Optimized Manufacturing of an EV Component at IMTS 2022
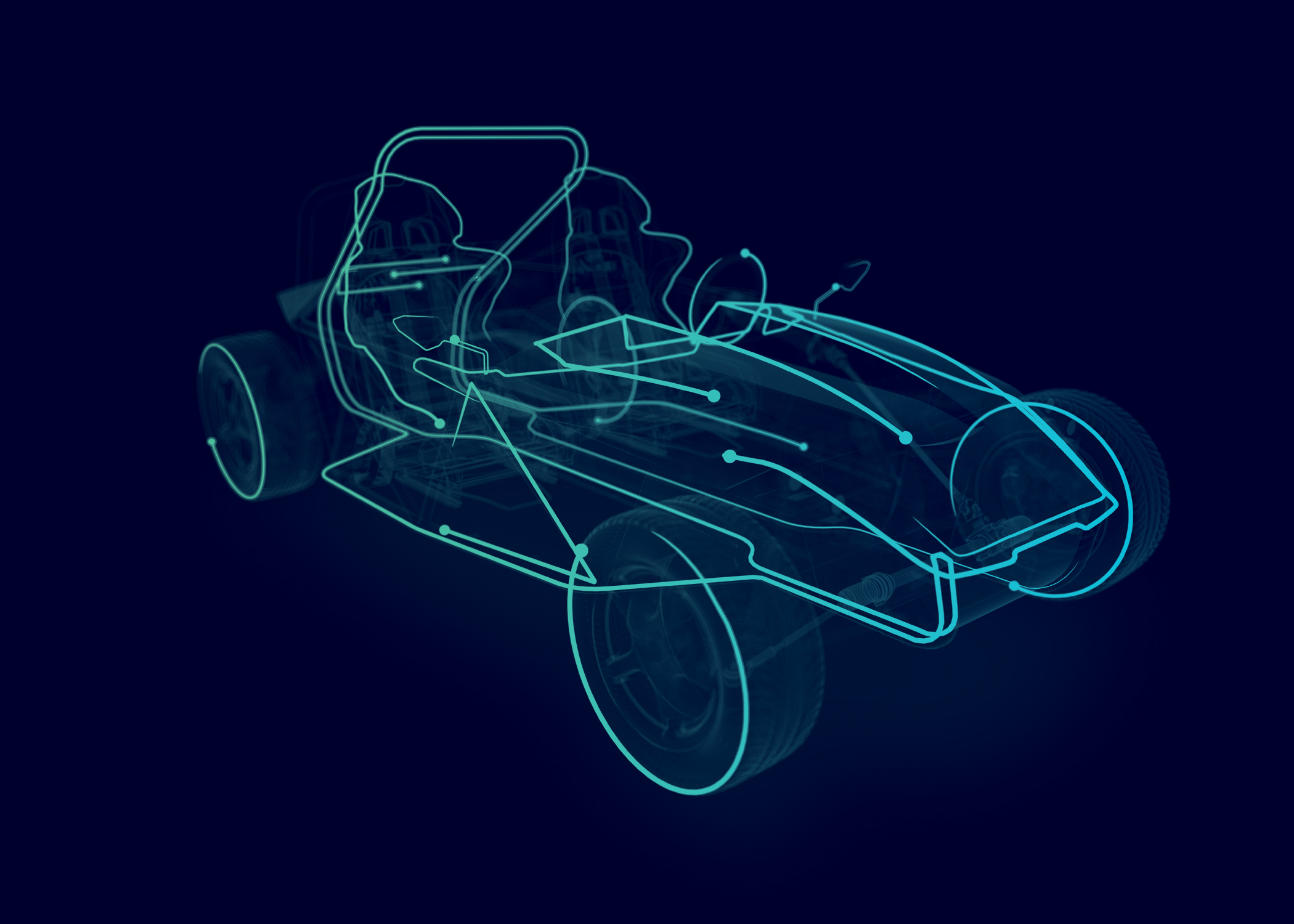
IMTS 2022 is right around the corner! Embark on your digital transformation with Siemens and see why manufacturers of all sizes choose to use Siemens Xcelerator, our open digital business platform that helps accelerate digital transformations for countless companies, our partners and everyone in our growing ecosystem. Siemens Xcelerator allows companies of all sizes to access the digital technologies, including NX for Manufacturing, to transform the way they compete, collaborate and connect. We help manufacturers combine the real and digital worlds, boosting productivity and achieving new levels of flexibility to bring products to market faster.
