Creating the perfect part with digital part production
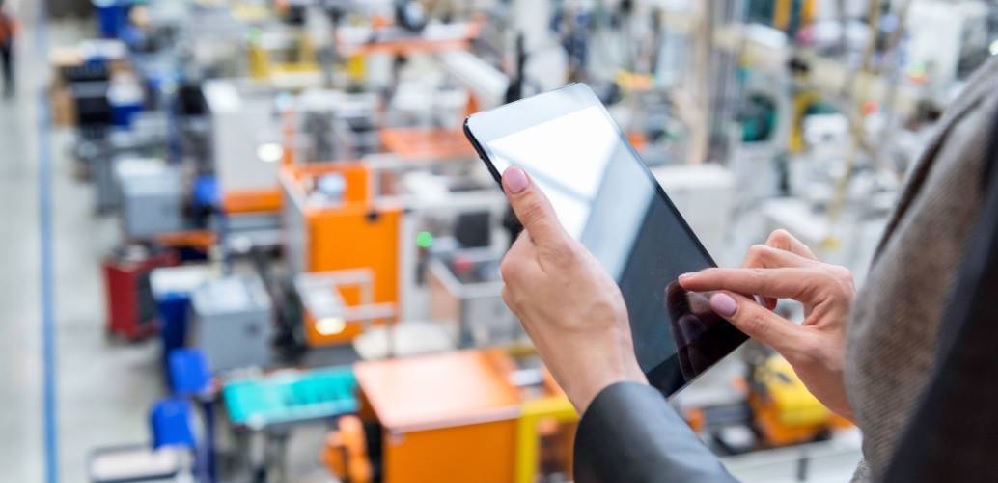
In today’s competitive industrial machining market, manufacturers need to build parts quickly while ensuring reliability and the highest quality. Also, it’s necessary to integrate these parts into the larger machines to meet high tolerance and precision needs while maximizing production capacity.
To stay ahead in this competitive landscape, machine manufacturers must merge their digital and physical processes while creating a continuous digitized communication and feedback loop to understand how part design changes impact the more extensive manufacturing process.
Listen to the webinar.
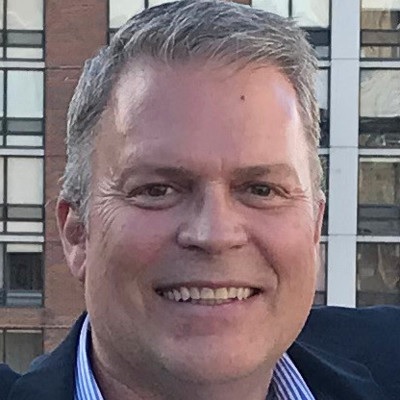
We are joined by experts Bill Butcher, Marketing Lead for Industrial Machinery at Siemens Digital Industries Software, and Frans Adamowicz, Solutions Director for Industrial Machinery at Siemens. This webinar reviews the value of the Digital Part Production solution, discussing three key differentiators:
- Highly Automated CAM – Easily reuse proven data to automate programming and optimize machining processes to deliver consistent results, improve quality, and reduce time to market.
- Synchronized Part Manufacturing – Increase operational efficiency of machine shops by using one integrated system to design, simulate, and machine parts.
- Additive Manufacturing – Create complex geometries that would be difficult or impossible to achieve with traditional manufacturing methods. These complex geometries can create parts that are often stronger and lighter than their traditionally manufactured counterparts.
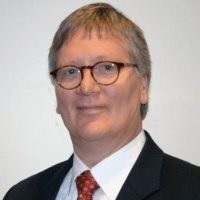
Read the transcript of this webinar:
Bill Butcher: We appreciate you joining us here today. New digital technologies are changing the way business operates in nearly every industry. However, few industries will be transformed as thoroughly as industrial machinery where digital technologies are not merely changing the way products are built and sold but how companies operate fundamentally. As part of this evolution, manufacturers must plan and decide how to upgrade and manage potentially thousands of pieces of machinery that have been deployed and are now becoming increasingly connected, delivering large volumes of data to be analyzed and understood.
When we look at the industrial machinery landscape, we continue to hear from our customers that several transformational trends mark significant turning points in this machinery evolution. First, there’s a marked shift towards personalized products and customized services. Second, machinery companies are challenged to design and build machines that support extended product mixes with rapid and frequent changeovers. So, because consumer preferences changes are more immediate, there’s added pressure to innovate quickly and compress delivery schedules. For example, a simple potato chip package that appears on the store’s shelves has the potential for multiple variants, leading to the explosion of complexity. These variants include sizes, shapes, packages per box, recyclability considerations and the effect of regional flexibility, including flavors, size and weights. This complexity quickly expands, and industrial components suppliers are quickly embracing IoT-enabled technology in their products. Therefore, machinery manufacturers are on a steep learning curve to take advantage of petabytes of data generated from today’s machines.
