Capital Systems Integrator: Solving for complexity with a platform generative flow
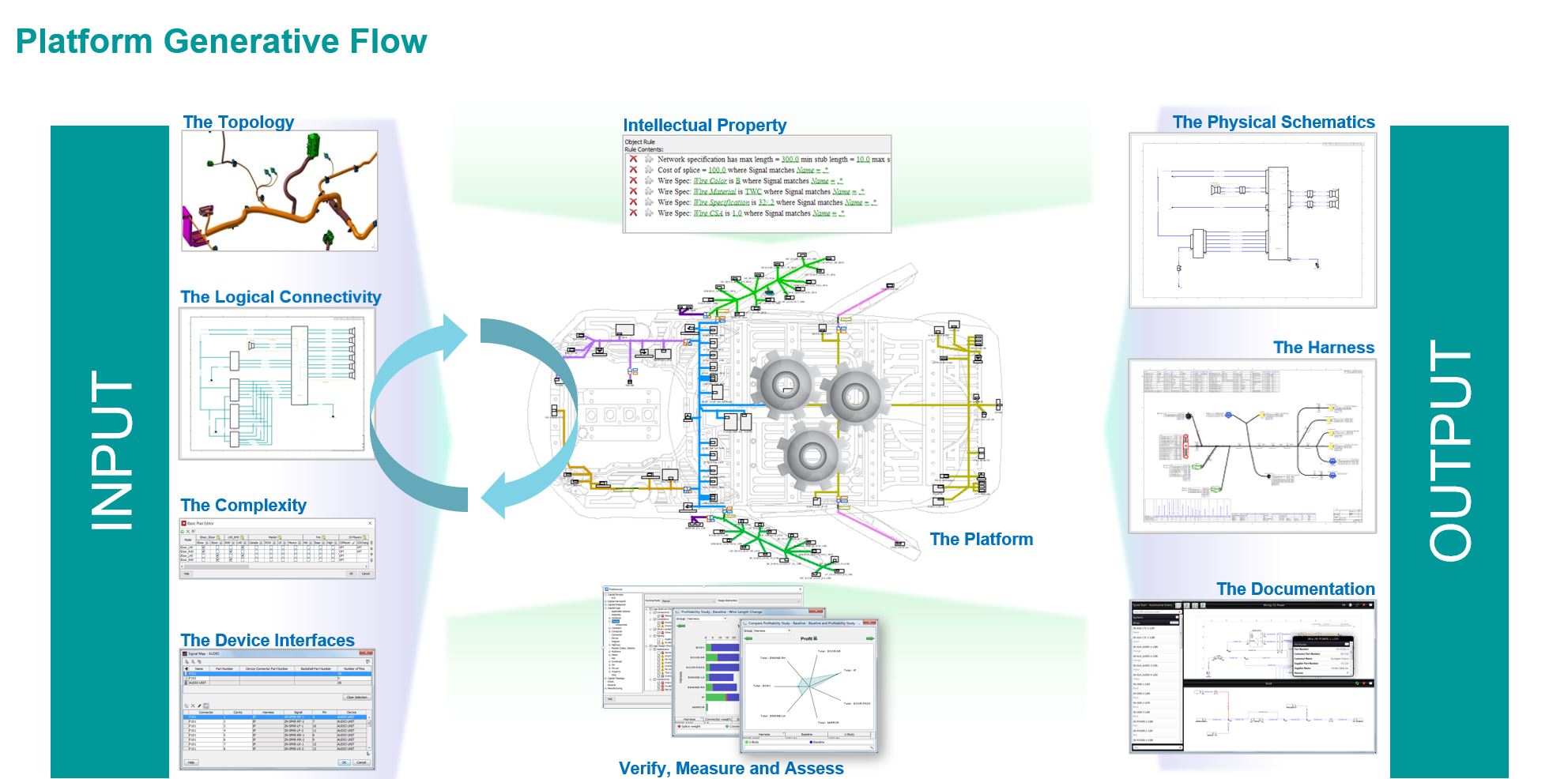
A generative flow approach enables “correct-by-construction” design by automatically generating accurate 150% wiring to support all allowable configurations
Modern vehicles are complex and software-defined – electronics account for about 40% of their total cost. Due to their increasing complexity, traditional design methods that rely on time-consuming, error-prone, manual tasks are no longer sufficient. Worse yet, these methods can delay development and impact quality. A generative approach enables “correct-by-construction” design by automatically generating accurate 150% wiring to support all allowable configurations at the platform level.
During a recent webinar, I, along with Erica Van Berkum, Senior Product Manager, Capital Electrical Distribution, explained the differences between traditional and generative design and walked attendees through a demo of the generative design flow using Siemens Capital. In this post, we’ll examine key components of the generative flow, and explain how they help designers navigate the increased complexity in today’s modern vehicles.
Traditional vs. Generative Design Flow
Today’s engineers are looking to reduce time spent on topology, complexity management and manual design optimization. Unfortunately, the traditional design flow lacks a way to optimize and validate designs in the platform context and depends purely on user-specific engineering know-how. Designing platform wiring schematics requires a deep understanding about the vehicle topology, and there is no mechanism in place to optimize the design. Developers can quickly become overwhelmed with changing requirements as they attempt to meet aggressive timelines.
