Defining sustainable battery innovation from production to recycling
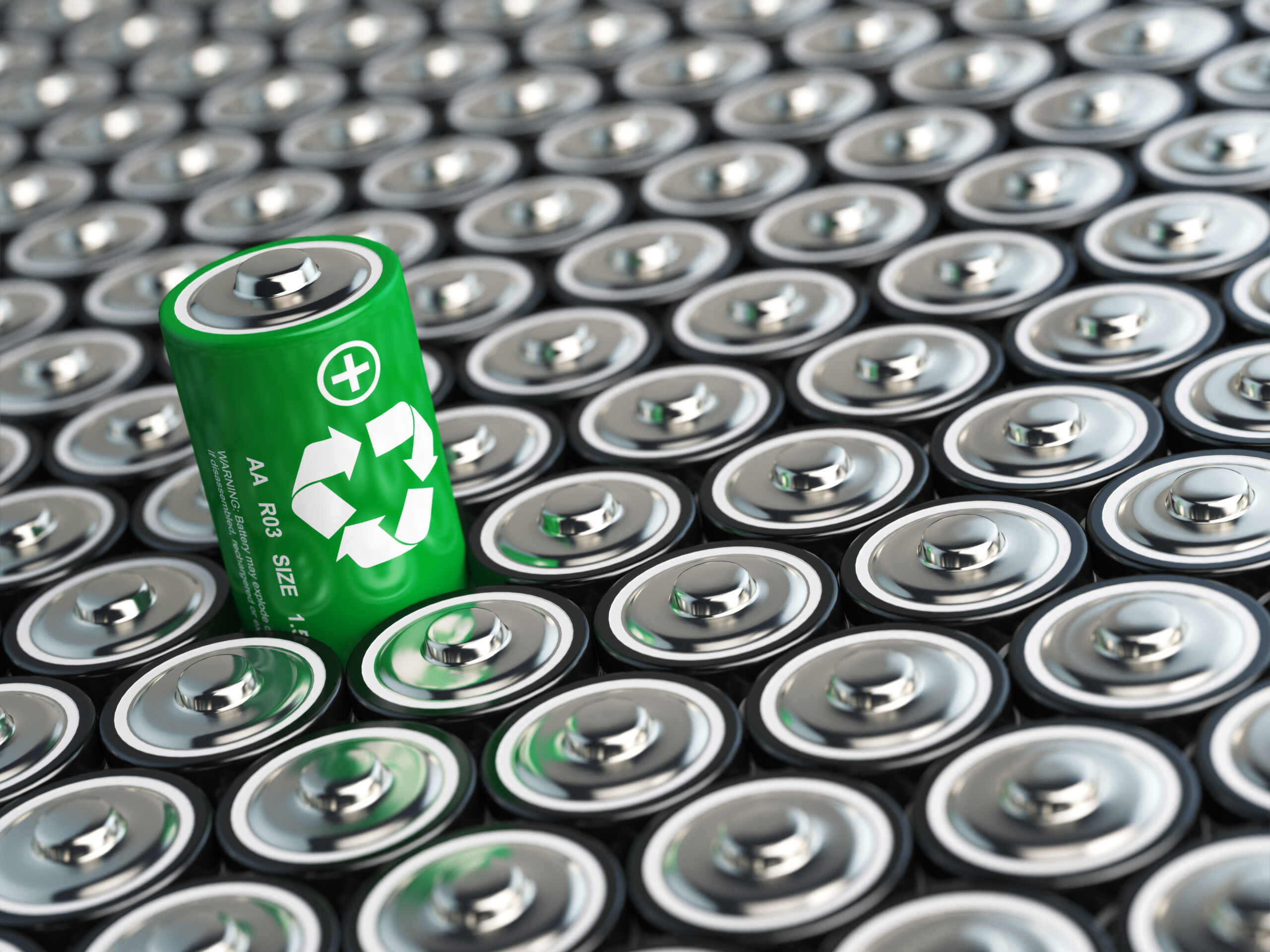
Electrification as an industry trend is at a high-level about decarbonizing our existing ways of doing things by removing fossil fuels as the dominant energy storage medium. That goal has accelerated development of battery technology, among other drivers. Unfortunately, batteries are not the silver bullet to all forms of electrification – sometimes for technology and physical limitations, other times for sustainability concerns. To answer the question of how to make batteries more sustainable, Puneet Sinha and I sat down with Magnus Edholm of Siemens Digital Industries to continue our conversation on the industry:
But for anyone without the time to listen in on the full second half of our conversation from the Battery Podcast, let’s go through the highlights. And you can catch part one here if you missed it.
