What’s New in NX for Manufacturing (June 2023)
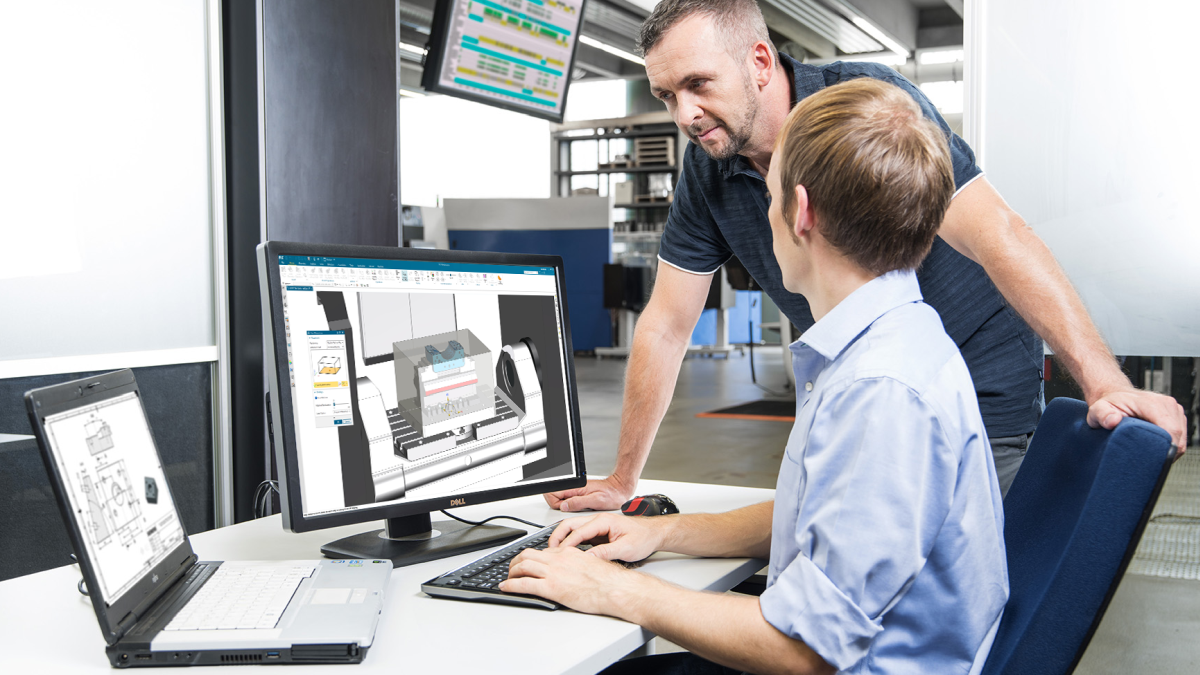
A new release of NX for Manufacturing is here! With NX 2306, you will encounter new capabilities as well as updated enhancements, enabling you and your company to reach new levels of productivity with NX for Manufacturing.
In this blog, you will learn about the latest features and product updates for our comprehensive software for part manufacturing including:
- NX CAM
- NX CAM On-Machine Probing
- NX Additive Manufacturing
- Part Manufacturing Data Management
- NX Assembly Line Planner
- NX Line Designer and Fixture Planner
What’s New in NX CAM
The Cloud Connect Tool Manager is a graphic-based interface that makes it easy for you to manage tools and components for efficient tool data maintenance in NX CAM software. Users can also import tools from vendor databases using web technology.
The easy-to-use interface and graphical design simplifies the programming workflow for defining and editing tools, requiring fewer clicks than before. Users can swiftly find the exact tools they need, saving valuable time and effort with dynamic tool preview and dimensions.
There are four display modes and two search modes for easy navigation and viewing. The intelligent search function goes beyond basic queries and can recognize multi-formulas, symbols, and keywords. Import tools directly from vendor databases and gain access to an extensive library to optimize productivity and efficiency.
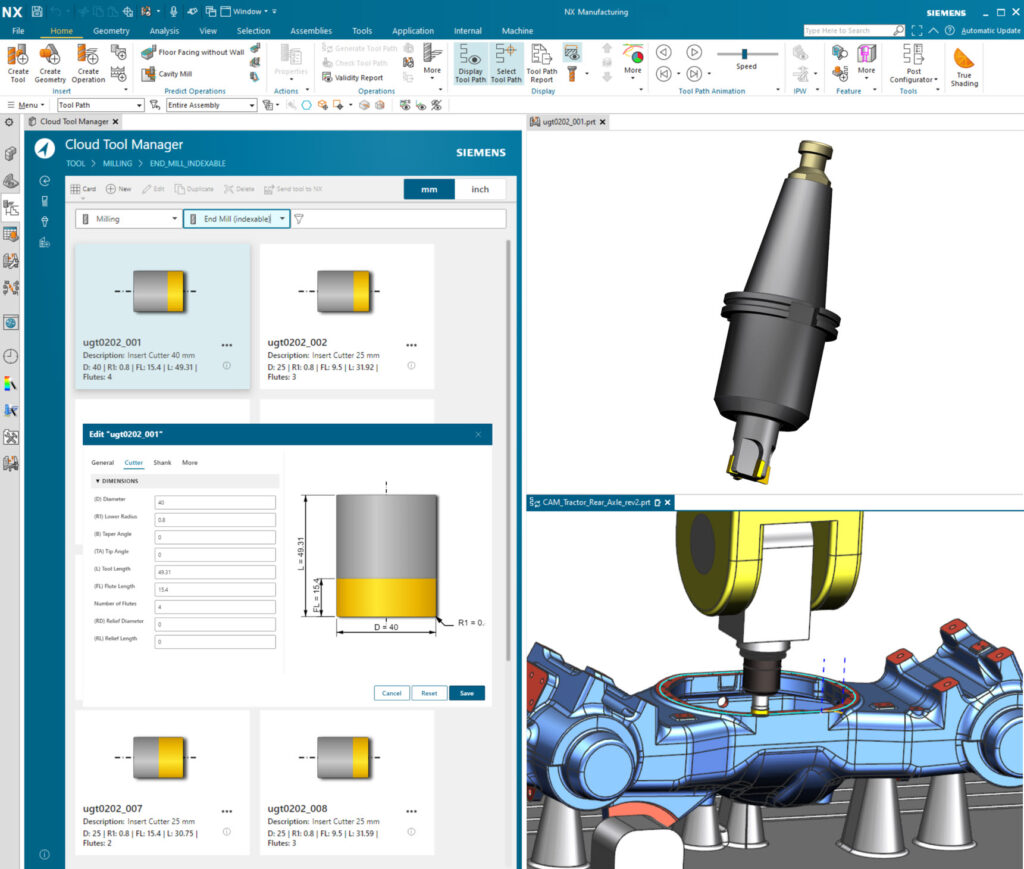
The new enhancements to the Position Part & Fixtures in Machine Context allow users to quickly and accurately position CAM setup on the machine with improved usability and visibility. For example, users have dynamic handle positioning with a bounding box or cylinder and can position part and associated fixture assemblies. Move setups dynamically instead of the machine and gain better visibility of setup in the machine tool.
