Future-proof with the IoT miniseries – ep. 2 Transcript
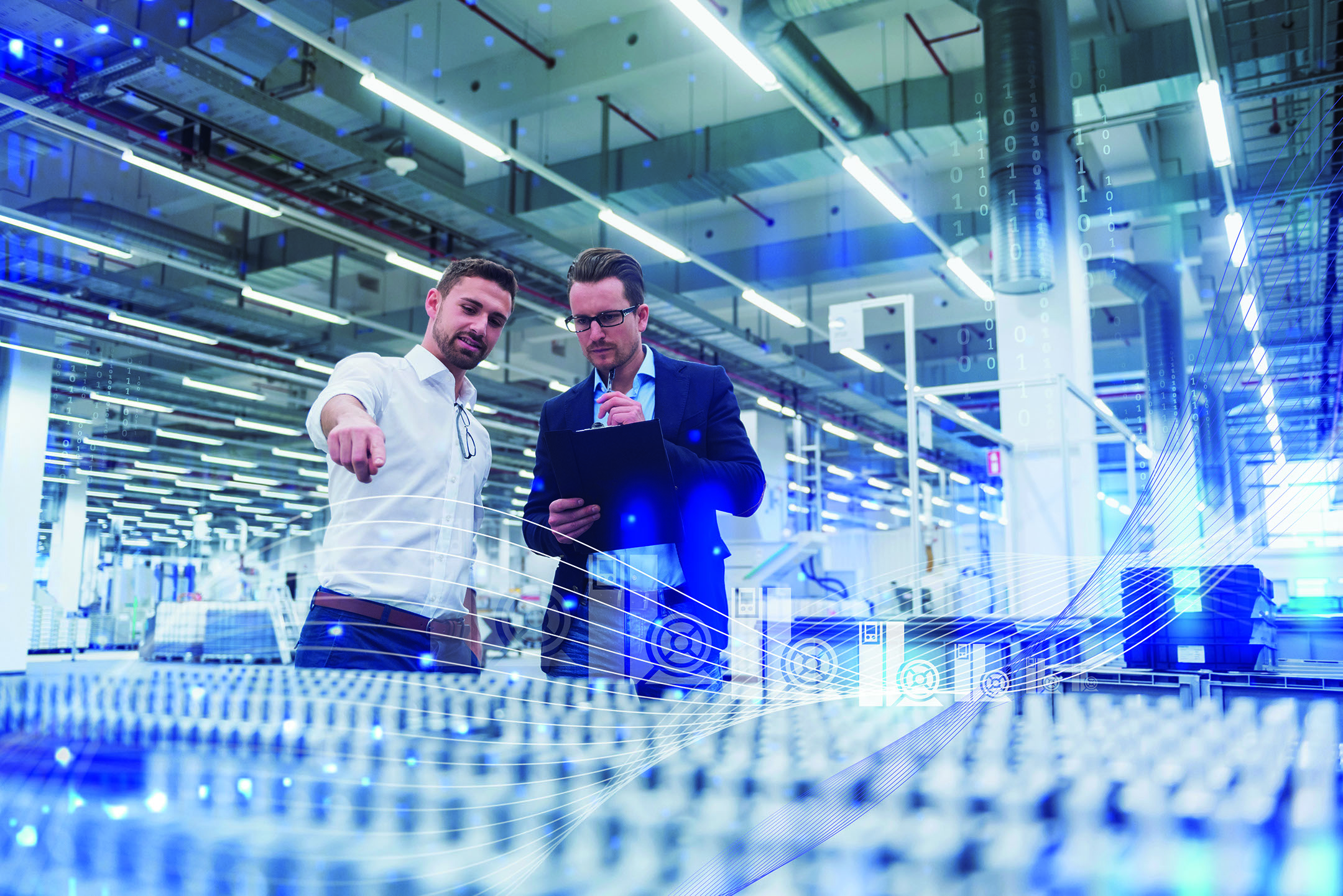
Welcome to the second episode of the miniseries Future-proof with the IoT, with your guest host Jörg Ludwig. Over the next few episodes, Jörg will be continuing his conversation with his guests – Heiko Dickas, Colm Gavin, Matthias Lutz and Sebastian Oeder – on how Internet of Things (IoT) is changing the industrial machinery industry and the pressures that have made it an impossible technology to ignore.
In the first episode, our experts covered how industrial machinery as a sector is adopting new business models as well as how hyperautomation is a growing strategy against industry competition. Today, the conversation of industry trends will be extended to low-cost competition as well as the next generation workforce. And throughout the episode, Heiko and Sebastian share their first-hand experience of these pressures from their time at the Siemens Bad Neustadt motor factory.
Hit that play button and read along as our experts dive into the major trends they see guiding the industry into the future as well as some solutions to apply IoT earlier for a greater return on investment.
Jörg Ludwig: Hello! This is “Future-proof with the IoT”, a podcast miniseries that is part of “The Digital Transformation: Solutions for Industrial Machinery Podcast”. This particular mini-series is focused on how to leverage digitalization to overcome manufacturing disruptions and bounce back stronger. I’m your special host, Jörg Ludwig.
