PCB design best practices: electrical/electronic co-design
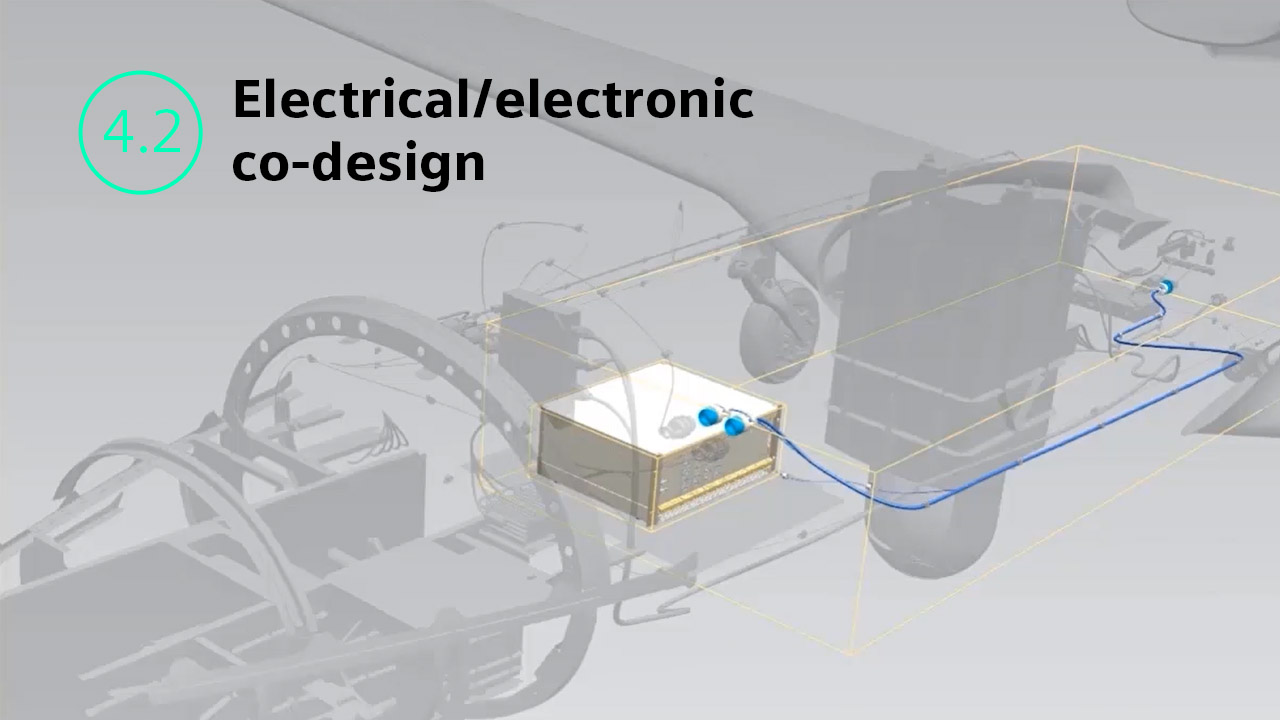
What is electrical/electronic co-design?
Circuit boards don’t work in isolation, they usually interface with other circuit boards via connectors, cables or harnesses. Electrical/electronic co-design is the integrated collaboration between these disciplines. This way, your entire hardware design from multi board electronic system specification to completed PCBs and cables can be handled within one integrated flow.
What’s not working?
Full systems design is usually done in a vacuum or by siloed teams. This causes a lack of visibility between all required engineering activities and results in lagging integrations between multi domains that takes place via legacy manual processes. This legacy methodology of engineering takes longer, is prone to human errors, and leads to higher engineering cost.
Best practices: electrical/electronic co-design
A system level integration would get you a digital twin via the digital thread, which would facilitate tightly integrated collaboration and the potential to remove errors downstream.
The evolution of electrical/electronic system level model-based design approach provides scalable solutions to support connectivity internal and external of the entire system, everything from the simplest cable within an electronic box to complex harnesses connecting systems-of-systems designs. This allows critical information such as connector part numbers and pin connectivity to be easily shared between PCB engineers and colleagues in a multi-domain electronic, electrical, and mechanical design flow.
The value gained from the scalability of a digital thread connecting electronic, electrical, and mechanical design activities results in more efficient and error-free systems design. This provides the greatest potential for return on investment (ROI) when designing today’s complex system level model-based designs.
Electrical/electronic co-design is a powerful design approach. We now have the capability to utilize the digital virtual world along with today’s automation to increase our design efficiency and optimization in successfully designing today’s complex systems. Having the ability to do this in the virtual world is better known as a digital twin. This methodology helps to reduce design cycle time, project cost, and time to market while increasing end product quality.
How it works: electrical/electronic co-design
Multi board PCB systems design typically require board to board connections made by standard or custom connectors and or cables, Siemens solutions scaled to support everything from the simplest cable within an electronic box to complex harnesses connecting systems of systems designs. This allows critical information such as connector part numbers and pin connectivity to be easily shared between PCB engineers and colleagues in a parallel electronic/electrical and mechanical design flow.
Once the multi-board Systems external interfaces are completed, Xpedition assists in managing the detailed interconnect information to drive the associated electrical harness design. The scalable Siemens solution provides a digital thread connecting electronic, electrical, and mechanical design activities resulting in a more efficient error-free system design.
Visit our website or watch this video to learn more about electrical/electronic co-design best practices: