Designing of a next generation EV Component at IMTS 2022
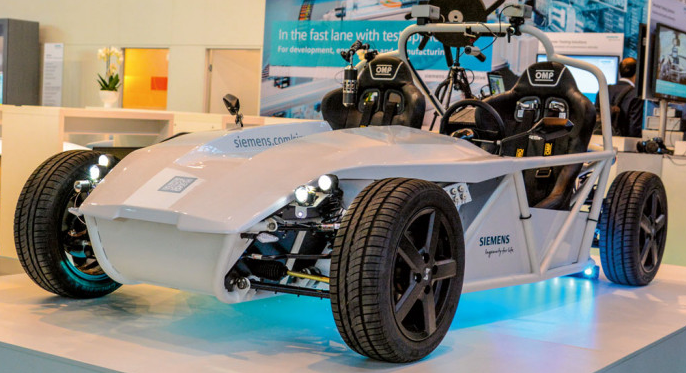
Digitalization will be center stage at IMTS 2022. Join Siemens and get a front row seat to our Digital Machine Shop showcase at North America’s leading manufacturing event in Chicago, September 12-17. Our showcase tailored to advanced manufacturing solutions demonstrates how a manufacturer can achieve high performance and quality all while meeting sustainability and profitability targets.
Visit our booth to experience the entire production process of a reengineered steering knuckle for an electric vehicle (EV) with a focus on optimizing the manufacturability, weight, performance and cost. The eRod, an innovative Swiss electric sports car, reveals how Siemens cloud-based software solutions and IoT-enabled machine tool technologies revolutionizes production with solutions ranging from digital twin technology to additive manufacturing and CNC machining.
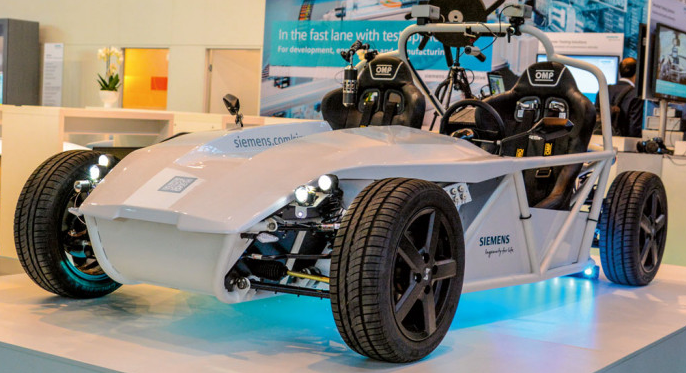
Image courtesy of KYBURZ
The foundation of a quality manufacturing process is always in the design. As a result, more and more companies use additive manufacturing as their guiding blueprint, resulting in less materials wasted and optimizing cost savings for real production. Manufacturers can produce quality parts at scale with industrial additive manufacturing software, from design to post-print validation. For the automotive industry specifically, the shift to electrification makes lightweight construction and sustainability goals even more top of mind for manufacturers. These challenges can be addressed through a holistic manufacturing process starting with the part conception and continuing right up to the production series using Siemens interoperable software applications and advanced hardware.
Simulation-driven design like topology optimization ensures that the optimal part is created with a minimal amount of material. NX additive manufacturing allows manufacturers to create optimal part designs with integrated generative engineering tools like design space exploration. For the eRod, this resulted in an innovative design of the steering knuckle, reducing its weight by 45% and improving its performance so that it can better handle stresses. By hollowing out the back of the spindle and smoothing out the knuckle, the significant weight reduction and enhanced performance was achieved, all while ensuring that the part’s structural integrity was not compromised.
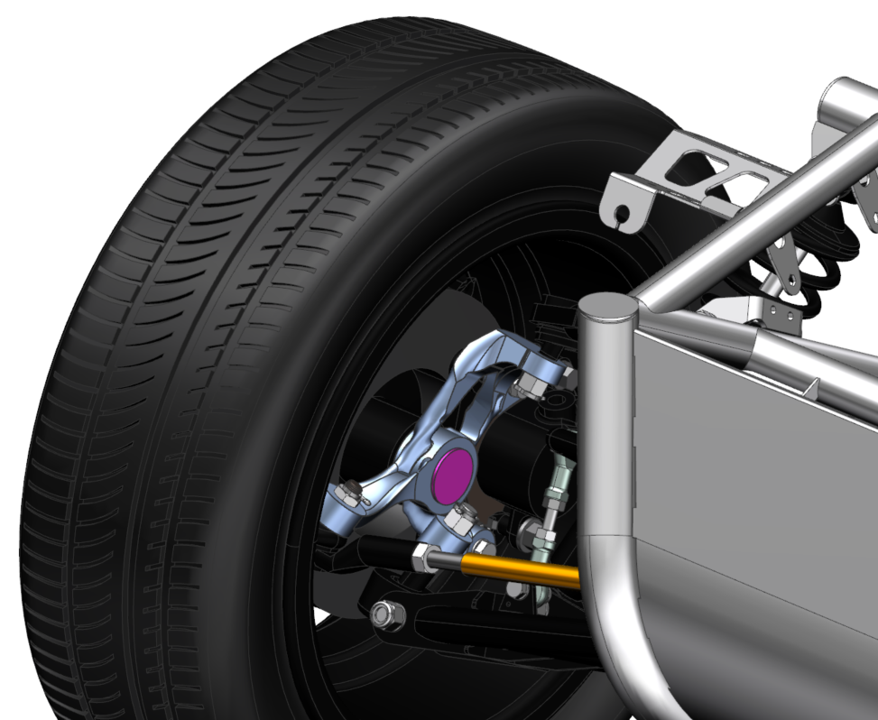
The Siemens Xcelerator portfolio enables uninterrupted workflow by having design integrated into NX, making for a seamless handoff to the next stage: the manufacturing engineering process. Discover how NX CAD, NX Additive and NX CAM software, work in tandem with the latest machine tool technologies to create an end-to-end digital manufacturing solution by converting a 3D part model into a real part installed on an EV.
Get the full experience at our IMTS 2022 exhibits. You will find Siemens in two booths: #133346 in the Controls-CAD-CAM pavilion located in the East Hall and in #433028 in the Additive Manufacturing pavilion located in the West Hall.
Stay tuned for the latest news on this industry-leading event! We hope to see you there.