An exploration of wire harness engineering
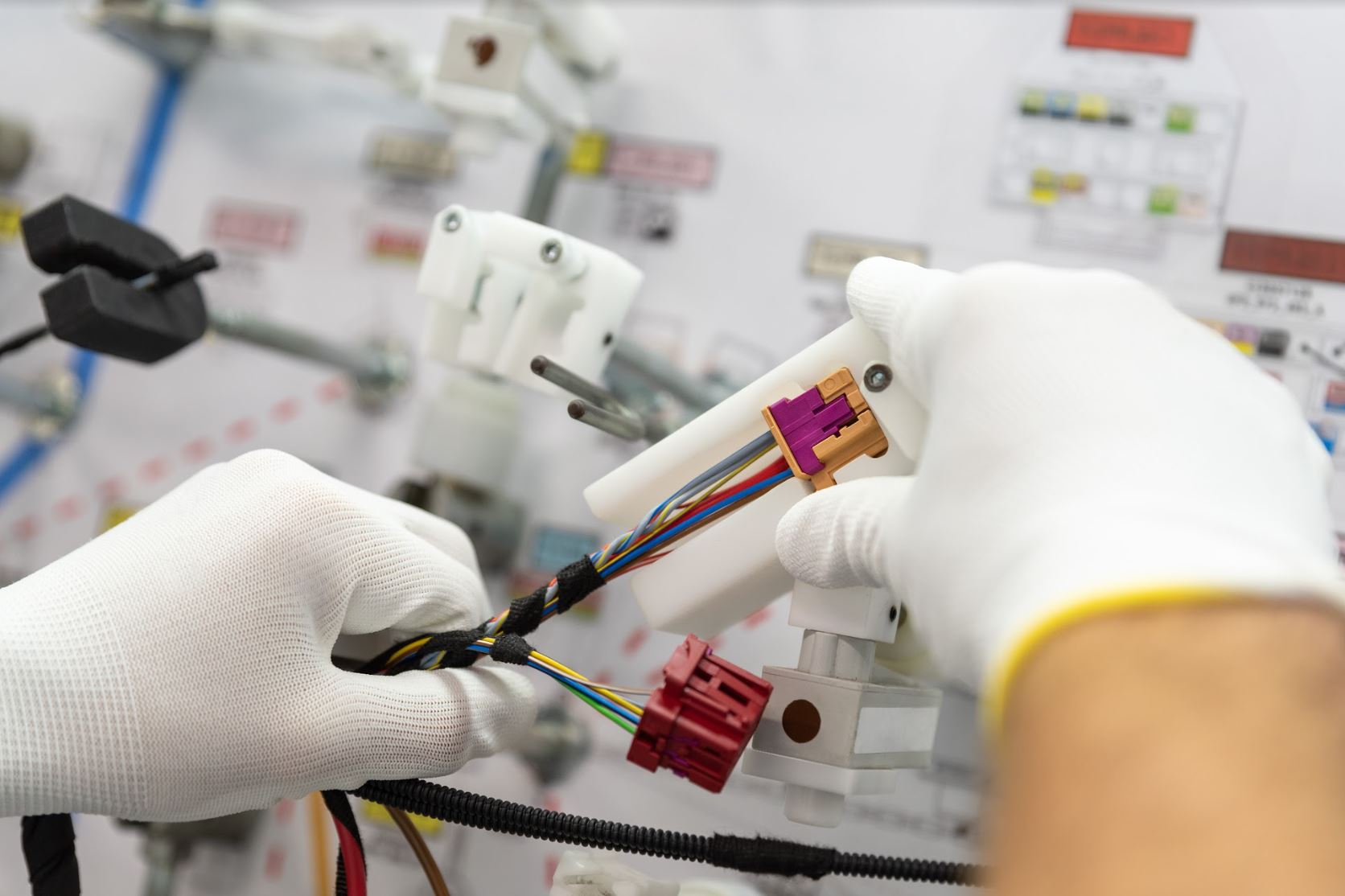
While wire harness engineering faces shorter program launch cycles and increasing price pressure, coupled with increasing product and configuration complexity, could the industry still be poised for growth opportunities?
The continually evolving automotive and aerospace industries faces multiple challenges owing to the demand for advanced features, autonomous control and the growing need for electrification. These megatrends directly impact and create the need for a highly sophisticated electrical and electronic (E/E) systems, which emphasizes the wire harness.
Recent market reports have stated that both automotive and aerospace wiring harness engineering industries are pointed towards growth. This is due in part to the very challenges that the industry is facing—there is a forecasted need for technology that will help wiring harnesses become more light-weight with smaller bundle diameters for instance, enhancing performance while refining the technology.
To understand how the market may move, it helps to have an introduction into the wiring harness itself. A wire harness is a system of insulated conducting wires bound together with insulating materials, used in the electrical system of a motor vehicle, complex machine or aircraft. Wire harness engineering is the development process of an electrical foundation for the safe and reliable distribution of power throughout a system. It forms the foundation of reliable, cost-effective and successful product design and manufacturing.
The design, engineering and manufacture of wiring harnesses is complicated by shorter program launch cycles and increasing price pressure, coupled with increasing product and configuration complexity.
However, despite the challenges, the technology is very much needed. Harness design software helps many companies address wire harness engineering challenges. Powerful design automation capabilities and model-based wiring harness engineering flows, help harness manufacturers cut costs, improve product quality and boost efficiency.
In some modern vehicles there are approximately 40 different harnesses, comprised of roughly 700 connectors and more than 3000 wires. The bundling of wires and cables into a wire harness simplifies connection to larger components as a single unit for drop-in installation, instead of connecting every individual strand.
Challenges in wire harness engineering
Although wire harness manufacturing has been around for more than a century, today’s manufacturers face myriad challenges with low margins, loss of tribal knowledge, complex processes, continuous change and stringent requirements for quality and delivery. By implementing model-based workflows, manufacturers can unify previously fragmented design and manufacturing domains by automating data exchange and facilitating cross-domain decisions. Through the integration of design rules that support automation and consistency across the engineering process, tribal knowledge can be captured instead of lost.
Harness design software
While digitalization is an essential step toward the implementation and realization of Industry 4.0, the success of harness manufacturers is dependent upon the ability to accurately design, optimize and cost the manufacturing processes, labor, material and resources required to produce wire harnesses. Wiring design software, such as Siemens Capital software, enables harness designers to accomplish these goals, with the potential to:
- Reduce design error by 50%,
- Improve quote-to-production cycle time by 30% and
- Improve formboard design time by 85%.
Learn more about Wiring Harness Engineering here.
Research how Capital products can help you tackle your wiring harness needs.
Sign up for our upcoming webinar on the growing need for digitalization in the harness industry and see how Siemens’ advanced harness design and manufacturing engineering solutions help companies transform challenges into competitive advantages.