Where to put decoupling capacitors on a PCB: best practices and design considerations
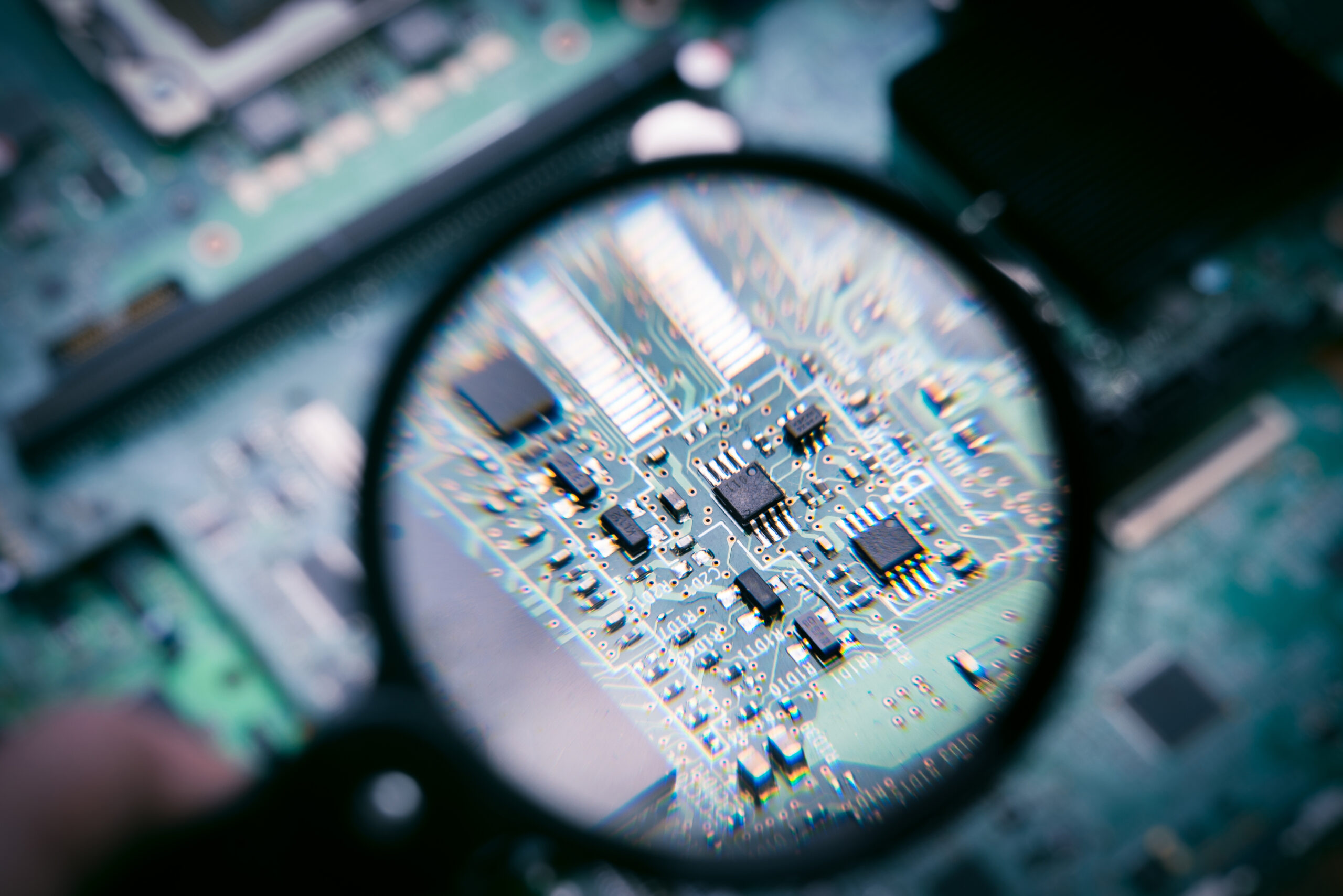
Why where to put decoupling capacitors on a PCB can make or break your design
If you’ve ever designed a PCB, you know that some parts of the process can feel like magic, especially when it comes to power delivery systems (PDS) also known as power distribution networks (PDNs). One of the more debated topics is where to put decoupling capacitors on a PCB. Should you place them as close as possible to components? Spread them evenly? Or just cram as many as you can fit?