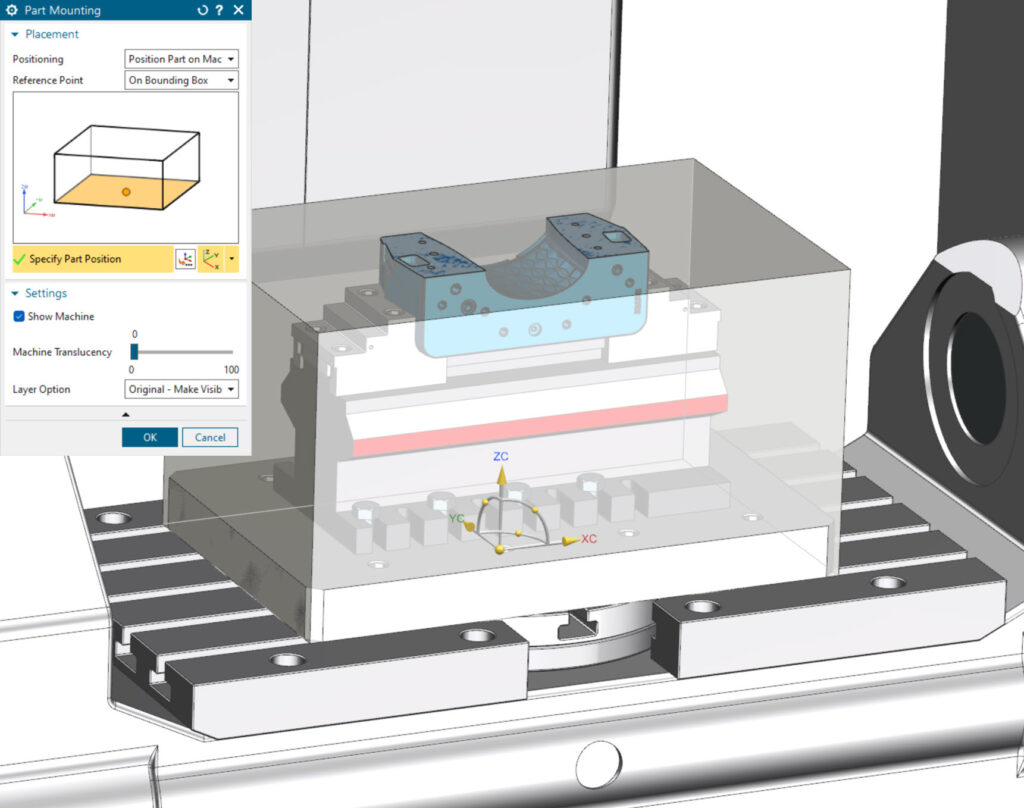
The new feature for Automatic Turning Tool Holder Collision Shape Creation provides increased process safety for holder collision checks. Users no longer need to manually specify collision shape and layer settings during the tool creation process, eliminating possible programming errors. The 2D holder shape geometry for turning tool holder is now created automatically during tool path verification.
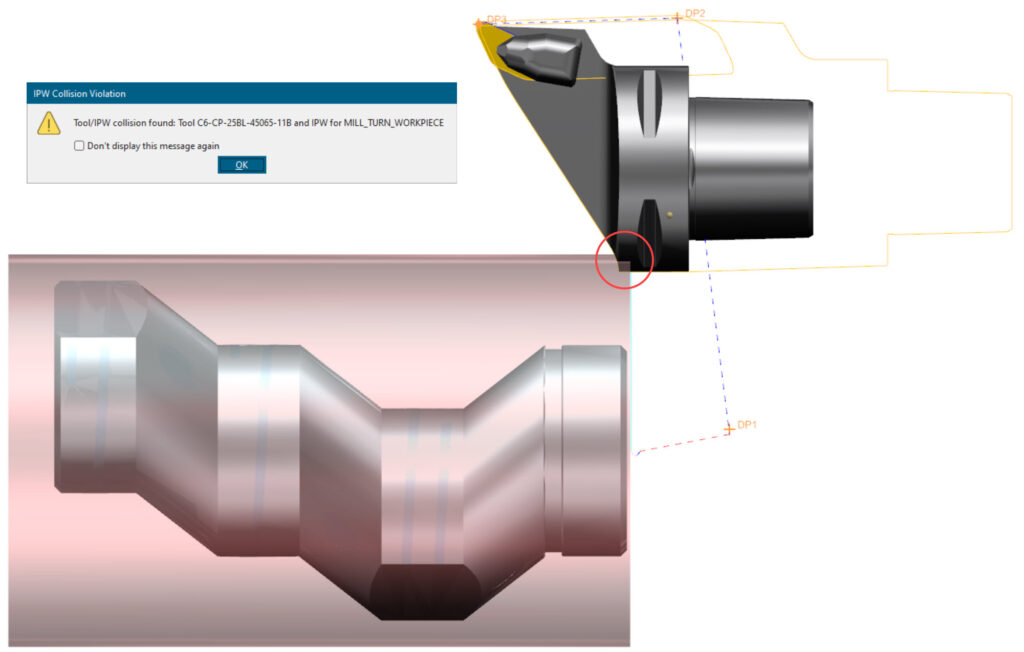
The Dovetail Mill Tool enhancement simplifies tool creation using industry naming terminology, allowing you to easily specify basic Dovetail tool parameters. Dovetail Tools supports the following operation types including Planar Mill, ZLevel Undercut, Solid Profile and 3 Axis Deburring.
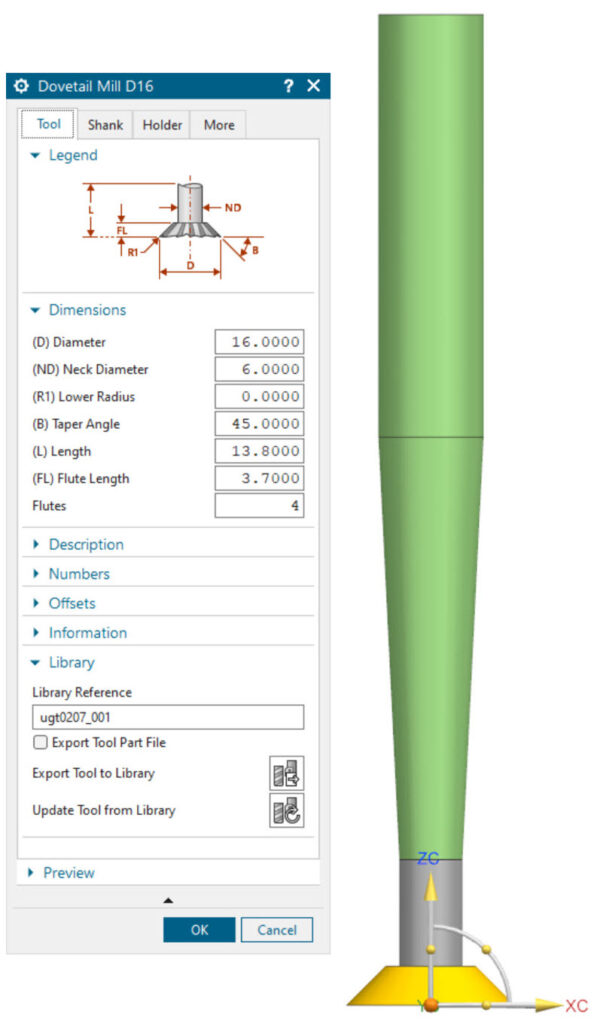
The Simplified Shank Creation is now available to easily define shank data while achieving more accurate representation of shanks. Reduce the risk of redundancies by organizing data in a multi-shank library so shank management is simplified. Define multiple step shanks by extracting shank data from 3D parts in the same way that holders are currently defined, making complex multiple step shank definitions much easier.
