What can electronics manufacturers do about the labor crisis?
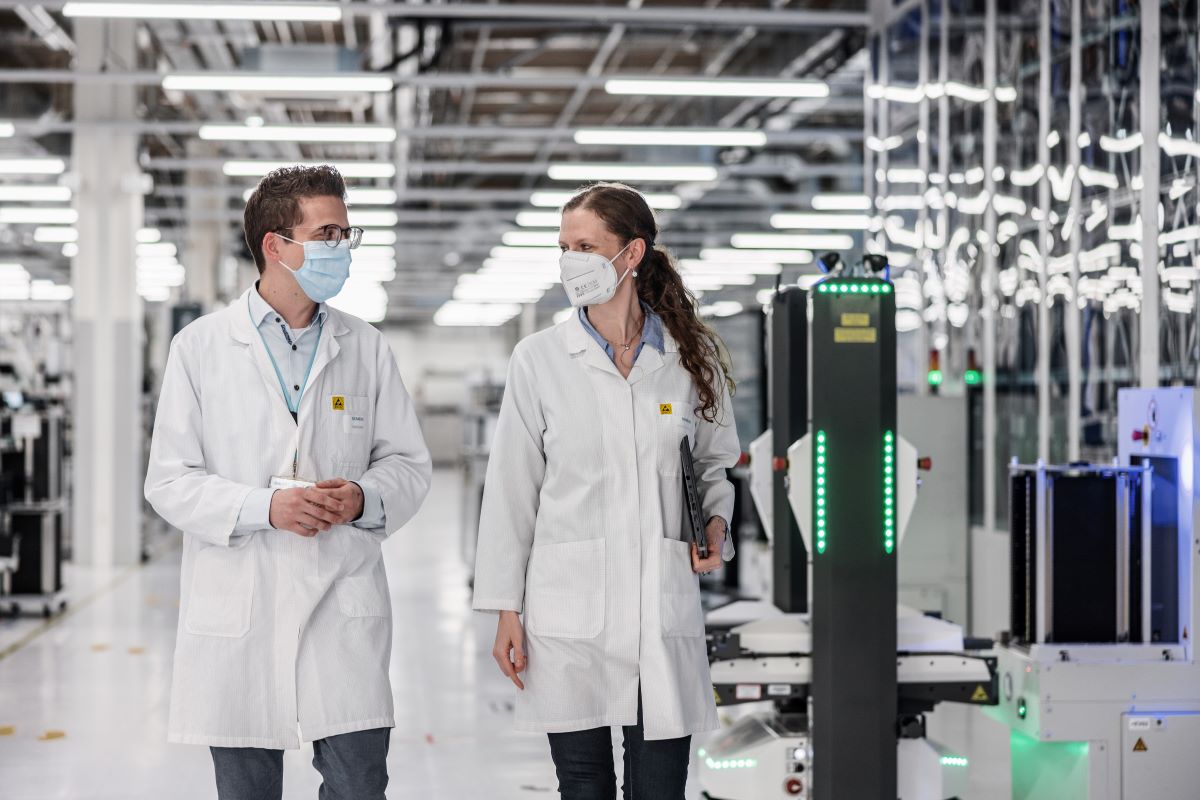
Watch the webinar on-demand to learn how digitalization can help.
There is an estimated shortage of 85 million workers worldwide across industries and regions today, a crisis driven by multiple factors. First and foremost, the global population is aging. Birth rates in 75 countries are below the replacement rate, and most projections estimate that by 2050, China’s working population will drop by 20% and Japan’s by 40%. That means that there are and will continue to be fewer people of working age to fill open positions.
The pandemic also played a part. In addition to the millions who lost their lives and those suffering from “long Covid”, the pandemic caused many workers to rethink their work-life balance. Workers are prioritizing positions with more flexibility both with regards to hours and hybrid/remote work and are more willing to leave a job that doesn’t offer those things. Last but not least, there is a huge gap in technology skills, primarily with regards to digitalization, programming, critical thinking and change management, which means that available workers cannot always fill the requirements of open roles. For SMBs especially, hiring qualified workers has become a major challenge.
Digitalization and MOM address labor challenges
Although the challenges are not industry-specific, in today’s candidate-driven market, manufacturing faces a distinct disadvantage in terms of conditions, compensation, and image when compared to other white-collar jobs. However, an integrated Manufacturing Operation Management (MOM) system can help electronics manufacturers address labor-related challenges, improve productivity and increase manufacturing output and quality. In addition, digitalization can improve electronics manufacturers’ positioning and help them attract qualified applicants.
For example, digitalizing manufacturing processes enables the automation of many repetitive and time-consuming tasks such as data entry and monitoring, machine operation, and quality control, reducing the workload on operators, allowing them to support multiple machines and focus on complex and value-added tasks. MOMs also include interactive guidance that supports first-time-right performance and reduces the learning curve for operators.
Operators aren’t the only ones who benefit from digitalization and MOM implementation—they also reduce the burden on process planners. Digitalization makes it possible to manage programming of all lines and machines in a single platform, supports numerous CAD/BoM formats and can accelerate BOP and recipe generation.
Digitalization can also help electronics manufacturers attract qualified employees. It eliminates a significant amount of the monotonous work that makes the field less desirable and gives workers the flexibility to rotate through guided and automated operations. In addition, it enables the flexible work arrangements that skilled candidates are looking for, such as allowing operators to monitor production processes remotely. Digitized factories are also more productive and profitable, which means they can offer employees job security and advancement opportunities.
Learn more in our webinar on-demand, in which Siemens experts Oren Manor and Markus Sauter will explore how you can address the labor crisis using digitalization.