First post in the series: Coronavirus impacts on the Electronics Industry
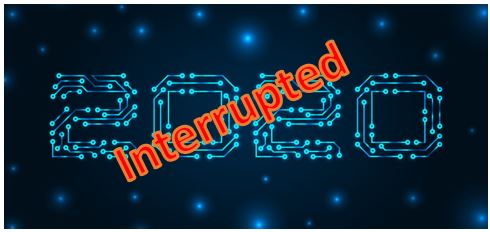
We interrupt this regularly scheduled program…
Just over two months ago, we were reading forecasts of 4% to 7% compound annual growth rate (CAGR) in Electronics design and manufacturing markets. We anticipated increased optimism due to the acceleration of the electric vehicle markets and modernization and digitalization of infrastructure, homes, and factories. In a McKinsey and Company research on the Automotive software and electronics markets, they forecasted “Autonomous driving (AD), connected vehicles, electrification of the powertrain, and shared mobility (ACES) …will expect 7 CAGR in the automotive software (SW) and electrical and electronic components (E/E) market” alone. 1 In early 2020, organizations were coming to grips with the new paradigm of trade discussions and tariffs, working through adjusted volumes and price-adjusted inventories, finding alternative suppliers, and implementing various other risk mitigating and efficiency optimization programs.
… Enter the COVID-19 pandemic to interrupt. This was not the start of 2020 that anyone expected! All existing plans, projects, and programs, now interrupted. A survey the ECIA conducted on Feb. 7 found a majority of component manufacturers (OCMs) didn’t know how the virus would impact their ability to supply customers. By Feb. 21, respondents said the impact would be “minimal to medium.” The reality, due to the closures in China, and the halting at major markets in Europe, will be much worse.
It is at these times when digitalization and the digital twin may have the most significant impact. Software and hardware vendors thought leaders, and technologists have been harping on digitalization and smart manufacturing for years. Digitalization of the manufacturing process through the digital twin of process, such that manufacturing planning can be simulated, optimized, and sent to production only after validation should be possible from any location. Ideally, the manufacturing planning solution would be robust with on-premise and cloud-enabled tools. In addition, process simulation solutions would allow manufacturers to access simulation models and studies from anywhere. Similarly, electronics manufacturing planning focused tools should be able to model and simulate the planning and programming process of electronics assembly manufacturing, from anywhere.
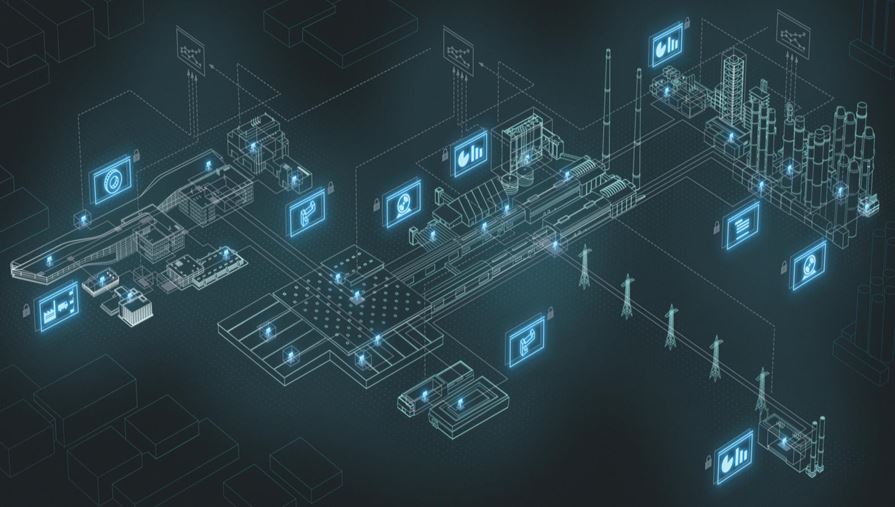
The digitalization of production, through the digital twin of production systems, allows assets in a facility to be managed, modeled, simulated, and monitored. To the greatest extend, smart decisions can be made when tools and insights that provide access to plant real-time or near real-time visibility, asset information, performance information, and issue tracking should be readily available from anywhere. There are obviously tasks, operations, and processes that must be done at the facility, with people. However, the good news is, based on an LNSResearch survey, 65% of best-in-class companies are at the pilot stage or beyond in their digitalization journey. 2
Having said the above, the majority of electronics manufacturers and suppliers expect business operations to be “back to normal” by July, according to a new IPC survey. Collectively, 75% of all respondents expect business to be back to normal by October.3 Light at the end of the tunnel. I hope 12 months from now the disruption to business, the markets, society, and we, as individuals, are not forgotten, or simply passed into history books without lessons learned. I am optimistic this will pass. Let’s use this to improve and ensure we prepare for future “Interruptions.”
Stay safe out there.