Modeling the true cost of a wire harness
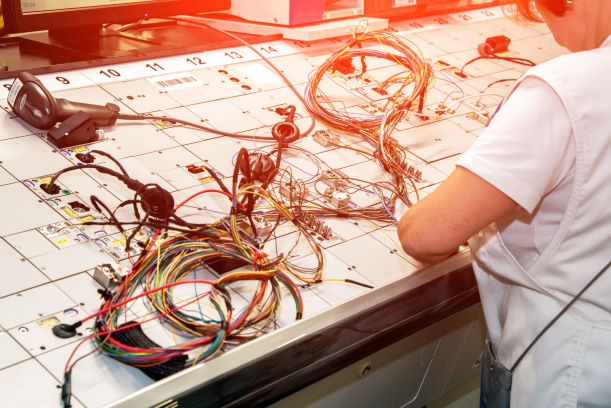
An automotive wire harness rarely has just a single part number that can be ordered and installed in a vehicle. Typically, there are many different versions of the same harness based on the orderable content in the vehicle (figure 1). These versions, often called harness levels, will each have a unique part number. The quantity of these levels and their content is what is typically called complexity. This complexity has a significant impact on the cost of the harness.

Quantifying these costs is often very difficult, especially with manual methods of deriving and costing the complexity solution. Therefore, traditionally, consideration of these complexity related costs has been with overly simplified cost modeling techniques.
The State of the Art
It’s not uncommon for organizations to have existing rules-of-thumb as a means of trying to capture these costs. For example, an organization might simply state that every new part number (harness level) equates to some standard cost (ex: $25k). This method is certainly better than not considering complexity related costs at all, and historically has been ‘good enough’.
Today, many automotive OEMs and Tier Ones are struggling with very thin margins and are looking to take pennies out of the material cost of the vehicle. In this kind of an environment, over-simplifications and rules-of-thumb just aren’t ‘good enough’. Without proper incentives, designs will be suboptimal and money will be wasted.
Some judgment is required to create models that are simple enough to be understood while capturing enough detail to guide engineers to correct decisions. The reality is that there are thousands of variables that slightly affect the cost of designing, manufacturing and shipping a harness. The prevailing ocean currents might affect the amount of fuel required for an ocean freighter to cross the Pacific. But, is such an unchanging and insignificant variable likely to cause one complexity solution to be more optimal than another? If not, it is probably safe to ignore it in the model.
Complexity related costs are particularly difficult to quantify since they’re often transparent to organizations and are absorbed in things such as logistics, plant down time, part scrap, etc. It is ultimately up to each organization to determine the level of detail that should be captured and modeled for their business realities with the ultimate goal of enabling optimal design decisions.
Piece Cost versus Complexity Management Cost
Wire harness manufacturers have a very good understanding of what it costs to assemble a wire harness. This piece cost includes the raw materials from the various tier two suppliers, the labor associated with manipulating and assembling these raw materials, the logistics for storing and shipping a single finished product and so on. The piece cost of the wire harness is generally inversely related to the number of harness levels (figure 2). In other words, as the complexity solution reduces the number of levels, the costs go up, while additional levels reduces the piece cost.
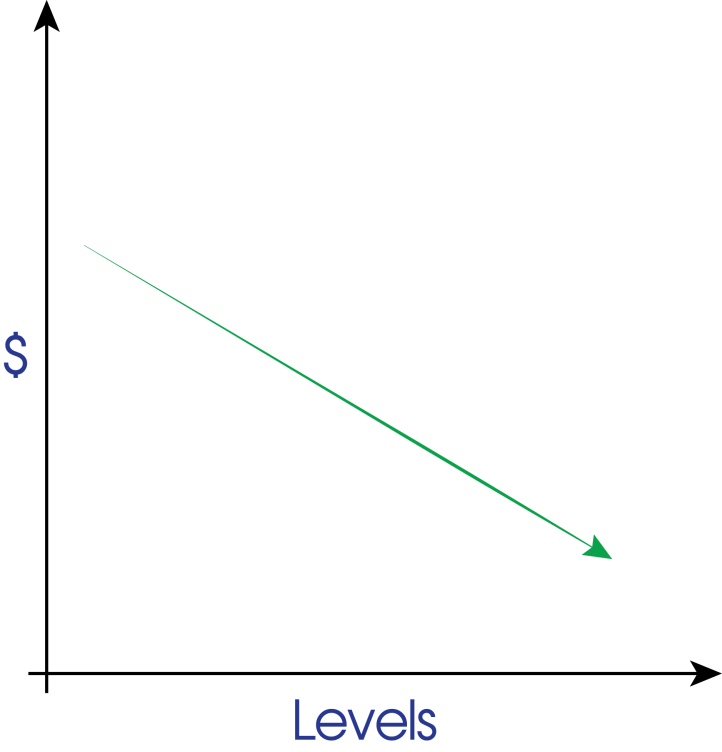
There are additional costs, however, that are not captured in the piece cost that increase with additional levels (figure 3). These are called Complexity Management Costs. By definition, these are costs that are directly related to the number of levels. As a short example, the more levels required for a harness, the more inventory that must be kept on hand. Additional inventory equates to additional costs. As mentioned, it’s these costs that are difficult to quantify and are often ignored or simply estimated with rule-of-thumb calculations which typically just aren’t good enough.