In today’s episode, we want to continue the discussion about the general trends that were hampering productivity in manufacturing even before COVID arrived. And for that, our specials guests are back: welcome Colm Gavin, Portfolio Development Manager at Siemens Digital Industries Software, Matthias Lutz, Head of PreSales and Solution Design at DI SW, and Siemens Bad Neustadt’s Heiko Dickas and Sebastian Oeder, leader of the digitalization team and head of the production unit main motors at the electric motor factory, respectively.
In the first episode, we talked about the trends of new business models and hyperautomation. Today, we will focus on low-cost competition and a new generation workforce. But those trends are nearly inseperable. For example, Colm, would you say hyperautomation and other technologies are key to our third trend: low-cost competition?
Colm Gavin: Absolutely. In talking with my colleagues about this hyperautomation, you know, hyperautomation came out as a response to low-cost competition. So, you need to be able to innovate to stay ahead with better quality, better service to compete against low-cost competition because we definitely see an increase in the competition overall in manufacturing, but it’s especially aggressive from lower-cost machine builders. The effect of low-cost manufacturers is that it will be difficult to maintain those margins. So, what’s important for the machine builder will be time to market, reliability, flexibility, they will become differentiators against the low-cost manufacturers. The machine builders will have to be more innovative to stay ahead of the competition. And one thing, an example that I work closely with a lot of machine builders is one way to combat the low cost is embracing the simulation tools where you can simulate a complete machine prior to the physical installation. This means faster startup for new production lines, reduced on-site commissioning, and ultimately better quality. Because that’s ultimately how you are going to win against the low-cost competitors is better quality. Because if the machines are not fully tested, or if they don’t comply with the feature specification, then that could result in long startup times which can be prohibitively expensive if there are some errors or parts need to be reworked.
Matthias Lutz: So, Colm, to remain competitive, customers need to increase their labor and machine productivity, while also reducing costs. This requires leveraging digital technologies to improve operational efficiency. For example, machine utilization, resource use such as material, energy, labor, maintenance processes, and the entire supply chain. And based on my customer conversations, I think it’s very important not only to think about low-cost competition and lowering prices and stuff like that. It’s more about differentiation. And with IoT, you can substantially change the way you are interacting with your customer. It’s not only about technology, it’s really about the way you interact with your end customer and to get a much better proximity to your customers, and therefore, I think IoT has the potential to make a machine builder an integral part of the value chain of production companies. Very exciting, and I really see this trend coming up that IoT will move the machine builder much closer into the core of the manufacturing company.
Jörg Ludwig: Yeah, it’s interesting to hear, Matthias. And Colm, is there a sector with high competition of low-cost providers?
Colm Gavin: What we’ve seen is really the manufacturers of the components that go into the machines – they are all competing against low-cost providers, manufacturers of pumps, bearings, valves, conveyors. So, those components that would go into a machine builder, whether it’s a packaging machine or whatever it would be, that’s what we’re seeing, at least among our customers, some real competition for those components within the machines.
Jörg Ludwig: And Sebastian, can the same be said for competition with Siemens Bad Neustadt? Is competition greater with international providers? What do you think?
Sebastian Oeder: We are in continuous competition with companies around the world for many years, so I would not rate this as a new trend or a new driver for our activities. No matter if competitors are in the local sector or not, the targets of our improvements are the same: coming more efficient, reduce lead time, and improved quality maybe with a different rating over time. For this objective, we are using our toolset in digitalization and automation along our entire value stream. Every implemented automated system or digital solution further increases efficiency and strengthens our position. My personal perception is that with a higher level of automation, also production costs will level up around the world. Not direct production-related factors and expenses and time like transportations, customs, and so on, will influence to a higher degree in the future.
Jörg Ludwig: Colm, that seems like a real sticking point for companies, especially with an aging workforce. With a high number of workers reaching retirement and the emergence of technology-enabled jobs as we’ve been talking about, how are companies expecting to fill the employee and skill shortage? Do you think that manufacturers and customers you talk with are worried about this?
Colm Gavin: Absolutely. This is one of the major challenges for a lot of US manufacturing companies. The manufacturing workforce is aging, baby boomers are nearing retirement. In fact, the Deloitte 2018 study stated that US manufacturing is looking at a potential shortage of 2.4 million workers in the next decade, taking their specialized skills and knowledge with them, as we refer to it, tribal knowledge just disappears out of the company. So, at the same time, the manufacturing industry is expanding, and they’re producing more jobs and they will be needed to be filled but there is that then shortage of skilled labor factor. And in my personal experience, this is a major issue for manufacturers. When we have digitalization discussions with them, this topic comes first to the list as far as what’s important for them – how we can help them with the aging workforce, and that tribal knowledge leaving their facilities. And we see this especially companies with large facilities in, say, rural areas in the US, where they really struggle to get skilled workforce who want to work in maybe not so glamorous locations in the US, they’d prefer to be in California, Boston, New York, or wherever, but getting skilled workforce is an issue.