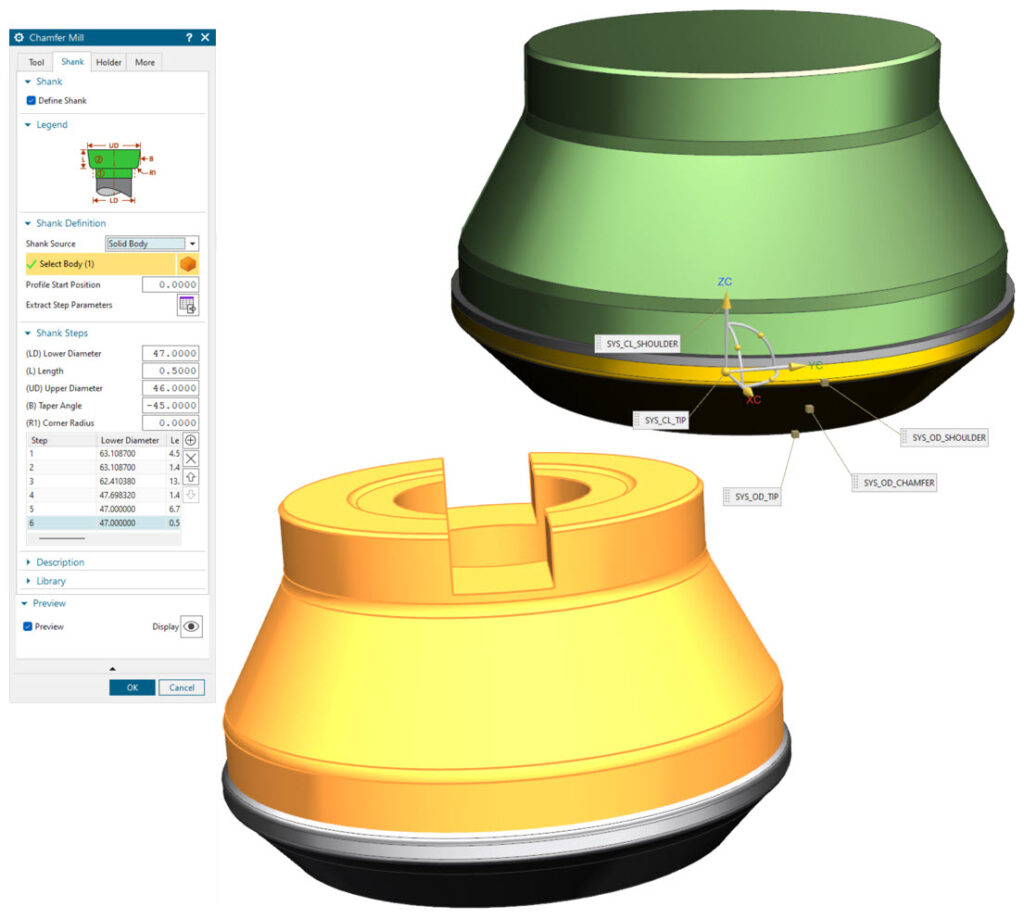
The Distance Measure with Pick on Path provides a quick way of verifying tool path related measurements. When the tool path is displayed, users can easily measure the distance between two points on a toolpath or between a point on the toolpath and a geometric object. It also facilitates the easy validation of measurements between a point on the toolpath and the cutting tool, as well as between the cutting tool and a geometric object.
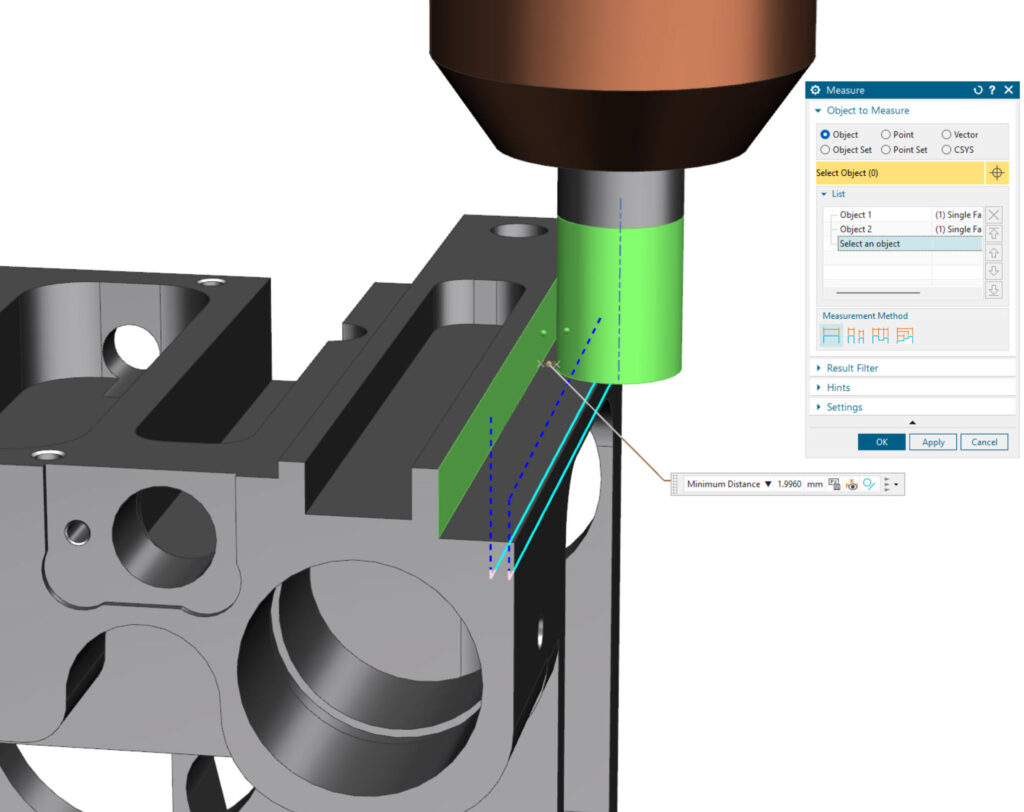
The Extract Operation Cut Area enables easier reuse of selected geometry for other operations. Users can now extract Cut Area selection from an operation reuse as a “Mill_Area” for subsequent operations.
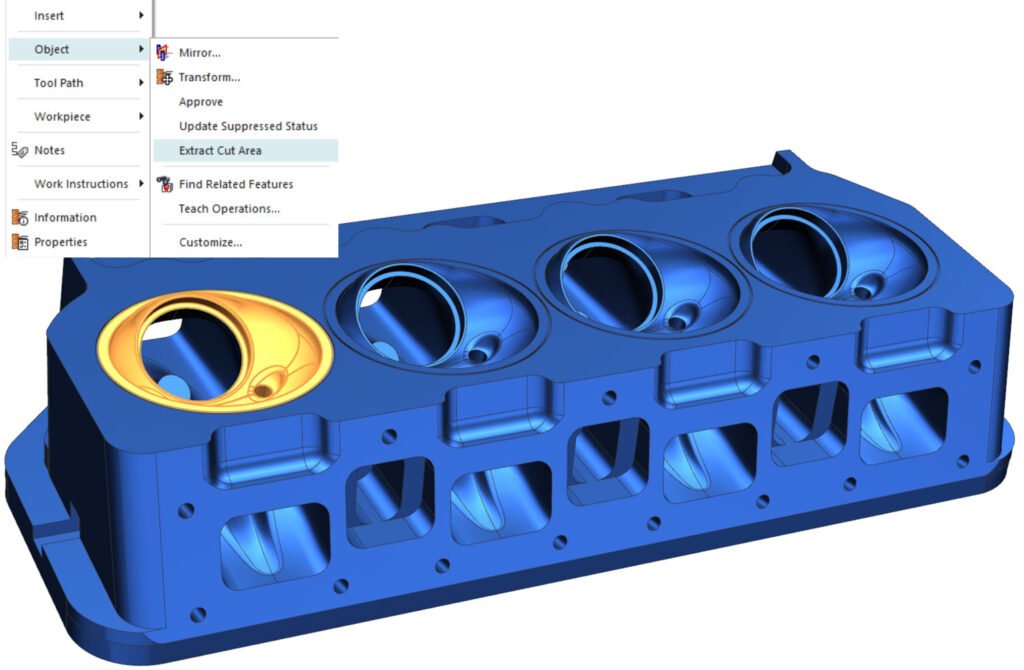
What’s New in NX CAM On-Machine Probing
Achieve precision and efficiency with NX CAM On-Machine Probing, which empowers users to seamlessly integrate measuring operations into their existing CAM program structure. Measure, evaluate and compensate for process variations throughout your machining process and enhance your quality and efficiency.
Experience a streamlined and intuitive workflow with the probing operation template conveniently located under the Probing Template. Programmers can easily access the necessary tools and functions to incorporate measurement tasks into their machining operations. This accessibility ensures that users can quickly transition between programming and measuring, optimizing their productivity and reducing machine downtime.
NX CAM On-Machine Probing provides users with a comprehensive range of possible cycles, which are intelligently based on the selected geometries. Quickly navigate and choose the most appropriate measuring tasks, resulting in a more efficient and accurate programming process.
NX CAM On-Machine Probing seamlessly integrates with real controllers, mirroring their parameter representation. This simplifies the programming process for experienced users while providing context and guidance for less experienced programmers. The toolpath of the measuring cycle can be verified via the on-board tools and represent the machine movements executed from the macro. This feature also offers a wide range of cycles for various geometries and is compatible with Siemens and Heidenhain controllers.
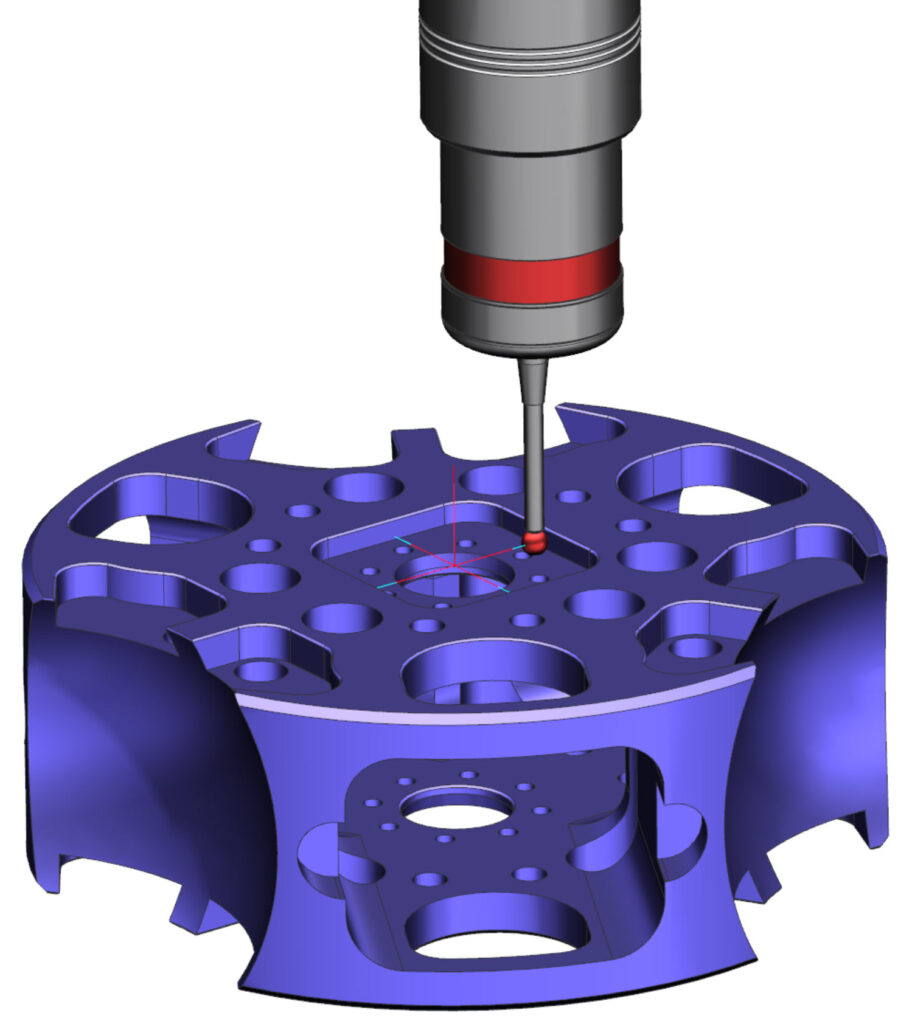
What’s New in NX Additive Manufacturing
Within NX Additive Manufacturing, you can now enclose parts within Sinterboxes. Sinterboxes are cage-like lattice structures that are created around selected parts. You can create either box-shaped or freeform sinterboxes that take the shape of the parts they enclose.
You can use sinterboxes to:
- Protect fragile parts from damage during 3D printing and also postprocessing.
- Prevent parts from getting lost, especially when you have either a large number of parts or very small parts in the build tray.
- Keep parts separated during 3D printing and postprocessing. This can prove especially useful if you have similar parts in the build tray and want to quickly and easily differentiate them (e.g. when combining orders from multiple customers in a single build).
There are three types of sinterbox structures: Grid and Rod (no design license needed), Standard Lattices, Voronoi
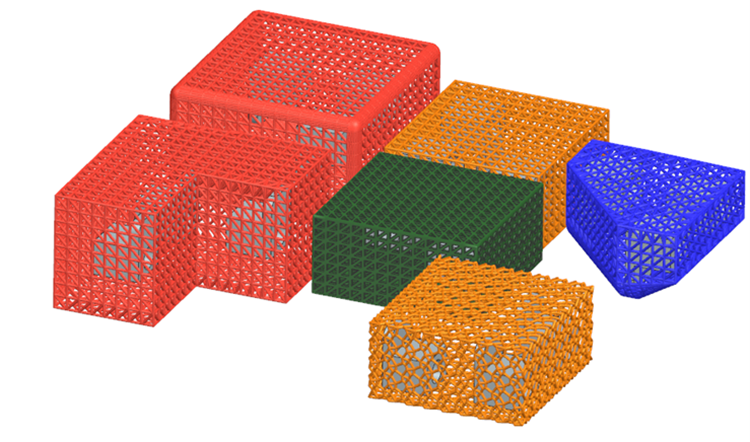
NX 2306 also includes improved support for NX assemblies within the additive manufacturing build tray. This means that when you add an assembly to the build tray, all parts and subassemblies of that assembly are automatically added as a group and the group is listed in the Build Tray panel.
You can reorder existing assemblies in the Build Tray panel by dragging them around or by Print Reorder Before or Print Reorder After commands. NX AM manages the assembly as an individual object, so when you move a part from an assembly, all other assembly members will also move. This means that assemblies can be moved while retaining the relative position and orientation of the individual members in the assembly. During nesting, the assembly will also be nested as a single object.
Also included in the NX2306 additive manufacturing functionality is improvements to the ease of use when setting up the build tray. IN NX2306, you can easily show and hide objects of a specific type like parts, supports, or the build volume in one click. This is especially useful if you have a large number of parts and support structures and you want to hide all parts, or all supports at once. You no longer need to select objects individually.
The addition of these new additive manufacturing build preparation functions means that NX2306 is the easiest to use, most powerful version of NX Additive Manufacturing to date.
What’s New in Manufacturing Data and Process Management using Teamcenter
Manufacturing data and process management enables companies to connect people, systems and machines with a digital thread.
Manufacturing data and process management have taken a significant leap forward with the integration of MRL (Manufacturing Resource Library) support for PrimeTurning Tools. This new technology from Sandvik increases CAM operation efficiency to a maximum and reduces cutting time by up to 50%. Produce an accurate surface finish, excellent chip control and better tool life.
The integration of PrimeTurning Tools into the MRL tool library delivers comprehensive management capabilities. New classes specifically tailored for all Sandvik Coro PrimeTurning products are available, allowing for seamless integration and efficient handling of these advanced tools. MRL provides an auto-mapping feature where the tool parameters and graphics automatically map from the vendor’s data to the new classes. From here, the customer can manage the components and build prime turning tool assemblies. NX CAM users can take full advantage of the new PrimeTurning tool path calculation to ensure a seamless transition from tool assembly creation to the machining process.
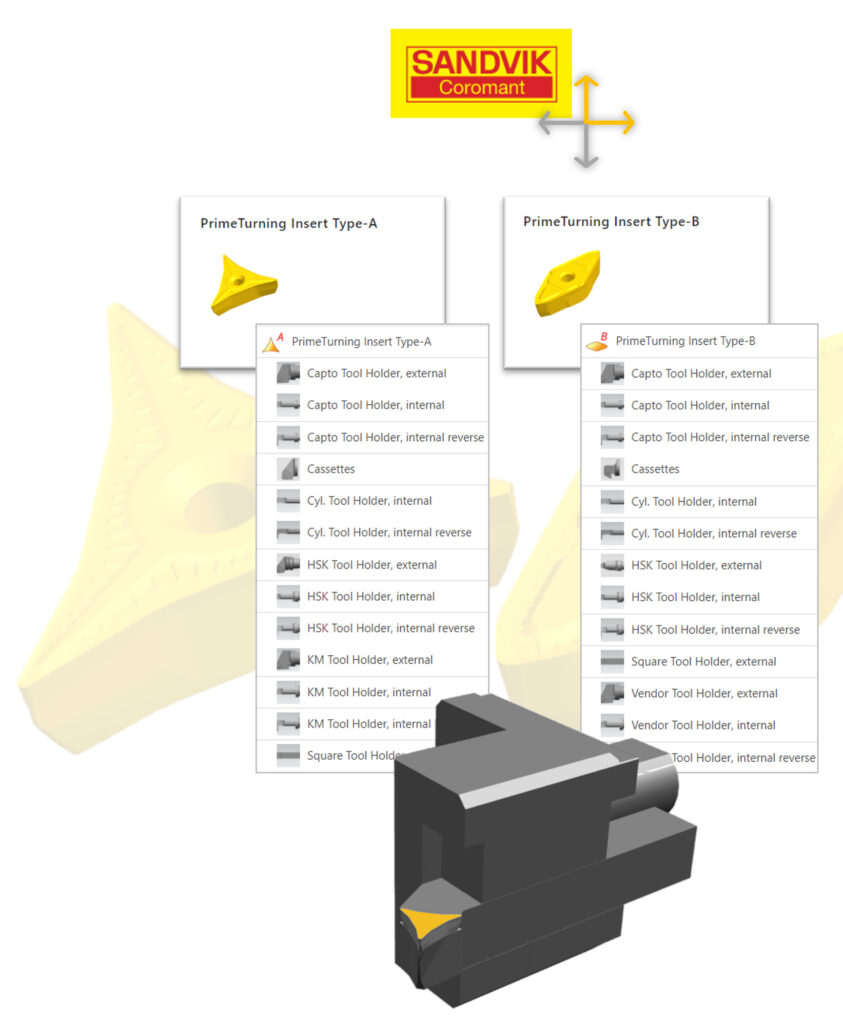
Another latest feature in manufacturing data and process management is the Enhanced devices retrieval from NX CMM, which NX CMM to retrieve all necessary resources from the MRL library, including support of the holding system to mount CMM devices and access to CMM accessories. The CMM Inspection can also be used as a stand-alone application, which ensures that all necessary resources related to CMM machines, measuring devices, and probing tools are readily available in NX.
