The Four Horsemen of Wire Harness Manufacturing
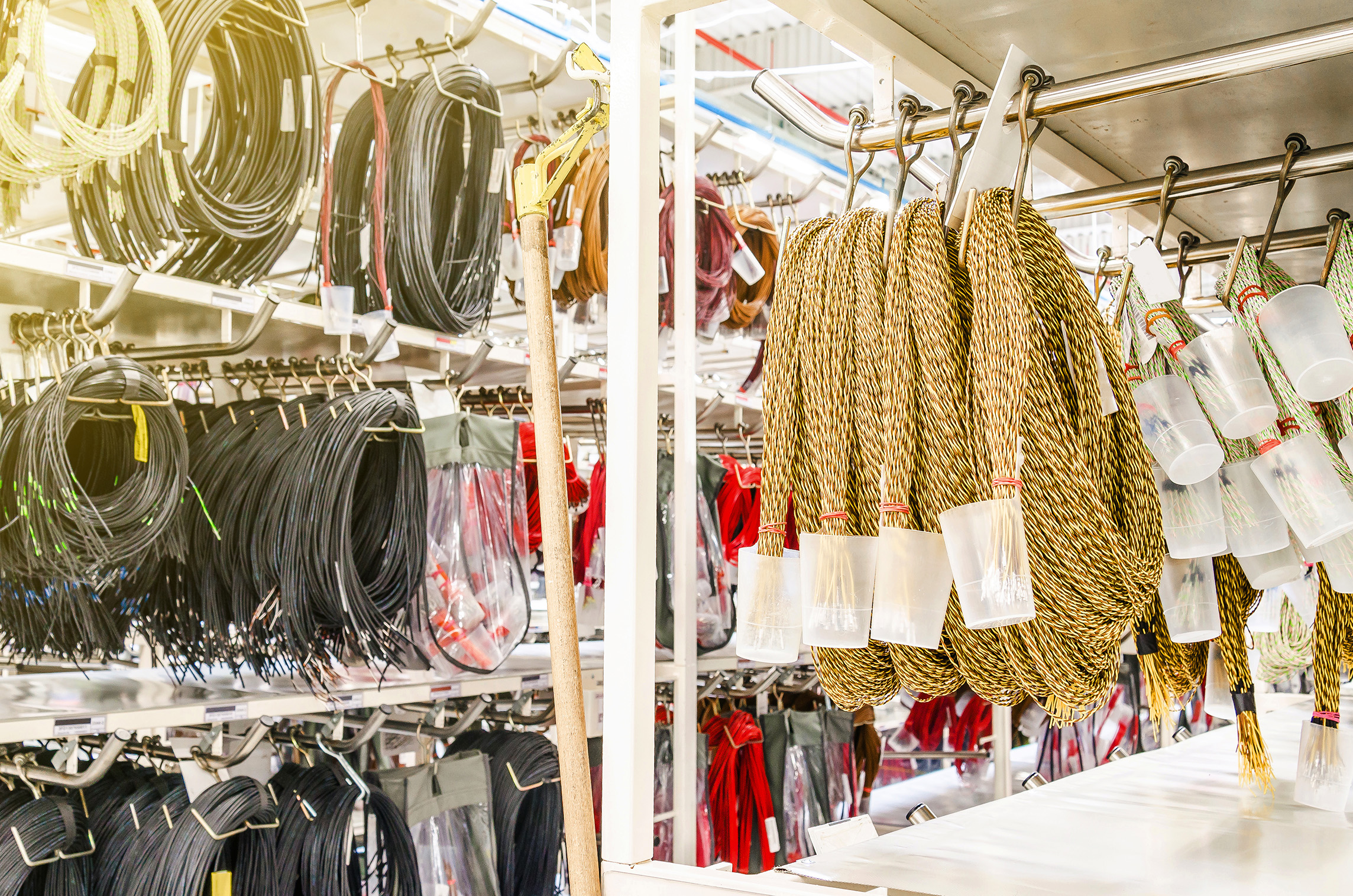
Growing demand for automotive E/E features also translates to a growing wire harness manufacturing industry. Analysts predict that by 2023 the automotive wiring harness industry will grow to over 70 billion dollars in yearly revenue and more than 91 billion dollars by 2025 (Future Market Insights, 2016). Even still, wire harness manufacturers often operate on small profit margins where unexpected costs can quickly prove disastrous. It is therefore critical for harness manufacturers to minimize costs during harness production and delivery. In a new whitepaper, we examine the four main sources of unexpected costs during wire harness manufacturing and shipping and discuss how modern digital solutions can help companies control these costs. So, what are these sources of cost?
