Siemens leads collaboration for advanced EV component manufacturing [article]
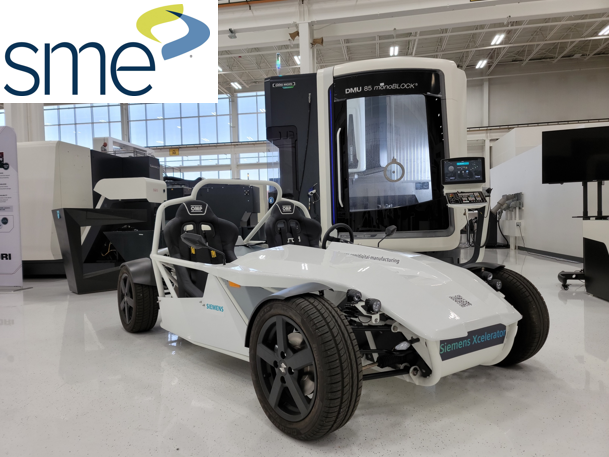
Imagine the collective expertise of Siemens, DMG MORI USA, Trak Machine Tools, and Walter USA LLC, now synergizing to redefine the landscape of part manufacturing for electric vehicles (EV).
A recent article published by the Society of Manufacturing Engineers (SME) explores how these leading companies in software, machine tool technology, and CNC automation can help companies enhance manufacturing efficiency and quality especially in EV components. Specifically, what does it take to seamlessly integrate the disciplines of manufacturing design, planning, and production to create superior products?
The article showcases a unique manufacturing challenge to redesign and produce a lightweight component for eRod, a Swiss electric sports car. It showcases how Siemens’ cloud-based software solutions and IoT-enabled machine tool technologies are transforming production. This digital based twin solution includes design, topology optimization, additive manufacturing, CAM programming and CNC machining, connecting the entire manufacturing processes. The narrative elaborates on the successful resolution of this challenge, utilizing Siemens Xcelerator portfolio along with manufacturing technology from Siemens partner ecosystem, including DMG MORI USA, Trak Machine Tools, Walter Tools.
This is a great example how digital tools enable companies to connect all the key stakeholders in the manufacturing process. Experts in additive manufacturing, NC programming, and industrial automation collaborate seamlessly can seamlessly collaborate on processes to produce next generation components.
A collaborative journey in designing and manufacturing the EV component
From concept to production, the article published by SME Manufacturing Engineering highlights the different manufacturing steps and advantages of using advanced software and automation.
It all starts with using advanced and unified technologies, exemplified by Siemens NX software Using industry-leading design features in NX, designers can model the 3D CAD part for crucial suspension components, such as the lightweight steering knuckle for the EV components.
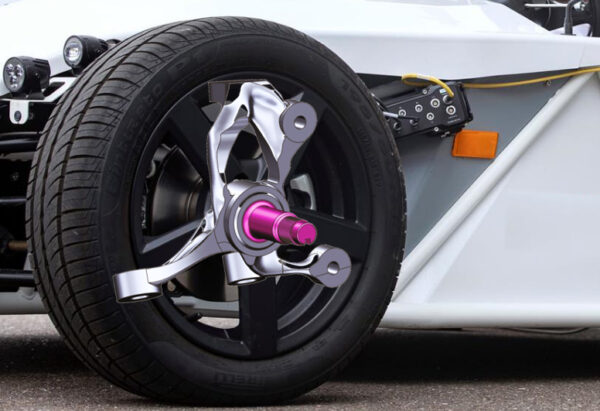
Using generative engineering tools, Siemens software can explore various design options to ensure that the parts not only meet performance standards but are also optimized for manufacturing. As design progresses, Siemens’ NX Additive Manufacturing solution facilitates optimal part designs and solutions. Through advanced simulations, Siemens ensures component strength and makes design adjustments for enhanced performance prior to production.
The integration of Teamcenter and Opcenter software streamlines process planning, automating programming and ensuring precision throughout the production lifecycle.
