Designing a winning Formula 1 car with NX CAD | Oracle Red Bull Racing
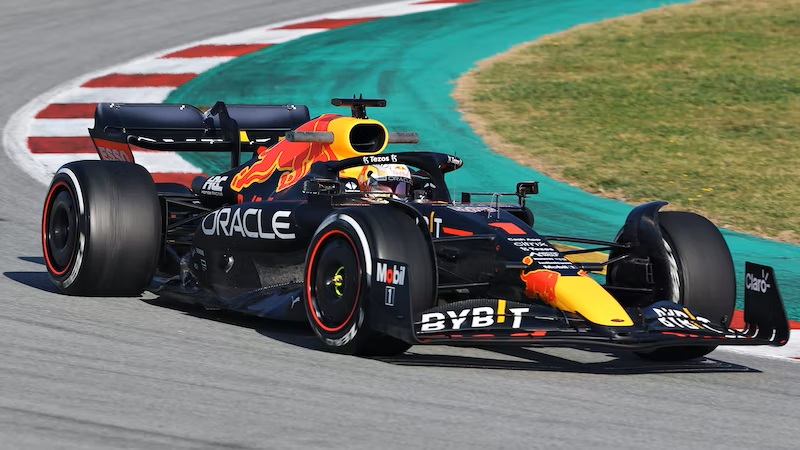
Oracle Red Bull Racing has been racing for 18 years, for all of which they have partnered with Siemens Digital Industries Software. Even before they were Red Bull, as Jaguar Racing and Stewart Grand Prix, the UK-based team has used Siemens software like NX CAD for their Formula 1 cars.
In 2022, they won the World Drivers’ Championship (with Max Verstappen as the driver) and the World Constructors’ Championship. At the first race of the 2023 season at the Gulf Air Bahrain Grand Prix, they took first and second place with Max Verstappen and Sergio “Checo” Perez (respectively) at the wheel, and again at the Saudi Arabian Grand Prix on March 19, 2023 with Perez and Verstappen (respectively).
On this episode of the Next Generation Design podcast, our host Jennifer Piper talks to Daniel Watkins, Head of CAD and PLM at Oracle Red Bull Racing about how they use NX CAD to design their F1 cars. In this episode, you’ll learn why the Oracle Red Bull racing team relies so much on Siemens’ NX, their biggest challenges in designing and improving their car, and the importance of a digital twin in perfecting the car.
Listen to or read the full episode: Designing For Speed using NX CAD
What You’ll Learn in this Episode:
Designing the Oracle Red Bull F1 car
The team’s design process is a very iterative loop, typically beginning with a concept from an aerodynamic perspective. Then, they mock up multiple variations of the concept in NX CAD. Looping in the 3D model from NX, they virtually validate the aerodynamics of the car using a computational fluid dynamics (CFD) process. Based on the results from the simulation, a 60% scale model will be manufactured to be tested in a wind tunnel to compare to the CFD simulation. Finally, a full-size car design will be chosen based on the analysis of prior tests to be made in NX. Using virtual tools from the Siemens Xcelerator platform for finite element analysis (FEA), parts are validated to ensure they are durable and capable of lasting on the track.
After many rounds of tests and simulations, the parts for the full-size car are manufactured and tested to see if they match the virtual validation in FEA. If the parts pass testing, they are manufactured and built into the F1 car. The first time they are seen in action is at a practice session, where the team can really understand how the parts perform and can be compared to the CFD and FEA simulations ran prior. If the results are good, they go racing, if not, they don’t. Oracle Red Bull Racing repeats this iterative process throughout the season—from concept to virtual validation to manufacturing to racing.
Siemens software tools used in the F1 design
Oracle Red Bull Racing utilizes many of the solutions from the Siemens Xcelerator platform in addition to NX CAD like NX for Manufacturing and Teamcenter.
Daniel says that a key strength of the team is the design and manufacturing of composite parts. For the last few years, they have been using Fibersim within NX to design and drive the manufacturing of composite parts. With their use of laser ply projection machines, Fibersim has dramatically reduced the variability that was due to manual processes, decreased material waste, and increased efficiency. With the collaboration for Fibersim and Teamcenter, a process that once took four days manually now takes around 10 minutes.
The openness in architecture and flexibility of the Siemens tools pushes the productivity of their engineers. Daniel estimates that there has been a 30% or more improvement on key parts in the manufacturing process, and that using NX open tools allows processes to be done five or six times faster than manually. Both of these improvements give time back to design better parts for the cars, with more iterations. Less time must be spent doing manual work or figuring out working within the tools, and more time can be designated to engineering and designing.
The role played by the digital twin in a car’s design process
“We have a digital process that runs from concept to track, and that process relies on that digital twin of the car,” says Daniel. The digital twin is pertinent to the processes at Oracle Red Bull Racing, with their virtual validation with CFD to FEA as well as virtually validating manufacturing tool paths. With the virtual mockup of the car, those at the track can see the car before seeing the real, physical model.
Then, the real car itself feeds data back to the team. It has information on how it runs throughout a race and that information can be used to change what the drivers need to do as they go around the track. All the while, the data is being fed into Teamcenter. As it is entered into the digital world, the information is pushed out to the necessary people to make quick decisions. With the digital twin, the right people can act quickly based on the right information being available at the right time.
The biggest challenges when designing a F1 car
Formula 1 teams are limited by the rules set by the FIA, resources, time, and costs.
The FIA, the governing body of the sport, gives out the rules each season anywhere from a month to six months prior to the beginning of the design process. When given rules by the FIA, the Red Bull team works to convert the rules into geometry and envision those rules and limitations in a 3D digital world. Then, engineers can be aware when coming up with the concepts for the car.
The FIA also enforces cost caps, which requires Oracle Red Bull Racing to rely heavily on their digital twins and digital validation. The integrated toolset of Siemens Xcelerator solutions allows the team to have high confidence in the parts that they do produce, saving time and costs that would have been spent on physical prototypes and development.
The F1 driver’s contribution to the car’s design
Contrary to what many may think, the drivers do not necessarily have direct input on how they want the car to be designed. They will always give feedback on how they think the car is handling or driving, what they feel when they’re driving, and the team uses that feedback to improve or change the car. Red Bull also uses a virtual driver simulation, where drivers can drive the car in the digital world from a scan of the track before going to the physical track. This way, the driver can experience the car and give feedback before they get to the physical model for race weekend.
Catch Oracle Red Bull Racing throughout the rest of this 2023 season, ending November 26 in Abu Dhabi.
Connect with Daniel on LinkedIn
Connect with Jennifer on LinkedIn
Continue listening to the Next Generation Design Podcast
Want to learn more about NX CAD software? Check out our website or try it for free.