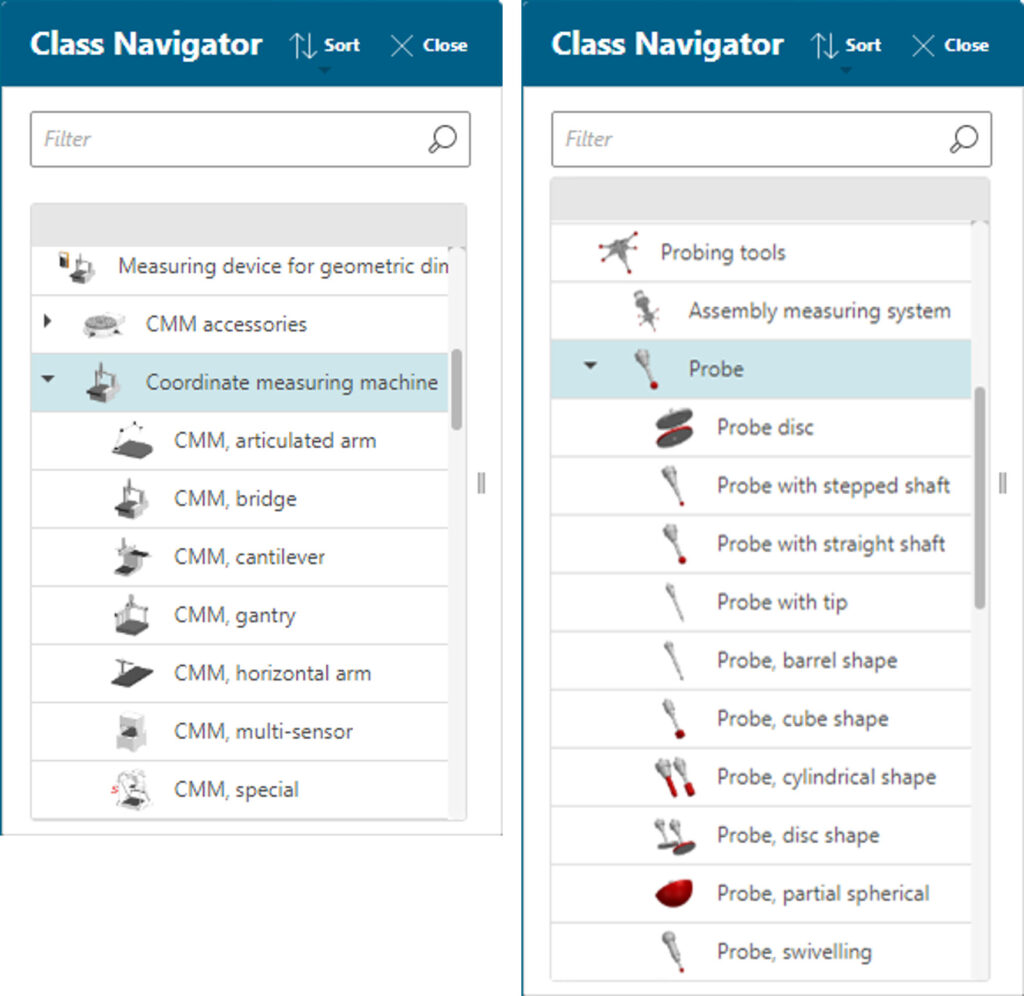
The NX CAM and NX CMM library consolidation enables access to all manufacturing resources in the combined machining application in NX CAM. Previously, CAM and CMM were separate applications in NX and users had to choose between using one or the other, with separate access to library resources for each application.
Users can now perform both tool path generation and inspection programming with a single combined application, providing a more seamless and efficient workflow for manufacturing operations and access to all required sources, including machines, devices and tools.
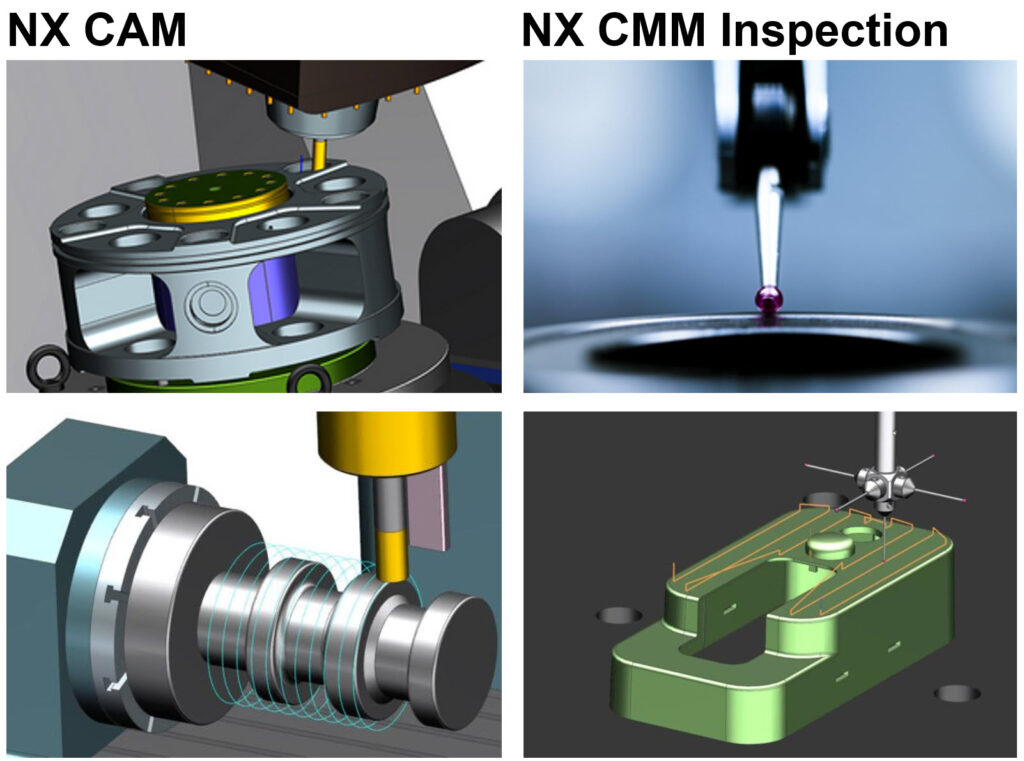
The Active Workspace Manufacturing Workspace is designed to improve productivity by providing a clearer assignment overview for manufacturing users. The Manufacturing Workspace offers a clear, organized layout where users can easily switch between the different views. Create manufacturing objects for various tasks such as CAM setups, additive print jobs or inspection operations. Optimize productivity and concentrate on daily tasks that will save time instead of searching for essential functions.
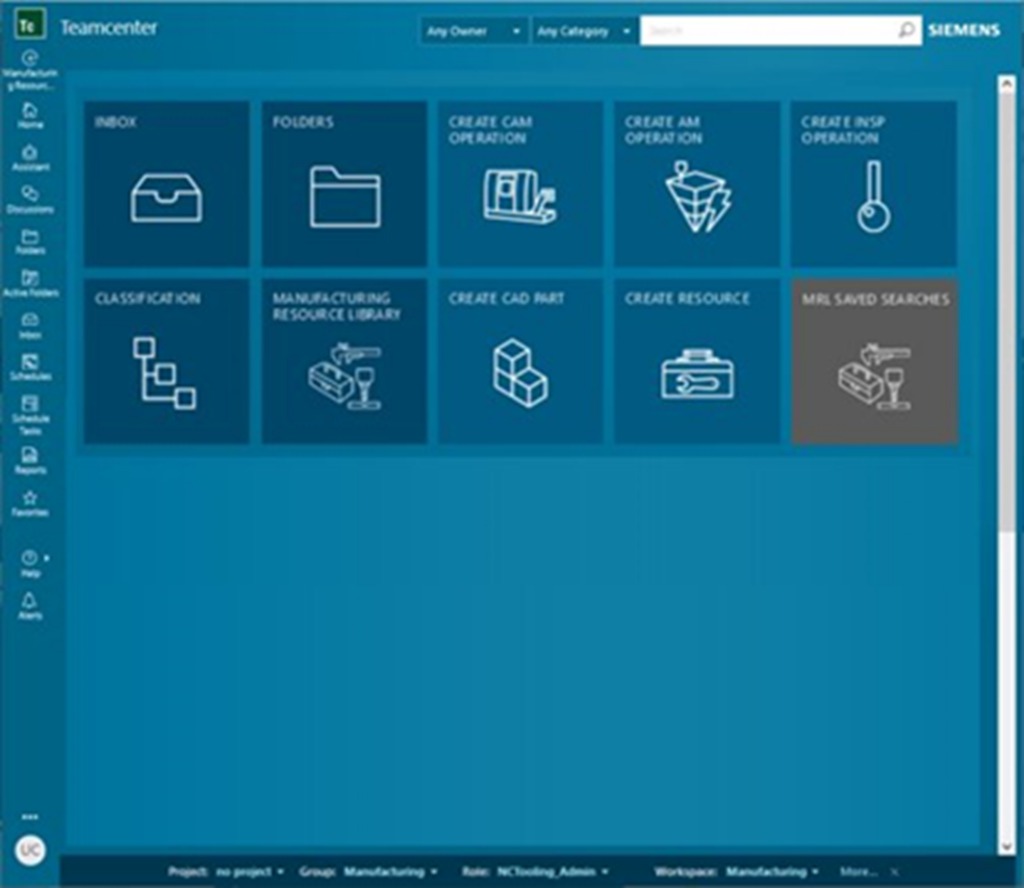
What’s New in NX Assembly Line Planner
The library of operations provides a repository of knowledge for reuse and optimization when planning station content in NX Assembly Line Planner. The operations and operation groups can be added to any process plan during station detailing and then can be adapted to the exact use case. The libraries contain a wealth of valuable knowledge, including common best practices, regional standards or plant-specific processes.
