5 insights from leading high-mix electronics manufacturers
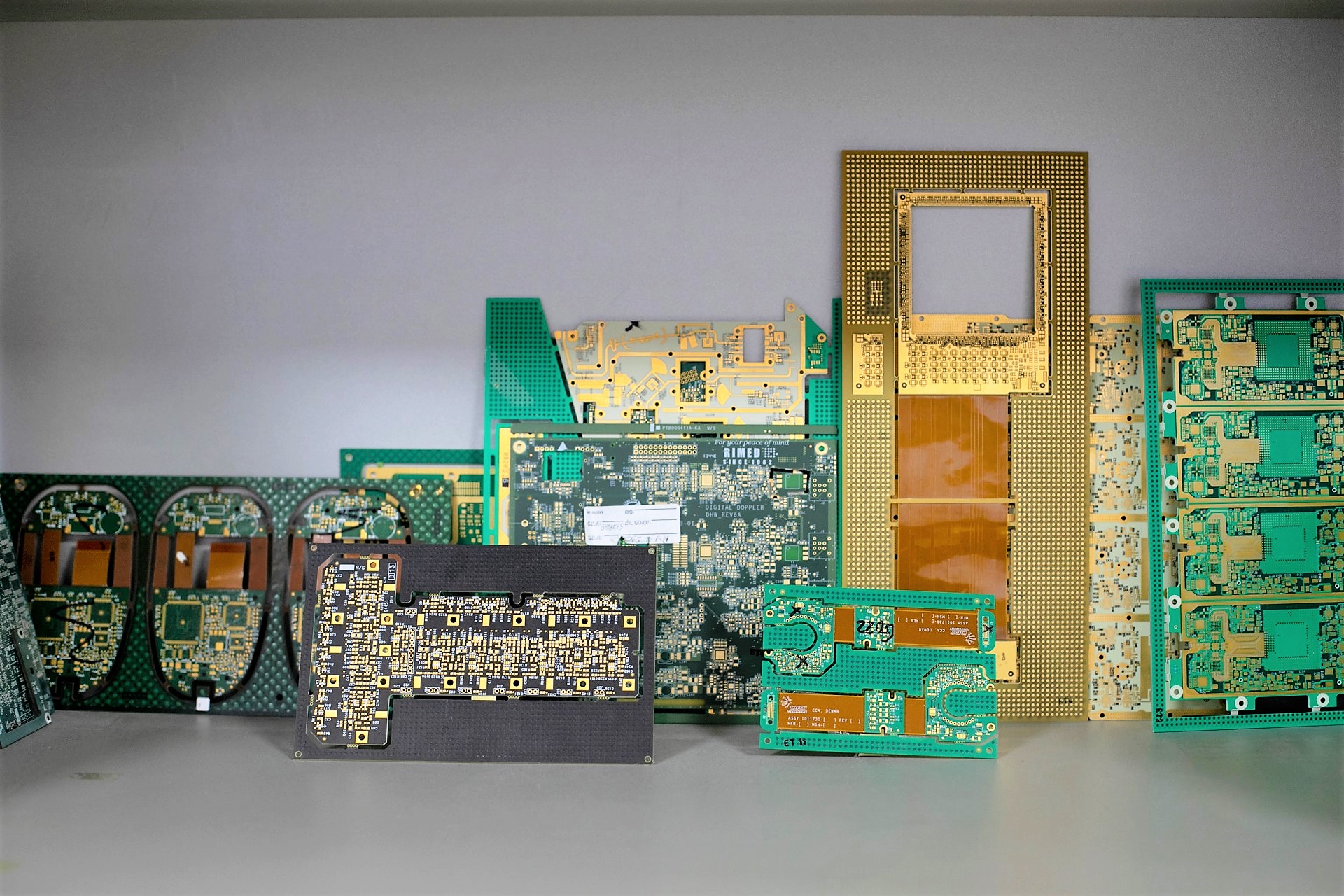
What are the keys to improved productivity, quality and agility in today’s highly dynamic electronics manufacturing market?
The answer is likely to be different for every manufacturer depending on the specific company situation, customer mix, where the company is in its digitalization journey, and other factors. However, there are major themes relevant to many manufacturers.
Below are five key things we’ve learned from leading high-mix electronics manufacturers around the world. Their experiences provide real-world insights into what others can expect and can also help manufacturers look beyond solving current problems towards a long-term, future-facing strategy that enables additional improvements.