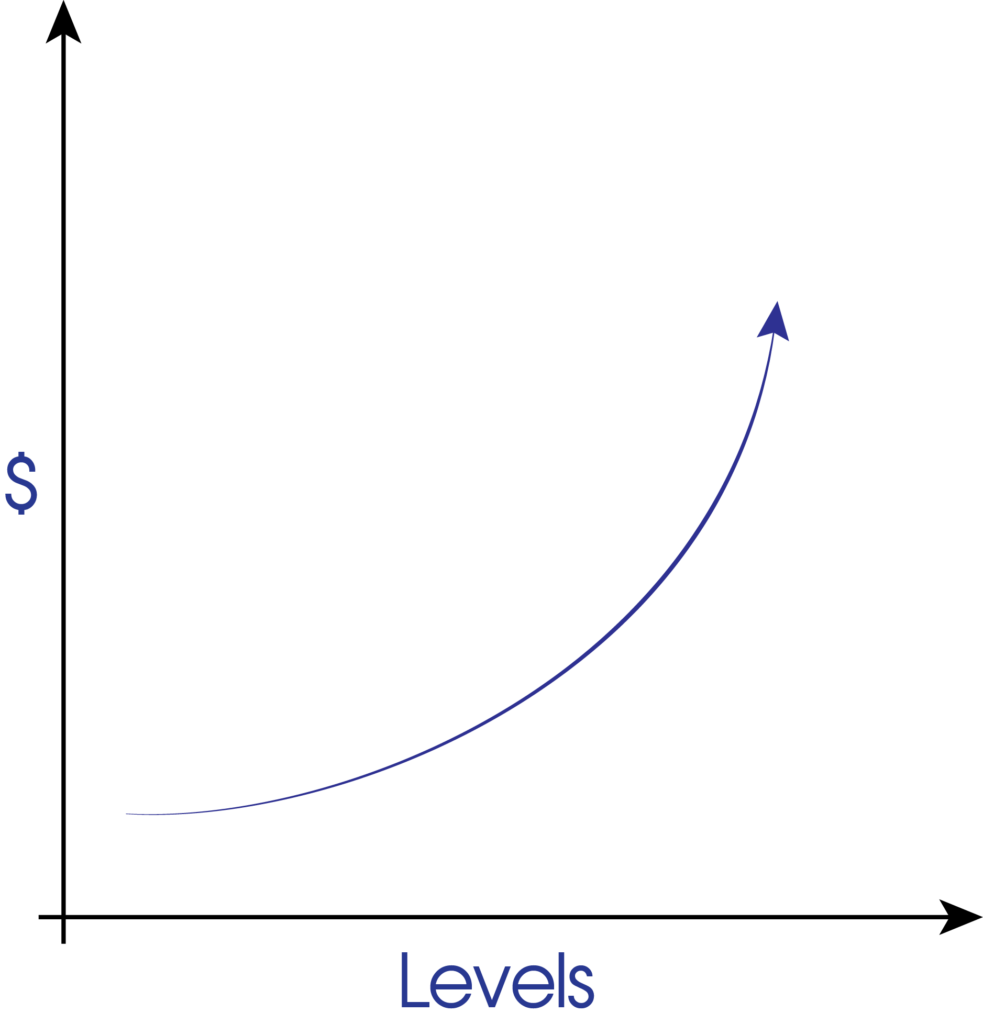
The true cost of a wire harness is the summation of these two curves, called the Complete Cost Model (figure 4). The ideal complexity solution is the one that is at a minimum spot on the combined cost curve. Without adequately modeling this combined cost curve, it is impossible for a human or an algorithm to arrive at this minimum point except by pure chance.
