Harness digital transformation to simplify product complexity
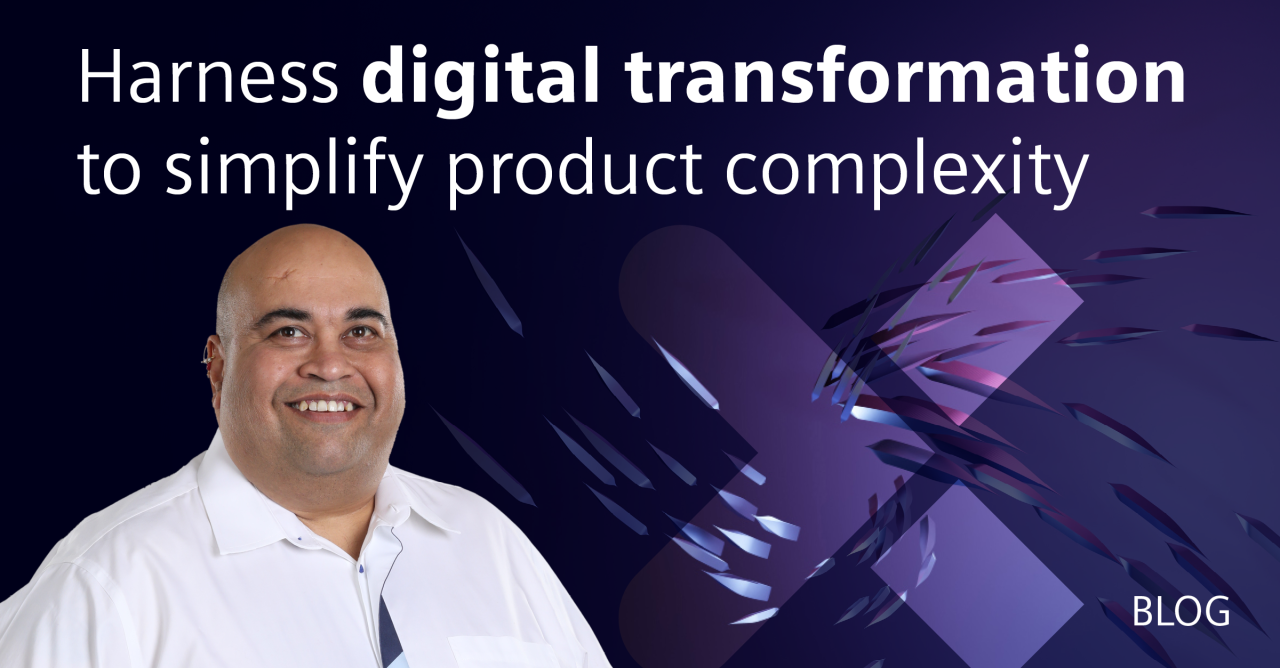
Mandar Lele – Industry Expert in Digital Transformation @Siemens Digital Industries Software | Electronics | Digital Twins | PLM | NPI | Supply Chain | Sustainability and Compliance
Post 2 of a 3-Part Series.
In today’s fast-paced global market, product development challenges continue to mount. Electronics are becoming more sophisticated, with customers demanding greater features, more options, and higher performance—all while expecting lower costs.
For Original Equipment Manufacturers (OEMs), the pressure to deliver new products quickly is compounded by ongoing supply chain disruptions. This makes designing, manufacturing, and delivering products more complex and cost-intensive. A fresh approach is needed to stay ahead in this fiercely competitive landscape.
Fortunately, digital transformation driven by the principle of integration provides a more holistic approach that outperforms traditional systems, allowing manufacturers to successfully address today’s product complexities.
Digital transformation turns complexity into a competitive advantage
At Siemens, digital transformation begins with the understanding that effective product complexity management must span the entire lifecycle of a product, from conception to market, with robust integration across systems such as Product Lifecycle Management (PLM), Manufacturing Execution System (MES), and Enterprise Resource Planning (ERP).
We understand that today’s multifaceted products require manufacturers to employ seamless collaboration across engineering, manufacturing, and operations domains. We also understand how to leverage collaboration to shorten NPI time-to-market and accelerate innovation.
Moving ahead begins with shifting left
Shift-left is vital because it allows companies to address potential issues early, reducing costs and speeding up time to market. Companies can better manage complexities and accelerate innovation by shifting focus earlier in the product development lifecycle, which is made possible by a PLM system tailored to their business and industry needs. This shift achieves an early focus on product variants and options sustained throughout critical phases of product design, manufacturing, and support. It promotes a model-based approach to product development, where requirement specifications capture the complexities of features and options for complete and successful product delivery.
As products become increasingly complex, managing quality becomes more challenging. Effective Requirements Management is essential for capturing the necessary configuration needs, which modern PLM systems leverage to address product variability and options. This robust configuration management lays the groundwork for defining the Bill of Materials (BOM) across design, engineering, manufacturing, and service, ultimately facilitating scaled testing and verification that mitigates quality risks.
The comprehensive solution for accelerating time to market
Increasing product complexity also increases documentation requirements—from customer needs to product requirements, from test cases to design and manufacturing plans—escalating in volume and can overwhelm the product development process.
To effectively manage this surging volume, embracing the idea that your process should dictate document creation and management rather than documents controlling your workflow is critical. That is why all elements must be integrated into a single system.
One unified PLM solution enables teams to instantly understand the impacts of any changes, streamlining updates across the chain. Changes in requirements can directly show which test cases, designs, and manufacturing plans need adjustments, ensuring that teams can focus exclusively on the affected elements, enabling them to move faster and with greater confidence.
Digital transformation is driven by connected platforms that increase visibility and elevate performance
Modern PLM platforms—tightly integrated with MES and ERP systems—enable early visibility into product costs, material planning, supplier collaboration, and compliance risk assessments through digital transformation. Supported by analytics and Quality Management Systems (QMS), these platforms provide closed-loop quality processes aligned with Design for Excellence (DFx) best practices, managing complexities with next-level agility.
Managing product complexities can become a critical competitive advantage with a flexible and scalable PLM platform driving enterprise-wide transformation. By breaking down fragmented information silos, digital transformation eliminates redundant efforts and enables teams to accelerate activities with complete confidence that all impacts are addressed.
Flexibility also means offering manufacturers the choice between on-premises and cloud solutions, allowing them to address unique security, compliance, cost, and scalability needs. Selecting the right deployment model enables manufacturers to optimize operations, protect their IP, and maintain a competitive edge in a rapidly evolving industry.
Contact us to explore how we can help your company. Stay tuned for our upcoming blog posts in this series to learn more about how Integrated Lifecycle Management can drive digital transformation and evolve your business.