Things to check for on a PCB
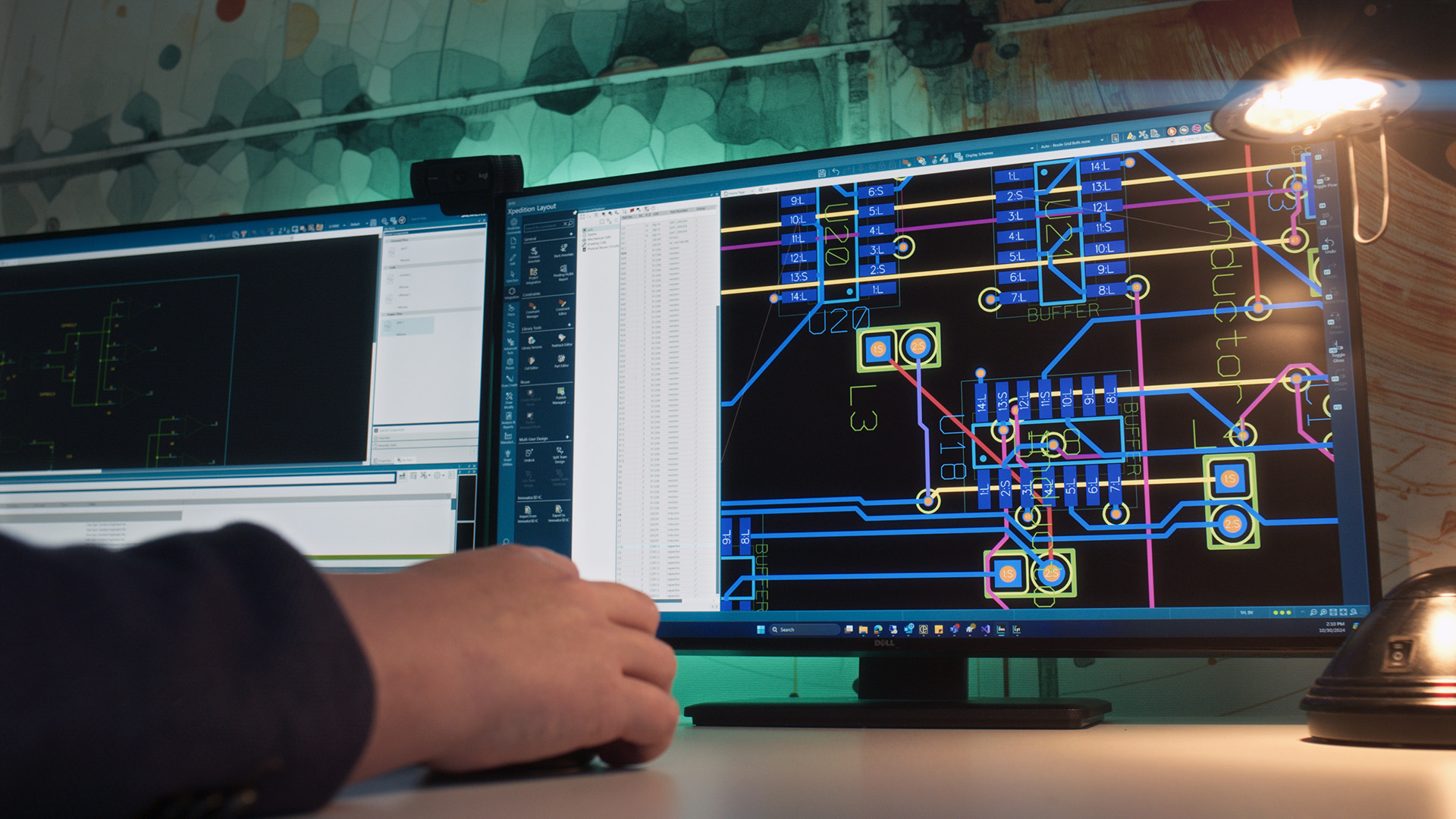
Ensuring the quality and functionality of a PCB at every stage from design through fabrication, assembly, and testing is critical to the success of launching any electronic product. The saying, “The devil is in the details” is especially true when it comes to the many details required in electronic systems design. There are three competing perspectives for success in PCB design: layout solvability, performance and manufacturability. I’ve mentioned these three perspectives before in a previous blog that you can reference here. In summary:
As a printed circuit engineering professional, you need to know and fully understand that there are three competing perspectives for success in PCB Design. To get it right the first time, focus on these three main areas:
- Layout solvability – Tackling complex packaging challenges.
- Performance – Ensuring good signal, power, and thermal performance.
- Manufacturability – Designing for high yield and lower costs manufacturing (DFX considerations).
When these areas are simultaneously addressed and come together, the result is a design with the highest possible component placement and routing density, excellent electrical performance, and efficient, defect-free manufacturing.