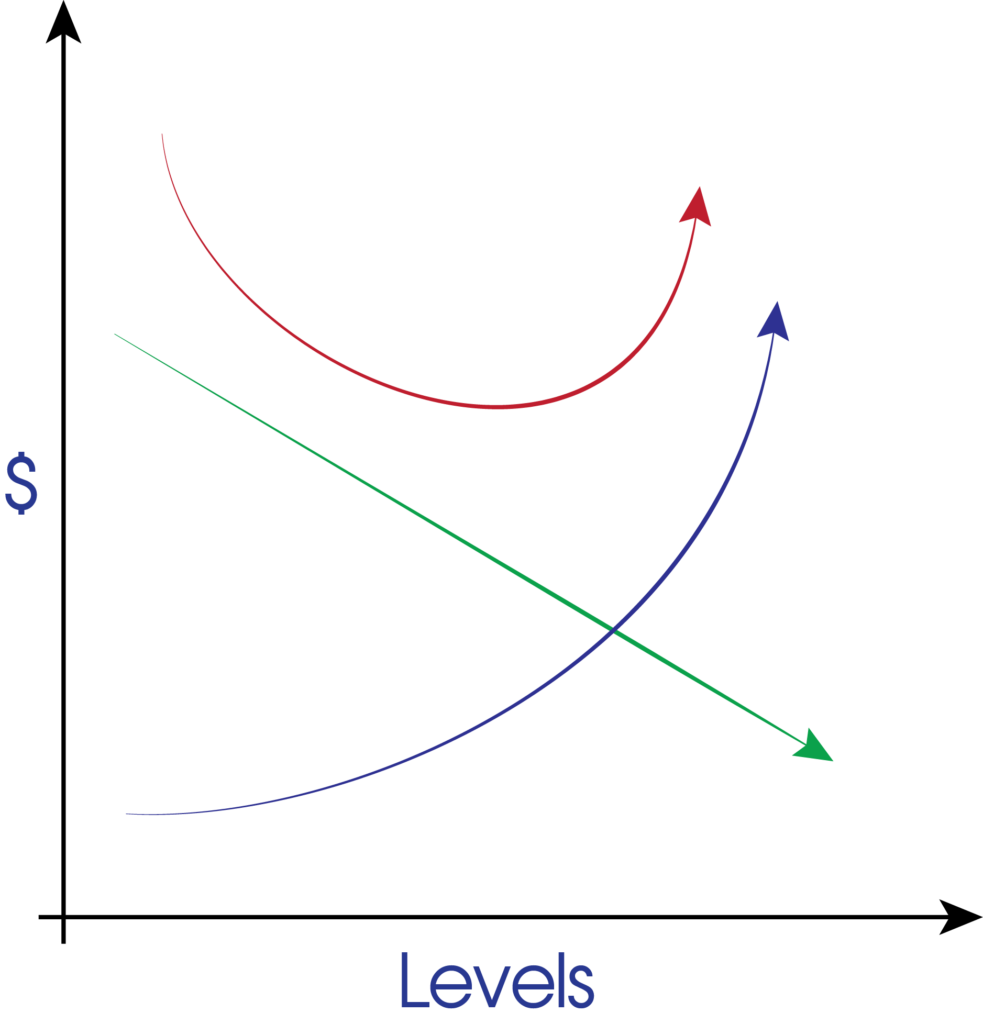
Considering the impact of variation complexity on the overall costs absorbed by the organization is less daunting than one might initially think. Cost models need only be good enough to make correct decisions. To learn more about defining and modeling the various factors that affect the cost of a harness, please read our whitepaper Modeling and Optimizing Wire Harness Costs for Variation Complexity. This paper includes a number of real world examples of such costs, a methodology for defining these factors so that they can be modeled, and guidance on methods for modeling them based on how their variability affects overall costs.
Historically, automotive companies have focused on understanding the piece costs of a wire harness and in many cases largely ignored the impact of variation complexity on the overall costs absorbed by the organization. With vehicles becoming more complex than ever, these methods will not suffice moving forward.