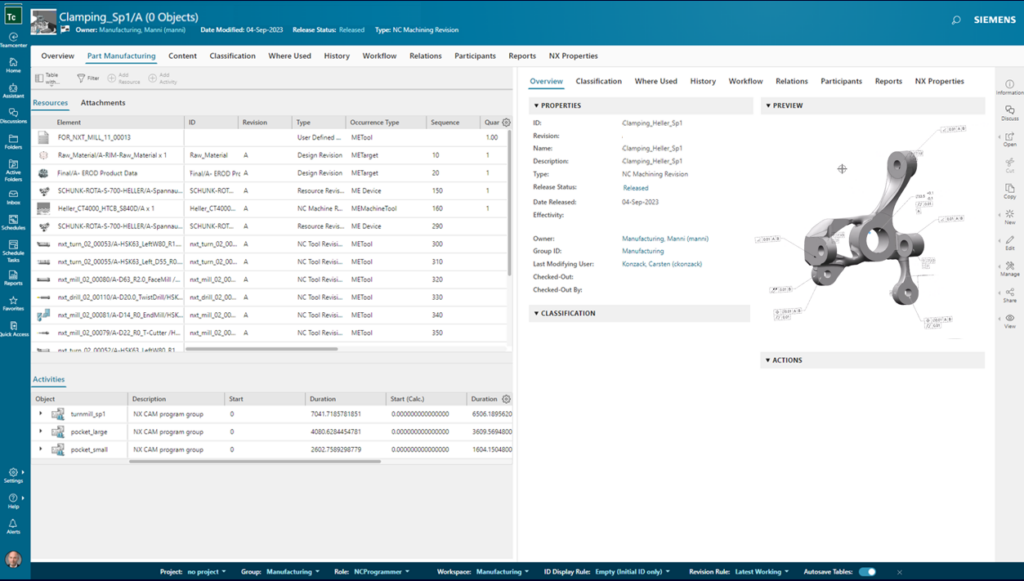
Opcenter APS optimizes production planning, generating optimal schedules for additive manufacturing and finishing processes, while Teamcenter centralizes product lifecycle data, facilitating seamless collaboration among design, engineering, and manufacturing teams. For example, in Siemens’ collaboration, Opcenter APS efficiently schedules additive manufacturing for components like the lightweight steering knuckle, while Teamcenter ensures accurate programming and measurement on the shop floor, maintaining version control for efficient production.
In the CNC programming phase, the engineers used NX CAM, one of the most comprehensive CAD/CAM software.
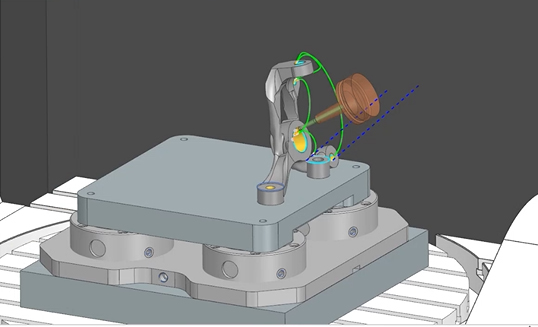
NX CAM enabled engineers to define and validate the entire machining process, ensuring collision-free operations and safety. By simulating using the actual NC code, it confirmed the safety of tight tool movements like for one of the drilling operation. Collaboration between engineering and manufacturing experts ensured optimal part positioning. NX simulation was employed to visualize the entire CNC machine working envelope, ensuring safe cutting and material removal. Collision-free tool paths and safe feature access were verified through G-code-driven simulation, using the same NC-code that controls the machine tool for EV components. With precise simulation in NX CAM, the entire machining process for EV components was confidently validated, even for intricate operations like drilling, confirming it was free from collisions.
Addressing Challenges in Machining Additive Manufactured Titanium EV Components:
Walter’s tooling hardware played an important role in addressing unique challenges presented by machining additive manufactured titanium components. These challenges included working with 3D printed Ti6Al4V stock material, removing brittle support structures, handling difficult-to-access features, and minimizing vibration during machining. Walter’s expertise and tooling solutions ensured that required tolerances were met during both finishing and cut-off operations, contributing to the successful manufacturing of these complex components.
The DMG MORI DMU 85 monoBLOCK machine tool was used to finish the 3D printed steering knuckle as part of EV component manufacturing. This advance machine can anticipate potential collisions between the machine and the part, or internally within the machine itself, such as the spindle hitting the table.
The Trak Machine Tools TC820si turning center efficiently produced components like the spindle during digital manufacturing, emphasizing the importance of choosing the right equipment.
