5 steps to discover sustainable, EV component manufacturing at EMO 2023 in Hanover, Germany
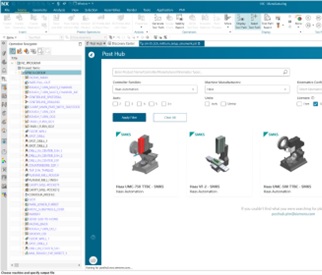
EMO 2023 is here, and we are excited to be at this year’s event in Hanover, Germany! If you are with us onsite or joining through our digital platform, we look forward to sharing our solutions for digital transformation can help you meet your challenges today and into the future.
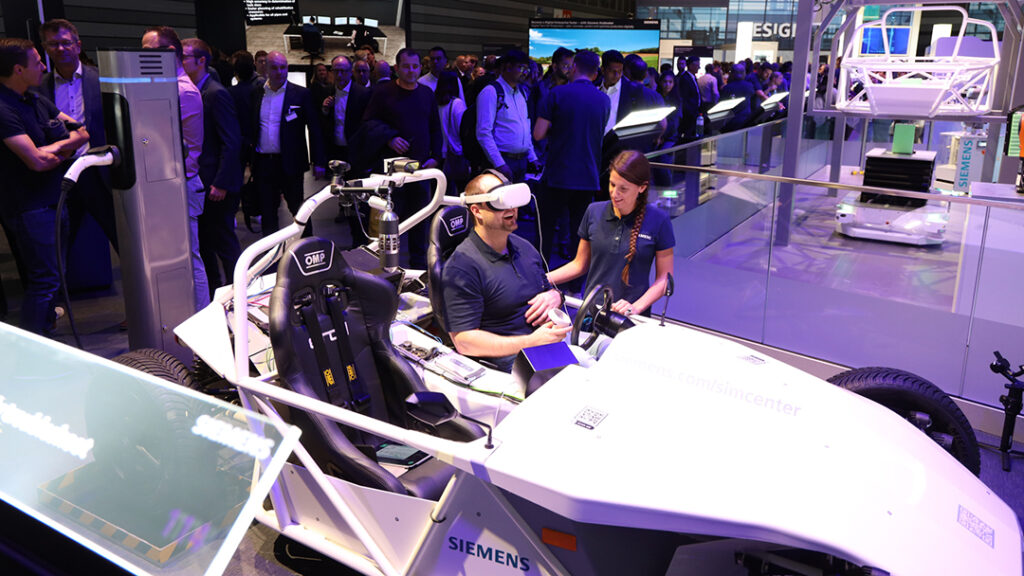
SimRod demonstrates how to sustainably manufacture sustainable products

Sustainability is a major topic at EMO 2023 and our SimRod showcase is the perfect starting point for learning how digital manufacturing empowers innovation and sustainable manufacturing. SimRod is a sustainable, all-electric (EV) roadster that demonstrates our ability to deliver a complete, end-to-end, design through manufacturing process using Siemens Xcelerator, our open digital business platform that enables customers to accelerate their digital transformation easier, faster and at scale.
SimRod validates the capabilities of manufacturers that have embraced digital transformation, and are using our unified solution for generative design, additive manufacturing, CNC programming, and more – all while adhering to sustainable production principles.
See the new high performance SimRod EV components and learn how they were produced
At EMO 2023, you will see the latest high-performance components that we have designed and produced for SimRod – the steering knuckle and our new light-weight wheel rim.

Our goals were to develop and manufacture new components for SimRod that would exceed the performance of the car’s existing OEM parts. This would require taking each part through a real-world process from design to production to manufacturing lighter-weight, more durable parts in a cost-effective and sustainable way.
Digital Machine Shop approach for EV manufacturing
In the space below, we’ll take a quick, high-level look at the digital machine shop approach that we utilized to produce the new steering knuckle and wheel rim.
If you are at EMO, make sure you stop by our booth to get an in-depth look at the technologies and processes that were employed in SimRod’s redesigned components. We would be happy to walk you through each step and answer your questions.
