Automotive Design with 3D Generative Design Tools from Siemens
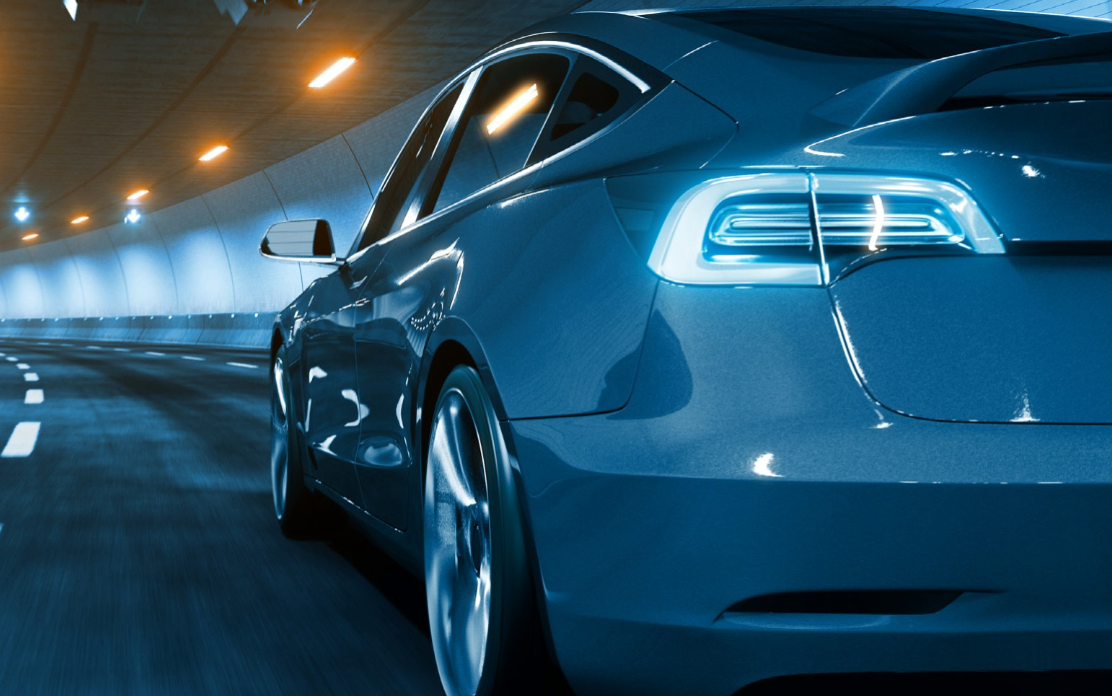
The automotive industry is undergoing profound transformations with the rise of electric vehicles, autonomous technologies, and more advanced network services. This growing complexity requires OEMs to adopt next-generation architectures that consolidate electrical control units (ECUs) into high-performance modes and connect vehicles to external networks through technologies like 5G.
These changes introduce challenges that extend beyond vehicle design, affecting the entire development process and requiring robust cross-domain collaboration.
In a recent webinar, Siemens explored how 3D-enabled generative design can be a game changer for the automotive sector, driving faster product development, improving collaboration across engineering teams, and reusing design data to lower costs.
Siemens’ Capital solution, part of the Xcelerator portfolio, integrates generative design to streamline electrical and electronic systems development, leading to significant gains in efficiency and innovation.
Harnessing the Power of Generative Design
Complexity of vehicle architectures is increasing drastically, due to advancements in electrification and autonomy. Traditionally, automotive systems involved distributed ECUs handling distinct functions, but now there’s a push toward centralized architectures.
This shift requires advanced design strategies and introduces new demands in terms of cybersecurity, sustainability, and efficient use of space within the vehicle. Siemens Capital software solutions provide a comprehensive response to these challenges through generative design.
What is Generative Design?
Generative design takes inputs like functional models and product plans and uses an algorithm to generate deterministic outputs that meet certification and manufacturing requirements. This automation saves time and ensures accuracy, which is vital when managing highly complex electrical systems.
Generative design enables innovation, because teams can shift their focus and energy to optimizing their architectures with reusable design elements such as circuits, layouts, and library parts.
Seamless Collaboration Across Domains
Cross-domain collaboration is another critical factor in modern vehicle development. For years, Electrical CAD (ECAD) and Mechanical CAD (MCAD) have operated in silos, making it difficult to align electrical and mechanical designs. This separation often leads to inefficiencies and costly errors. Capital bridges the gap between ECAD and MCAD through integrated tools that promote collaboration and streamline data exchange.
An important feature of Capital software is the digital twin, which enables engineers to create a virtual model of a vehicle and test design changes before building out physical prototypes. This process reduces errors, cutting costs and accelerating the development timeline.
Addressing the Complexity of Modern Automotive Systems
As more functions are consolidated into fewer ECUs, the physical wiring becomes more intricate, and the design far more complex. Siemens’s generative design capabilities enable engineers to synthesize wiring configurations that meet space, safety, and performance requirements – automatically.
The Importance of Automation in the Development Process
Automation is at the heart of Siemens’ approach to addressing the challenges of modern vehicle development. Through the use of 3D data and generative design, engineers can synthesize thousands of wires and splices that make up a vehicle’s electrical distribution system, helping to manage data volume while reducing human error.
Siemens’s solutions help OEMs to optimize configurations despite complexity using automation, while maintaining the flexibility to support different vehicle models and configurations. This capability is crucial for handling the diverse range of options that customers expect, ensuring that manufacturers can meet demand without compromising on quality or performance.
After space reservation studies, MCAD engineers create platform-level topology by adding inlines, break pathways, and separate harnesses, using data from Capital design. This topology, with devices and inlines, can be used to automatically generate a 2D E/E design with slots and bundles. Wiring synthesis defines and routes the wires for the individual harness level and the system routes the logical signals to define the necessary wires. It assesses the impact of optional devices and connections on harness complexity, using vehicle model constraints to derive the maximum complexity harness configuration for each harness, ensuring optimal wiring synthesis for each vehicle configuration.
Overcoming Integration Challenges and Managing Change
Capital Harness design and engineering tasks enables automation of composite and derivative harnesses using defined options, which can be exchanged to NX. This lets an MCAD engineer understand each derivative that exists and their placement In MCAD world to perform further analysis.
The traditional separation between ECAD and MCAD data has hindered smooth integration across domains in the past; however, Siemens Capital solves these problems with seamless data exchange and change management throughout the design process. This integration ensures that all necessary data, including connector and wiring information, is available for both electrical and mechanical teams.
What’s more, change management methodologies within the Capital system ensure that updates are automatically reflected across all stages of the design, minimizing the risk of errors and reducing the number of design iterations.
See the Demo
Siemens Capital can revolutionize your approach to vehicle design, streamlining collaboration across engineering domains. To gain a deeper understanding of how Siemens’ generative design and automation tools work in action, watch the full webinar for a live demonstration.
Learn more about Siemens Capital and Xcelerator portfolio to explore how these technologies can be integrated into your workflow to accelerate development, reduce costs, and build the next generation of vehicles.