Navigating new pressures in automotive E/E systems design
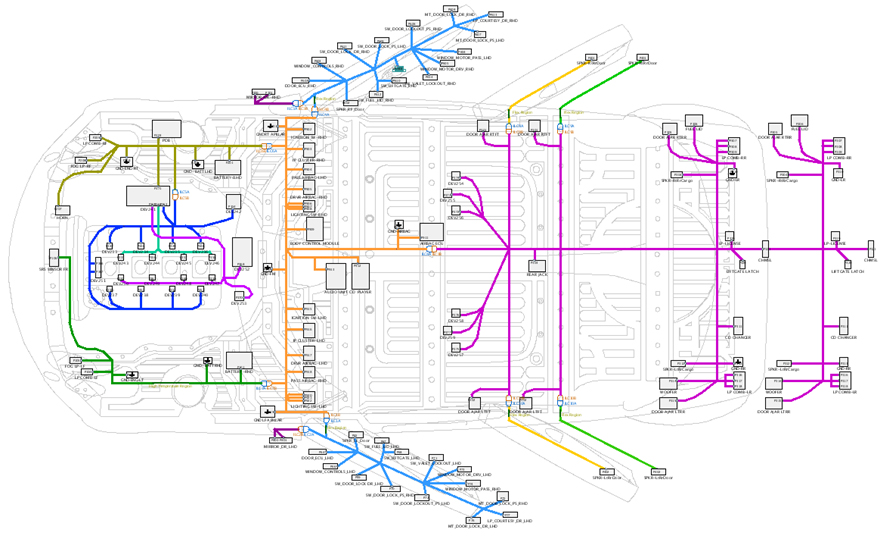
Automotive executives see innovation as critical to the success of their companies. Today, that innovation is largely the result of electrical, electronic, and embedded software advancements. The increasing implementation of advanced driver assistance systems (ADAS), vehicle connectivity, and active noise cancellation is enabled by advancements in sensor, processor, networking, and other technologies. These trends are driving three new sources of pressure for automotive companies: growing design complexity, increasing cost, and frequent cross-domain change management. The pressures of cost, complexity and change management create a demanding environment in which engineering teams are pushed to design increasingly complicated vehicles on tight budgets and shrinking timelines.
Growing complexity in automotive designs is a twofold problem. Individual vehicles are becoming highly sophisticated cross-domain systems, blending electrical wiring, mechanics, electronics, and software. As more features become electrically or electronically enabled, vehicle-level complexity will continue to rise. On top of this, automotive manufacturers must account for the complexity driven by customizability and vehicle variants. Vehicle models are offered with an array of optional systems and features that can produce millions of unique vehicle configurations (figure 1). In fact, just 20 optional features results in more than 1,000,000 unique buildable vehicles. For companies that operate in global markets, this number is even larger as regional differences can affect the features that will be in demand.
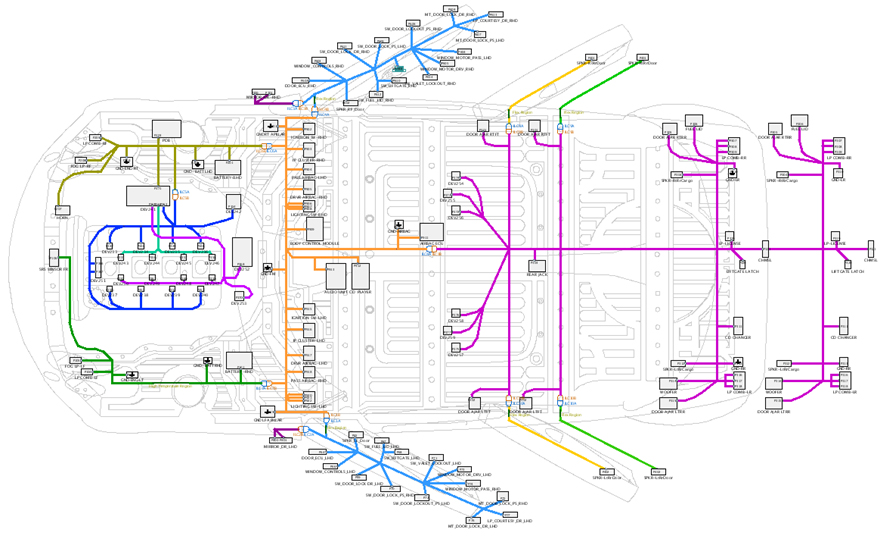
Next, cost is a paramount concern in the intensely competitive automotive industry. Increasing demand for electric and electronic features means that companies must keep larger inventories on hand, parts become obsolete driving re-design efforts, and miss-builds become more likely as automakers handle massive numbers of design variants. Design, marketing, manufacturing, logistics and engineering groups must work in concert to meet market demands for features and performance while managing production cost. Leveraging data from all of these domains is critical to constraining these costs.
