Modeling successful IT/OT convergence in Bad Neustadt
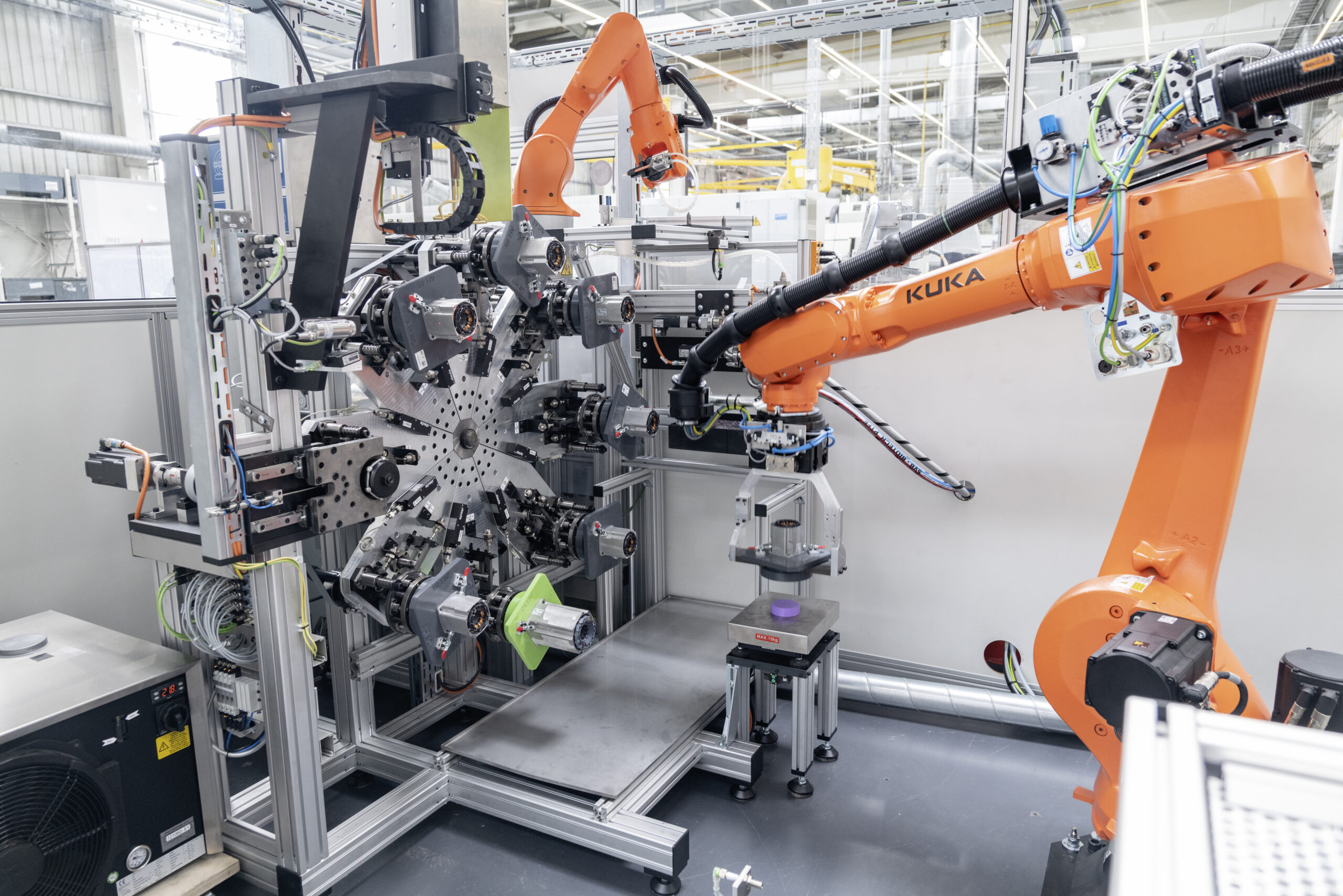
Undergoing a digital transformation creates new paths of opportunity for manufacturers as they strive to tackle labor shortages, rising operational costs, and many other common challenges in the field. When considering other pressures such as rapid technological advancements, accelerating demands for high quality products, and calls for more sustainable processes, the industry has begun to move towards a digital renaissance.
