to recalibrate processes and minimize or eliminate predicted delays. The addition of production sequencing in APS also allows for advanced knowledge of when production operations should begin and when raw materials need to be made available which provides actual dates for purchasing that facilitate supply acquisition as close as possible to production — improving available cash flow.
Top considerations for APS deployment
At NEO, our consultants help customers build the right strategies for successful APS deployments. This includes a digital-first mindset supported by the people, KPIs, processes and technologies currently available. In doing so, we find implementations are better able to leverage existing assets, workflows and expectations without adding equipment to achieve the desired results. While some industries remain fearful of implementing APS solutions due to concerns about process readiness, a major benefit of strategic deployments is how APS evolves organizational processes even when starting with the most basic data inputs — such as bills of material. When considering APS, think about the solution as progressive whereby cost savings, productivity and cash-flow benefits naturally and continuously improve as the technology is utilized, people are trained, best practices are followed, and data is added. For more information on this process and APS, in general, please read this article.
About Marcel Wenzel Meyer and NEO
Marcel Wenzel Meyer is the managing partner at NEOEP Engenharia de Producao LTDA (NEO), a Siemens Digital Industries Software Expert Partner specializing in production planning and scheduling technology and production engineering. With extensive expertise in supply chain processes and technologies, planning, programming and production control systems, NEO is headquartered in Porto Alegre, Brazil with a branch in Portugal and plans to expand into Europe and the Americas in the next few years.