Opcenter Quality 2209 has been released!
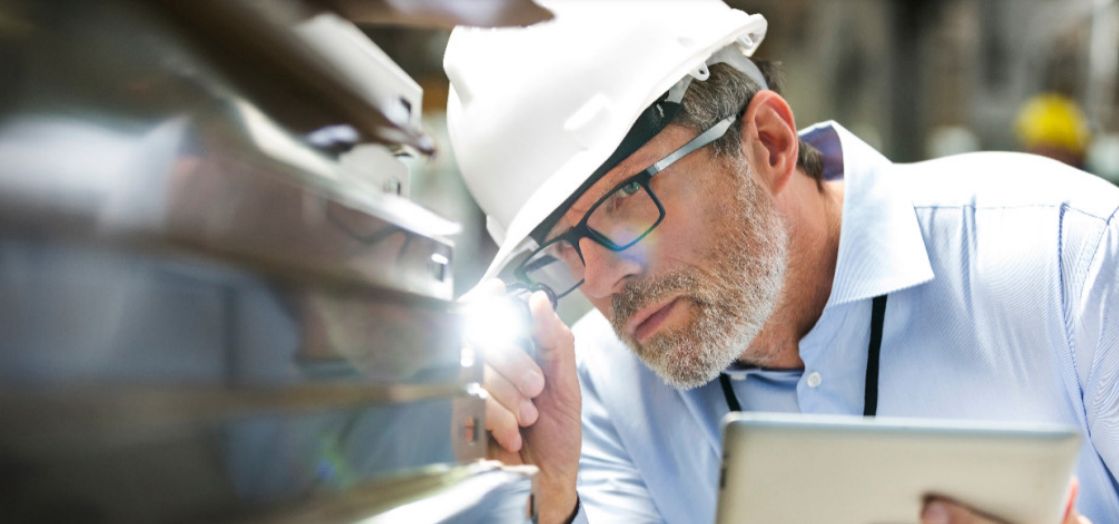
Minimize analysis deviations
Using Opcenter Quality Control enables you to pair the comprehensive digital twin with features in Teamcenter® Quality software in real-world production. Using Opcenter Quality Control supports all quality processes on the shop floor. This starts with documenting inspection results and includes controlling production processes and supporting the necessary processes that are carried out in case of deviations. This can even include adapting inspection specifications to production conditions.
To harmonize the offerings across Siemens Digital Industries Software, Opcenter Quality is being moved to year- and month-based version numbering. Version 2209 stands for the September (09) release in 2022. Therefore, version number 2209 follows version number 13.2.
Opcenter Quality 2209 brings you the following benefits:
- Minimize analysis deviations by visualizing production results and comparing them to the specifications
- Enhance the complaint management process by merging all relevant data
- Extend support of VDA requirements for PPA
- Increase FMEA and control plan capabilities
- Expand usability for gage management
- Enhance support for the supplier PPA based on VDA requirements
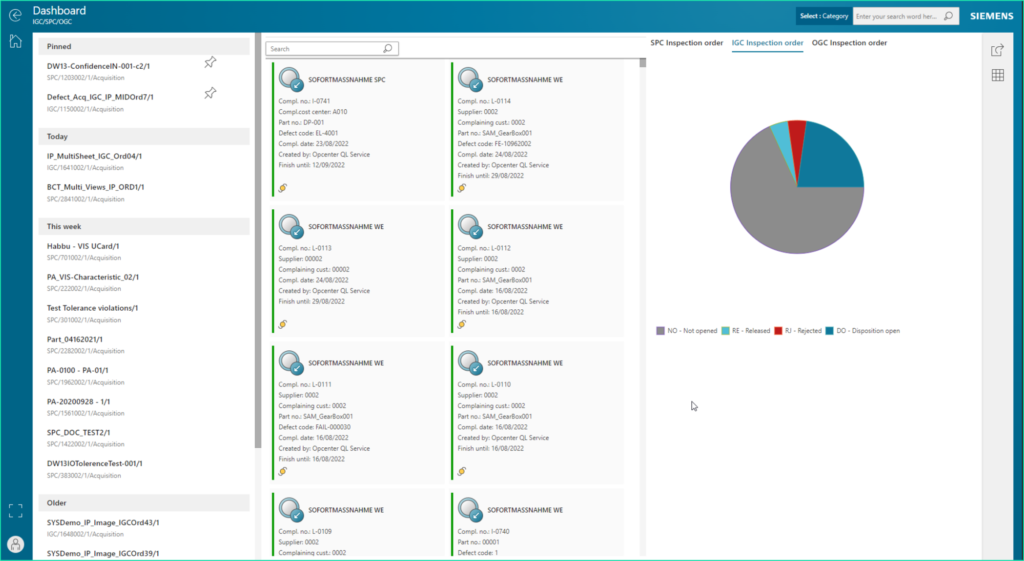
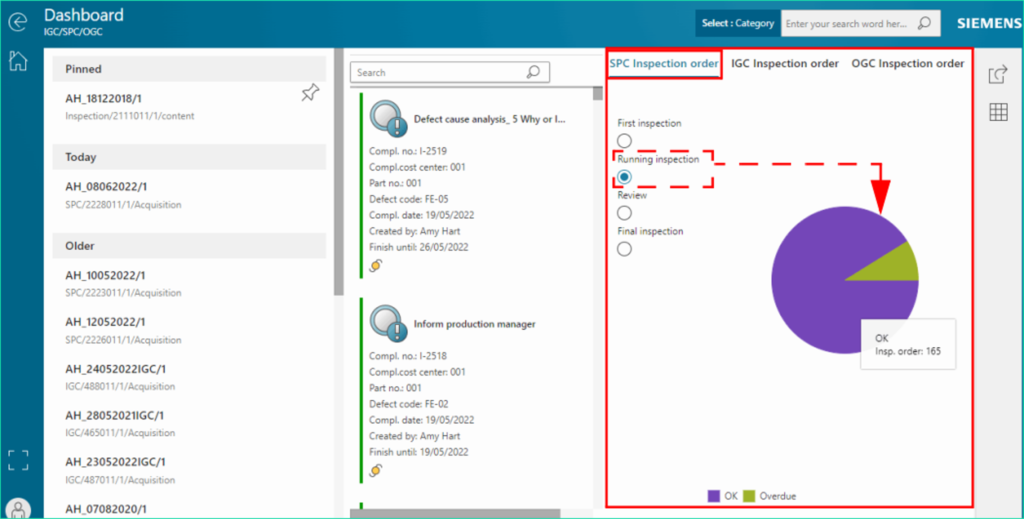
Some features:
- Support web graphical inspections for IGC, SPC and OGC
- Combine individual complaints into one complaint
- Enhance the VDA report product-related test results
- New properties on FMEA function objects
- Opcenter Quality Gage Management (CALVIN) – language configuration
- New optimized process in Opcenter Quality Portal based on smart client technology
Already using Opcenter Quality? See what’s new in version 2209, or learn how to experience the benefits of closed-loop quality for best-in-class products with our videos.
