Slash automotive engineering and testing time with virtual prototypes and smart simulation
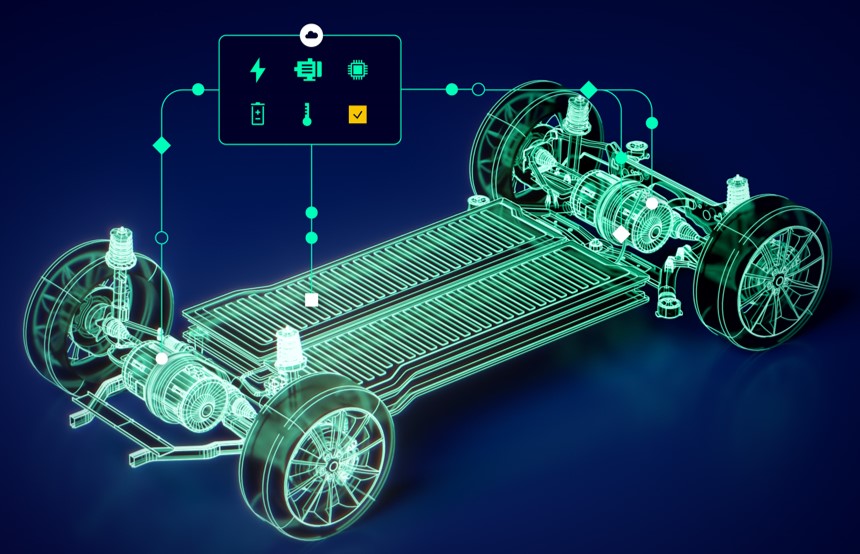
The automotive market is evolving rapidly, driven by the shift to electric vehicles, consumer demands for innovative features, and sustainability. The resulting emphasis on software-centric design, while offering flexibility and scalability, poses new challenges for automakers. Software development requires iterative updates, rigorous testing, and complex integration with hardware components.
However, the traditional approach to development relies on prototype testing late in the process to verify and validate designs, including hardware and software operations. By that point, if changes are required, it often means delaying the release of the design.
Watch the video to learn how boundless virtual verification and validation can help you accelerate automotive product development.
As the industry shifts to electric vehicles, the number of delays has increased significantly
Verification and validation become much harder, taking up to 50% of overall development time. Any shortcuts are risky because any oversight or failure to validate designs fully can result in costly recalls, damage to brand reputation, and, most importantly, compromised safety.
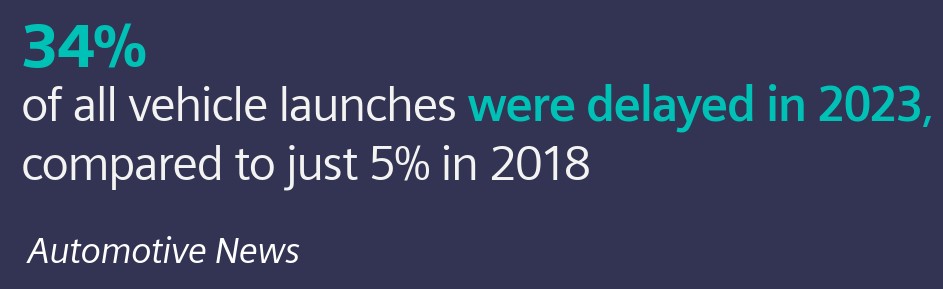
When you cannot fully verify and validate your designs until later in the development cycle, you make too many unsubstantiated decisions. If these assumptions prove to be incorrect, your timing and quality are put at risk.
