Future-proof with the IoT miniseries – ep. 5 Transcript
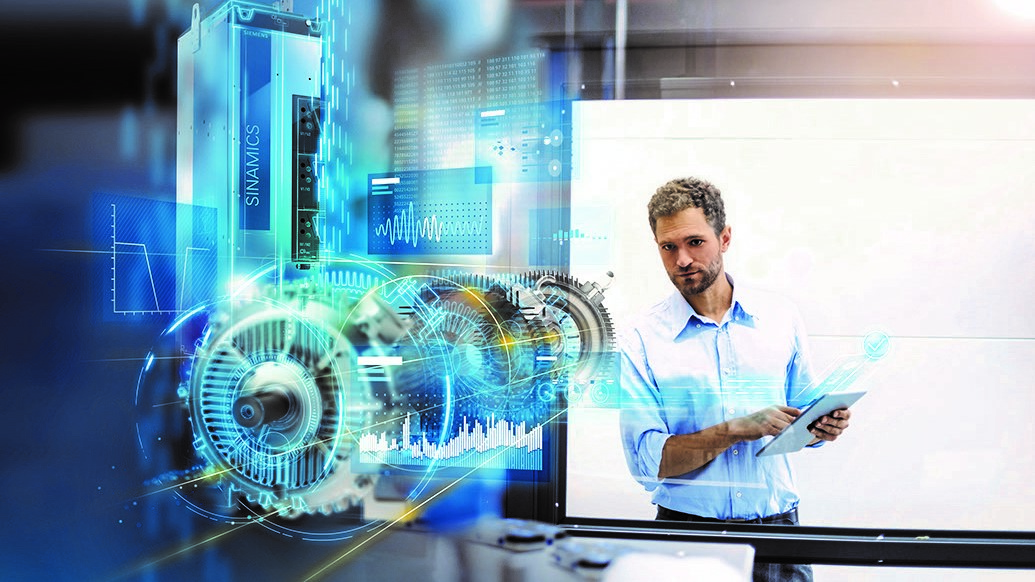
In the fifth and final episode of the Future-proof with the IoT miniseries, our experts tie together many of the topics and trends most relevant to the industrial machinery industry. Our guests from the Siemens electric motor factory in Bad Neustadt reflect on their experiences pivoting their entire factory’s operation with the insight and plans they had accumulated through their use of the IoT. And almost everyone agrees that the pandemic was a catalyst for rapid change to come in securing flexible supply chains and factory environments, to be able to handle the next disruptive event when it happens.
Read along with the podcast below and if you enjoyed the discussion please think about subscribing on your favorite podcast platform to stay up to date on all things digital in the world of industrial manufacturing from Siemens. Enjoy!
Jörg Ludwig: Hello! This is the final episode of “Future-proof with the IoT”, a podcast mini-series for the IM industry to learn how to leverage digitalization to overcome manufacturing disruptions and bounce back stronger. I’m your special host for this mini-series, Jörg Ludwig.
In our previous episodes we covered the challenges and trends in the Industrial Machinery industry as well as how IoT is helping processes in a normal state of affairs. If you’re new, we’d highly recommend those episodes. They are available on all your favorite podcast platforms and we’ll have links for you in the description.
But today, for our last episode, we’ll be talking about how sudden and fluctuating economic conditions, such as the COVID pandemic we are living in, can affect a manufacturer and how IoT can ease the associated costs and pain.
Welcome back Colm Gavin, Portfolio Development Manager at Siemens Digital Industries Software, Matthias Lutz, Head of PreSales and Solution Design at DI SW, and Heiko Dickas and Sebastian Oeder, leader of the digitalization team and head of the production unit main motors at the Siemens Bad Neustadt electric motor factory.
So, most everyone has heard a variation of the saying, “A stitch in time saves nine.” How can manufacturers use the industrial IoT to prepare for disruptions?
Colm Gavin: So, disruptions can be entirely unpredictable, like you said, leaving manufacturers and their supply chains at risk. So, resources may become sparse, teams may be unable to work, operations may not even be safe to resume. And so, one solution we have for that, especially around safe operations being able to resume in regard to the COVID-19 is something we have with our tools in the adherence for social distancing for the safe startup of lines. In this solution, we’re able to combine different technologies, such as real-time location services – so, devices that can be placed on assets or on people, so we can verify their location inside the facility. That data is then fed into our plant simulation tool via an IoT interface. We leverage MindSphere to take the data from the real-time location services, or RTLS solution, we feed that into plant simulation via an IoT interface. And then within Plant Sim, now we’re able to simulate the movements of people and tracking of assets. So, this allows companies to simulate the safe working distances for workers and verify where are there areas where there could be a high probability of risk where there was a lot of traffic, people working maybe too close together. And so, once they were able to simulate that, again, by leveraging IoT to bring in that real-time location tracking, then we can simulate it and react accordingly. Space out the workers, put separations in where needed.
