Podcast series: Additive manufacturing – an industrial revolution (Part 4) – Materials Solutions future
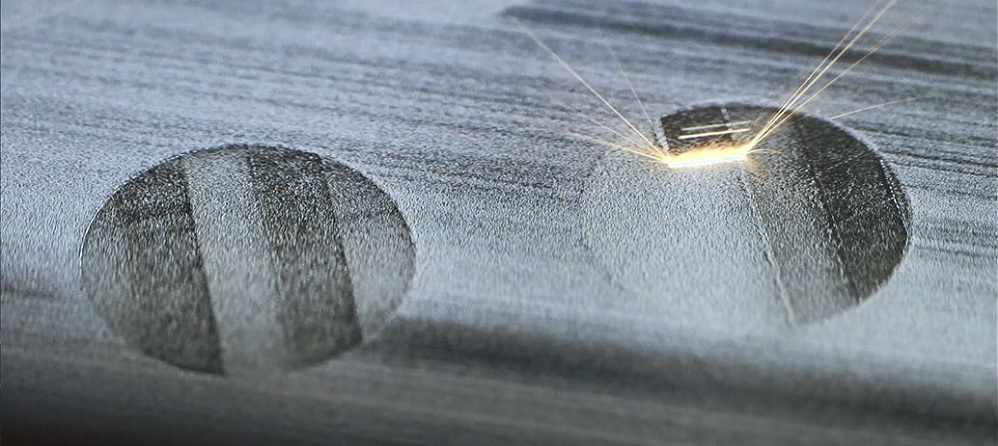
In this fourth podcast of our new additive manufacturing podcast series, we are joined once again by Tad Steinberg, manager of Siemens Energy’s Additive Manufacturing (AM) business development, and Trevor Illston, Chief Technical Officer for Materials Solutions Ltd. As mentioned in our third podcast, Material Solutions is a print service provider that Siemens acquired in 2016 where they print complex metal parts with exceptional quality.
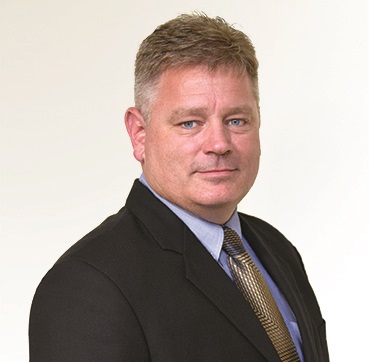
In that episode, we discussed the services Materials Solutions provides, diving into what customers are doing with additive and documenting their customer needs. Lastly, we touched on the future of material solutions.
In this current episode, Tad and Trevor elaborate on that future. In the ongoing expansion of their facilities, they add new materials and capabilities to their services, which can be a problematic endeavor requiring more learning.
Challenges in new materials and machines
Some materials can be straight-forward, like processing nickel superalloys, which is relatively painless; others involve mixing titanium or aluminum to the nickel, becoming more sophisticated and complex.
In this scenario, there’s a challenge in working with varied characteristics in the additive machine. Therefore, it’s essential to respond to the additive process by optimizing it to suit the material types. Also, moving from one machine vendor to another requires a learning curve. Each machine has its features and challenges. New machines can take six months to a year to understand, even when using the same material characteristics.
Moreover, it’s essential to ensure that each machine is consistent with established standards, including the software, setup and calibration to guarantee consistent results. So, special care is required to safeguard these items when setting up new capabilities. Also, a constant recalibration process is critical to the preventative maintenance method. Therefore, ongoing monitoring of process variables from the OEMs is vital to guaranteeing performance expectations.
More materials are accumulating to the set of available materials to use. One of the unique things about Material Solutions, in the early days, was identifying a limited palette of materials. However, customer’s needs came into play, thus developing more materials. A massive explosion of material types is growing in the market, enhanced by technology, making it challenging to keep up with what’s available. Therefore, it’s essential to target the resources for materials that adapt to customer needs, applying new materials to work adeptly on a machine, thus qualifying it for customer acceptance. This requires selective measures in choosing proper materials.
Industrializing additive manufacturing and its evolution
On the software side, the goal is to industrialize additive manufacturing to print quality parts repeatedly, in serial production. A serial software tool is necessary to control and manage the manufacturing process and record the output continually. This journey needs to be simplified. Subsequently, as technology progresses, software tools and packages are also moving, making it easier to transfer from one part of the process to the next, providing a seamless conversion without errors – a significant change in the process.
One of the major catalysts for change in additive manufacturing, prompted by climate change, is efficiency, most valid with industrial gas turbines and narrow engines – especially in aerospace. Therefore, regulations provoke the need to reduce emissions and fuel burns, propelling people toward innovative design components. Consequently, additive manufacturing enables designs not possible with conventional manufacturing.
Subsequently, a broader range of components is available in additive manufacturing. The traditional mindset is starting to change with attrition, bypassing the conventional perspective to advance additive’s possibilities further, hastening the delivery of benefits, backed by confidence in the technology that’s proven in the marketplace.
Learn more by listening to this fourth podcast in the additive manufacturing series.
You can also access this podcast via Apple, Stitcher, Spotify, Castbox, TuneIn or Google.
Siemens Digital Industries Software is driving transformation to enable a digital enterprise where engineering, manufacturing and electronics design meet tomorrow.
Xcelerator, the comprehensive and integrated portfolio of software and services from Siemens Digital Industries Software, helps companies of all sizes create and leverage a comprehensive digital twin that provides organizations with new insights, opportunities and automation levels to drive innovation.
Also, for more information on Siemens Digital Industries Software products and services, visit siemens.com/software or follow us on LinkedIn, Twitter, Facebook and Instagram.
Also, listen to podcast01, podcast02 and podcast03 in this series.
Siemens Digital Industries Software – where today meets tomorrow.
About our experts:
Tad Steinberg – Manager of Siemens Energy’s Additive Manufacturing (AM) business development, an experienced, results-oriented technical leader demonstrating the ability to build and lead global teams to new levels of business-to-business success in fast-paced environments. Ten plus years of management experience and more than 20 years of experience within the Aerospace and Energy sectors.
Trevor Illston – Chief Technical Officer for Materials Solutions Ltd