What is Siemens Immersive Engineering? | Siemens & Sony partnership
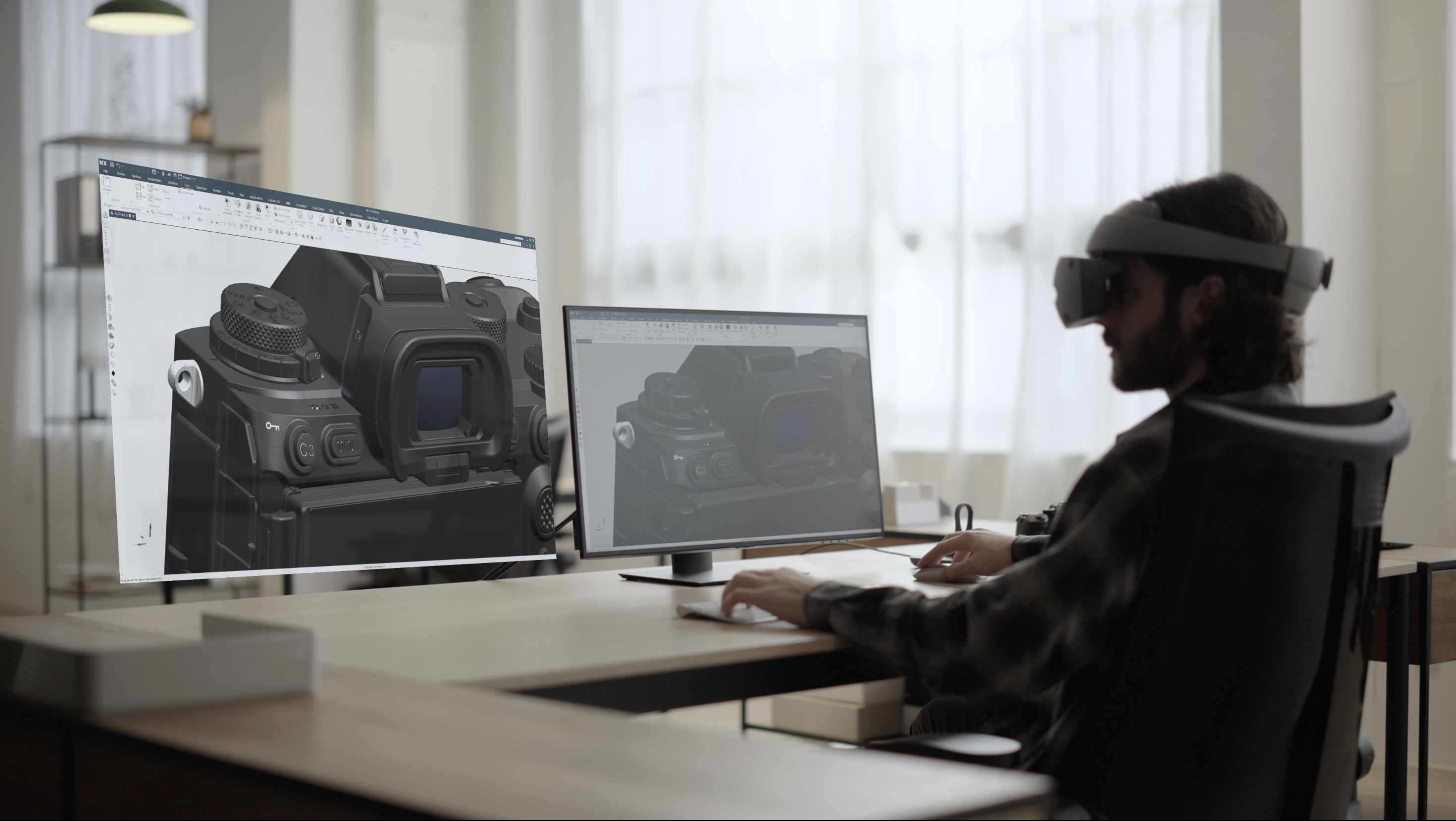
Welcome to season 4 of the Next Generation Design podcast, and welcome back to another recap. You can watch the full video of the episode below.
On this episode of the Next Generation Design Podcast, our new season 4 host Greg Arnot speaks with Ben Widdowson, Head of Marketing for Immersive Engineering for Siemens’ NX, and Henry Kondo, leading Sony’s XR and 3D display business. They explore the exciting collaboration between Siemens and Sony, unveiling new developments in immersive engineering and the industrial metaverse.
Ben and Henry share insights into the evolution of design processes—moving from traditional methods to cutting-edge immersive environments where engineers can interact with 3D models in real time. Learn how the Siemens’ NX Immersive Designer software and Sony’s XR head-mounted display (HMD) are breaking new ground in engineering workflows, enabling faster decision-making, and enhancing the digital twin experience.
