Electric and Autonomous Vehicles Introduce New Dilemmas for E/E System Design
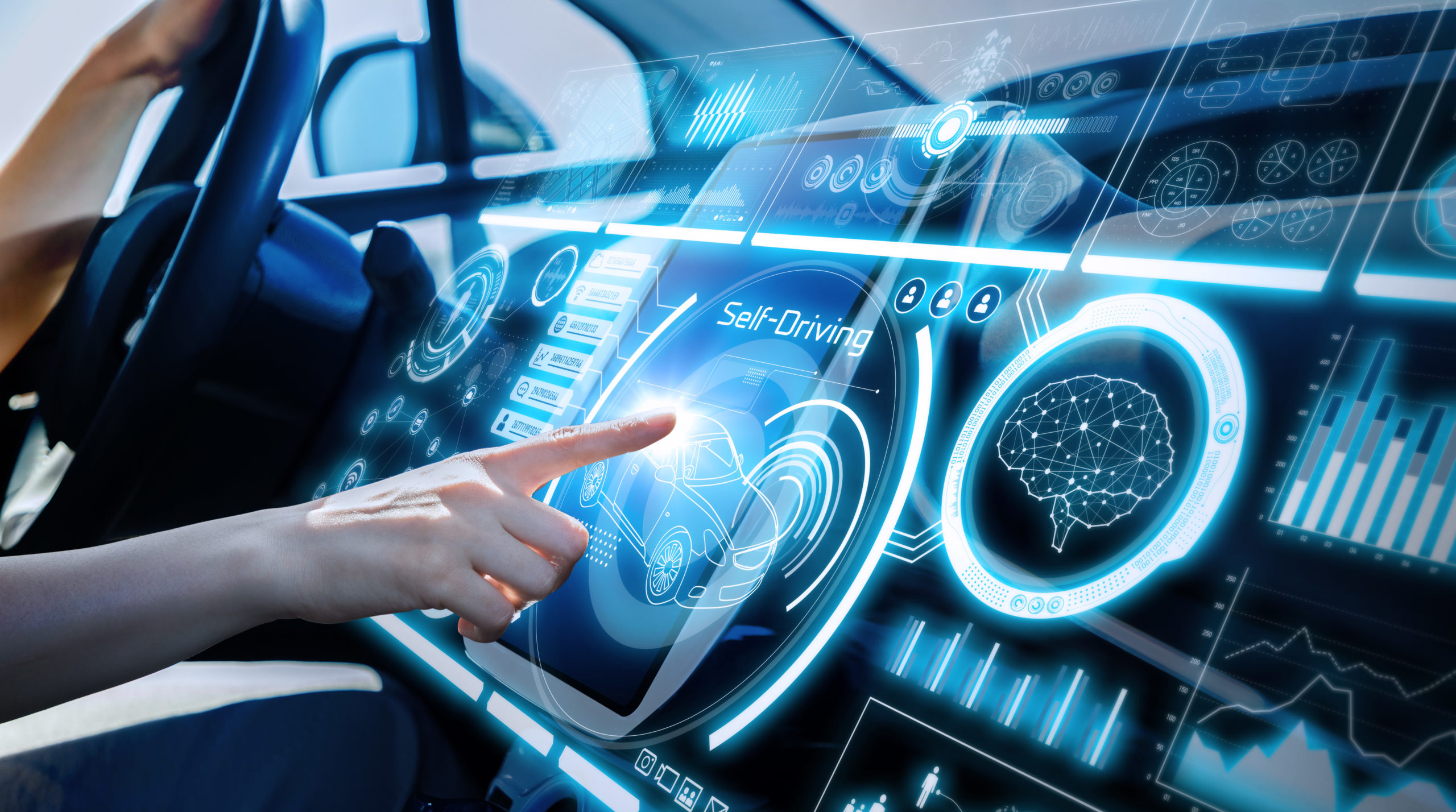
In the automotive industry, several dilemmas are created as advanced vehicle technologies are introduced to realize the trends of tomorrow in automotive: autonomy, connectivity, electrification, and shared mobility (ACES) (figure 1). These trends are not progressing in isolation; they are interconnected, but drive different challenges and aspects of product development.