While attending many industry conferences the last few years, I have participated in many insightful and at times “passionate and colorful” discussions with many of the industry’s top subject matter experts in electronics systems designs. In these discussions, when the topic of PDS or PDNs unfolds, they always involve capacitor values, quantities, and their physical locations within their respective circuits on the PCB. From general rules of thumb to OEM application guidelines, or by lessons learned from actual testing, there is no shortage of philosophies and or suggestions when it comes to where to put decoupling capacitors on a PCB. Yet, no matter who or where the information is obtained from, nor what “best practice” is suggested to follow, the commonality is to establish a well-balanced PCB stackup where the configuration contains tightly coupled power and ground [reference] layer pair(s) situated in and or throughout the stackup. This, along with a thorough power analysis/simulation of your design is key to creating a successful PDS or PDNs within the PCB. This has never been more evident to me while I sat in on Lee Ritchey’s recent technical presentation on Power Delivery System Design at PCB West 2024. His technical insights are truly gold, in my opinion! Let’s dig into to best practices and design considerations, and what the real-world implications are.
The basics: what do capacitors do?
Capacitors on a PCB aren’t just there to “look good.” They’re essential for stabilizing power delivery by storing and releasing charge during high-speed switching events. Think of them as mini-batteries that provide a quick energy boost to keep your ICs happy when demand spikes. But here’s the thing: their effectiveness isn’t just about their specs…it’s also about where and how you place them.
Why where to put decoupling capacitors on a PCB matters
You might think, “Just stick the capacitors next to the chip, and you’re done.” And while that’s a popular rule of thumb and or an industry best practice, it’s not always that simple.
Take power planes, for example. If your PCB has closely spaced (tightly coupled) power and ground planes, let’s say 4 mils apart, then capacitor location matters much less than you’d expect. Why? Because the planes themselves provide some of the necessary capacitance and spread the charge efficiently.
Now contrast that with a board where the planes are farther apart. Suddenly, the inductance between the capacitor and the chip becomes a bottleneck, and placing capacitors strategically becomes crucial.
Real-world lessons
During Lees’ technical session, he shared a real-world example from a 10 Gbps line card design. This high-speed board had thousands of pins, dense components, and serious power demands. Placing capacitors directly under a 2,000-pin BGA (ball grid array) chip was avoided. Why? Because cramming capacitors under the BGA would’ve made assembly and rework extremely complex and or nearly impossible. Instead, they distributed the capacitors around the board, ensuring they were accessible and easy to assemble while maintaining performance.
Another case shared by Lee involved a simple I/O module where just four capacitors were used—two 1 µF ceramics and two 100 µF tantalums. Interestingly, these capacitors didn’t even play a major role at the design’s operating frequencies. The PCB’s tightly coupled power planes carried the workload, proving that sometimes less is more when the design is right.
Busting some myths
Here’s a myth that might surprise you: ultra-low inductance capacitors aren’t always better. Sure, they sound fancy, but their benefits can disappear if they’re connected through high-inductance mounting structures. In many cases, using common capacitor package sizes like 0402 or 0603 with well-designed vias is a smarter and more cost-effective choice. Surprisingly, common best practices of bypass capacitor placement, such as close as possible, underneath each part, by every power pin, and with traces to power pins are not very accurate.
Practical tips for where to put decoupling capacitors on a PCB
So, how do you ensure your capacitor placement doesn’t become the week point of your design? Here are some practical tips I’d like to pass along from Lee’s technical session:
- Use closely spaced planes – Keep power and ground planes as close as possible (tightly coupled), 4 mils or less is ideal. This minimizes spreading inductance and reduces the dependency on capacitor placement. A caveat: if power planes are not closely spaced (creating a low inductance plane capacitor), it is not possible to do high speed signaling unless all of the capacitance needed to do high speed signaling is mounted on the package as Intel does.
- Distribute capacitors evenly – Instead of crowding them around chips, spread them across the board. This approach helps with power stability and provides good grounding for signal returns.
- Prioritize accessibility – Place capacitors where they’re easy to assemble and won’t obstruct rework. Accessibility is especially critical in dense designs with BGAs or other complex components.
- Choose the right package sizes – Stick with common sizes like 0402 or 0603 unless you have a specific need for something else. These are readily available and perform well in most applications.
- Complete a PDS analysis – Do your due diligence by simulating your PDS which includes your bypassing scheme, and to calculate power system impedance vs. frequency.
Where to put decoupling capacitors on a PCB might not seem exciting, but it’s a make-or-break factor for your PCB’s power delivery system, which is a critical part of any electronic systems design. The good news? By understanding the science behind placement and learning from shared insights and real-world examples by industry experts like Lee Ritchey, you can design boards that are not only reliable but also easier to manufacture and maintain. I’d like to thank my dear friend and industry expert Lee Ritchey of Speeding Edge for allowing me to share insights (golden nuggets) from his technical session. Remember, every design is unique and requires the upmost due diligence, but with these principles in mind, you’ll be well on your way to mastering the art (and science) of where to put decoupling capacitors on a PCB.
Looking for more PCB design best practices?