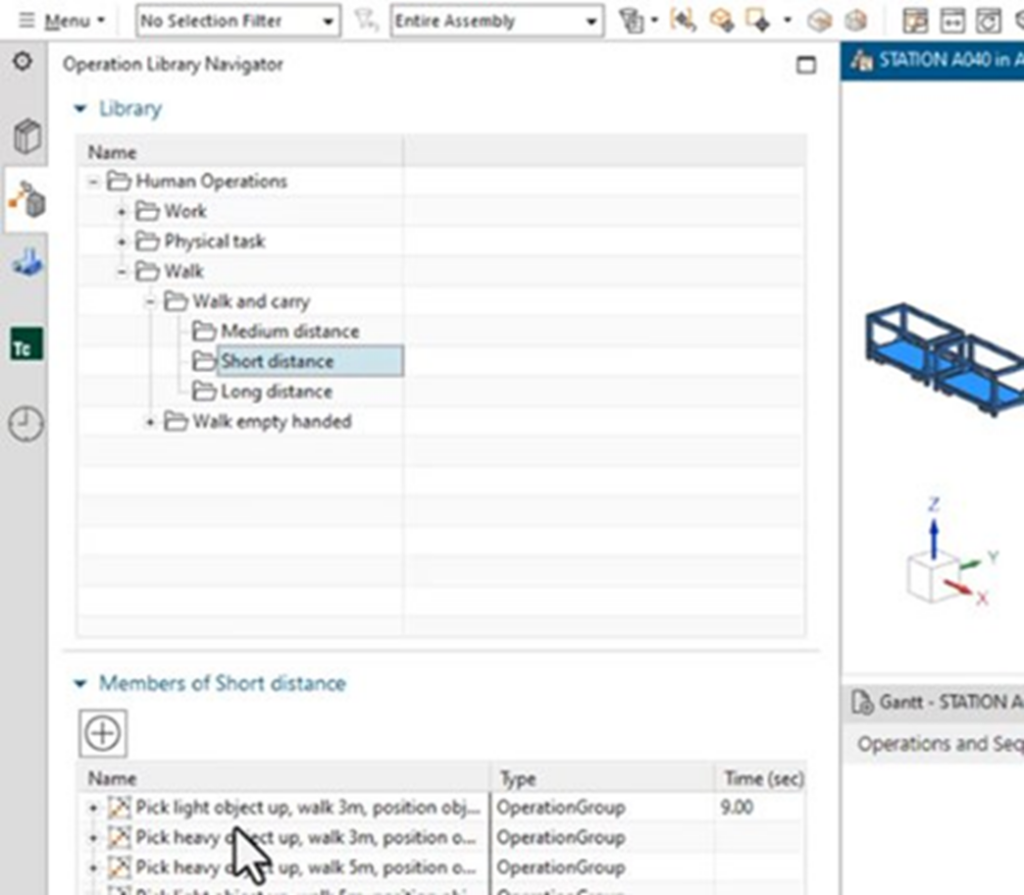
The PERT viewer has been enhanced to support multi-product assembly, providing increased functionality and visibility into the product build-up. Users now can review the actual calculated cycle time of each station directly in the PERT view to quickly identify problematic stations as well as stations with available capacity. Another enhancement is handling of images for the variants within the PERT view. Users can capture an image for each variant in every station, providing an exact representation of the product build-up for each configuration to aid in analysis and decision-making.
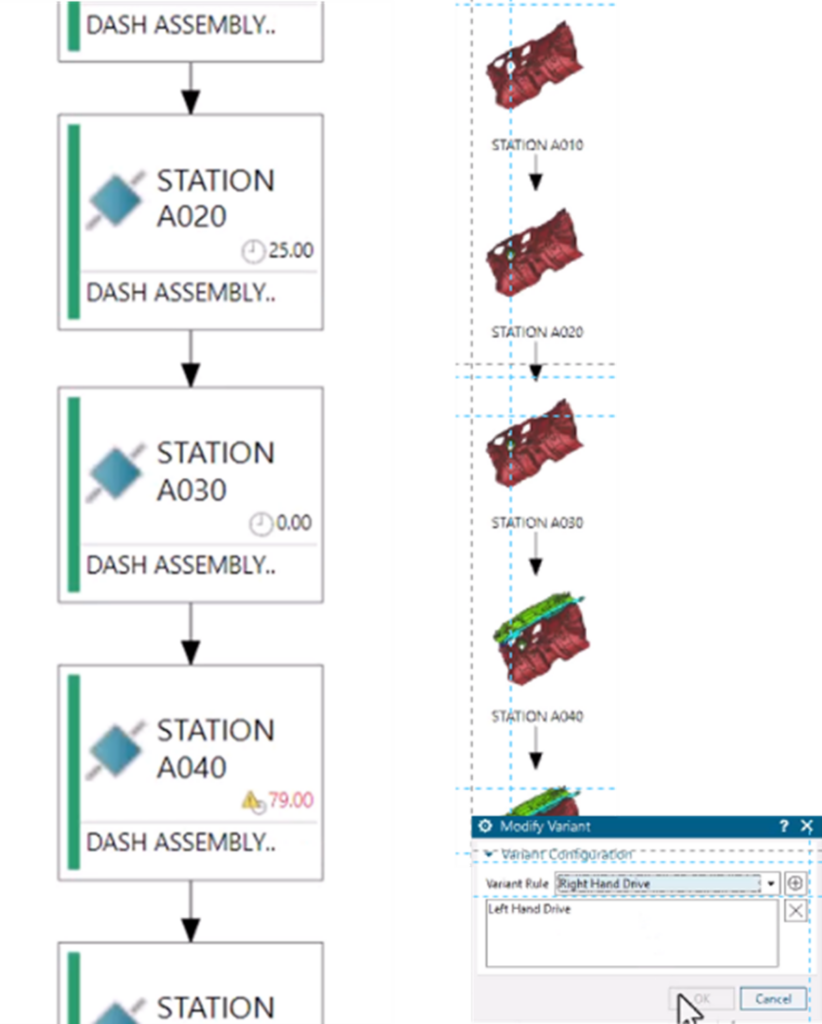
What’s New in NX Line Designer
The Attribute Viewer provides a convenient and efficient way to view and edit the attributes of a resource in a plant structure within the Plant Navigator in NX Line Designer. Users can easily access and modify attributes defined by the administrator, which ensures consistency and accuracy when working with attribute data.
