Revolutionizing Manufacturing with Integrated Intralogistics and MES
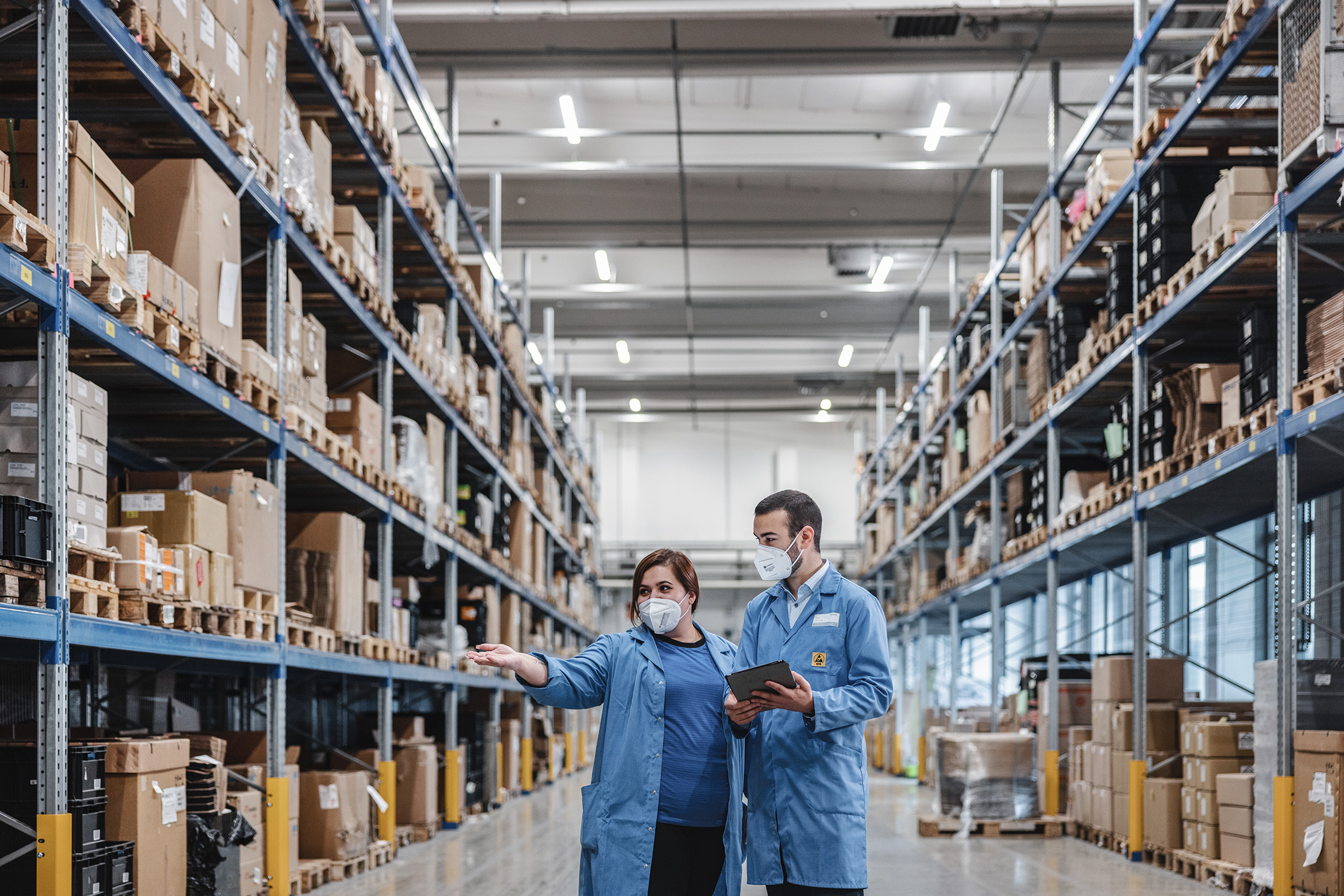
Live webinar: A detailed insight for logistics managers
The manufacturing industry’s landscape is ever evolving, with increased automation, digitization, and lean manufacturing principles at the forefront of innovation. As the pace accelerates, the role of logistics managers becomes increasingly challenging, especially in navigating the intricacies of production and delivery processes. The integrated approach of intralogistics and Manufacturing Execution Systems (MES) has emerged as a promising solution to these complexities, boasting benefits that could significantly improve manufacturing operations.
The role of intralogistics and MES
Intralogistics involves the management of material flow within a facility, encompassing warehousing and internal transport. Conversely, MES deals with the execution of manufacturing operations. The intertwined nature of these two systems is critical in facilitating smooth operations within a manufacturing setup. However, the absence of a streamlined integration can often lead to increased redundancy, duplicated work, and a larger margin for error.
An aligned and integrated approach to intralogistics and MES fosters a unified system configuration, which drastically reduces redundancies and boosts overall operational efficiency.
Real-life challenges of a logistics manager
A logistics manager is the nerve center of a production facility, responsible for managing a vast array of functions, from material procurement and storage to overseeing production schedules and dispatching goods.
One of the major challenges is maintaining accurate, real-time inventory levels. Given the dynamic nature of production schedules, keeping track of materials, their quantities, and their respective locations can be daunting. This is further compounded by the risk of miscommunication and human error, which can lead to significant delays and increased costs.
