Creating low-code solutions with big impacts
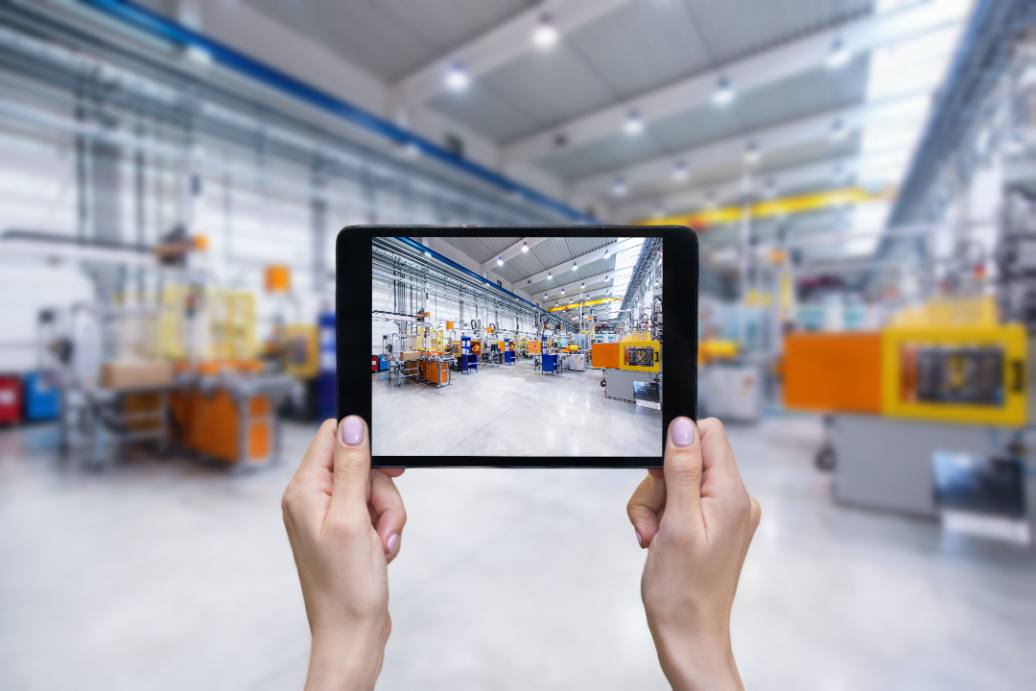
The Werner von Siemens Award acknowledges employee achievements that have a positive impact on Siemens’ business, company culture and society. This award recognizes landmark projects that empower our customers to shape a more sustainable world, make a positive difference for societies and capture the spirit of what it means to transform the everyday.
We talked with award finalist Philipp Lutz, IT Business Partner for Low Code in Siemens Digital Industries Software Motion Control, about his solution, “Digital Material Supply Revolution.” Read on to see how he used low-code development to create a state-of-the-art industrial IoT solution around supplying material to the factory floor – and find out what surprised him the most about low-code development.

Q. Can you tell us about the award and your solution?
A. My team of five and myself are finalists in the Werner von Siemens Awards in the category “Digitalization/IoT”. Our intralogistics project “Digital Material Supply Revolution” successfully implements a solution that includes IoT-triggered transport orders and visual planning through an integrated low-code application.
This solution enables the delivery of production material based on real-time demand with an easy-to-use interface, connected to both the ERP system (SAP in this case) and IoT sensors. The sensors are integrated within production material channels to update inventory records automatically and avoid over- or understocking.
Q. How did you get into Mendix application development?
A. Currently I am an IT Business Partner, but previously, I was a full stack web developer. In my current role, I prefer not to manage projects without having an idea of what is really being done technically. With the “Digital Material Supply Revolution” project, I thought, let’s create an app. Now I don’t have time to fully code from scratch, so I thought, let’s give Mendix a try. It was very easy to get started with; I hadn’t worked with low code at all before that, and now it has evolved into being part of my current role.
Q. Can you give us an overview of the problem your solution is solving and how the idea originated?
A. Supplying material to the factory floor is usually automized, without any humans involved. The stock level in the ERP system will tell you “we don’t have enough material,” and this will trigger a transport/order and delivery automatically.
But we’re seeing a common problem in manufacturers right now. Their stock levels don’t match. What you have in the system (ERP) and what’s on the shop floor are not the same, which means that very often you need to search for your material. That takes time, which costs money. Also, if you need to stop the production because the system indicates that you don’t have enough material, and then you realize that you do have what you need on the shop floor, that would mean again time and cost waste. Last but not least, once a year you need to do a proper inventory of your material for financial and compliance purposes. This is much easier if you really know what’s on your shop floor, not just in the ERP system.
One may say that there are many other solutions of this nature on the market. That is true, but what makes our “Digital Material Supply Revolution” solution unique is that we’re handling all of this in real-time through the industrial IoT sensors and in a visual way, so we have a bird’s-eye view of the shop floors — just like when you are searching for a location on Google Earth. We can position a coordinate system and have a complete overview of all our material channels, our storage locations where we can deliver the materials to, and the real stocks of material. We can also plan the transport routes there.