Insight #1: Standardize engineering tools and NPI processes throughout the enterprise, across production lines and sites
Connect Group NV provides printed circuit board (PCB) assembly and cable assembly services, focusing on the automotive, railway, healthcare, infrastructure, defense and avionics industries. After acquiring several other manufacturers with plants in multiple locations, the company embarked on a program to unify the engineering, manufacturing and new product introduction (NPI) processes of all sites and relevant departments. With Valor™ Process Preparation with Valor Parts Library already in use at some Connect Group factories, Connect Group NV decided to implement them at all locations and access additional engineering functions.
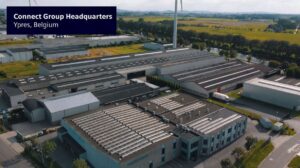
The benefits of standardization for Connect Group NV included:
- Production portability and reduced offline work. Shared processes have made it much easier to reallocate projects. A project can be moved from one manufacturing site to another in minutes instead of hours. The comprehensive digital twin approach has also eliminated manual processes, saving time and reducing errors.
- Workforce mobility. With a unified training process, the company has achieved a smooth and consistent onboarding of new staff across all sites. It is now simple to reassign employees to new projects and support their desires to move to new locations, as the same processes are in place everywhere.
- Best practices can be integrated across all factories. This has improved quality and efficiency company-wide.
Learn more about standardizing engineering tools:
Insight #2: Real-time production visibility is vital for small to medium manufacturers working with high-mix production
ICCO EMT is an electronics manufacturer in Romania that provides manufacturing services for the automotive, medical and consumer electronics industries, among others. It runs 55 new product introductions (NPIs) and 3.5 million finished goods a year including surface mount technology (SMT) lines which are connected to Internet of Things (IoT) boxes. The company has launched automated control systems like Valor Process Prep and Opcenter Intelligence Electronics to reduce errors, provide real-time notifications when problems arise, and deliver special consumption reports that some of its customers require.
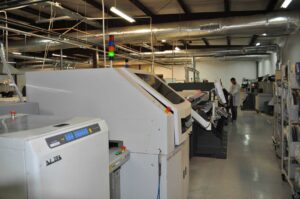
The benefits of real-time visibility for ICCO EMT included:
- IoT integration on the shop floor. Using automated processes for data mining, analytics and insights the company has gained powerful analytics and reporting capabilities.
- Maximized efficiency and quality. The entire engineering process is now done digitally and there is no need to check orientation and positioning, saving two to three hours per NPI depending on the complexity of the board. The reporting function helps ICCO EMT discover trends and proactively perform maintenance when required, for example, tracking machine uptime/downtime, percentage of defects and more to improve efficiency.
- Improved traceability and quality reports for the customer. Board-specific data compilation and reporting makes it simple for ICCO EMT to track and identify boards and track quality metrics including pick issues and scrap rate reports for their customers.
Learn more about ICCO EMT’s accelerated processes:
Insight #3: Automate the full material flow
ROJ Srl (ROJ) is an industry 4.0 pioneer and a leading electronics designer and producer for automotive, telecom, and industrial verticals based in Italy. To prevent bottlenecks due to missing materials, ROJ often ended up purchasing too many components, and the material frequently expired before it could be used. ROJ was looking to gain full visibility into materials on the shop floor with a cost-effective mechanism for planning and controlling the flow of materials throughout the factory.
ROJ had invested in advanced storage solutions, including smart shelving and automated guided vehicles (AGVs) that could bring the materials to where they were needed on the shop floor. To fully benefit from these investments, ROJ implemented Opcenter Intra Plant Logistics and Opcenter Execution Electronics with a customized solution that could aggregate data from manufacturing lines, kitting stations and the warehouse, and generate a prescriptive model of material flow.