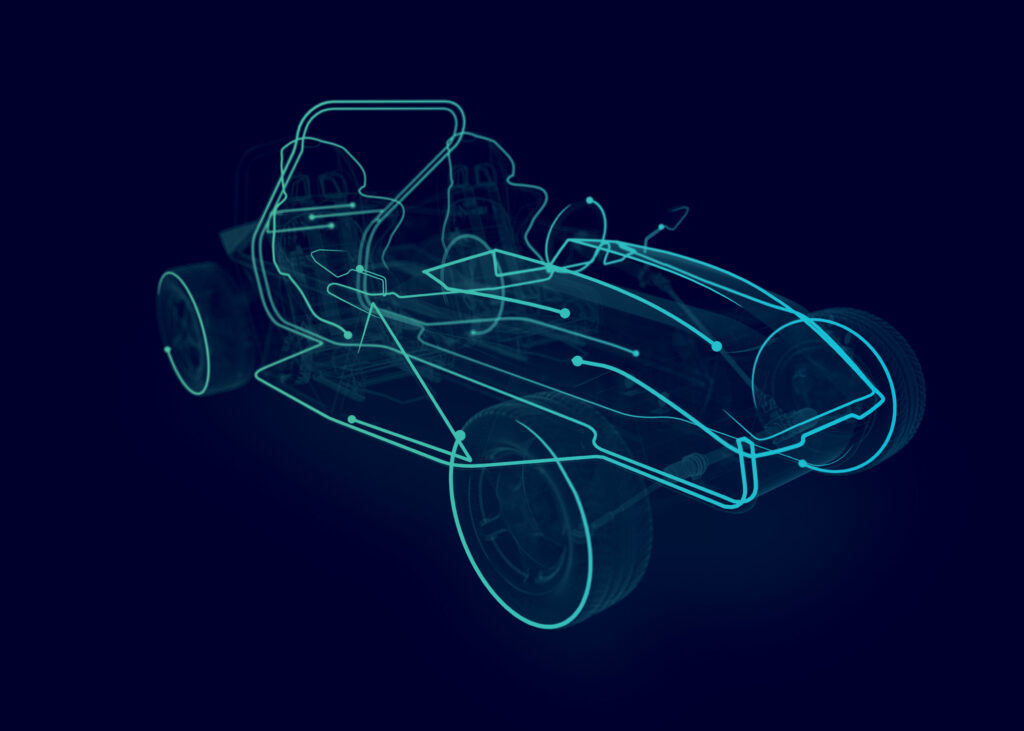
In our previous IMTS 2022 blog, we discussed how the manufacturing process starts with the design and how NX CAD, NX Additive Manufacturing and NX CAM software work in tandem with the latest 3D printers and machine tools to create an end-to-end digital manufacturing solution. At booth #133346, experience the highly efficient production process where Siemens manufacturing experts will take you through an immersive digitalization demonstration from redesigning the part and preparing for 3D printing to creating custom fixturing and toolpaths, as well as validating the NC programs – all with one software system.
As we transition from the design phase to the machining stage, the electric vehicle (EV) component was created using the latest topology optimization technology then 3D printed with additive manufacturing, ensuring optimum orientation and support structures of the EV steering knuckle. Working with the integrated NX for Manufacturing solution, users can seamlessly connect the additive and subtractive manufacturing steps, making the process associative and flexible. Final machining is programmed with NX CAM using key capabilities such as advanced programming, post-processing, and simulation. Feature-based machining allows users to automate the NC programming of the EV component to dramatically reduce programming time while ensuring expert knowledge is captured for future re-use. In the case of the eRod component, automating routine tasks reduced the programming time by 60%.
