Connected engineering is more than communication
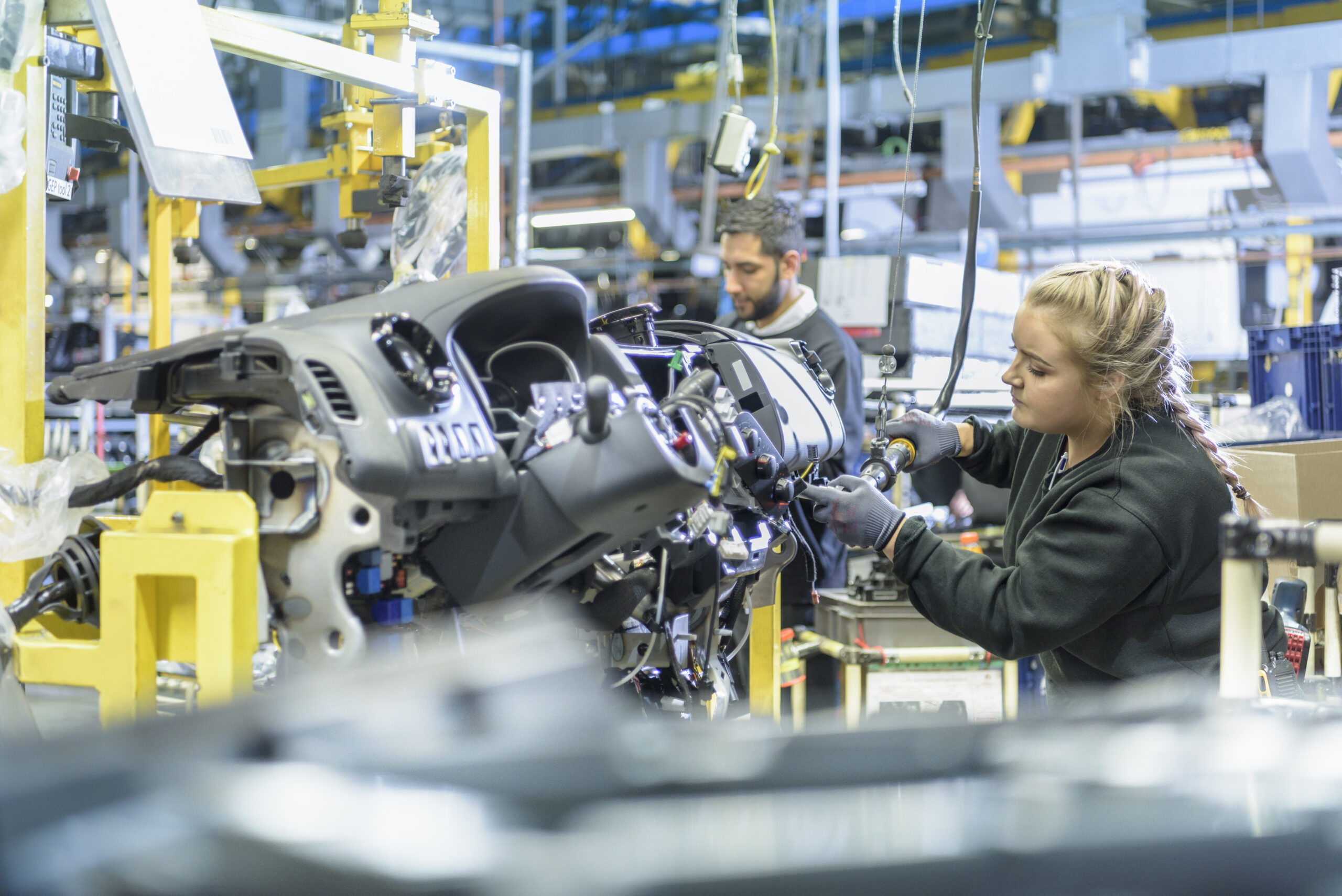
In the third interview with Nand Kochhar, VP of the Automotive and Transportation Industry at Siemens Software, on model-based systems engineering (MBSE) for automotive development he addresses how to integrate teams to work on their complex projects. Not only do the complex programs of today need specific requirements to guide development practices as was discussed in episode 2 of the Future Cars podcast with Conor Peick, but teams need to understand how the Product Definitions connect the work of electrical engineers with software or mechanical engineers. And it is important to remember that while Connected Engineering does enable efficient interdisciplinary development, it is so much more.
