Automating 3D printing design
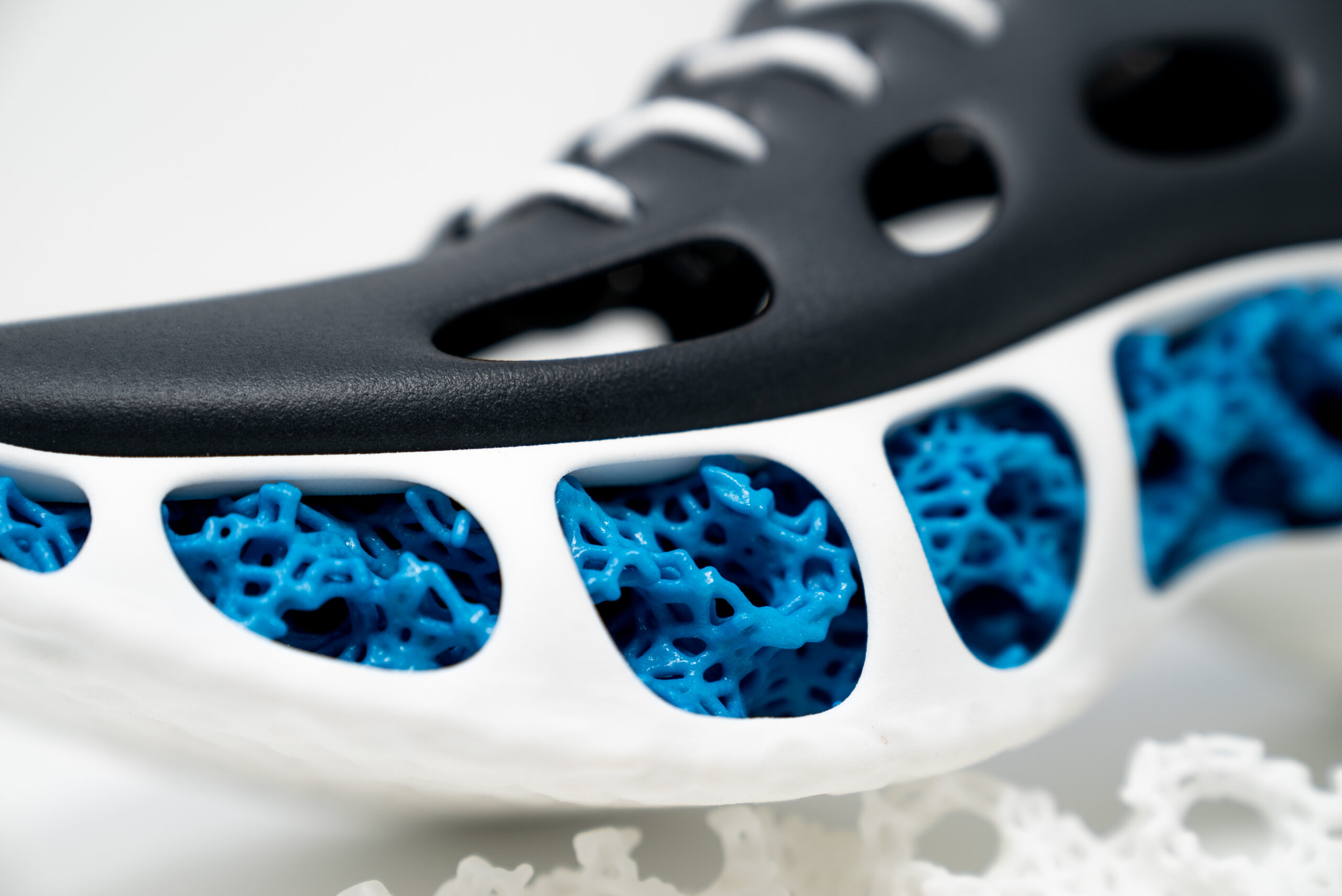
Additive manufacturing (AM) is an evolving technique for industrial production, but with that growth comes complexity in the development process. Using the right tools eliminates much of the hurdle to a successful AM program, but automating some of these processes provides a faster time to market while creating a larger design space at in the concept design phase of development. There are many ways to automate and optimize the design process depending on the application, but here are a handful from the series Advancing Additive by Aaron Frankel.
Multi-objective optimization
For many, structural optimization is finding the best performing alternative to a pre-designed component, the mounting locations and critical geometry are labeled, and software starts cutting away unnecessary geometry. But with enough foresight, multi-objective optimization can be leveraged to expand the design space at the beginning of development. This earlier simulation process decouples development from the experience of designers and engineers to truly provide the best possible part for the product.
Algorithmic modeling
Part of AM’s appeal is the complex structures it can produce, but creating these geometries has often limited the possibilities because of the tedium in designing them. Algorithmic modeling drag-and-drop elements that can be reused and readjusted with ease. This replaces the need to code the geometric patterns and model them manually. These geometries can include lattice structures, meshing techniques and even surface based patterns for rigidity.
Durability simulation
There is some amount of variability in every additive manufactured component, with porosity and other localized microstructures. Mitigating the formation of these defects is not completely understood, but with the right software tools the durability of parts can be gleaned without destructive testing. A lightweight part is only better if it can withstand the operating environment it was designed for. And simulating this is accelerating with the addition of machine learning to pinpoint problem areas.
Implicit modeling
Topology optimization is great for finding an unknown solution, but what if the geometric definition is already known? Implicit modeling allows the use of equation-driven geometry, even for structures that would otherwise be impossible with traditional modeling techniques. It could be a know structure that requires no support structures while printing, or a geometry optimized for heat transfer of a fluid. Using a known function reduces the time and resources in simulation to find the result.
Organic lattices
Lattice structures are a critical optimization tool in the additive manufacturing toolbelt. They can provide increased performance by reducing the overall weight of a component by removing much of the solid material and they can even create specific deformation characteristics to better match organic structures. This could help designers create an ultra-lightweight shoe that exactly compensates for the gate of an athlete. Updates in how these are designed have expanded the usable number of lattices and how much they can be tweaked.
Siemens Digital Industries Software is driving transformation to enable a digital enterprise where engineering, manufacturing and electronics design meet tomorrow. Xcelerator, the comprehensive and integrated portfolio of software and services from Siemens Digital Industries Software, helps companies of all sizes create and leverage a comprehensive digital twin that provides organizations with new insights, opportunities and levels of automation to drive innovation.
For more information on Siemens Digital Industries Software products and services, visit siemens.com/software or follow us on LinkedIn, Twitter, Facebook and Instagram.
Siemens Digital Industries Software – Where today meets tomorrow