By contrast, the generative flow manages data in a platform context, focusing on designing a complete vehicle, not just a single harness. Generative design enables users to capture and develop competitive IP, accelerate system integration and reduce design time and costs. As an added bonus, this approach enables teams to evaluate alternative architectures that improve the quality and performance of next-generation vehicles.
The figure below illustrates the generative design flow using the Capital platform:
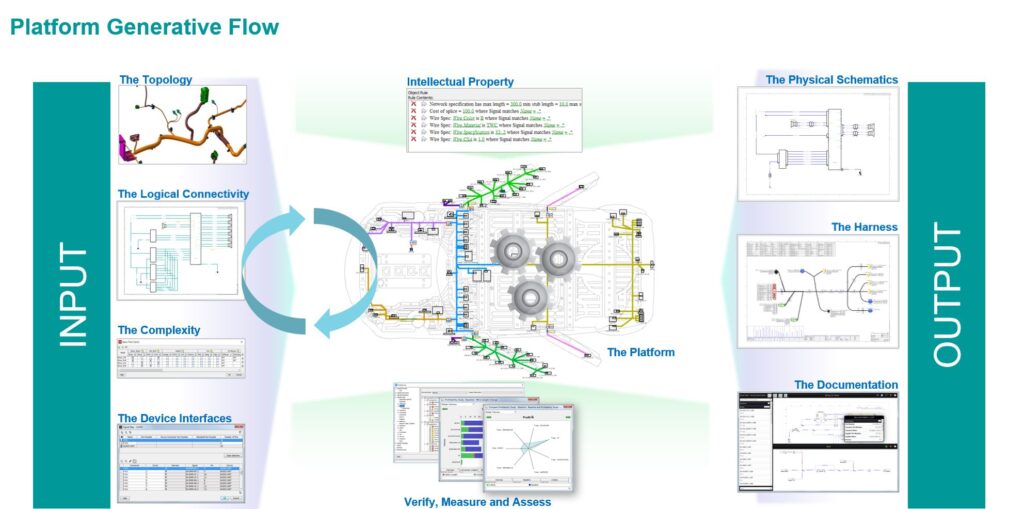
As you can see from the illustration, Capital Systems Integrator consumes the inputs and delivers consistent and repeatable wiring connectivity based on customizable design parameters. The generated connectivity is consistent across the complete vehicle, ensuring all configurations are supported.
The circle on the left represents the iterative process, which allows engineers to adjust design parameters and generate new wiring connectivity as needed. After the desired wiring is completed, the system synchronizes connectivity to the harness and generates physical schematics. In addition, the service documentation process also consumes data in the platform context. By iterating the design from the beginning, engineers can ensure data quality and continuity throughout the design process.
Key Components of a Generative Design Flow
The generative design flow consists of the following components:
- Logical connectivity: Logical connectivity is a key input for Capital Systems Integrator as it generates physical wiring. To generate any kind of complexity, option tagging must be applied to the logical design objects such as devices, device pins and nets. Option tagging can be simple, describing the applicable feature in a straightforward manner, without complex option expressions. By eliminating the need to add physical information to establish connectivity, Capital Integrator increases the reuse of logical designs across projects, boosting productivity.
- Wire generation: Capital Systems Integrator consumes the logical connectivity and calculates a cost-optimized solution for each configuration. The synthesis engine (which generates the physical connectivity) takes into consideration all options applied to logical design objects, bundle and slots. Additional design parameters control the preferred termination method – such as splicing versus multi-termination – and help to determine valid routing paths. At any point in time, the synthesis engine ensures that the wiring is consistent across the platform.
The generative flow supports the “right first-time” design approach. Once the Capital environment is set up to meet your company’s standards and requirements, you can easily adjust project-specific parameters without reinventing the wheel, further accelerating the design lifecycle.
- Derivative harness complexity: Capital Level Manager (CLM), an Integrator add-on tool, can be used to automate harness-level complexity and deliver consistent and repeatable results. This works by leveraging a derivative flow. Parameters for optimization include cost metrics, annual volumes, take rates, option packages and giveaway restrictions. The CLM optimization results can be used to determine if a given harness family becomes a modular candidate – for instance, when an expected giveaway savings cannot be achieved.
- Modular harness complexity: Capital Systems Integrator gives engineers the flexibility to apply customized modularization to manage complexity efficiently. The ability to consistently generate option expressions on the wiring is essential to automating and validating a modular design and is a core functionality of the Capital Integrator synthesis engine.
- Harness design and synchronization: In Capital, data is traceable and consistent across abstractions. This enables 150% design content for a single harness to be synchronized between the platform and the harness abstraction. Once the data is generated, it can be enriched and processed, as needed.
To summarize, Capital Systems Integrator consumes logical connectivity and auto-generates wiring based on customizable design parameters. The synthesis engine ensures that the generated connectivity is consistent and supports all required configurations. Using one tool – Capital Systems Integrator – you can design multiple platforms, and for every harness family, a different complexity concept can be applied.
Watch the full webinar to see a demo of the concepts explained in this blog post. You can also learn more information about the Siemens Capital suite of tools for automotive design here.
Stefan Fischer, Senior Product Manager
Stefan has 20+ years of experience in the automotive market and has been working with the Capital portfolio since 2005. He held positions at Yazaki Europe Limited including Capital Generative deployment for production lead, tools and methods lead engineer, advanced engineering engineer, system engineer, resident engineer – production support at OEM plant, and routing engineer.