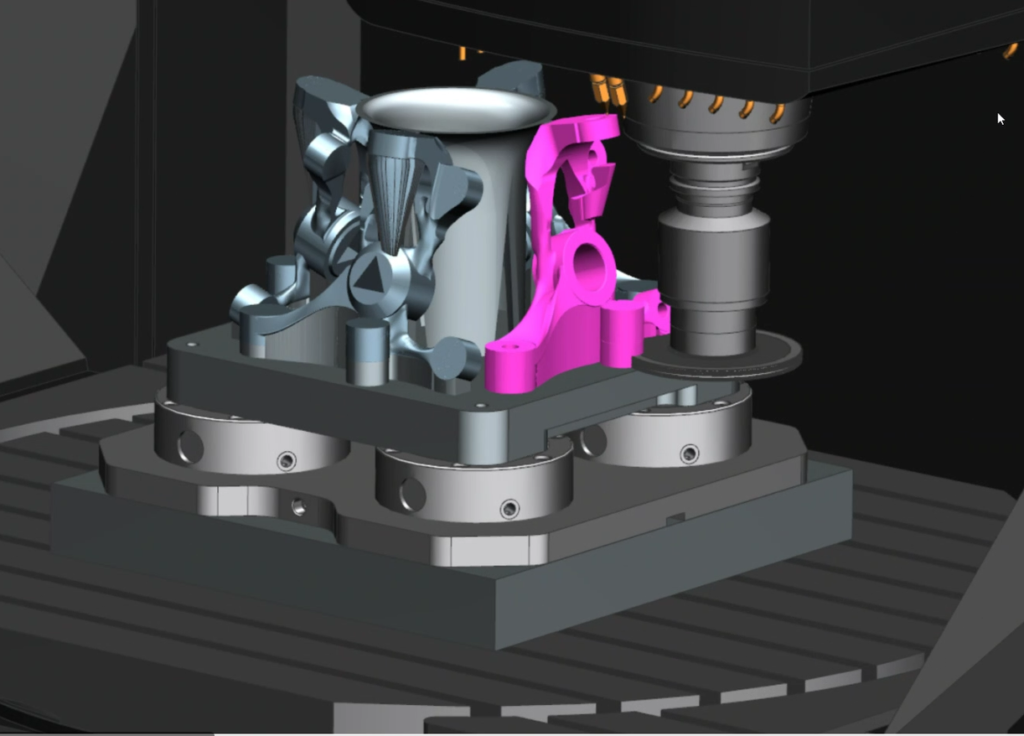
At our CNC programming station, you can witness how NX CAM provides comprehensive and integrated NC programming capabilities in a single system. This enables the use of a single system to program the most challenging 3D models such as the organic shape and light-weighted eRod wheel knuckle. By leveraging our G-code-driven simulation, you can validate the programs as if it were being executed on the CNC machine. This accurate simulation of the machining process prevents any possible interferences in production, resulting in high quality toolpaths. Utilizing this integrated machine tool simulation in NX CAM enables efficient and collision-free multi-axis machining to finish the EV car component.
Lastly, using Post Hub you can access over 1,000 post-processors accessible directly from NX CAM. This constantly expanding cloud-based platform allows users to download the digital model of the machine with the kinematics, and the simulation driver to postprocess and simulate the NC code in NX CAM. In the case of the eRod steering knuckle, downloading and installing the machine kit takes seconds, which helps us verify the NC code and minimizes the amount of machining steps required.
For the next stage of the production process, we can now better optimize the manufacturing process by inputting verified NC programs directly into the IoT-enabled SINUMERIK ONE. Stay tuned for the last phase of the highly efficient production process of the EV component and experience the seamless transitions between each stage at IMTS 2022. Discover how digitally connected manufacturing engineering software and machine tool automation can empower your business, too. We hope to see you there.