Administrators have the flexibility to group and structure attributes that share similar content. For example, attributes related to the cost of a resource can be grouped together, streamlining data management. The Attribute Viewer option is currently available in NX-managed mode only.
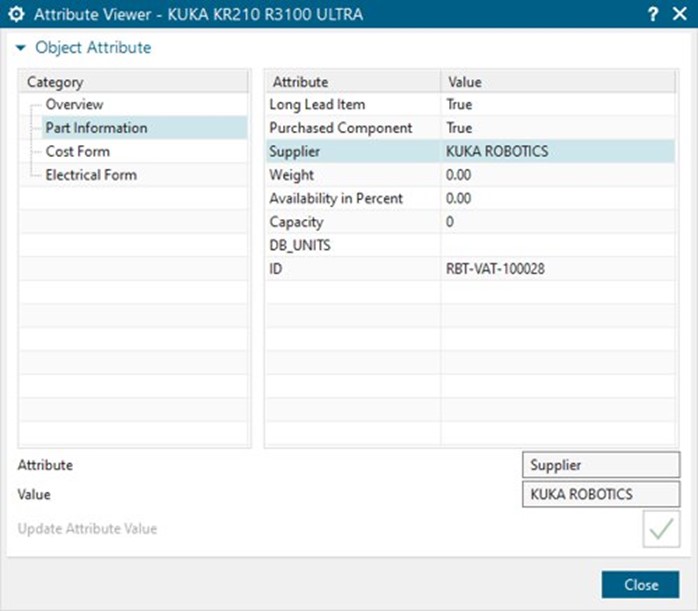
The Resource Library has undergone expansions with the addition of new content, which will soon be released on the Support Center. These additions primarily focus on various types of conveyors and related equipment, including flattop conveyors, pedestal conveyors, electrified monorails including junction and turntable, three rail power and free conveyors and structure track conveyors.
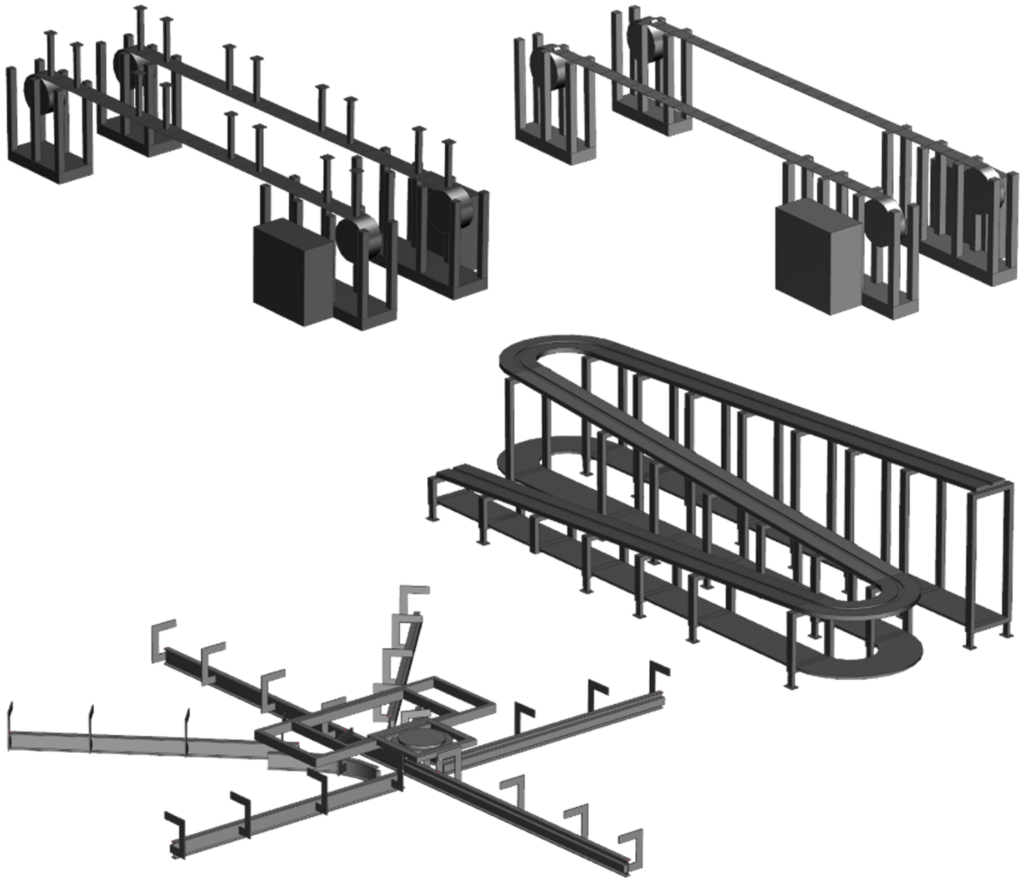
What’s New in NX Fixture Planner
The new Set as End Item command allows fixture designers to define any unit design as an end item. This simplifies the data to maintain detailed designs and kinematics definitions for fixture units. This approach improves load speeds and provides a better integration between design and simulation applications.
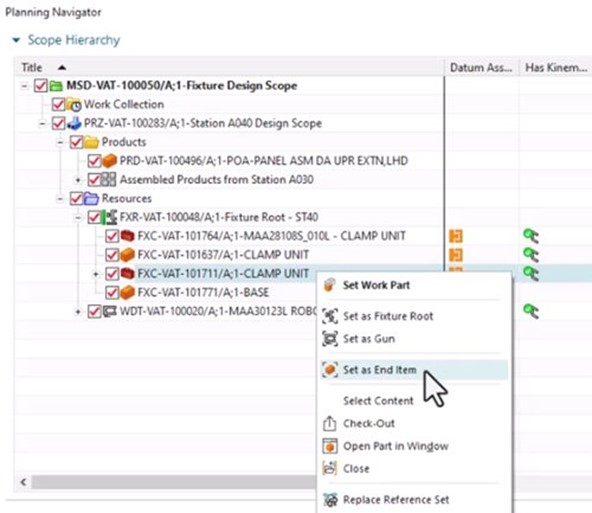
Learn more
To learn the details of the new NX for Manufacturing features, you can check out these step-by-step tutorial videos on our online community.
Explore NX’s advanced capabilities for NC programming by signing up for the NX CAM cloud-based trial. No installation is required meaning you can run NX in your browser, in just a few minutes.
For more information about the new design capabilities in NX 2306, check out this blog.