This scenario is rapidly changing the landscape for electrical and control automation engineers. Simultaneously, there are insights gained from so much information, which can be handled by automating production processes. The trend of hyper-automation requires vast amounts of data and cloud-based analytics to accelerate learning about machine behavior and performance to automate machine functions. However, adding sensors may not be enough. You need to have the capabilities to analyze the explosion of the complex data that you’re monitoring. Global competition has always existed. The competition comes from more flexible agile startup companies based on machine learning and not encumbered by existing business processes or a legacy customer base. Also, the aging workforce in many parts of the world has forced employers to replace experience with machine learning; hence, many machinery companies may not survive this transition.
So, how do you become a catalyst for change and help your customers take advantage of the trends I just spoke about? Well, the machinery companies that build and service the most automated, flexible, connected and adaptable machines are the ones that will define the future.
Let me share some of the ways’ machinery companies are working to increase their competitive advantage. The first is increasing machine flexibility – adding capabilities to existing machines, adding automation, software and mechanisms. For example, even historical mechanical and pneumatic systems are being replaced with electrically controlled functionality. Second, increase connectivity. IIOT combines smart sensors and cloud analytics to help build machines’ intelligence, enabling machines that adapt to their environment in real-time. Lastly, companies are building strong, intense partnerships with their customers. These partnerships not only solidify traditional business models but they’re also providing new business models, including subscription or production-as-a-service opportunities.
Understanding your customers and the effect of the trends in the market drivers can be overwhelming. However, the challenge of the machinery industry, whether it’s an OEM, a supplier or a downstream customer, can be summarized under one commonality: complexity. The true disruptors in the machinery industry won’t be those that are trying to limit complexity. There will be those who try to embrace it. We believe you need to bring innovative machines to market faster than your competition. You want to lower development costs and create reduction and operating costs. There is also a need to develop new business models that out-innovate, building differentiation through insights that do not duplicate easily.
No one knows better than you that your design, manufacturing and service processes increase in complexity exponentially. Each new machine created is built on a legacy that passed a variant of what came before. The design engineering process should leverage lessons learned and pass variants to generate more value for each custom design. Machinery manufacturing is dynamic. Each new machine executes through several methods, machines, and processes. It must be flexible to adapt to late changes, customer demands, purchase component deliveries, and even labor and machine changes. Also, service complexity will rise dramatically as field operations try to support each unique customer demand for high-performance and zero downtime.
We believe that true leaders in the machinery space (the disruptors I talked about earlier) will embrace these key concepts to turn complexity into a competitive advantage with a comprehensive digital twin. Insights and data from a comprehensive digital twin allow companies to accurately simulate the machines’ performance, build more flexible and connected machines handling a broader range of products, and enable quicker responses as consumers’ preferences change.
And keep in mind that any part of the real product production environment that isn’t represented in the digital twin can’t be simulated, thus introducing risk into your business, including modern, adaptable and personalized solutions. It is essential to provide people across an organization with easy-to-use tools. It can pull information from many places, presenting that information to them in a way that’s consumable for the task they’re trying to complete. Additionally, a flexible ecosystem allows information technology to play a more critical role in pursuing complexity as a competitive advantage. Although no one tool or vendor can do it all, if the tools you choose don’t work well together, they will fall far short of the goal.
So, we help manufacturers through these challenges through the application of Xcelerator, our integrated portfolio of software services and application development platform that encompasses all of Siemens software products and technologies. Xcelerator is a technical software foundation of a company’s digital enterprise that enables continuous ingenuity and product performance, product development, production operations and life cycle support. Xcelerator can also be personalized and adapted to fit customers and industry-specific needs to help companies of all sizes become digital enterprises. And we’ve done exactly that to create a specific industry solution for our Industrial Machinery customers.
Combining our in-depth industry knowledge with the accelerated portfolio, Siemens can create specific industry machinery solutions that provide an unstoppable advantage. Hopefully, you’ve been paying attention and joining us on some of our other webinars. We’ve already presented some Advanced Machine Engineering (AME) and Intelligence Performance Engineering (IPE). Today’s focus is on Digital Part Production, and we will dive a little bit deeper into how to master the precision of the perfect part. So, I’m going to ask my colleague and friend, Franz Adamowicz, to take it over and explain the solution to you in greater detail. Here you go, Frans.