Matthias Lutz: Yeah. Manufacturers need to ask several questions to become better prepared in case of disruptions like a pandemic. And I think we’ve all seen it in our personal lives. So, we are much better prepared than we have been one year ago. Those questions for manufacturers are for example, how do you safely ramp down operations if you cannot keep assets or processes up and running? For example, due to a disruption in the supply chain which we are currently experiencing in many industries. Or how do you increase efficiency to maintain profitability when you are not running at 100% capacity? Or in general, how do you maintain productivity if teams cannot physically go to the plant? Also, this happened in many cases, here in Germany and all over the world. What I have seen when talking to my customers during the pandemic by pursuing smart factory initiatives – in part by adopting IoT – manufacturers can embrace solutions that help answer these questions in a much more faster and efficient way. Manufacturers that have some level of digitalization underway, are better positioned to handle the ups and downs of a disruption. And therefore, I strongly think that the whole pandemic situation has somehow increased the level of adoption of IoT technologies, and more and more of our customers are really experiencing the benefits of their installed solutions.
Jörg Ludwig: Sebastian, let me ask you a challenging question. Did Bad Neustadt have a plan for such situations or did the COVID pandemic totally take you by surprise in that sense? So, how prepared was the factory?
Sebastian Oeder: So, with the factory Bad Neustadt, just as the biggest portion of mankind I think, have not foreseen the impact of COVID brought to our lives and the threats. But the emergency plans of the factory that define in general how to proceed in case of an emergency did work right away. It’s already clear who is a member of a crisis team, how to communicate, and so on. This team was formed right away and really did a great job. So, in general, I feel much safer in the factory than for example, in my home supermarket.
Jörg Ludwig: Okay. So, was having digitalized so many areas of the factory a good caution for what was to come?
Heiko Dickas: Yeah, for sure. For example, almost my complete team can work remotely and can support the shop floor in this way. But also, the group leads and production leads like Sebastian can control their lines by having so many things digitalized. Having specific dashboards created on the real needs, it’s possible also to stay at home from time to time and to minimize the risk of this pandemic.
Jörg Ludwig: So, over the pandemic, the IoT market has been developing in two directions. Existing customers like Bad Neustadt continue the pursuit of long-term projects, while quick wins are the focus of new projects. It seems like digitalization efforts for a short time have been often part of this current crisis management of many companies. We could say that the biggest drivers for the next generation of digital implementation have not been the CEOs, the CIOs, or the CDOs, but the Coronavirus? Do you agree that the COVID pandemic has acted as a catalyst for digital transformation in many companies?
Matthias Lutz: Definitely. So, when looking at my daily routine during the COVID, I have seen a, let’s say, digitalization wave which I haven’t seen during the last, let’s say eight years in our company. But when it comes to shop floor use cases or machine builders, I think there’s not a clear yes or no, it’s a yes and no. So, many of our customers were somehow struck by the economic downturn and they have shifted certain strategic initiatives to a point in time where they can breathe again and where they see the horizon at the end of the pandemic. But still, I think digitalization is a step-by-step journey, and customers who started this journey before, or taking maybe smaller steps right now are definitely in a better position after the pandemic. And quick wins in digitalization are difficult to implement in the industrial environment because IoT projects often spend a period of many years as we see at Bad Neustadt. The reason for this is simple, a smart factory doesn’t grow on a Greenfield but almost always develops out of the brownfield. This mix of old machines with propriety legacy interfaces and modern systems that can already be connected via, for example, MQTT or OPC UA can always be seen in the long term, that pandemic will not change that. So, my call to action is, “Start now, refocus as well on your digital initiatives and you will be much better prepared for the time after the pandemic or for every other hardship that will come during the next years.”
Jörg Ludwig: Thank you for your perception, Matthias. So, once a manufacturer decides to start with digitalization, what are the areas where the IIoT can help manufacturers better prepare for unforeseen and uncontrollable events?
Sebastian Oeder: This question is quite difficult to answer in general, as we have no idea what the unforeseen event will look like. If you reflect this question to the unforeseen event of the current pandemic, the main challenge is to run our process in a safe environment for all of our employees. One of the most effective tools is social distancing, which practically means staying at home and work remotely if possible. Even with a high level of automation, the operational production process still requires a physical presence on site. But with advancing factory digitalization, and IoT emergent solutions, the need for personal interaction is already being reduced step by step. Production engineers can perform a wide range of analyses like tracking performance issues based on IoT-connected machines remotely. They can virtually enter a part of the factory, either a certain machine or a process, and receive up-to-date information about operations. This allows them to enhance decision-making and solve issues without being present on site. I’m convinced that continuing that trend further in the future, will also help to cope with unforeseen events even better.