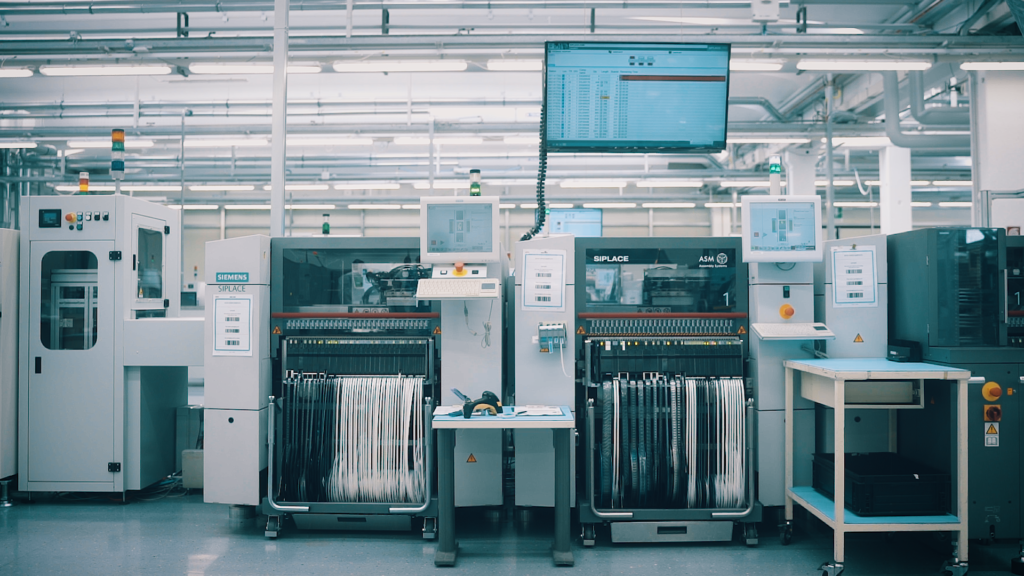
The benefits of automating the material flow for ROJ included:
- Preventing material starvation. Opcenter Intra Plant Logistics gives ROJ visibility and enables smooth and continuous just-in-time (JIT)/Kanban material delivery between warehouse and production, optimizing changeover time while eliminating material starvation.
- Ensuring correct material is used and preventing defects. By looking at data coming from the machines in real-time, ROJ can predict exactly when materials will need to be replenished and coordinate delivery of stock from the warehouse just in time rather than let it sit outside where it can be damaged by moisture.
- Prevent material obsolescence. With just-in-time material delivery, ROJ no longer needs to over-order and run the risk of materials expiring before they can be used. They can also easily dispatch reels of material based on their age.
- Reduce inventory. With better inventory accuracy and full material traceability, ROJ can accurately plan future work orders and avoid unnecessary changeovers.
Learn more about material flow automation:
Insight #4: Include manual manufacturing processes in the digitalization efforts
BMK, based in Germany, is a leading global provider of electronic engineering and manufacturing services for the entire lifecycle of assemblies. Its portfolio includes the development, manufacturing, and end-of-life management of electronic assemblies and finished units for customers in the industrial, energy, vehicle, telecom, and medical sectors. Given the industry trend toward high-mix, low-volume production, BMK faced the challenge of fulfilling more frequent NPIs and engineering change orders (ECOs) while increasing efficiency and maintaining profitability levels. To accomplish this, the company expanded its digitization efforts to include what were previously manual manufacturing processes.
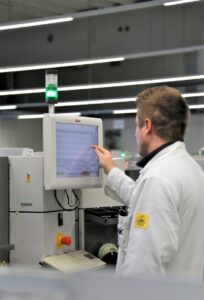
The benefits of automating manual processes for BMK included:
- BOM quoting became an automated process instead of a manual one. Rather than loading, preparing, scrubbing, formatting, checking, and comparing BOM data, the process is now automated. BMK can create more accurate quotes faster and can use the powerful database backend to track and reuse its work for future projects.
- Stencil data can be generated faster. With Valor Process Preparation data is generated automatically and quickly, and a footprint only needs to be checked once. The same footprint can be for all instances of the component, including new projects, saving significant time.
- NPIs take less time. The company gained the capacity to run high-complexity NPIs and grow its capacity without adding staff.
- The entire SMT process is faster. It was accelerated by 10%!
Learn more about BMK’s digitalization process:
Insight #5: Improved quality means less scrap and waste – and reduced costs
Egicon, based in Italy, is an emerging European electronics design and production house that provides high-quality manufacturing services for industrial sectors including automotive, agriculture, biomedical and aerospace. The need to provide customers with warranty support and traceability data started the company on a digitalization journey that eventually led to the full automation of its manufacturing processes and enhanced quality monitoring.
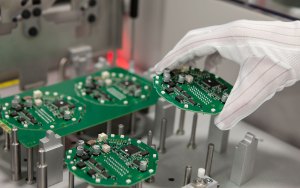
The benefits of real-time quality monitoring for Egicon included:
- Quality events are identified in real-time. With continuous monitoring of overall equipment effectiveness, Egicon has been able to significantly reduce waste-related costs.
- Better quality control. Egigon has reduced its repair rate from 30 ppm to six, and achieved a scrap rate of zero percent.
- Attract new business. The improved quality has increased customer confidence in the company and helped it attract new business.
Learn more about quality monitoring:
Summary
Current market trends are accelerating the shift towards high-mix, low-volume manufacturing. Planning ahead and implementing manufacturing best practices can no longer be delayed, and so referring to best-in-class manufacturers is an important way to learn and decide what future-facing strategies can be developed and implemented in your factory.
Talk to us about the best strategy for your company.