Frans Adamowicz: Thank you for joining, and I’ll be your presenter for the next 30 minutes, talking more about the three differentiators. First, we have the highly automated CAM. You can easily reuse proven data to automate programming and optimize machining processes to deliver consistent results, improve quality, and reduce time to market. Secondly, we will talk about synchronized part manufacturing. Using one system to simulate the machine parts avoids multiple data transfers and manual work impacting overall efficiency. Lastly is additive manufacturing, and this is used to create complex geometries that would be difficult, or in some cases, even impossible to achieve with traditional manufacturing methods. So, these complex geometries are often more robust and lighter than their conventional manufacturing counterparts.
- Highly automated CAM solution software allows OEMs and suppliers to automate programming and optimize their machine processes to deliver consistent results. You can automatically create optimized CNC machine programs directly from the part designs by using feature-based machining. It can automatically recognize and program a wide range of machining feature types, including pockets, slots and holes, typically for machining components. A modern CAM system, like Annex CAM, enables you to capture and reuse predefined manufacturing parameters. Using process templates and machining data libraries, you can share expert knowledge and preferred machining methods, which can help standardize the production processes. Application-specific software significantly improves the NC programming productivity compared to the use of generic functions. For example, the automated chamfering and pinch turning operations helps engineers to quickly create optimized tool paths, freeing up valuable programming time and increasing companies’ throughput. As one of the largest suppliers of electronic machinery equipment, ASM technology uses Annex feature-based machining to effectively transfer design intent and automate NC programming time. ASM reduced NC programming time of machine components up to 91 percent while improving part quality by 90 percent.
- Synchronized parts manufacturing provides end-to-end orchestration of integrated engineering, manufacturing and quality processes. It leverages the product configuration backbone to provide a common definition of variability and quality. The aligned workflows between quality, manufacturing and engineering teams will improve collaboration and reduce the need for coordinating operators’ guidance for processes, reinforcement, production governance, time nonconformance and deviation management to support continuous improvement processes and decision-making. Also, it improves the quality integrated into engineering processes and change management, reducing failure costs and increasing customer satisfaction. Additionally, you can do KPI monitoring from machine monitoring to line implants performance analysis.
- Additive manufacturing provides the most efficient results to have a truly integrated additive manufacturing process. It is a design solution that can create complex geometries and build solutions to prepare the model for 3D printing. Also, it provides a manufacturing solution that can support all printing technologies integrated with conventional subtractive machining. For example, in conventional production, a gas burner can consist of 13 individual parts, which need to be measured, then welded together and tested. Still, with the additive manufacturing model, it can be reduced to a single workpiece and the development lead time reduced from 26 weeks to three weeks.
A real customer example is a bottle testing machine developed by a Belgium company called Delta Application Techniques. It is testing plastic bottle leakage through a vacuum device. This machine was built in Romania, and in a combined project, Siemens updated and modified it, installing hardware and software from Siemens and now sold in Belgium. Within Delta Engineering, only 20 percent of the cost of this quality testing machine is spent on buying components, and the remainder is being kept in-house by internal part manufacturing and machine assembly. In this digital thread, we are demonstrating the process steps needed to produce motor brackets.
However, part manufacturing is more than just machining the brackets, and our digital part production solutions show the value of having an integrated process – the digital production twin. So, from planning to programming, CNC and CMM are connected to production scheduling, actual machining in a managed production environment, and ensuring quality through validation step capturing and managing issues if they arise.
I will present the most relevant solution capabilities for each process step that helps machine builders achieve their customers’ requirements.
I visualize these process steps sequentially, but of course, in an integrated process, some steps can run parallel. For example, you can implement process templates in manufacturing planning to capture knowledge and best practice process plans for reuse. Also, you can manage all your manufacturing resources like tools, fixtures and machines using a single digital library capable of accessing classified and fully defined mobiles of resources from downstream applications, such as CAM and CMM inspection program software. Thus, a continued thread of information from a single source of data can be created connecting manufacturing, planning and production environments.
Tool and product costing. Product costs and prices are decisive in determining how successful a company will be with products in today’s competitive global markets. OEM suppliers and toolmakers’ efficient and quick costing processes, high-cost transparency, and reliable cost estimates are mandatory for achieving excellent cost management for products and tools along the entire supply chain. You can leverage existing costs engineering with existing resources. Early decisions about product design and manufacturing determine up to 80 percent of the future production costs of a new product using decision templates. Cost management provides companies with more opportunities to optimize product costs to maximize margins, profits and return on investment. It also enables companies to obtain reliable cost estimates and high-cost transparency to achieve target costs.
