Six common questions about power module cooling
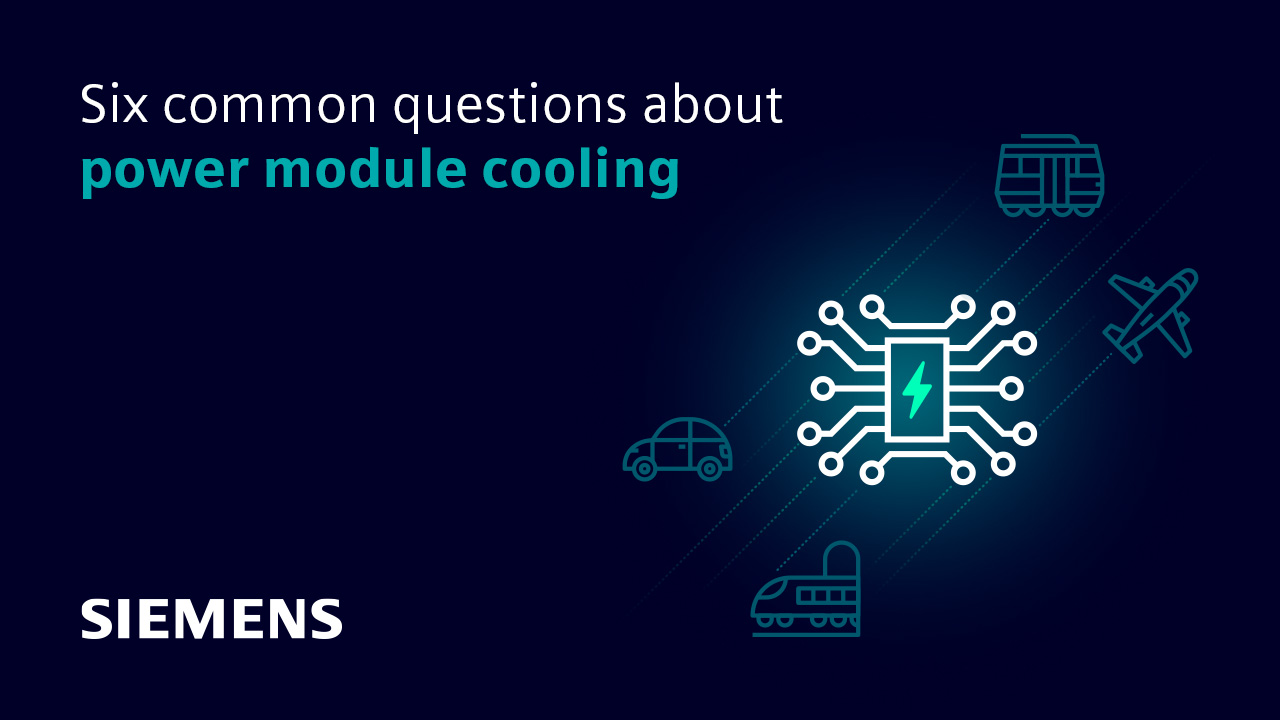
Power modules are essential components in power electronics, providing power conversion and power management. However, they generate a considerable amount of heat during operation, which can lead to decreased performance and even damage. Proper cooling is therefore necessary to ensure the power module’s longevity and optimal performance. This blog will provide an overview of six common questions about power module cooling that may arise when designing power modules for your application.
1. Are device temperatures equal?
Power modules are subject to uneven temperatures due to the localized heat generated by power components such as power transistors and diodes. Different parts of the power module will therefore reach different temperatures depending on their individual thermal resistance, power dissipation and physical position. It’s therefore important to ensure proper cooling measures such as heatsinks and air flow paths are taken into consideration when designing or selecting power modules for your application.
As power modules are most often filled with silicone gel or resin, measuring the components’ temperatures is not possible at all without impacting accuracy. Classical methods like using a thermocouple, which will provide accurate readings for the temperature at each power component, are not sufficient. Additionally, power modules need to be tested under different conditions to observe how the temperature varies across power components.
Using measurements of the electrical parameters offers the possibility to determine the junction temperatures of every discrete component. Adding simulation software, the current distribution between parallel components can be analyzed during the design process. This takes the power module board’s parasitics into account and enables the designer to determine the power dissipation in every single component, by using the simulated current distribution. Knowing the power dissipation enhances the setup of the thermal simulation, as the static state case can be then represented in the simulation. The deep integration of the thermal simulation software such as FloEFD and the electrical simulation software like Xpedition AMS can even further enhance the verification process. The combination of thermal and electrical models allows the analysis of the switching behavior of both domains.
2. What is the value of the device’s thermal resistance to the heatsink or case?
The value of the device’s thermal resistance to the heatsink or case can be determined using a thermal resistance measurement tool, such as a thermistor or thermal imaging camera. This will measure the power module’s temperature across its surface and allow you to calculate the thermal resistance between the power module and heatsink/case. Additionally, power modules are often rated with their thermal resistance value, which can be found in the power module’s datasheet or user manual.
3. What is the best thermal interface material?
The best thermal interface material (TIM) for power modules varies depending on the application. Commonly used TIMs for power modules include compounds such as thermal grease, graphite-filled pads, and phase change materials. Each of these compounds has its own advantages and disadvantages in terms of performance, cost, and ease of installation. In general, a thermal grease with high conductivity is a good choice for power modules due to its low cost and easy application process. However, other TIMs such as graphite pads or phase change materials may be better suited for certain applications due to their higher heat transfer rates. Ultimately it’s important to research your specific power module cooling needs in order to determine which type of TIM will perform best in your particular application.
4. How can I optimize the device placement for thermal behavior?
Optimizing power module device placement for thermal behavior can be done by considering factors such as power dissipation, heat source location, and heatsink layout. To ensure proper cooling performance and efficient heat transfer, power modules should be placed close to the heatsinks to reduce the thermal resistance between components. Additionally, power modules should be placed away from high-temperature sources such as other power modules in order to prevent any hotspots from forming that could impede performance or cause damage. Finally, when arranging multiple power modules on a board it is important to ensure adequate airflow paths are available for maximum thermal efficiency. By optimizing device placement for these factors you will achieve optimal power module cooling performance and reliability.
5. What materials should be used?
When selecting power modules for an application, it is important to consider the materials used in their construction. Materials such as copper and aluminum are common choices for power module heatsinks due to their thermal properties, while other materials such as graphite-filled pads or phase change materials can be used with power modules depending on the specific application. It’s also important to select power module components that are rated for high temperature operation and have the appropriate insulation ratings for your application. Ultimately the best material selections will depend on your particular power component cooling requirements.
6. What are the dimensions of the heatsink?
The dimensions of the heatsink should be determined based on the power dissipation, power module size, and other factors such as airflow paths. Generally speaking, a heatsink with a larger surface area will provide more efficient cooling for power modules due to its increased thermal mass. Additionally, power components should be placed close together in order to reduce thermal resistance between components and improve cooling performance. For more information regarding power module heatsinks it is recommended to consult with a specialist or refer to the power module’s datasheet or user manual.
Simulation tools, like Simcenter FloEFD and like Xpedition AMS can help answer basic questions like these when you are designing power modules.
To learn more about designing power modules, download our whitepaper, Power modules: A four-dimensional design challenge calls for a holistic design and verification approach.