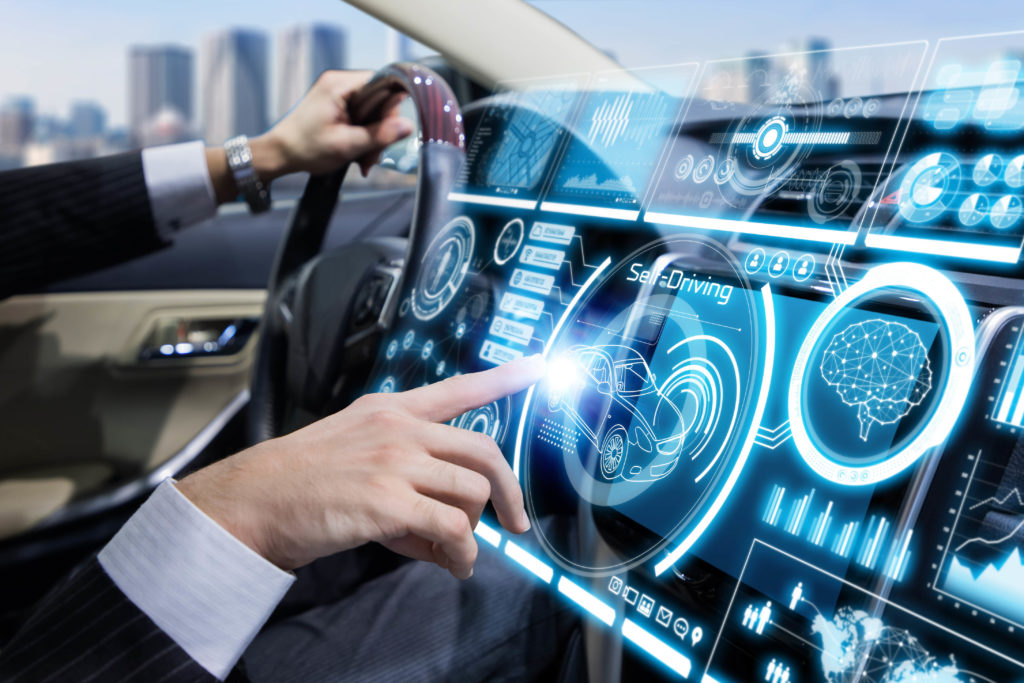
Electrification and autonomy are driving OEMs and EV startups to develop clean-sheet vehicles and E/E architectures to maximize the profitability of the EVs they sell (McKinsey & Co., 2019). However, this approach comes with challenges at the architecture and vehicle levels (figure 2):
- Significant weight increase requires new architectural optimisation.
- New safety considerations for high-voltage (HV) systems driven by regulations.
- Multiple voltage architectures to support the vehicle powertrain, sensors, ECUs, and other devicesdemands verified separation of cabling and automated checking of the electrical system design.
- Previously unrelated systems are now highly interdependent, e.g. energy storage, braking, and power electronics in EV braking systems.
- A ‘rush-to-market’ for EVs requires increased design automation and virtual verification.
- Manufacturers face extreme packaging challenges as they try to fit the largest HV battery in the vehicle as possible.
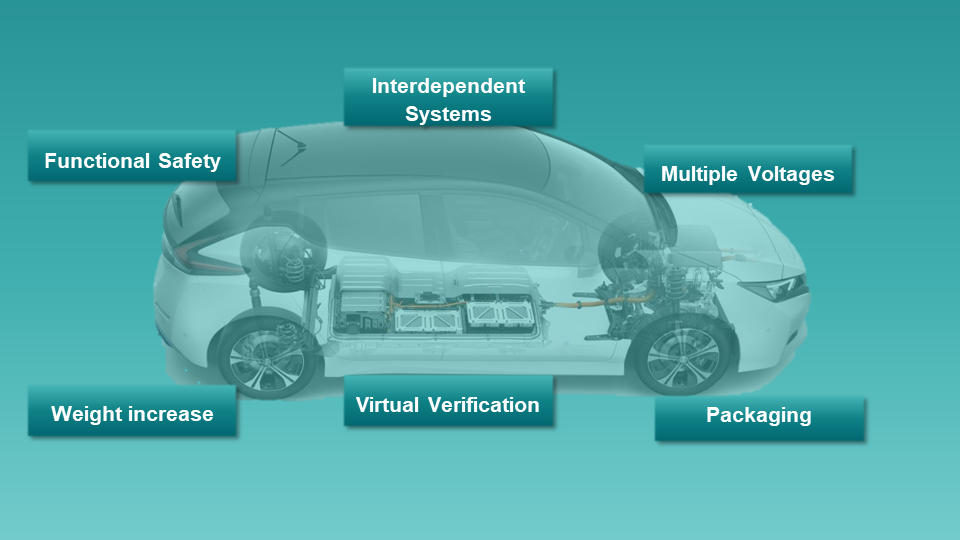
When we look at the more detailed design and implementation requirements of the E/E system for an electric vehicle, three key areas need to be considered. First is the integration of the E/E system with the vehicle body and mechanical components. The mechanical and structural design of the vehicle must account for physical constraints of the E/E system such as wiring bundle diameters, minimum bend radii, and, of course, the battery.
