Manufacturing supply chain resilience
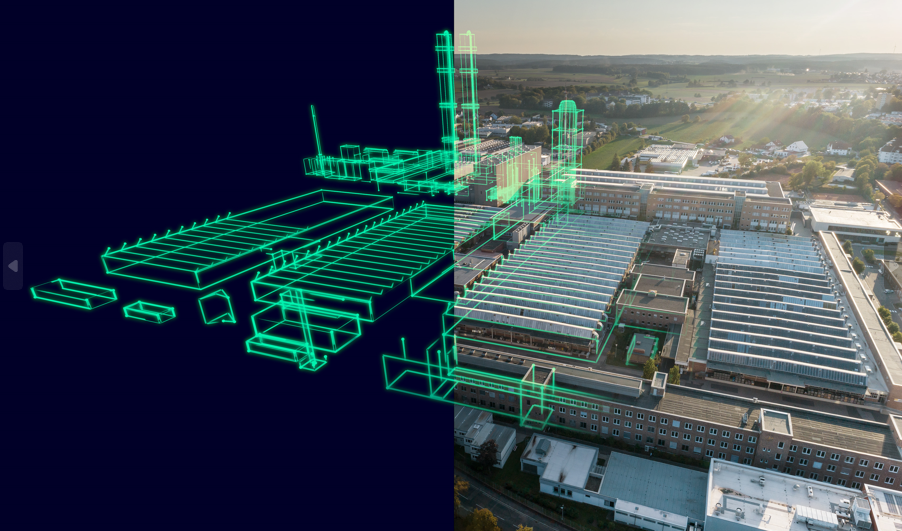
Every company in every industry has been adversely affected by supply chain challenges over the past several years. Ensuring supply chain resilience throughout our industry and within your product lines has never been more important or easier to secure. We’ve experienced disruptions before for various reasons, be they earthquakes, floods or fires at factories. But recent years have also added pandemic and geo-political causes for disruptions.
The electronics industry is no exception. We have seen the scarcity of electronic components impact the delivery of everything from automobiles to servers. Companies have had to become resourceful in finding replacement components and many software solutions have evolved to assist with the commercial aspects of the component supply chain disruptions.
Industry disruptions in a manufacturing supply chain
Often overlooked, but equally important is the manufacturing challenges brought on by supply chain disruptions. When it becomes necessary to move electronics sourcing out of a region or facility, the bare printed circuit board as well as the assembled printed circuit board are also impacted. Even the new alternate parts proposed as replacements can have a substantial impact on the manufacturing of the PCB.
Printed circuit boards are each a custom, high-precision product and while your boards can likely be built by multiple suppliers, the suppliers’ processes, materials and equipment will vary widely. Under normal circumstances your sourcing team regularly works to qualify new suppliers both on the fabrication and assembly side. But when supply chain disruptions catch you off-guard, how can you quickly qualify a new supplier’s manufacturing fit for your products?
You will want to first address the materials used in the PCB stackup. Each fabricator will maintain an inventory of the laminates and prepregs they have qualified and are most comfortable using. Another fabricator may use completely different materials to achieve similar electrical performance. Or they may need to special order material to accommodate your impedance and loss specifications, especially for higher speed designs. A mismatch here and you will have to respin your design to accommodate new clearances for differential pairs, as an example. A good stackup planning tool will allow you to easily compare the projected electrical performance of a fabricator’s proposed stackup to your spec stackup.
Ensuring supply chain resilience in fabrication
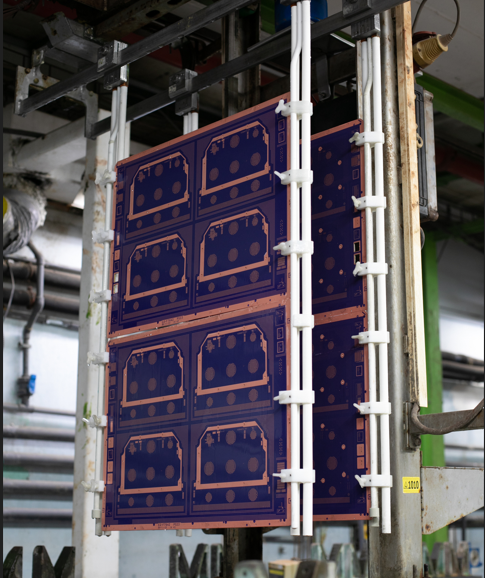
The bare PCB, and even packaging substrates for that matter, are fabricated using a variety of chemicals, processes and equipment. Do your designs include sequential lamination? If so, how many stacked vias does the fabricator allow? The answer will vary between fabricators. And what about backdrill to trace spacing? Some fabricators will be able to accommodate closer proximity than others. The variations in fabrication capabilities are numerous, but with the proper Design for Manufacturing (DFM) solution, you can easily assess a prospective new supplier’s ability to easily manufacture your boards or substrates, ensuring your overall supply chain resilience.
Component supply chain resilience
Finally, the assembly of the PCB must be considered when changes are made to the Approved Vendor List (AVL). A component can be parametrically qualified as an alternate part and be in the same package form but still not be an appropriate fit. With the miniaturization of designs and components, even the slightest differences in component body dimensions can have an impact on the manufacturability of your PCB.
The differences in component height or standofff are frequently overlooked. Additionally, the lead form may have a different dimension for the pin contact area, causing either a weak solder joint or a possible short through bridging.

And if you need to move the assembly of your PCBs to another contract manufacturer, or even to a different site for the same manufacturer, you will want to know if that move will cause you to change any aspect of your design. One of the greatest differences between contract manufacturers is with the application of solderpaste. The solderpaste they use and how they apply it as well as the stencil shapes and sizes they feel work best for various package types, constitute their “secret sauce” for how to assembly PCBs.
As I suspect you have caught on by now, a capable DFM tool will enable you to identify the manufacturing impact changing your component AVL and your contract manufacturer will have on your products.
Our Industry’s Challenges
The challenges we face will never stop coming. One could even argue if the past few years are any indication of what’s to come, the challenges will only accelerate. You won’t be able to evaluate the impact of manufacturing supply chain changes in the same way you have in the past. There’s too much at stake. A systematic DFM and stackup approach is required for supply chain resilience.