Vehicle recalls, however, may prove to be the most costly. A problem discovered after the car is on the market is up to fifty-times more expensive to fix than one that is identified in development. Large-scale recalls are even more expensive because they cause damage to the manufacturer’s brand and reputation in addition to the financial cost of recalling cars.
Finally, during E/E systems development, engineers must consider the impact of design changes in multiple domains. Changes in the requirements for the vehicle platform and systems are the most obvious as they can require all new connectivity schemes. Each change affects the rest of the system, and the unforeseen effects can be very difficult to predict. Migrating an ECU to a new location or network in the architecture may affect performance elsewhere in the system. This change in behavior may cascade, causing any number of sub-systems or functions to fail. Such a change can even completely invalidate the technical implementation of the architecture, driving the re-design of multiple systems.
Navigating the Storm
If a design process could address all three of these issues, what kind of capabilities would it need? This design flow would need to help engineers manage increasingly complicated electrical and electronic systems, costs that result from this complexity, and more numerous design changes that have wide-ranging effects. Generative design fulfills each of these requirements.
Generative design uses automation to generate architectural proposals for the logic, software, hardware, and networks of the electrical and electronic systems of a vehicle (figure 2). This enables engineers to iterate on these proposals, optimizing for performance, reliability, and weight. Through generative design, teams can address the rising challenges of complexity, cost, and change management.
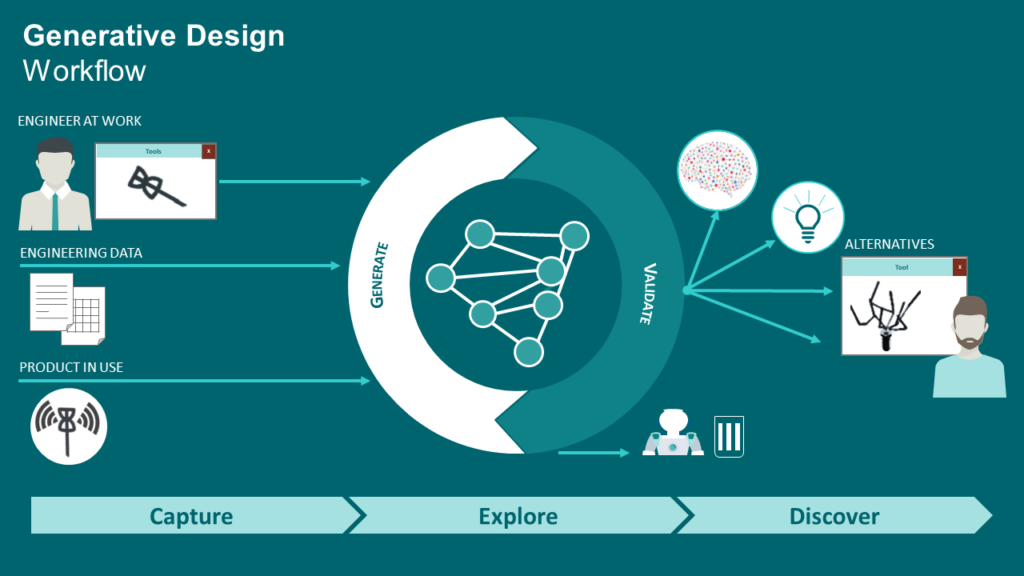
Employing automation throughout the design process will help design teams manage complexity without increasing time-to-market. Automation empowers engineers to focus on the most critical aspects of E/E systems design and verification, and reduces the need for design changes by quickly generating proposals that engineers can evaluate and iterate on to reach optimal designs.
Teams must also be able to re-use validated data across vehicle platforms to improve quality and reduce development costs. Design re-use accelerates development cycles and reduces change orders by leveraging known-good design data in a new vehicle platform. This prevents the design teams from spending time and resources manually re-designing vehicle systems that may already exist. Generative design enables engineers to apply existing data to new platforms effortlessly to maximize the benefits of re-use.
Generative design can enable automotive design teams to overcome the pressures of complexity, cost, and change management. Implementing such a flow, however, requires a tool set that supports advanced design automation, a holistic view of the project in a platform context, and seamless integration between design domains and upstream and downstream tools. Part two will explore how generative design can be achieved in electrical and electronic design, delivering engineers tooling to deal with complexity, cost, and change management.
Read more here: What is generative design and why do you need it?