The Advantages of Smart Manufacturing
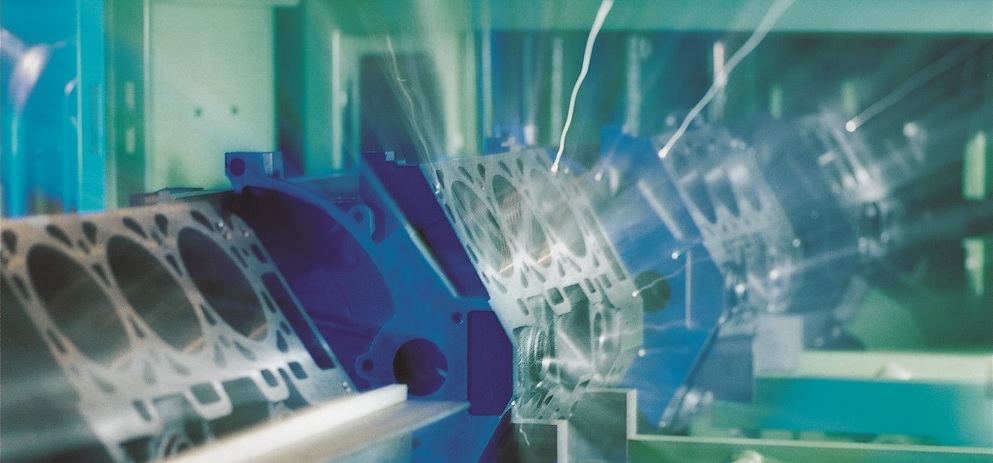
Summary
With technological advancements all around us in the manufacturing industry, it’s important to understand how improving machinery operations is dependant upon making your factory smarter.
Today, in our fourth and final podcast of these series, Bill Davis — the Director of Industrial Machinery and Heavy Equipment Solutions at Siemens — and I, we’re discussing the smart manufacturing techniques to use to improve machine assembly, shop layouts, and process simulation.
So, listen to the Final Episode of Siemens PLM Podcast series, to learn how to be more efficient in terms of generating more cash and reducing the quality problems overall, with the help of the digital twin.
In this episode, you will learn:
- How to make sure you get the right parts to the right spot on the assembly floor at the right time. (01:53)
- Why process simulation is important for continuous improvement. (02:55)
- Why scheduling machines and multiple product lines at the same time is as important as the individual assembly process. (05:12)
- What you can do to bring a machine into the commissionable state as quickly as possible so that you don’t have idle time for your cash. (06:30)
- Examples of use cases where companies have implemented the simulation and seen a reduction in errors and time, while an increase in cash flow. (09:49)
- What closed-loop quality is and how does it work. (14:29)
How do you make your factory smarter? With ubiquitous technological advancements, a company needs to stay in step with understanding how to improve machinery operations, which is dependent on a smart factory.
This process includes simulation – a crucial element to the smart manufacturing space, process and machine.
This fourth podcast in a series on Smart Manufacturing by Siemens Digital Industries Software, solutions for the industrial machinery industry by Siemens Digital Industries Software, is stressing the importance of innovative manufacturing techniques for smart factory operations.
Insightful input from our resident expert in this podcast series is Bill Davis, Director of Industrial Machinery and Heavy Equipment Solutions at Siemens, whose engineering expertise spans over 30-years with 20 years as an engineer.
Smart manufacturing – where to begin
Smart manufacturing requires a smart assembly layout – getting the right parts and machines in the correct place on the assembly floor at the right time. A software solution requires simulating the positioning of the machines on the floor, eliminating high-traffic areas, removing bottle-necks due to slowness in receiving materials and optimizing work cell locations for optimum utilization.
Having everything in a relative arm’s reach improves efficiency; however, the factory also requires process simulation. Order and functionality are the standards for overall conflict resolutions to foster adaptability, predictability and extendibility. This means finding the necessary tools, human or machine, to perform a quality job.
The shop floor and simulation
So, it’s not merely a focus on the shop layout capabilities, but also a need for process simulation at the human level to factor in any problematic issues, which usually don’t surface until complications occur in the field. Simulation of these issues is highly valuable for continual improvement of the design and development process. Also, it includes machine assembly and scheduling of machines on the product lines.
Ultimately, less time is spent in commissioning and debugging obvious known issues from the PLC code generation, thus getting the machine to the customer more rapidly via simulation of parts and kinematics. Moreover, this simulation gives back time in physical stress analysis and fatigue.