Colm Gavin: And from my side in regard to unforeseen or uncontrollable events, we’ve talked about this many times already on this podcast, but the obvious thing to the obvious solution for an uncontrollable event in machine builders and manufacturing is the predictive maintenance and condition monitoring. Those are solutions that give you the transparency into your operations, allowing you to implement solutions, whether it’s condition monitoring, predictive maintenance, asset performance management to maximize the asset performance and health. So, taking the time to install those solutions and develop those algorithms – whatever it may be around predictive maintenance – this is something that can at least prepare yourself for an uncontrollable event, whether it’s on the machinery, a critical part fails, how are you able to get ahead of that. These solutions can solve common challenges and add risk to operations, such as lack of awareness to predict when an asset failure may occur, excessive downtime caused by calendar-based maintenance approaches, and our inability to use a machine of peak performance without causing a failure. So, it has been said before, but predictive maintenance and IoT are really the only way to implement these condition monitoring solutions and with predictive maintenance.
Another topic as part of this would be energy consumption. How can organizations increase efficiency and drive sustainability? You can maybe adopt IoT solutions to give you a better understanding or transparency on your resource consumption. And maybe with this level of knowledge, organizations can reduce the energy costs. So, with visibility into how much energy is actually being consumed, you can determine better ways to reduce the waste. So, for example, an IoT-enabled factory could help you identify a leak that is causing excessive water loss just as an example. Or you may be able to pinpoint a process that can be run during non-peak hours and incurring an energy discount and so on.
Matthias Lutz: So, the global pandemic has shown that disruption is typically outside of a manufacturer’s control. So, nobody knew that this pandemic will happen and therefore, I learned that organizations should look for ways to increase the reliability of their assets in areas they can manage. I specifically want to talk again about the closed-loop digital twin, so using IoT data to feed digital models. With this you can get live performance data from products and plants and operations, you can analyze this data to virtually validate the performance of assets in the real world and understand how they act under various conditions. Once you have done that, you can execute extensive testing to understand machines at a deeper level in a fraction of time and cost of physical efforts. And digital twins can be used eventually to optimize your assets in production, to influence your future product designs, and improve the quality of your machine – and with that, you can minimize the risk of failure and maximize performance levels, especially during situations like we are currently experiencing during the global pandemic.
Jörg Ludwig: And this concludes our last episode of our mini-series “Future-proof with the IoT,” a big thanks to our listeners and everyone who made this happen. Thank you Colm, Matthias, Heiko and Sebastian for lending your time and industry knowledge to the questions of IoT of industrial manufacturing.
If you missed any of the previous episodes, be sure to check out your favorite podcast platforms as we walk through industry trends and solution journeys. And for more information, visit us online at siemens.com/mindsphere
We hope you enjoyed the mini-series, take care and stay healthy!
About the Host and Guests
Jörg Ludwig – Since 2018, Jörg has been in the sales enablement team for MindSphere and since October 2020 also for Mendix, globally responsible for the creation of learning paths, enablement sessions, and value selling trainings and workshops. Prior to Siemens, Jörg ran his own business as a Value Selling trainer and coach for more than 7 years. He gained Sales experience and expertise from over 16 years in global Software Sales organizations.
Heiko Dickas – Heiko is the Team Leader of the digitalization team since the beginning of 2017 in the Bad Neustadt motor factory. His scope is being an enabler for the production unit in terms of digitalization. Heiko has been with Siemens for more than 30 years in different functions.
Colm Gavin – With over 20 years of experience in the Siemens Digital Factory, Colm works on business development for digitalization topics as they pertain to Siemens SW and Factory Automation, specifically virtual commissioning, Industrial IoT, Industrial Edge and AI topics.
Matthias Lutz – Matthias joined Siemens 14 years ago, starting in supply chain and procurement department. In 2015, he moved to the industrial customer service organization, focusing on industrial IoT and digital services.
Sebastian Oeder – Sebastian is Head of the production unit main motors in the Bad Neustadt motor factory. He has a background as a production manager at Siemens Energy and as a consultant at Siemens Corporate Technology.
Siemens Digital Industries Software drives the transformation to enable a digital enterprise where engineering, manufacturing and electronics design meet tomorrow. Xcelerator, the comprehensive and integrated portfolio of software and services from Siemens Digital Industries Software, helps companies of all sizes create and leverage a comprehensive digital twin that provides organizations with new insights, opportunities and automation levels to drive innovation.
For more information on Siemens Digital Industries Software products and services, visit siemens.com/software or follow us on LinkedIn, Twitter, Facebook and Instagram.
Siemens Digital Industries Software – where today meets tomorrow