Discover the potential of these immersive tools to reshape industries, reduce prototyping costs, and provide a more intuitive, human-scale approach to product design. Plus, hear how this collaboration is expected to inspire the next generation of engineers by making the design process more interactive and exciting.
Listen to the audio-only or read the transcript: Immersive Engineering: Revolutionizing the future of product design with Siemens and Sony
What you’ll learn in this episode:
How has visualization in product design software evolved over time?
The episode kicks off with some background on the evolution of visualization in design– from pen and paper, to 2D CAD on computers, to 3D CAD. The introduction of 3D CAD allowed for visualization of a product in its design phase. Over time, the accuracy, quality and realism of visualization tools in CAD software increased but “real-time” and “high quality” didn’t typically go in the same sentence. Ben says, “You could either get a very nice-looking picture, which took a long time to render, or you could use a technique used in games, where you get a very nice picture in real-time, but the quality is maybe reduced—it’s not ray-traced.” But over the years, with technologies like RTX, renderings can be done in real time. Now in present day, Sony and Siemens explore the possibilities of high-quality, real-time visualization with Immersive Engineering, where the new design process has become virtual in a real-world space.
What are the Industrial Metaverse and Immersive Engineering and why are they important?
We keep hearing the term “Immersive Engineering” and “Industrial Metaverse” but what do these terms mean? We’ll explore Immersive Engineering throughout the episode, but it is just one part of the Industrial Metaverse. Ben explains that the Industrial Metaverse is ” a way to bring together the most comprehensive digital twin of your production process or product but also bring it together with real-time data from the actual product or process itself.” The Industrial Metaverse allows us to fully immerse ourselves into a digital world through simulations with real-world physics and life-like visualizations, while also tying in real factory production or sales statistics. We can also collaborate with others, seeing digital twins in real-time with other people, no matter where they are in the world.
Henry adds that with immersive XR technology, we can realize real-world objects in the Metaverse with high-quality display and convey the feeling of really touching objects with the controllers that accompany the new Sony XR head-mounted display that was recently announced. With the collaboration between Siemens and Sony, we can begin to fully realize the Industrial Metaverse and explore it.
How did Siemens and Sony launch the NX Immersive Designer and XR headset collaboration?
Prior to the Immersive Engineering collaboration, Sony was a customer of Siemens Digital Industries Software, leveraging tools our product engineering tools like NX CAD for their products such as TVs, cameras and audio equipment. The switch to NX CAD from a previous competing CAD tool led to a 30% increase in productivity, which then brought up the question, “What is the next step in productivity?” leading Sony to develop a headset to support mixed reality engineering. As an expert and innovation in the hardware space, Sony then came to Siemens to be a software partner nearly three years ago to become a strong power in software and hardware collaboration.
NX has supported virtual reality (VR) headsets and VR design reviews for many years, but with these headsets, we have only ever been able to just view existing data. Ben notes that with previous headsets, “You can open an immersive view, walk around the data, and move parts around but you’re always very limited in being able to do any meaningful engineering work within that environment.” With the tight integration between NX Immersive Designer and the Sony XR HMD, Siemens and Sony have created a solution that enables you to not only look at the data and leave notes, but actually create, edit and manipulate geometry within the immersive environment.
What are VR, AR and MR, and how is Sony’s XR different?
VR stands for virtual reality and it puts a user in a virtual world with virtual images. AR is augmented reality, where you can see the real world but digital information is added on top. Then, MR is mixed reality which lands in between VR and AR, there is a mix of real and digital worlds. XR is a combination of VR, AR and MR.
Benefits of NX Immersive Designer and the Sony XR HMD
Henry mentions that the Sony XR head-mounted display has three main characteristics that set the product apart from other headsets on the first market. First, there is 4K per eye and 55 pixels per degree, creating a very accurate high-density display. Second, there are two hand controllers connected to the display: one triangular-shaped pointing controller that allows for accurate, precise operations and manipulation of data, then a ring-shaped controller for more intuitive control. Lastly, the XR HMD includes flip-up and flip-down functionality and see-through camera technologies allowing for a seamless connection between the real and virtual worlds.
NX Immersive Designer software sets itself apart from past NX VR tools. While mainstream headsets have been supported for years and continue to be supported, NX Immersive Designer is specifically integrated with the Sony XR HMD to allow manipulation and editing of parts and geometry in an immersive world and going beyond just viewing data. Ben notes that this collaboration has a focus on “enabling creators,” as our NX customers are designing products like cars, planes, boats, buildings, etc. The introduction of this Sony hardware enables customers to interact with data in ways they haven’t before, making design changes in real time in an immersive world and seeing their products at a human scale.