As mentioned, both the steering knuckle and rim would need be lighter weight and more durable to meet our performance requirements. They would also need be reliably and cost-efficiently producible in a real-world manufacturing environment. This would require a highly automated manufacturing process leveraging the latest 3D printing, CNC machining, and CMM inspection technologies that are all seamlessly connected. In other words, a digital machine shop.
In traditional manufacturing process, redesigning and producing a new part is a slow process with work done and managed in silos. There are lots of interface discussions, nonconcurrent work, and many variants that are incompatible with each other.
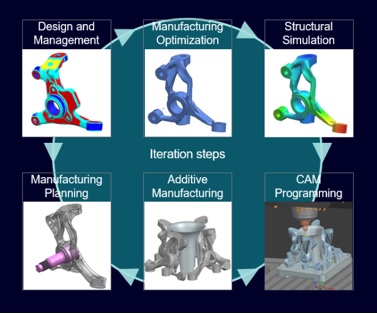
By utilizing a digital machine shop, powered by Siemens Xcelerator, we gain a data-driven manufacturing environment that seamless connects engineering, processes, machines, robots, equipment and other elements of the operation. This provides us with the infrastructure to quickly and efficiently produce the high quality, lightweight parts we need.
At our booth, we will walk you through each step of the digital machine shop approach addressing key challenges in the SimRod production journey including:
Step 1: Easily manage and re-use manufacturing data created in the product life cycle
Teamcenter Manufacturing provides the data backbone that allows us to:
- Maintain transparency across the manufacturing organization and eliminate separate databases
- Download and upload NC data and tool target data to/ from NC controllers
- Meet regulatory compliance constraints on traceability
- Provide process accountability by documenting the production processes
- Increase planning efficiency, maximize resource utilization, achieve production targets, run a more agile business
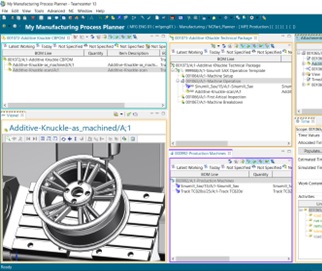
Step 2: Create noise, vibration and harshness (NVH) optimized rim for e-vehicle & increase competitiveness with quicker iterations on efficient models.
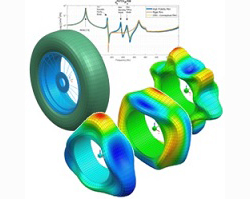
Post Processing, Machine Simulation and Simcenter 3D enabled:
- Fast and efficient model creation
- Ease what if study for tire/rim design
- Cover the full design space in early design
- Simple and minimal data created for investigations
- Creation of a precise parametric model
Step 3: Reduce programming time and minimize errors through simulation
NXCAM allowed us to create better parts in less time to:
- Take advantage of the latest machine tool technologies and manufacturing processes
- Program a wide range of milling, turning and multi-function machines all within NX CAM
- Save up to 90 percent on programming time by automating routine tasks
- Get it right the first time on the shop floor by simulating and validating NC programs in the context of the machine tool process
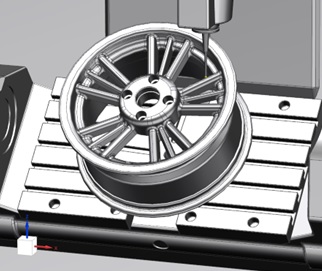
Step 4: Optimize the manufacturing process and improve workpiece quality
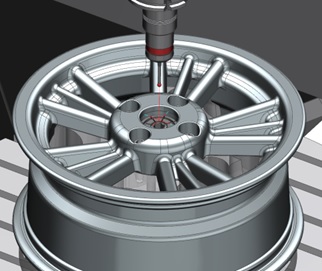
The NX CAM On-Machine Probing module provided comprehensive measurement technology to optimize the manufacturing process and improve workpiece quality.
