Girsberger simulates and optimizes wood cutting operations offline using a digital twin
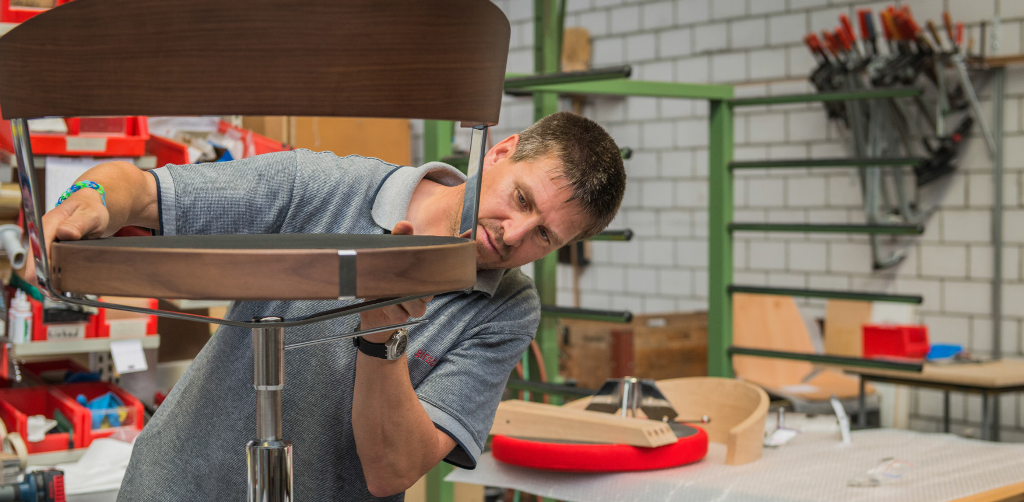
Switzerland-based furniture manufacturer Girsberger AG, has been producing innovative seating and tables with outstanding ergonomics, resilience, and durability since 1889.
Girsberger uses NX CAM with custom postprocessor for programming of NC wood machining.For the wood machining center, a complete 3D model was not available. Girsberger built a complete representation using NX. This way, they can simulate and optimize the wood cutting operations offline using the machine’s digital twin, saving machine occupation time, unsuccessful attempts and avoiding collisions.
Challenges
To remain internationally competitive in a country such as Switzerland with its high infrastructure and labor costs is quite a challenge. Combining sophisticated, original design and functionality with maximum practical benefits, Girsberger creates tomorrow’s classics. This requires an uncompromisingly honest use of materials as well as precision in manufacturing with high craftsmanship.
Since 2007 Girsberger has been using a computer numerical control (CNC) machining center from a leading German manufacturer. The size of the gantry machine is sufficient for work pieces – multitude of curves and freeform geometries. This suggests generation of the machine programs based on the parts’ geometry information from NX. Controlling the machine, however, is a proprietary CNC system designed by the machine manufacturer. It is not compatible with popular control systems used in milling centers used for cutting metals or plastics. Consequently, no suitable postprocessor programs or machine room simulation are available for this specific CNC machine. For computer-aided manufacturing (CAM), the preconditions had yet to be created.
Solutions
Janus Engineering is a partner of Siemens PLM Software for the optimization and automation of the CAD/CAM/PLM process chain using NX CAM and Teamcenter® software.Janus supported Girsberger in this automation challenge by programming a postprocessor. It allows automatically generating very efficient code for the CNC machining center based on the geometry data from NX. This required taking into account unique properties of the machine tool. It supplies some rotating parts with electricity using cables rather than slip rings, for instance.
For the wood machining center, a complete 3D model was not available, either. Girsberger built a complete representation using NX. This way, they can simulate and optimize the wood cutting operations offline using the machine’s digital twin, saving machine occupation time, unsuccessful attempts and avoiding collisions.
Results
Although both the mechanics and the control system of the machine are up to the task, simultaneous multi-axis machining was not possible due to programming limitations. The CAM implementation using NX enabled them to program the most complex machining patterns requiring simultaneous axis movements. Being able to utilize all capabilities of the machining center greatly reduces production-related restrictions for furniture designers. This also substantially contributes to the competitiveness of Girsberger whose Girsberger products’ user-oriented, ergonomic design is a significant distinguishing feature, particularly when competing with volume producers.