This result means a company generates more revenue, reducing the margin of erosion from errors and quality issues. However, none of these benefits could occur without the digital twin. Siemens has many examples of companies implementing the digitalization of machining or manufacturing centers, reaping more money, thus justifying any extra cost in this investment, resulting in faster machines via digital twin for software development and validation.
To learn to make your factory smarter and bringing quality to your parts and overall process, listen to this engaging podcast on Apple Podcasts, Stitcher, Spotify, Castbox, TuneIn, Google and RSS Feed.
Listen to podcast1, podcast02 and podcast03.
About the author:
Bill Davis is the acting Industrial Machinery and Heavy Equipment Industry leader for Siemens Digital Industries Software. His experience and insights have been acquired from a career spanning 30 years in engineering and operations management with machinery and heavy equipment companies. Bill holds a master’s degree in Business Administration from Marquette University, with a concentration in Operations Management and Strategic Marketing, as well as a Bachelor of Science degree in Mechanical Engineering from Milwaukee School of Engineering.
This concludes the fourth blog and podcast in a series on Smart Manufacturing and the trends affecting the industry. Our future blogs will spotlight excerpts from the transcript of these podcasts, providing technology solutions for where today meets tomorrow.
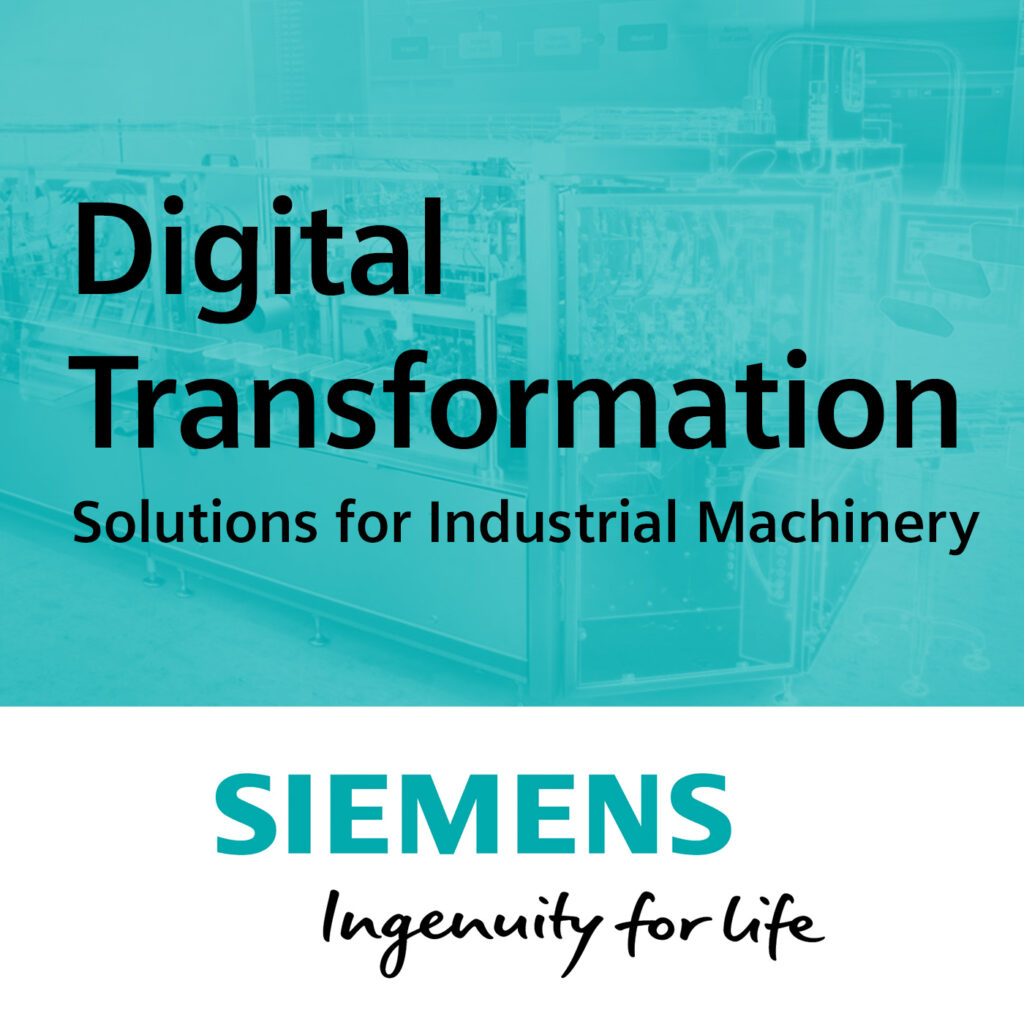
Digital Transformation Podcast
The Digital Transformation: Solutions for Industrial Machinery Podcast by Siemens Digital Industries explores the advantages of smart manufacturing, a digitalized product development strategy and the solutions it offers for the Industrial Machinery industry.
