Bridging the skills gap in manufacturing through reskilling, upskilling and educating
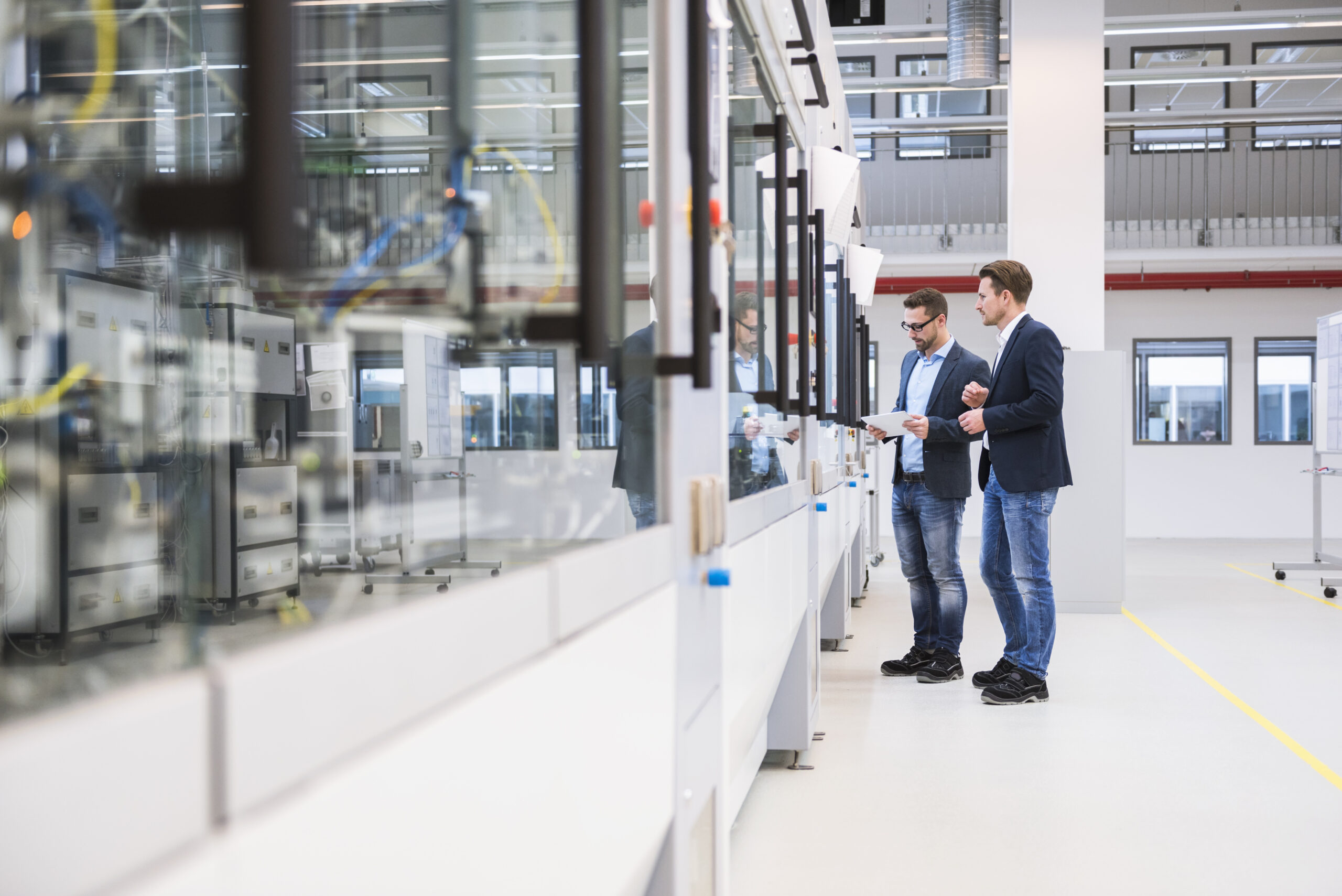
The manufacturing industry is in a constant state of change, bringing both opportunities and challenges. Between an aging workforce, ongoing supply chain disruptions, and the constant push for innovation, companies face a widening gap between current skills and new job demands. Addressing this gap calls for a focused approach on reskilling, upskilling, and education to equip both current and future workers for evolving landscape of manufacturing.
