Are your alternative parts well validated before release
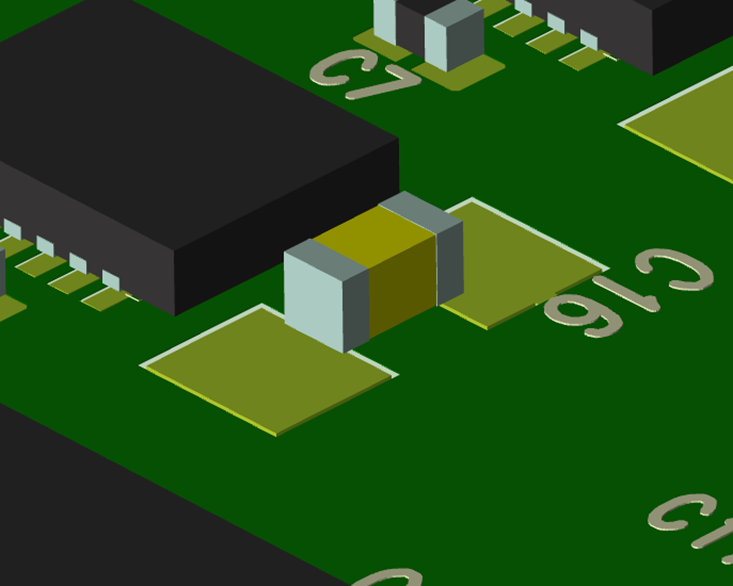
Traditional ways to validate alternative parts
The traditional way to evaluate alternative part is by reviewing the alternative part manually with the physical component, or within the component’s datasheet.
The first step is to make sure the size of the alternate part is acceptable. The maximum tolerance in the datasheet is used to calculate the maximum component size to evaluate the final size of the alternative part is within the size limit.
The next step is reviewing the pin, the pin pitch of the alternative part should be matched well with the original part, the pin size of the alternative part should also be within the allowed tolerance.
For the pin location review, it would be complex. Typically, designers are using a spreadsheet to calculate the internal gap and external gap of the pin, then compare it to the internal and external gap of the corresponding toeprint, a formular based on IPC standard is used to ensure the pin location of the alternative part is well fit with the toeprint.
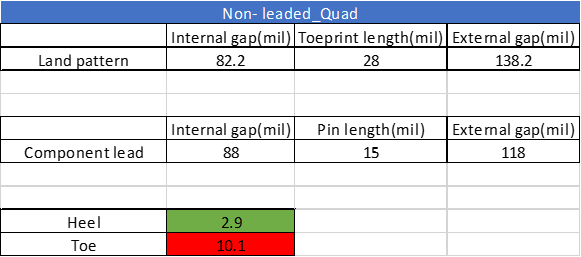
With the above steps, a new alternative part can be simply validated, but in some cases, it is more complicated. When the alternative parts’ pin distribution is asymmetrical, the simple method of using a spreadsheet is not applicable for the evaluation, an optimized approach is needed to verify the fit. Designers will prepare a 2D component drawing with CAD tool, and virtually placed in on the ECAD footprint, to verify the compatibility of the alternative part.
These methods help to make sure the alternative parts are properly validated for decades, but the processes are obviously manual, any manual process would be time-consuming and error-prone. But before implementing a dedicated automation tool, these steps are very important in the alternative part selection process, to ensure the alternative parts fit well on its toeprint.
Automated validation process to alternative parts
With billions of online 3D component library models integrated, Siemens EDA provides an automated method to conduct the alternative parts validation. With the automated process, users can even validate their alternative parts in their layout environment. The 3D component libraries contain accurate component body geometries and lead geometries, these component models can be automatically assembled on its footprint, and validate the component-to-toeprint compatibility within a manner of few minutes based on IPC standard.
With this new automated process, alternative parts can be validated in a high efficiency way, which eliminates the potential assembly risks before it is released and added into company’s AMLs.