This enabled us to:
- Monitor all critical machine and process parameters that affect performance, detect process variations, and adjust process parameters in real time
- Validate programming in the digital twin through simulation of the measurement movements
- Transform the part manufacturing process and reduce time to market with a digitalized process delivering improved quality by predicting and eliminating errors
Steps 5: Reduce production ramp up and ensure safe operations on the shopfloor with the digital twin technology
Digital twins of CNC machine tools and a new approach to cloud-based processors enabled us to:
- Increase safety by avoiding possible collisions on the machine with the G-code-driven simulation
- Generate production-ready NC programs for a wide range of CNC machines
- Get the preprocessor for your machine from Post Hub, the NX CAM’s clod-based solution for postprocessing
- Try any Smart Machine Kit Solution (SMKS) without a license to ensure that you use the right kit for your application
- Improve manufacturing sustainability by accelerating setup, minimize test runs, scrap, and tool brakeage, while reducing energy consumption
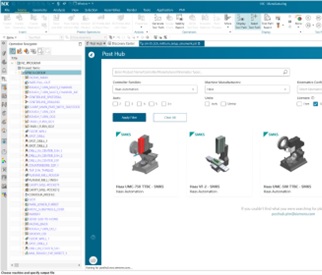
Visit Siemens at EMO 2023
We are excited to share our solutions for cost-effective, sustainable digital transformation at EMO 2023. You can meet us in Hall 9, booth G54. You can also find us here:
Siemens main booth 54 in hall 9 you can find us also here:
- DMG MORI | Hall 2, booth A21
- CERATIZIT GROUP | Hall 5, booth C69
- Sonderschau Bildung | Hall 8, booth A54
- Future of Connectivity Area | Hall 9, booth H22
- Future of Sustainability in Production Area | Hall 16, booth F11
Exhibit layout – Siemens location: Hall 9, booth G54
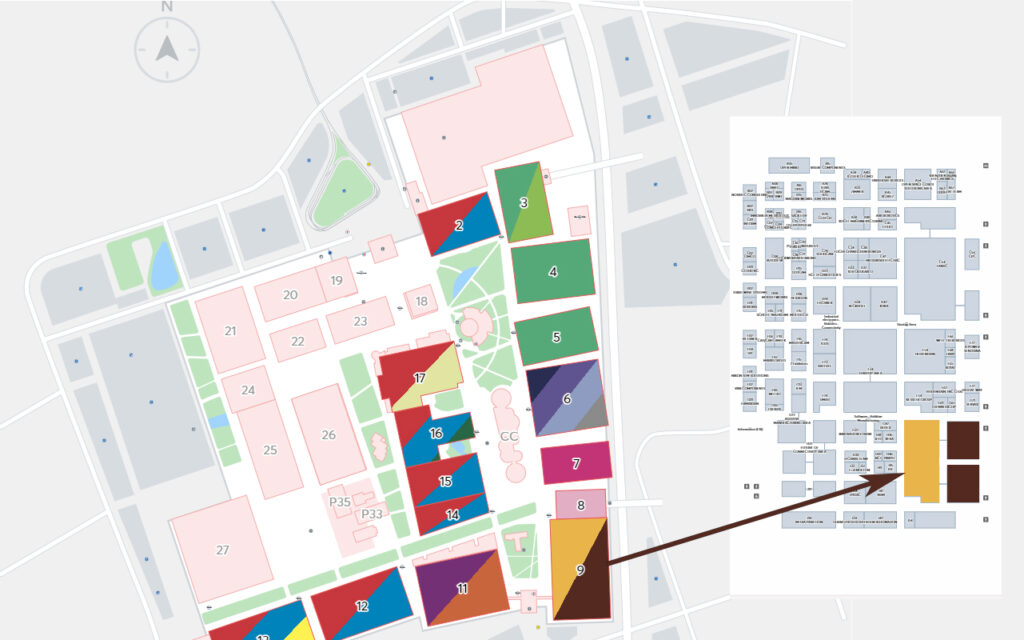