CMC programming. Highly automated CAM solutions allow original equipment manufacturers and their suppliers to automate NC programming and optimize machining processes to deliver consistent results, improve part quality, and reduce time to market. By minimizing the manual input during the manufacturing planning process, companies can reduce waste and eliminate costly errors in production. In addition, modern CAM software provides automated capabilities and the ability to reuse knowledge and data from past productions, enabling engineers to program and digitally validate complex parts in minutes. This can streamline and accelerate the entire part manufacturing process, giving OEMs and suppliers a competitive advantage.
Quality inspection programming. The control and inspection planning feature manages the process steps and activities to control critical elements during manufacturing. The potential risk could not be mitigated entirely but controlled systematically to identify defective parts. In this feature, we leverage the information on the 3D model or the 2D drawings with their PMIs. PMI stands for product manufacturing information, and PMI can be used to automate inspection programming. FMEA, or failure mode and effect analysis, allows detecting failures in the design and manufacturing process in the early phases of development before production. FMEA improves functional safety and product reliability and reduces warranty claims and costs. This methodology is supported by Siemens and allows you to support FMEA planning by the specification of new industry standards. It is a direct connection, so you can download CMM programming from Teamcenter and upload it to MES.
Production scheduling. Machine shops can be very dynamic environments, with scheduling changing every day, sometimes every hour. Having a flexible scheduling tool that posts all the recipes or builds a process from the digital twin helps find the best path forward. As a result, you can maximize production plan reliability and resources usage and provide the best sequence of operations according to plant resources and constraints. For example, based upon company rules, allow the planner to select the best order sequence. And wide visibility into real-time work in progress production and plant capability will enable you to reschedule capacity when needed. Also, creating a detailed schedule for tool and equipment optimizes set up times to ensure product due date and minimize deviation.
CNC machining. Parts are manufactured using a cost-effective, time-efficient process. Transfer work packages are used to enable machine tools’ latest technologies, like high-speed machining and machining robots, to capture operator’s feedback. You can plan and validate multiple operations for single parts and have advanced capabilities to program new generations of CNC machines like multi-axis, multichannel and machining robots that enable manufacturing complete products in a single setup. Additionally, verify machine characteristics continuously to enable diagnosis triggering maintenance.
Additive manufacturing capabilities. Traditional manufacturing techniques for components generally involve material removable, and once produced, the assembly process of the multiple components often involves specialized processes and tooling. Additive manufacturing is changing the way products are made. Often it becomes a part of a hybrid manufacturing process, enabling an associative workflow between design, simulation and build preparation. Digitally integrated data between additive manufacturing and CAM systems allow for easier process programming after the part has been printed. Moreover, one important capability is the ability to perform optimal orientation, improving print process simulation.
Production execution. Discrete manufacturing is often characterized by limited Folium and very high complexity. New markets, new materials and new technologies require increased flexibility in manufacturing processes while straining plant efficiency and productivity. Our production execution discreet solution provides visibility into work in process, product traceability, and genealogy to create dashboards and monitor production KPIs to support the plant managers in making the right decisions for the business. The most critical capabilities here are the end-to-end orchestration of integrated engineering, manufacturing and quality process, and an operator’s guidance for processes reinforcement and production governance, including seamless integration with automation systems on the shop floor.
Quality inspection validation. Teamcenter quality can be used to extend Teamcenter active workspace capabilities with a problem-solving process integrated into the quality product family, feeding back into our FMEA. This solution provides a closed-loop approach from design to manufacturing on the shop floor and backward. Centralized quality management to capture data and detect nonconformance from internal sources, suppliers or customers. Quality issue management allows recording quality issues throughout the company by all users as a central solution. Problem-solving will enable you to find and eliminate root causes effectively, considering all internal knowledge basis as a comprehensive root cause, and analysis, corrective and preventive action management tools utilizing commonly known methods. Quality action management centralizes all quality-related activities and monitors their company-wide status with automated escalation mechanisms for securing on-time closure of quality actions.
I would like to end the session with three success stories showing how companies can benefit from using our digital part production solutions.