Want to learn more? Opcenter Quality is a quality management system (QMS) that enables organizations to safeguard compliance, optimize quality, reduce defect and rework costs and achieve operational excellence by increasing process stability. The integrated process capabilities (control charts, statistics, quality gates) can detect production errors to avoid further processing and shipment of nonconforming material.
We have plenty to say about the benefits and features of Opcenter Quality, but our customers have stories to tell as well. Here are three examples of manufacturers that leverage Opcenter Quality for a competitive edge:
- Miba is one of the leading strategic partners in the international engine and automotive industry. Siemens Digital Industries Software solution helps Miba streamline global quality assurance work in pursuit of zero-defects initiative. Miba uses Opcenter Quality to lay the foundation for further digitalization steps. If you want to learn more, click here.
- Pepperl+Fuchs is a global company headquartered in Germany with more than 80 foreign subsidiaries on six continents and manufacturing facilities in Germany, the United States, Singapore, Hungary, China, Indonesia and Vietnam. To digitalize and globally streamline quality-related work across all locations, the company invested in Opcenter Quality. If you want to learn more, click here.
- Merit Automotive Electronics Systems is a global supplier of complex mechatronics modules and switches to the automotive industry. Reducing the amount of paper on the shop floors and having all history data available at any time has made Opcenter Quality an asset. It delivers full control and a reliable support tool for the managers and supervisors involved in the decision-making process.
If you want to learn more, click here.
Find out more about Opcenter Quality.