To address all three perspectives for success, a checklist can be invaluable. From a custom, internal checklist to all the industry specifications that include IPC specs, to the many individual supplier’s checklist which are typically available for download from each of the respective suppliers’ websites. There is no shortage of checklists available on the web. It just depends on what part of the overall process you’re in or at what stage a PCB, or a PCB assembly (PCBA) is in, that determines what things you need to check for on a PCB. Whether you’re designing, manufacturing, or inspecting a PCB and or a PCBA, here’s a breakdown of key considerations for each phase:
Design phase
In the design phase, the foundation for a reliable PCB is established. Typical key checks include:
- Requirements – Customer requirements/input/needs/wants (becomes its own checklist)
- Mechanical input – Ensures all critical physical features to include board outline, mounting holes, tooling holes, slots, cavities, and components locations as well keep-ins and keep-outs, and any component height restrictions are identified.
- Schematic verification – Ensure the circuit design matches the intended functionality and logic.
- Design Rule Check (DRC) – Use EDA tools to verify trace widths and spaces, clearances, and other critical constraints that align with the requirements.
- Component placement – Optimize component layout for optimal performance which includes signal integrity, thermal management, and manufacturability/producibility.
- Signal integrity analysis – Simulate critical signals (i.e. high-speed, RF, etc.) to avoid crosstalk, reflections, and electromagnetic interference (EMI)/electromagnetic compatibility (EMC) issues. The key here is routing all signals adjacent to a solid ground (reference) plan.
- Power Distribution Network (PDN) – Ensure appropriate power and ground layer pair coupling, proper decoupling and low-impedance connections for power delivery.
- Design for Manufacturing analysis – Ensures all aspect of the design will comply industry standards and best practices to achieve the highest yield at the lowest cost.
Fabrication phase
During fabrication, the physical board is created. Typical things to check for on a PCB in this phase are:
- Gerber file accuracy– Double-check exported Gerber files for layer alignment, drill files, and design integrity.
- Fabrication documentation – The recipe (details) that are conveyed from engineering to fabrication to ensure the end results meets the design intent/requirements.
- Layer registration – Ensure multilayer stacks are correctly aligned to prevent connectivity issues.
- Material quality – Confirm that the PCB material meets the required thermal and electrical properties.
- Solder mask and surface finish – Verify even application of solder mask and uniform surface finish (e.g., HASL, ENIG) to protect exposed copper and ensure solderability.
- Via quality – Check for properly plated and filled vias to ensure reliable interlayer connections.
Assembly phase
Assembly involves placing and soldering components onto the fabricated board. Things to check for on a PCB:
- Component orientation – Confirm the correct orientation of polarized components like diodes, capacitors, and ICs.
- Solder joint integrity – Ensure solder joints are smooth, shiny, and free of cracks, voids, or bridging.
- Pick-and-place accuracy – Verify that automated assembly machines place components precisely on their designated pads.
- Thermal profiling – Use an optimized reflow oven profile to avoid thermal damage to components while ensuring proper soldering.
- Cleaning and coating – Remove flux residues and apply conformal coating, if required, to protect the board.
Testing phase
Whether it be flying prob, bed-of-nails, or clamshell methodology, testing ensures the assembled PCB meets all functional and reliability requirements. Typical key tests include:
- Electrical testing – Perform continuity and isolation tests to ensure correct connections and absence of shorts.
- Functional testing – Verify the PCB operates as intended under normal operating conditions.
- Boundary scan testing – Use JTAG for testing inaccessible pins or verifying IC functionality.
- Environmental testing – Subject the PCB to temperature cycling, vibration, and humidity tests to evaluate durability.
- In-circuit testing (ICT) – Check individual components and their connectivity on the assembled board.
General considerations across phases
Regardless of the phase, always considers these things to check for on a PCB:
- Documentation completeness – Ensure requirements, schematic, BOM, fabrication drawings, assembly drawings, and test instructions are accurate, correct, and up to date.
- Compliance with standards – Adhere to industry standards such as IPC-2221 (design), IPC-A-600 (Fabrication), and IPC-A-610 (assembly).
- Test point accessibility – Design and verify test points for easy debugging and validation during production and maintenance.
- Thermal management – Evaluate thermal performance to prevent overheating in high-power designs.
- End use – Product/performance class, producibilities levels, where, when and how the final product is to be used, are vital pieces of information that need to be known.
A successful PCB is the result of careful attention to detail at every stage of its lifecycle: design, fabrication, assembly, and testing. By keeping in mind these things to check for on a PCB, you can minimize defects, reduce costs, and ensure reliable performance. Combining close collaboration with your external suppliers along with robust industry design best practices with thorough inspection and testing methods ensures the success of your electronic designs.
Looking for more PCB design best practices?