Engineer’s Corner: Real-world BOM challenges
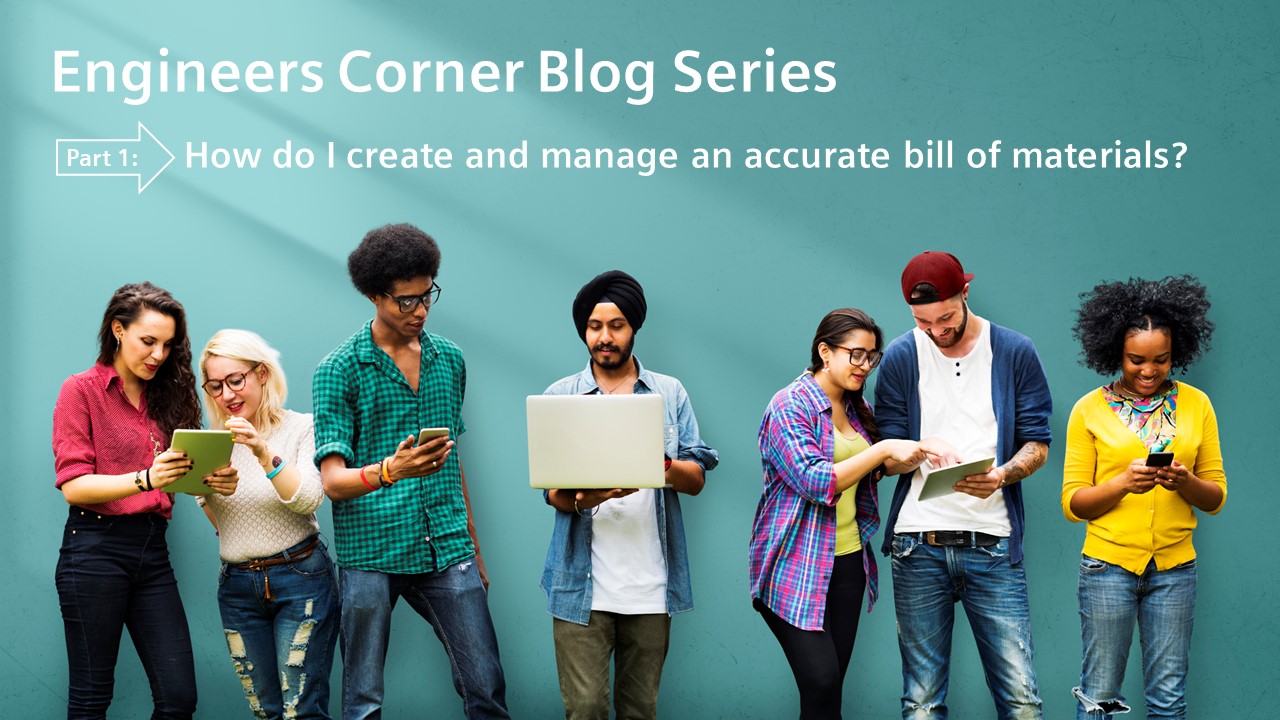

Navigating product variability in consumer electronics
In today’s fast-paced electronics industry, managing Bills of Materials (BOMs) for products with multiple variations is a common challenge. Let’s explore a scenario that many engineers face and discuss potential solutions.
The challenge: Smartphone model variations
Imagine you’re the lead engineer for a new smartphone launch. Your company plans to release the phone in three storage capacities (64GB, 128GB, 256GB), two colors (black, white), and with region-specific network bands. That’s at least 18 different variations to manage in your BOM!
Key challenges include:
- Maintaining accuracy across all variations
- Efficiently updating the BOM when changes occur
- Ensuring all stakeholders have access to the correct version
- Managing inventory and procurement for variable components
The traditional approach and its pitfalls
Traditionally, many companies have relied on spreadsheets to manage BOMs. In our smartphone scenario, this might mean:
- Creating separate spreadsheets for each variation
- Manually updating each spreadsheet when changes occur
- Sharing updates via email
This approach is prone to errors, time-consuming, and can lead to miscommunication between departments.
Before we dive into modern solutions, let’s take a moment to visualize the critical role and challenges of BOM management in electronics:
As we can see, SaaS PLM solutions offer significant advantages in addressing these challenges. Let’s explore how such solutions can specifically help with managing product variability.
A modern solution: Product Lifecycle Management (PLM) with variant management
A more effective approach leverages PLM software with robust variant management capabilities. Here’s how it can address our challenges:
- Single source of truth: Instead of multiple spreadsheets, all variations are managed in one central system.
- Automated updates: When a change is made to a common component, it automatically updates across all relevant variations.
- Variant rules: Define rules for how variations differ, allowing for easy generation of new variants.
- Stakeholder access: All departments can access the most up-to-date information, filtered for their specific needs.
- Integration with other systems: PLM can integrate with ERP and SCM systems for better inventory and procurement management.
Implementation tips
If you’re considering implementing a PLM solution for better variant management:
- Start by thoroughly mapping out all your product variations and the rules that define them.
- Involve stakeholders from all departments in the planning process.
- Choose a PLM solution that offers flexibility and scalability to accommodate future product lines.
- Invest time in training to ensure all users can effectively use the new system.
Conclusion
While managing BOMs for variable products like our hypothetical smartphone can be complex, modern PLM solutions offer powerful tools to streamline the process. By centralizing data, automating updates, and providing clear visibility to all stakeholders, these systems can significantly reduce errors and improve efficiency in BOM management.
For a comprehensive guide on BOM management, including more details on handling product variability, download our free eBook.
In our next post, we’ll explore challenges related to component obsolescence and strategies for proactive management. Stay tuned!