The first one is Telsmith, Inc. This company, founded over one hundred years ago, designs, manufactures, markets and services a full line of mineral processing equipment. One of Telsmith’s widely known brands is Iron Giant, which gives an idea of the size of the equipment. Crushers can be up to 15 feet tall and weigh more than 60 tons. Facing challenges to increase their CNC programming output and improve NC machine productivity, they use Annex CAM to make easy changes to CAM models with synchronous technology, integrate toolpath simulation and verification and high-speed support machining. Telsmith claims that their new efficient CAM process led to a performance rating of 193 percent better than other CAM software. Annex CAM generates more programs despite being used to program more complex machines. For manufacturing, it digitalizes effective department processes to boost your productivity, including synchronized manufacturing with a mobile-driven process, increasing machining efficiency by using the latest CAT CNC technology and produces higher quality parts with streamlined data flow across the entire operation.
The second success story is Proform. This company was founded in 1967 and is located southwest of Leon, France. Proform first specialized in cold forming of tubes and then became a specialist in bending all types of stainless steel and nickel alloys. It’s a small company with 210 employees and facilities covering 40,000 square meters, a yearly revenue of 28 million euros, with more than 60 percent of that coming from exports. So it has a dealer network covering more than 40 countries. Proform needed to implement a scheduling solution that can keep pace with the company’s growth, managing diverse materials, part types and deadlines. They also needed to increase their manufacturing capacity. Using an advanced planning and scheduling system, the increased administrative efficiency of work centers by 87 percent improved the ability to meet deadlines with a 96 percent on-time delivery rate. In addition, it multiplied workload by 20 times, reducing the number of people administrating work centers from three to one.
And the third customer example is Toolcraft. Toolcraft is a precision manufacturer in Germany. They have 350 employees and 17 CNC machines. In 2011, they purchased their first additive manufacturing machine, an early entrance into the 3D printing field. Toolcraft now possesses ten powder bed additive manufacturing machines. In addition to 3D printing, Toolcraft offers the entire process chain, starting from design and ending with non-destructive testing on the part. Using our tools, the company achieved a 50 percent reduction in tool weight, reduced cycle times by 30 percent and consumed less energy in the process.
In concluding this presentation, I want to mention this is the first of four presentations on Digital Part Production. For each theme, we will conduct a dedicated webinar later this year. For example, highly automated CAM will have a webinar in August. Synchronized part manufacturing webinar is in October and more details on additive manufacturing in December. Invites will be sent out for these.
Bill Butcher: Your customers are demanding that customized machines are delivered in shorter timeframes. I think that’s known today, and to meet these demands these machine designs are becoming exponentially more complex. We talked about how high levels of customization are increasing machine complexity and driving the need for synergy across machine designs and manufacturing strategies. Siemens is the only company to provide you with an available digital solution to simulate machine design and bring it to life in the digital world.
This comprehensive portfolio that we talked about today is Xcelerator, combined with an application development platform to accelerate your efforts further. The engineering teams innovate and create precise, digital twins of your products, productions and operations to manage the complexity of smart products and smart production operations. Siemens offers the flexible and adaptable applications and solutions required to help you build more flexible machines required for you to adapt to the changing consumer needs. Thank you all for joining us today.
Software solutions
Siemens Digital Industries Software drives the transformation to enable a digital enterprise where engineering, manufacturing, and electronics design meet tomorrow with the Xcelerator™ portfolio.
Xcelerator is a comprehensive, integrated portfolio of software, services and an application development platform, accelerating businesses’ transformation into digital enterprises. It unlocks a powerful industrial network effect – essential requirements to leverage complexity as a competitive advantage, no matter the industry or company, to seamlessly create tomorrow’s complex machines.
About our experts:
Frans Adamowicz is Solutions Director for Industrial Machinery, responsible for supporting the industry lead in delivering key strategic initiatives, solutions, and global business development. As part of the industry’s team, he’s responsible for identifying key initiatives and developing solutions for the industry while working closely with industry-leading customers and providing thought leadership on new and emerging issues faced by the machinery industry. Franz’s experience and insights are derived from a 35-year career of delivering software-based solutions for product engineering and manufacturing innovation for the global manufacturing industry. He has held leadership positions in multiple functional areas, including sales and services management, country and industry marketing management, having focused exclusively on the industrial equipment and machinery industry globally since 2007.
Bill Butcher is the Marketing Leader for the Industrial Machinery industry team and has over 20 years of experience within the manufacturing software and technology space. In Bill’s current role, he is responsible for delivering strategic marketing content, including campaign strategy, go to market messaging, and digital inbound content that communicates the value of the Siemens Digital Industry Software portfolio to the enterprise SMB and SAS channels.