Shifting dynamics in manufacturing
Supply chain instabilities and technological innovation are two major forces shaping the current talent gap in manufacturing. The pandemic exposed the vulnerability of global supply chains, prompting many manufacturers to reassess their strategies. Some have opted to bring operations closer to home by nearshoring, while others are diversifying through offshoring operations. Both approaches, while stabilizing supply chains, create challenges in ensuring the workforce has the necessary skills for these modernized operations.
In addition to these supply chain concerns, the pace of technological advancement has left many workers wanting to learn how to operate new technologies. Automation, artificial intelligence (AI), and advanced manufacturing technologies are revolutionizing the shop floor, but they also require specialized skills that aren’t widely available in today’s workforce. This creates a growing demand for workers who are equipped with the capabilities to manage both digital and physical manufacturing processes.
Automation is changing how employees work
Automation and AI are transforming how manufacturing functions. No longer confined to simple, repetitive tasks, workers can now engage with advanced technologies that manage everything from quality checks to process optimization. Hyperautomation, where every aspect of production is automated where possible, is a growing trend that increases efficiency. However, this shift demands that workers acquire new skills, especially around digital processes and data analysis, to remain effective.
As automation continues to rise, companies will need to support their workforce in gaining these competencies. It’s not just about operating machines; it’s about understanding the sophisticated digital ecosystems that drive modern manufacturing.
The critical role of reskilling and upskilling
Manufacturers must prioritize reskilling and upskilling their current employees if they hope to close the skills gap. Reskilling equips workers with the know-how to operate new technologies and automated systems, while upskilling helps employees expand on their existing skill sets. Both are essential in keeping the workforce adaptable in an ever-changing industry.
By investing in continuous learning programs—whether through digital learning platforms or immersive experiences like augmented reality (AR) and virtual reality (VR)—companies can offer workers flexible and interactive opportunities to develop new skills. These technologies allow for hands-on training without disrupting operations, making them ideal for busy manufacturing environments.
Upskilling and reskilling not only empower workers with new capabilities but also enhance their value within the organization. As employees gain proficiency in modern systems, they become better positioned for career advancement, creating a mutually beneficial situation where both the workforce and the organization can thrive.
Building a future-ready workforce
Beyond addressing the needs of today’s workforce, manufacturers must look toward building the workforce of tomorrow. This means actively engaging with educational institutions and STEM programs to foster interest in manufacturing careers among younger generations. By supporting internships, apprenticeships, and practical learning experiences, companies can give students the chance to explore advanced technologies and understand the potential of a future in the industry.
Credentialing programs, in partnership with educational institutions, are also critical. By offering industry-recognized certifications in areas such as AI, smart manufacturing, and digital tools, manufacturers can create clear pathways for workers—both current and future—to gain valuable skills without needing a traditional degree. These credentials ensure that employees stay competitive while giving companies confidence that their workforce can handle emerging technologies.
The ongoing commitment to people
Ultimately, the skills gap in manufacturing isn’t a problem that can be solved overnight. It’s a human challenge that demands long-term investment and collaboration. By focusing on reskilling, upskilling, and education, manufacturers can build a resilient workforce equipped to meet the demands of today and tomorrow.
As the industry continues to transform, so must its workforce. Through a combined effort of embracing digital technologies and supporting worker development, manufacturers can not only close the talent gap but also ensure their employees are prepared to thrive. In the end, this investment in people is what will allow the industry to succeed in the long term.
For more information about reskilling and upskilling in manufacturing, listen to our Digital Transformation Podcast, where industry experts explore in depth how organizations can empower their people.