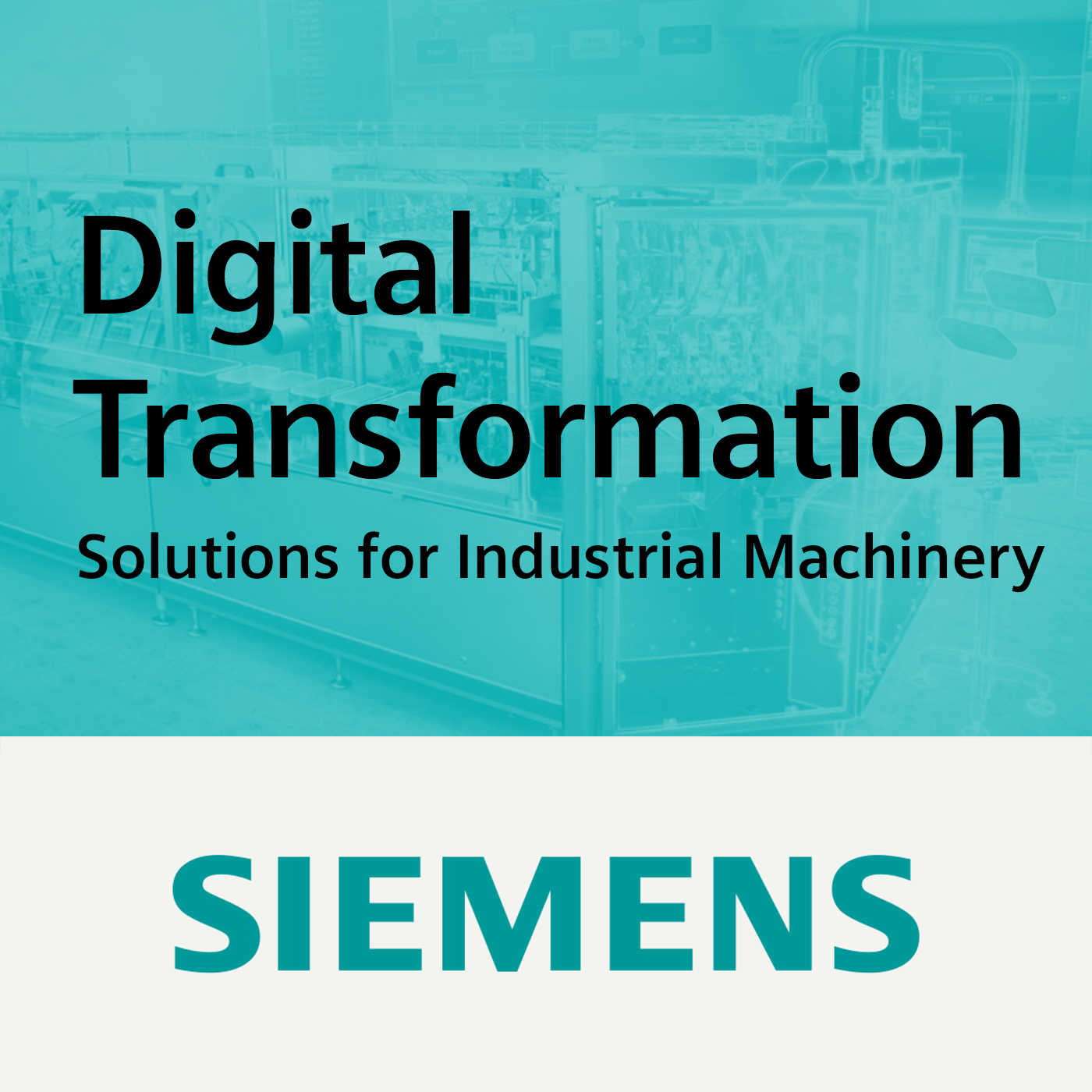
Digital Transformation Podcast
The Digital Transformation: Solutions for Industrial Machinery Podcast by Siemens Digital Industries explores the advantages of smart manufacturing, a digitalized product development strategy and the solutions it offers for the Industrial Machinery industry.