With both expectations and challenges rising, businesses are embracing new methods to cut costs, enhance production lines, and make operations more sustainable. Many manufacturers have reaped the benefits of integrating their information technology and operational technology capabilities through a process called IT/OT convergence. By implementing IT/OT convergence, factories can identify challenges on the shop floor using data from machines and processes to deploy operational solutions and address problems.
Joining the “brain” and the “body”
IT/OT convergence can ensure that manufacturing operations and systems are transparent and unified, enhancing the ability to make informed decisions while increasing access to data across the organization. In most factories, however, IT and OT systems are siloed; as well, teams that work with each respective system have different skill sets and training. IT systems oversee the company’s information stores while OT systems encompass all the hardware and software that monitor physical devices and processes. In essence, uniting these systems connects the “brain” with the “body”.
Once an enterprise can facilitate seamless communication between departments through interconnected systems, it becomes easier to augment operations and reduce operational costs. This connectivity helps manufacturers gain comprehensive insights into their operations, allowing them to perform predictive maintenance and monitor processes and machines in real-time.
Setting the example
The perks of consolidating IT and OT technologies are not aspirational; Siemens electric motor factory in Bad Neustadt, Germany, successfully actualized the rewards of IT/OT convergence, solidifying itself as a role model. Through investing and committing to IT/OT integration, Bad Neustadt gave their teams more control of machine and process data, helping the factory bolster productivity while becoming more competitive.
By putting IT and OT data to work, Bad Neustadt was able to get the most out of their machines. Now, the factory could better identify inefficient machines that needed to be replaced and even predict which machines would need maintenance before they failed. Additionally, the factory could use data insights from those machines to thoroughly supervise energy consumption. More tangible benefits Bad Neustadt saw include:
- Process improvement through more transparent master data
- Lower carbon footprint and reduced energy costs
- Automation of time-intensive tasks
- Optimized testing processes
Tackling unique challenges
While IT/OT convergence helps manufacturers keep up with rising costs and achieve sustainability goals, there are a few challenges organizations need to look out for during their integration journeys. Widescale implementation of new technologies requires commitment from the top down. To ensure that employees are ready for the shift, leadership must thoughtfully approach implementation efforts and demonstrate dedication to its success beyond just the first stages.
From there, it’s crucial that the respective IT and OT teams are properly prepared and trained for the process shift. Workers being unable to acclimate to technological and operational changes could hinder IT/OT convergence. To overcome this, the IT and OT teams must be primed to learn to work together so that the business can take full advantage of their expertise.
Outside of implementation hiccups, IT/OT convergence increases the risk of exposure to cyber threats. In general, digitalization creates more complex ecosystems, prompting attackers to exploit their weaknesses. Safeguarding vital industrial systems requires building a unified workforce and having transparent operations so that cybersecurity can be both managed and enhanced.
Collaborating is key
When all is said and done, facilitating collaboration—whether it be between systems, machines, processes, or people—is pivotal to actualizing the benefits of IT/OT convergence and side-stepping its potential pitfalls. With people from each team working together, organizations can productively leverage their operational data; however, this will require both comprehensive training and support from upper leadership.
Dedicating time to realizing IT/OT convergence will help factories stay competitive as challenges such as labor shortages and supply chain disruptions intensify. By successfully unifying IT and OT systems, manufacturers can create data-driven environments that support better decision-making and operational efficiency. Overall, this leads towards creating smarter factories, bolstering sustainable operations, and ultimately revolutionizing the manufacturing landscape.
Siemens Digital Industries Software helps organizations of all sizes digitally transform using software, hardware and services from the Siemens Xcelerator business platform. Siemens’ software and the comprehensive digital twin enable companies to optimize their design, engineering and manufacturing processes to turn today’s ideas into the sustainable products of the future. From chips to entire systems, from product to process, across all industries. Siemens Digital Industries Software – Accelerating transformation.