Q. How does your solution fit into the industrial Internet of Things (IoT)?
A. This is one of the important success factors of the project. We have the back-end logic and then we have the IoT portion, and each of them can work independently from another because we specified which standard interfaces we use in between. So, if something changes on the back-end side, it doesn’t matter. I can focus on the application, and if, for example, we add more sensors to the application or we use a different technology to connect to our back-end system, it doesn’t matter because there’s a layer in between that is already specified and standardized.
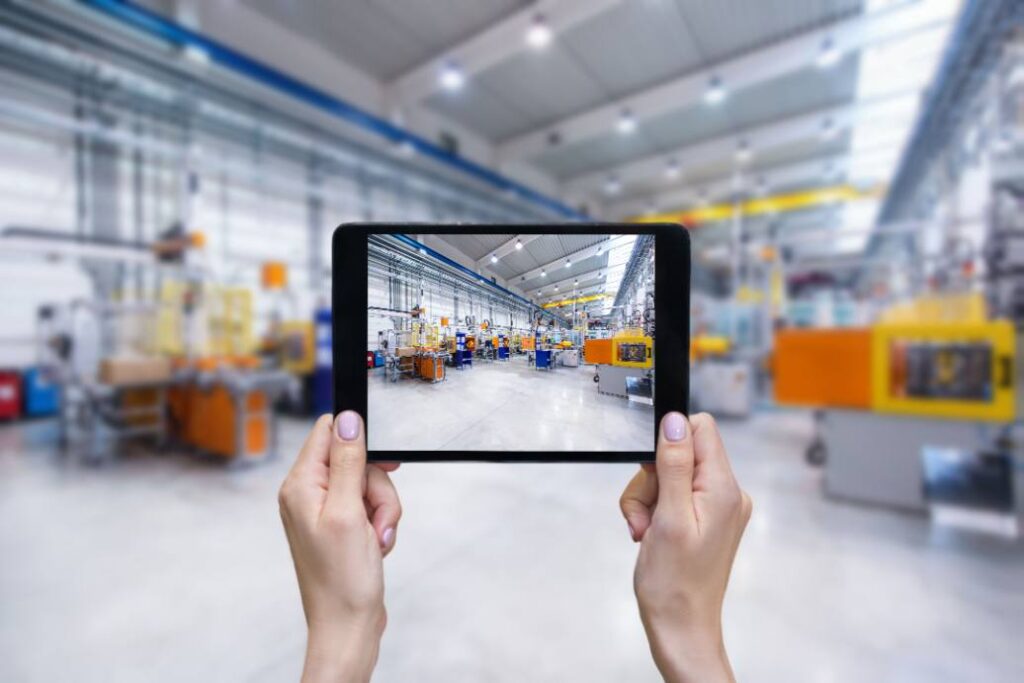
Q. What makes this solution innovative?
A. The standard systems that are on the market don’t offer this kind of real-time “material tracking” functionality. They’re all based on bookings in the ERP system and not based on IoT sensors that track real-time consumption. Also, the fact that it’s visual, you have this mapping of the shop floor, which helps save time and errors. It’s much easier to look at your shop floor and know where everything is, instead of working off of tables and charts.
It’s a small change. Going from bookings to this, you think it’s not that big of a thing, but it is a big thing. This use case, and this problem, is present at virtually every factory in the world – every factory needs to transport material from the warehouse to the machine. This is a simple use case, and you can do so much with that small change and it benefits everyone.
Q. How did you benefit from using low-code development for this app?
A. You could do it without low code, then it would just be a traditional web application, but it’s much faster with low code. You can work in an agile way, where you don’t know in the beginning how the solution will look. This is much easier with low code because you can implement changes so much faster and, if you’re wrong, if you need to specify something else or change the database or something, it’s done with seven or eight clicks in Mendix. With classic web development, that would take you a day. Even when the application is in production, you can make edits on the fly and the release process is real simple, compared to a traditional development approach. This agile microservices-focused approach also gives us more flexibility and independence than the rigidness of standard monolithic development. Because of this, we also benefited from using low-code development by giving the customer what they asked for, and quite quickly.
Q. What has the reaction been from the manufacturers now using the application?
A. They’re happy! This is not an innovation that comes from my head. The idea comes from the people who are using it now, so that’s why they’re happy, because they got exactly what they wanted and they participated actively in the development process. It’s very important, for any IT project, to have users on board who know exactly what they want and who see the value of the outcome.
Q. Did anything about working with low-code development surprise you?
A. I was surprised at how fast you can implement changes and correct mistakes. You’re so flexible even later on, even though you’re already in production with the application, you can still change a lot of things that would be difficult with classic web development. That makes it fun to work with. What keeps surprising me is how much fun I can have just dragging around boxes in Mendix.
Have an idea for an app that can improve your organization? Start building today, for free.