Faster innovation
Automakers today are being squeezed to innovate faster than ever, the number of disciplines required to develop a successful vehicles has expanded far beyond the almost entirely mechanical designs of the past century. That comes from replacing purely mechanical systems with mechatronics – remote lock doors need to be able to receive input both electronically from the remote and through mechanical means on the door itself, or in the newest cars it may also include software to unlock your doors with a personal electronic device. Examining even this relatively simple system, development requires input from the mechanical engineering team to ensure components fit within the door and any linkages work effectively, electrical and electronic engineers need to ensure the mechatronic or electronic control systems fill function effectively in the confined space near other electrical systems like window controls and cabin audio. And software engineers need to ensure that the system works reliably for the customer but also that it is as or more secure that the purely mechanical equivalent.
Complexity of the situation only grows as more systems are connected within the vehicle, take the goal of electric vehicle propulsion – electrical systems need to be more robust to handle the loads for charging batteries and running the engines, these systems require a very different architecture compared to internal combustion engine (ICE) counterparts. Mechanical and electrical engineers need to work within their own environments to optimize the complete system, but they also need the external system requirements to be displayed in relevant context. A mechanical engineer needs to know the dimensions of a harness, but not necessarily the function. Much like a software engineer needs to know of the electrical mechanical interfaces but not how the digital signals invoke mechanical outputs.
Systems beyond the vehicle
But connected engineering is not restricted to the design of vehicles, in fact it is important throughout the entire development process and even beyond the factory floor in some cases. Many of the processes for accelerating automotive design rely on simulating behaviors rather than physically testing every system. That is great for well understood physics problems, but in multi-physics simulations and attribute balancing processes the projected results from simulation need to be validated against real-world tests and optimized for future use. This process is especially useful for vehicles with multiple variations. One model of truck might have four different wheel bases for cab and bed styles, mixed with multiple drivetrain types and even fuel types, testing each of these combinations separately would be an onerous process. Instead an OEM might pick a representative sample to compare simulation results again real-world testing and fit the remainder to the correlation.
For autonomous transportation technologies the integration of development teams between the physical and virtual worlds may also extend beyond the showroom floor. More tradition mobility offering may aggregate driving data to improve the autonomy functions of the all vehicles with the technology, where new encounters are added to a repository of possibilities and the systems can learn how to approach novel problems. For fleet vehicles and distributed mobility networks, the routes of the vehicles might be optimized based on the available infrastructure of the region they operate within.
There are so many possibilities for the future of the automotive and transportation industry, but implementing them safely and faster than the competition requires a comprehensive solution. Connected Engineering is part of that solution and for more information on how it is accelerating the development of vehicles make sure to listen to the third interview with Nand Kochhar on Software and Systems Engineering, an MBSE solution for the automotive market.
Siemens Digital Industries Software is driving transformation to enable a digital enterprise where engineering, manufacturing and electronics design meet tomorrow.
Xcelerator, the comprehensive and integrated portfolio of software and services from Siemens Digital Industries Software, helps companies of all sizes create and leverage a comprehensive digital twin that provides organizations with new insights, opportunities and levels of automation to drive innovation.
For more information on Siemens Digital Industries Software products and services, visit siemens.com/software or follow us on LinkedIn, Twitter, Facebook and Instagram.
Siemens Digital Industries Software – Where today meets tomorrow
Nand Kochhar is the vice president of Automotive and Transportation Industry Strategy for Siemens Digital Industries Software. He joined Siemens in 2020 after nearly 30 years with Ford Motor Company, where he most recently served as Global Safety Systems Chief Engineer. In this capacity, Kochhar was responsible for vehicle safety performance of all Ford and Lincoln brand products globally. He also served as Executive Technical Leader, CAE, and as a member of Ford’s Technology Advisory Board. Kochhar’s tenure at Ford also included executive engineering leadership across a range of disciplines including in product development, manufacturing, digitalization, simulation technology development and implementation.
Kochhar has additionally been active in SAE International, where he has served as Chairman of the Executive standards committee, leader of a cross-industry group focused on driving standards for mobility, autonomous vehicle development, electrification and connectivity. Kochhar also served as Chairman of SAE’s Motor Vehicle Council for 2015-16 terms, after which he was named the Vice Chair of Technical Standards Board (TSB) in 2017 and then TSB Chair in 2018 and 2019.
Kochhar graduated from Missouri University of Science and Technology (Missouri S&T) with a master’s degree in Engineering Mechanics. He was inducted as a member of the Academy of Mechanical and Aerospace Engineers at Missouri S&T in 2005. He lives in Northville, Michigan with his wife and two kids.
Conor Peick works as a writer covering Automotive and Transportation topics for Siemens Digital Industries Software. In this role, he has helped produce a variety of materials including blogs, articles and whitepapers on automotive topics ranging from wire harness design and manufacturing to embedded software development and overall industry trends.