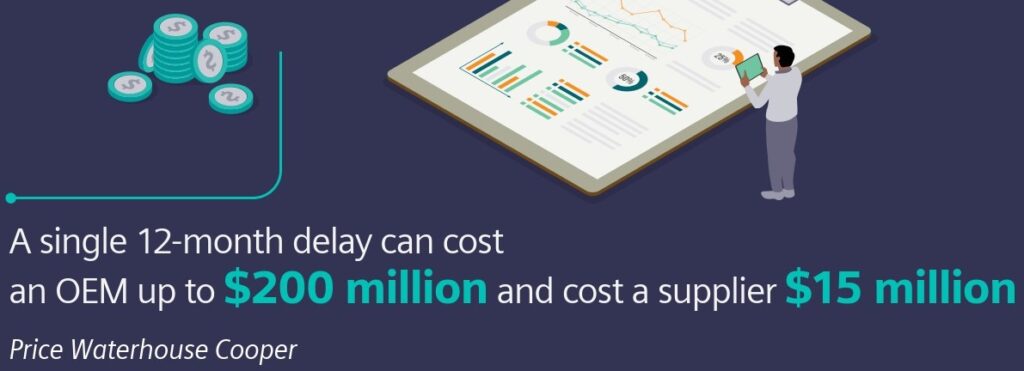
Virtual prototypes allow engineers to design, iterate, and test components and systems earlier in the vehicle lifecycle process. This speeds up the development cycle by allowing quick modifications and iterations based on simulation results. By identifying issues early, you can avoid time-consuming and costly post-production modifications.
Efficient engineering processes will help reduce product delays
Over the last few years, virtual prototyping and simulation tools have grown in range and capability to predict product performance more reliably. When you augment these processes with artificial intelligence (AI) and machine learning (ML), the scope of what you can test and resolve in the digital world is all-encompassing, limited only by your imagination.
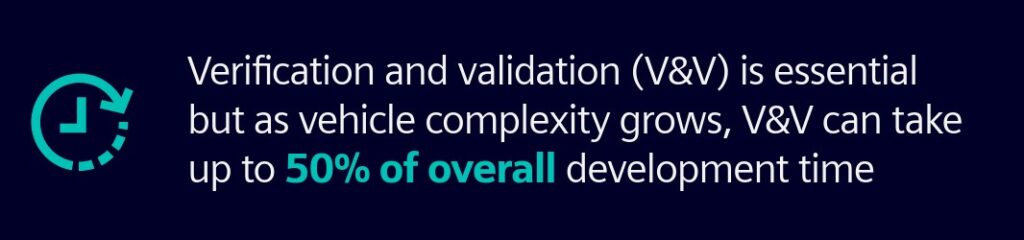
In today’s ultra-competitive automotive environment, assessing the effectiveness of your current verification and validation processes is critical. By adopting design and simulation tools or making better use of current ones, automakers can significantly improve product development processes and speed, reduce errors, and facilitate change management.
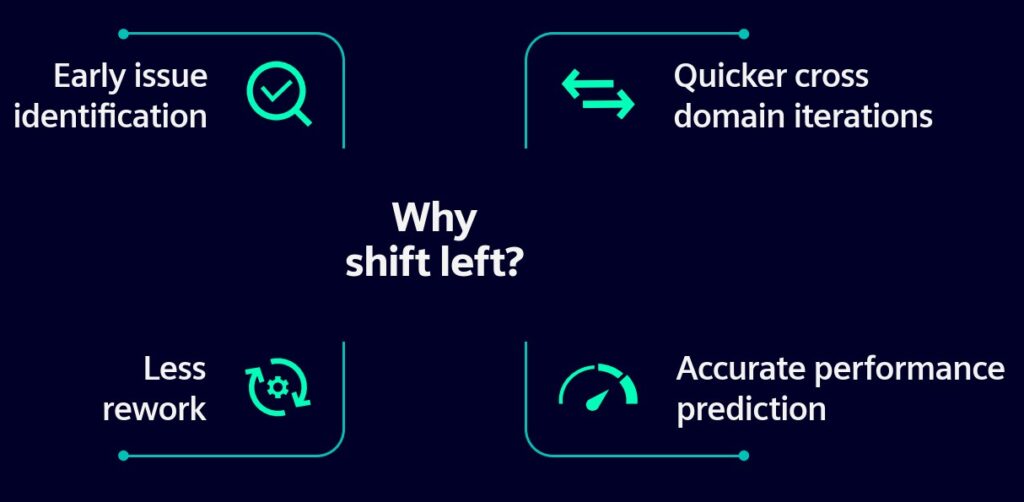
How can you solve real-world automotive engineering problems faster?
With Siemens Accelerated Product Development, you can solve real-world problems faster in a digital environment with—
- Smart simulation and testing
- Systems and vehicle integration
- Regulatory compliance and certification
Advance the future of mobility with Siemens Accelerated Product Development.