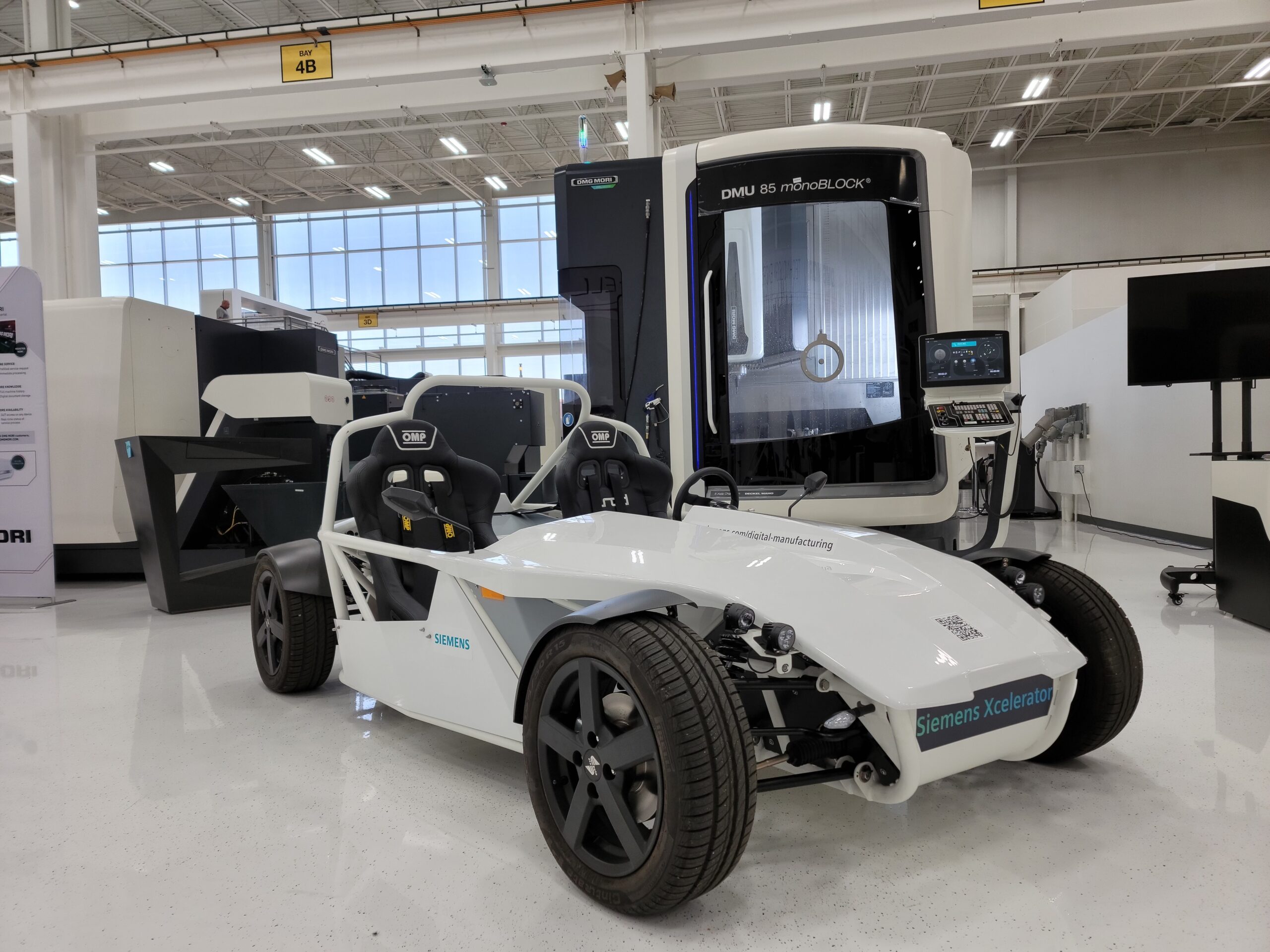
Learn more about EV component with NX CAM
Interested in a deep dive of each step for the EV component manufacturing? Explore the 4-part blog series:
Part 1: The challenge of redesigning and manufacturing of the EV steering knuckle
Part 2: Data management for seamless digital manufacturing
Part 3: Additive manufacturing: design and 3D printing
Part 4: CAM / CNC programming for high-performance toolpaths with NX CAM
The SME article touches on not just about what each company can do independently — it’s about how industry-leading experts joined forces to address unique manufacturing challenges resulting in a superior product interested in learning more? Dive into the SME blog of the EV component manufacturing for in-depth insights.