Second are the designed-in safety assurances for the E/E system implementation. To enhance the E/E system safety, electrical engineers investigate signal routing and ensure proper separation between signals that may cause interference. Critical systems also require redundancies to prevent failures from becoming catastrophic. The third key area is the use of simulation to verify the E/E system implementation early and often. Electrical load analysis solutions can help engineers to test the system under various simulated road conditions, such as rapidly alternating battery charging and discharging to simulate stop-and-go traffic.
Finally, the content and complexity of E/E systems is experiencing another step change due to the arrival of automated driving technologies. An autonomous vehicle will need thirty or more additional sensors to perceive its driving environment, and significant new processing power to interpret all of the new sensed data. This will add a significant amount of E/E content, and thus weight and complexity, relative to a non-automated vehicle. For instance, GM found that a self-driving version of the Cruze compact car had forty percent more hardware than a human-driven counterpart.
How are companies responding to these transitions?
As we work with companies across the world grappling with these challenges from electrification and autonomy, we see a number of trends in how the most forward-looking are adapting their approach, processes, and tools for vehicle development. These companies are at the point where today meets tomorrow for E/E systems engineering. Companies on the forefront of this transition share some key characteristics: they have integrated E/E engineering disciplines, accelerated their adoption of automation tools, began virtual verification at the concept stage, and established a cross-domain model-based systems engineering product development approach.
Integrating E/E engineering disciplines early in the design process minimizes late design changes that can delay development, simultaneously incurring cost. These changes commonly surface when integrating systems for the first time in development vehicles. Companies often find that different groups of engineers developing systems in parallel do not always make the same assumptions about system interfaces, data exchange formats, signal scaling, offsets in CAN messages, and more. This is especially common when engineering teams are under-resourced and under significant pressure to deliver hardware for management milestones and to meet imminent start of production (SOP) timescales.
Next, successful companies are automating processes wherever and whenever they can. New entrants into the automotive industry, especially those whose background is in software development, are often the most progressive in this regard. Engineers at these companies possess a cultural expectation to automate everything possible, and thus have experience with implementing such automation in a variety of contexts. Companies used to operating in the safety-driven environment of automotive or aerospace have approached automation with more reservation, but established OEMs are responding to this trend.
Virtual verification at the conceptual stage allows engineers to proceed through the design process knowing that accurate models undergird their actions (figure 3). With accurate models, engineers can make better design decisions and optimize systems more quickly while still achieving the original design intent. Tight integrations between mechanical and electrical designs at this early stage are vital to ensuring systems perform as expected when they are realized in physical vehicles.

Finally, successful organizations are implementing model-based systems-engineering practices to manage the exploding complexity of the many interdependent systems in their vehicles. Already complex systems, such as braking systems, are rapidly becoming more difficult to integrate. Digitally tracing requirements and their realization in electrical system designs is the only way to develop systems of this complexity. As a result, designs have to be driven and managed from the system-level, not just at the start of programmes, but all the way through the programme. Moving forward, this management will need to continue after SOP, as service-oriented architectures enable over-the-air updates to vehicle functionality.
These leading companies, however, still face challenges in the implementation of the advanced engineering methods that will be required to develop next-generation vehicles. In part 2, we will discuss how an integrated and digitalized suite of E/E systems engineering software will be a crucial foundation for these companies to pursue today as they prepare for the vehicles of tomorrow.
Read more in our white paper: Solving the E/E dilemma of electric and autonomous vehicles
Comments