Leveraging NX Immersive Designer and the Sony XR HMD upon release will be simple. Both the hardware and software will be available for purchase through Siemens. A base seat of NX is required, then NX Immersive Designer is available through Value Based Licensing. With Value Based Licensing (or token-licensing), only a singular subscription is needed to access over 100 add-on modules in NX CAD through a check-in/check-out system. No requirement to buy each individual module you need separately. Once the headset is plugged into your PC, you can launch NX Immersive Designer in just one click in NX and immediately enter the immersive view. You can view parts in the VR view where everything is virtual, or leverage the see-through technology allowing you to see the real world around you with your virtual objects.
How does Siemens and Sony’s partnership help engineering workflows?
Henry notes that Sony is a customer and user of the new solution. The development of the HMD involved input from Sony engineers that are designers and users of NX, taking real feedback and enabling Sony’s engineering work to be more futuristic. Before virtual and digital engineering, real physical mock-ups and prototypes had to be created out of clay or plastic in order to test the product. With virtual engineering, Sony increased productivity and accuracy and reduced the time it took to design new products. With the new Immersive Engineering solution, they can see the products on the screen in real size and explore them with intuitive controls. This shortens the design time which then allows for more iterations as well as more products to be produced and go-to-market quicker.
Ben then mentions two customers that have been able to test out the Sony XR head-mounted display, Natilus and Briggs Automotive (BAC). Natilus is a San Diego-based aerospace company that is developing a new blended wing body design aircraft for cargo and in the future, passenger use. They wanted to know whether the parts and full plane that they are developing would fit through the doors and in the hangar itself. With the Sony XR HMD and NX Immersive Explorer, they were able to see a full-scale, mixed reality digital twin in their hangar. They could see whether the airplane would fit through the doors and alongside all the equipment in the hangar, and they even said things such as “Oh my God, I didn’t realize how big our plane was,” since they have not built one yet. It was the first time seeing their design come to life in human scale, a completely different experience from seeing the design on a 2D screen. “Straight away, they started diving into engineering decisions that they could have made differently. To me, that was really validating and fascinating,” Ben notes.
Briggs Automotive was also able to leverage the HMD. A big challenge for them is collaboration across the UK and Germany, as they require bringing in engineers from one site to the other for design reviews and looking at the physical assembly in person. With Immersive technology, they can speed up the decision-making process with virtual collaboration and meeting in the virtual world for design reviews and then with NX Immersive Designer, they can make design changes in real-time in the immersive view. Briggs Automotive also makes custom cars for their customers, and with the Sony XR HMD, they can show the customer a digital twin of their car and see exactly what they are buying and make any necessary design changes alongside the engineers.
How Oracle Red Bull Racing will leverage NX Immersive Designer and the Sony XR HMD
We hosted Oracle Red Bull Racing on the podcast last season, and they also expressed their excitement for the future of design with NX Immersive Designer and the Sony XR HMD at CES earlier this year. With races each week, the engineers at Red Bull have to make design changes to the car quickly week-to-week. With engineers both traveling with the vehicles to races and back at their base in the UK, immersive will allow them to collaborate in the virtual world and make design changes in real-time, significantly speeding up the design validation process and allowing production to happen sooner, which is crucial for turning around design changes in such a fast-paced environment. “Oracle [has been tracking] the number of design changes they’ve been able to make in a given season and correlating it with the number of points they’ve won in races [for many years],” Ben adds. With Immersive Engineering, their design process can become even more productive and enable them to win more races.
What has been the reaction to the Siemens and Sony Immersive Engineering partnership?
Ben and Henry have both attended multiple events, including our own Realize LIVE to get feedback from customers and the media on the Sony XR HMD, which the initial announcement of the partnership and product being at CES. Henry notes that media coverage has positively covered the “superior picture quality and the uniqueness of the controls,” and note how the Sony headset is unique compared to Apple or Meta’s headsets, with Sony’s focus being on enabling creators.
Ben mentions that since CES, his team as well as Henry have done around 1,500 demos for customers, receiving an enormous amount of overwhelmingly positive feedback. Ben specifically mentions that people understand and appreciate the tight integration between the software and hardware and the ability to interact with CAD data in real time. They also understood how the controllers work and how they are designed for creators. Lastly, many appreciated how easy it was to adjust the headset for glasses, as the display can slide in or out to come closer or further away to your face depending on if you wear glasses. Glasses-wearers don’t have to take their glasses off and thus can still experience a rich display.
Both Ben and Henry conclude with excitement about the product launch, with Henry noting how unique it is and Ben saying it has been the “coolest project I’ve ever worked on in my life.” Keep up with the launch of the Sony XR head-mounted display and NX Immersive Designer, launching later this year on our website.
Continue listening to the Next Generation Design podcast.
Want to learn more about NX CAD software? Check out our website or try it for free.
Comments
Leave a Reply
You must be logged in to post a comment.
Built for Sony’s HMD, it lets users edit rich 3D models natively in NX, supporting augmented Incredibox Sprunki and mixed reality for placing virtual objects in real-world settings.