To start of our conversation, I asked Puneet how companies can pursue improvements in energy density, battery longevity, reliability, and cost while making batteries more sustainable, because they are a very intensive product. It takes 30 to 40 units of energy to produce a battery with one unit of capacity today. That makes battery production itself a candidate for decarbonization, not just a mean to do so in other industries. The energy for a gigafactory is not likely all from renewable resources, some amount of the grid capacity will have come from fossil fuel-based power plants. Understanding this is important while discussing vehicle emissions for example – the tailpipe emissions of an electric vehicle are negligible, but the production emissions are often much higher than those for internal combustion engine vehicles.
Making battery production more energy-efficient helps decarbonize the industry and has an associated cost savings for the manufacturer. Operations expenses drop when less power is used per battery. And companies are trying all sorts of things to make production more efficient. One example we showed off in 2023 was a topology optimized robotic gripper for battery pack assembly. By reducing the weight being moved around with an additively manufactured part, the robot was able to move more efficiently during operation. This is only one, highly visual example of progress. Most improvements will come out of holistic optimizations of production and design, few sustainability benefits can flourish while only looking at part of the equation for development. The next improvement might come from a chemistry optimization and improved cooling performance, or a mechanical breakthrough that relies on new manufacturing techniques.
Improve and track
Improving the sustainability of batteries is great, but manufacturing is not isolated from the material supply chain or the wider product ecosystem. The improvements made need to be tracked, shared, and improved upon at a much larger scale for the industry to get to its best. That means tracking the associated emissions and environmental impacts of the raw materials being used in production and providing provenance information to customers on how their battery was manufactured, where, and how they might go about returning it to the material stream through reuse, remanufacturing, or recycling.
This is maybe, the biggest hurdle for battery manufacturers and users to clear in making the industry more sustainable. Only 5 percent of batteries are recycled today. And in the next few years, the first cars to hit the road in droves (around 2010) will be ready to replace their batteries. We, and I do mean that collectively, need to be able to either find new applications for these batteries for grid storage or create better paths for those batteries to be disassembled and reused for new batteries. This is where the proposed battery passport regulations come into play.
Not a solo challenge
Making these changes to the battery industry, from production to recycling is not intended to be an individual goal. Working alongside other battery manufacturers and supplier to decarbonize the industry will make the product a more appealing option in more applications. And finding the path to that solution may also require talking with experts and trusted technology partners like Siemens to figure out what has already been learned, how to learn faster, and how to transition into the digital age as we talked about in the first part of our conversation with Magnus.
But if you are looking to learn more today, there is still plenty I could not cover from our discussion with Magnus. You may also want to check out our website siemens.com/battery or listen to any of our other episodes with experts on the Battery Podcast.
Siemens Digital Industries (DI) is a leading innovator in automation and digitalization. In close cooperation with its partners and customers, DI is the driving force for the digital transformation in the process and manufacturing industries. With its Digital Enterprise portfolio, Siemens provides companies of all sizes with all the necessary products, along with consistent solutions and services for the integration and digitalization of the entire value chain. Optimized for the specific requirements of individual industries, this unique portfolio enables customers to enhance their productivity and flexibility. DI continuously extends its portfolio to include innovations and the integration of future-oriented technologies. Siemens Digital Industries, with its headquarters in Nuremberg, has a workforce of around 72,000 people worldwide.
For more information on Siemens Digital Industries products and services, follow us on LinkedIn, Facebook, Twitter, and YouTube.