But one thing I think that IoT can really help with this, we have tools in our MindSphere® Suite – Collaboration Board being one – which is really all about collaboration and aimed at capturing that tribal knowledge before it leaves the company forever. This particular tool allows operators, at different locations, document and share issues that they were having on a production line. it’s always moving that tribal knowledge that might be on paper into a digital format so they can capture their experience on the machines, on the production lines, and share that within the company. So, that’s an IoT-based tool within MindSphere that we feel can help. We need ways, we need tools to capture that tribal knowledge before it leaves the company.
Matthias Lutz: I think that’s a very important point because worker shortages means manufacturers will have an inability to deliver open orders on time, expand production levels, respond to customer needs, leverage new market opportunities, and develop new innovations and new products. We had some discussions around a huge press line at an automotive customer. And somehow, our task was to get this press line connected to our IoT platform to look into all the automation settings and to find some correlation to the actual, let’s say, quality of the produced products. And then digging deeper into that use case, I felt that a huge driver for this initiative was that a lot of this workforce will retire soon and some of this knowledge should be preserved in algorithms, in data structures, and eventually, in actual applications that lead to a better outcome of this press line.
Jörg Ludwig: Thanks, Matthias and Colm for your perception. Sebastian, is retiring workforce becoming an issue in Siemens Bad Neustadt?
Sebastian Oeder: It is not a major issue in our current situation. There are already standards and tools in place that ensure the transfer of know-how on quite a good level. Personally, I think that the generation change is a chance to further develop our digital use cases. The generation of digital natives adapts more easily to digital solutions and carries that mindset into our processes; that places a trail from centralized experts to decentralized multiplicators, which is very important. Nevertheless, we see a huge impact of automation and digitalization to the required skillset and competencies of all of our functions. Everybody from group leader to manager in production, quality or logistics needs to develop the required competencies to efficiently use the digital tools. In Bad Neustadt, we implemented an active competence management. For each profile, the required competencies are defined and linked to the required trainings. This is the most important factor from my point of view.
Jörg Ludwig: If a retiring workforce is not as much a problem for Bad Neustadt, what has been a hurdle to adopting a new factory workflow? Has it been difficult to implement the tools that use IoT data?
Heiko Dickas: As Sebastian mentioned, we already have most of the knowledge from the retiring workforce. But to look in a more cultural way, we had a lot of effort by operating inline systems, servers, and so on. We had to take care of updating systems, security topics, implementing hot-fixes, and so on. Also, if we wanted to connect machines from different locations in the world to have an overall overview about it, it was not very easy to realize that. And to switch to a cloud solution, we now can focus more on setting up use cases, of course. You have also some infrastructure topics in terms of setting up a connection to be done. But especially at the beginning, we had also to learn many things, also, as an early adopter for MindSphere version two and later to move then to version three, but we don’t have to overwrite the MindSphere itself. So, we can focus and we can use the manpower creating benefits for the shop floor productivity.
Jörg Ludwig: So, thanks Colm, Matthias, Heiko and Sebastian! All these insights and challenges in manufacturing have been really interesting and helpful for a view into the Industrial Machinery industry. I’d like to thank our listeners for joining us for the second episode of “Future-proof with the IoT”. We still have so much of the story to share. And in the next episode, we will cover how the Internet of Things can help solve these industry challenges. Take care and we hope to have you again!
About the Host and Guests
Jörg Ludwig – Since 2018, Jörg has been in the sales enablement team for MindSphere and since October 2020 also for Mendix, globally responsible for the creation of learning paths, enablement sessions, and value selling trainings and workshops. Prior to Siemens, Jörg ran his own business as a Value Selling trainer and coach for more than 7 years. He gained Sales experience and expertise from over 16 years in global Software Sales organizations.
Heiko Dickas – Heiko is the Team Leader of the digitalization team since the beginning of 2017 in the Bad Neustadt motor factory. His scope is being an enabler for the production unit in terms of digitalization. Heiko has been with Siemens for more than 30 years in different functions.
Colm Gavin – With over 20 years of experience in the Siemens Digital Factory, Colm works on business development for digitalization topics as they pertain to Siemens SW and Factory Automation, specifically virtual commissioning, Industrial IoT, Industrial Edge and AI topics.
Matthias Lutz – Matthias joined Siemens 14 years ago, starting in supply chain and procurement department. In 2015, he moved to the industrial customer service organization, focusing on industrial IoT and digital services.
Sebastian Oeder – Sebastian is Head of the production unit main motors in the Bad Neustadt motor factory. He has a background as a production manager at Siemens Energy and as a consultant at Siemens Corporate Technology.
Siemens Digital Industries Software drives the transformation to enable a digital enterprise where engineering, manufacturing and electronics design meet tomorrow. Xcelerator, the comprehensive and integrated portfolio of software and services from Siemens Digital Industries Software, helps companies of all sizes create and leverage a comprehensive digital twin that provides organizations with new insights, opportunities and automation levels to drive innovation.
For more information on Siemens Digital Industries Software products and services, visit siemens.com/software or follow us on LinkedIn, Twitter, Facebook and Instagram.
Siemens Digital Industries Software – where today meets tomorrow