Moreover, logistics managers are tasked with ensuring smooth and timely material flows. Any disruption in the production line due to unavailability of materials can have a domino effect on the entire production schedule.
Lastly, the need for lean manufacturing – reducing waste while maintaining productivity – adds another layer of complexity. Balancing efficient production with minimal inventory is no easy task. This is where the aligned and integrated approach of intralogistics and MES can truly shine.
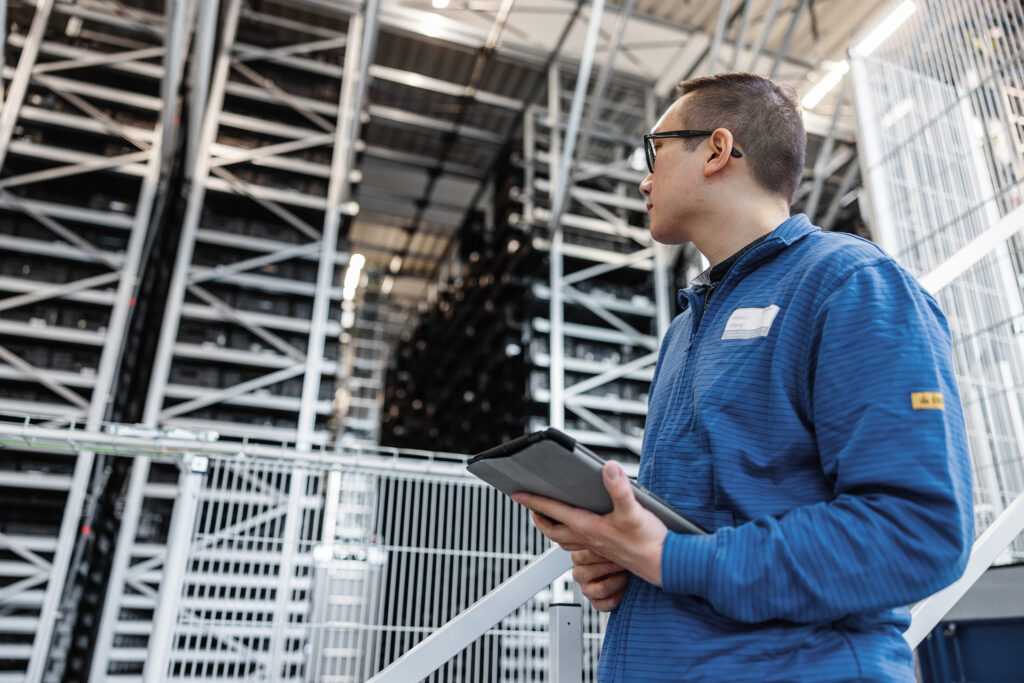
Opcenter IPL Scheduling Engine: a paradigm shift
Central to this integration is the Siemens Opcenter Intra Plant Logistics (IPL) Scheduling Engine. It closely monitors the production process in real-time, enabling it to generate timely replenishment and commissioning orders. The engine considers product data, operational status, material usage, and production waste to create a realistic forecast of material requirements. This method aligns with lean manufacturing principles and significantly reduces waste and inefficiencies in the production process, helping logistics managers maintain lean inventories without impacting production.
The evolution from traditional to IPL Just-In-Time replenishment
To better understand the benefits of this aligned approach, let’s compare the traditional manual Kanban, eKanban, and Just-in-Time replenishment processes.
With manual Kanban, logistics operators need to manage the physical inventory of each part number, typically with at least two bins. This labor-intensive approach doesn’t scale well with increasing parts or stations, leading to efficiency issues and increased risk of errors.
The eKanban process digitizes inventory management, reducing manual labor and ensuring a more efficient picking flow. However, both Kanban systems operate on an inventory surplus model, often maintaining double the necessary materials at each station. Although efficient, these systems may not perfectly align with lean manufacturing principles.
The IPL Just-In-Time replenishment model addresses these shortcomings. By synchronizing with the production schedule, it minimizes the need for excess material in the production area and supplies only what is necessary for active production. It matches material supply with production requirements, scales effectively with increasing parts, stations, and products, and significantly reduces the effort required for replenishment and material commissioning.
Material replenishment reimagined
The integrated approach to intralogistics and MES reinvents material replenishment, a task that often burdens logistics managers with complexities. The IPL replenishment process assigns a cost to each container in the inventory based on attributes such as the material’s location, status, customer, etc. The system then utilizes the lowest cost material during commissioning, ensuring consistent enforcement of business rules during the material selection process.
For example, if a company’s policy dictates using consigned material first, IPL’s Just-in-Time replenishment aligns with manufacturing execution to select the consigned material for an upcoming changeover. This complex process can handle steps automatically and optimize material flow, significantly reducing the risk of error while enhancing efficiency.
Conclusion: the integrated approach as a game changer
The integrated approach to intralogistics and MES is a game-changer for logistics managers. By increasing efficiency, better aligning with lean manufacturing principles, and improving scalability, this approach allows businesses to meet their production goals without compromising on quality or timeliness of logistics. For logistics managers struggling with the complexities of their role, embracing this approach could be a significant step towards improved operational efficiency and productivity.
Learn more about integrated intralogistics in our upcoming webinar on August 16, in which Zac Elliott will discuss current challenges in intralogistics management, show how common production replenishment flows do not scale, and demonstrate new technology used to manage intralogistics on the shop floor.