The main sources of cost variability arise during harness production and delivery are rework, obsolescence, premium freight and manufacturing inefficiency (figure 1). Collectively, we have come to think of these as the ‘Four Horsemen of Wire Harness Manufacturing’. These sources of cost are common across the industry, and their effects on the bottom line of a harness manufacturer can be significant. Reduction or elimination of harness rework alone can save millions of dollars each year for the harness manufacturer.
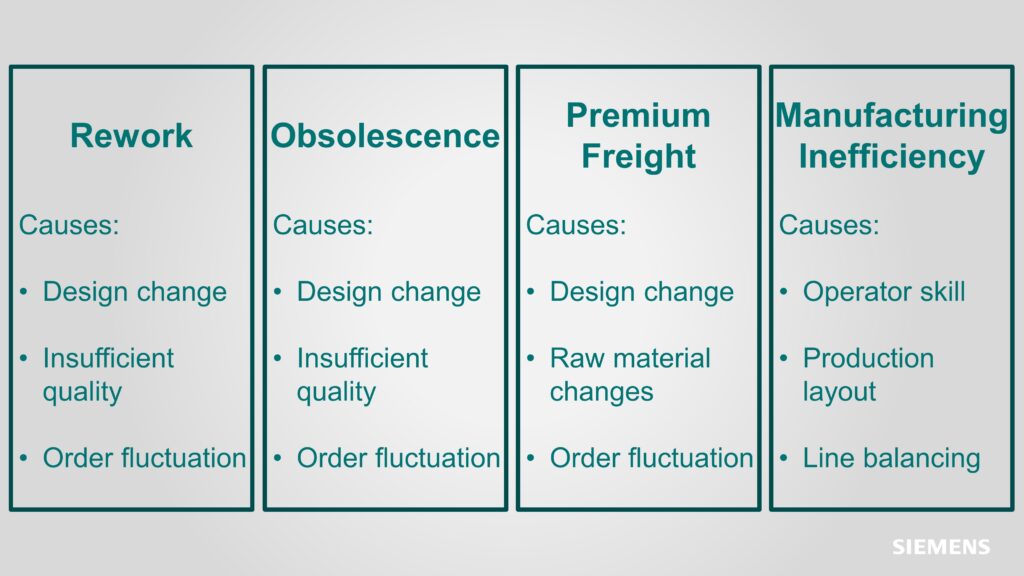
Figure 1: Rework, obsolescence, premium freight and manufacturing inefficiency are the main sources of cost variability for harness manufacturers.
This is, of course, easier said than done. The Four Horsemen are highly intertwined and driven by several factors that are hard to control. Harness rework, for example, can be driven by design change, quality issues and changes in order mix or volume. As the harness manufacturers reworks harnesses to meet updated design requirements or solve quality issues, they may need to rely on premium shipping options to fast-track needed materials or to get reworked harnesses to the customer as quickly as possible. In the worst case, any harnesses that cannot be reworked are considered obsolete. While each situation has unique challenges, the net effect is unplanned cost that eats into the harness manufacturer’s profitability.
Fortunately, modern electrical system and wire harness engineering software solutions, such as Capital from Siemens Digital Industries Software, feature capabilities designed to combat the root causes of rework, obsolescence, premium freight and poor manufacturing efficiency. Capital’s robust digital thread and automation features prevent design errors upstream, ensuring they never reach the production floor. Traceability of design revisions and harness levels back to the initial requirements ensures that harnesses are produced to meet specifications and original design intent. Engineering changes can also be incorporated into harnesses more quickly and safely, preventing potential rework cost. And finally, integrated manufacturing planning and simulation tools can help optimize harness production and even adapt to changes in take rates or late engineering changes.
To learn more about the Four Horsemen of wire harness manufacturing and how Capital can help minimize unexpected costs, please download our new whitepaper, 4 horsemen of wire harness manufacturing.
You might also be interested in: