Integrate automation with cobots
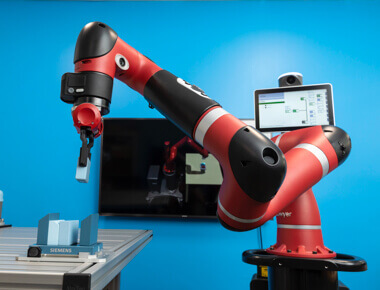
Over the last decade, industrial manufacturing has seen a wealth of advancements in innovative technologies that optimize factory operations while combating challenges such as escalating operational costs and labor shortages. While many organizations are taking full advantage of these breakthroughs and reaping the benefits, many aren’t seeing a straightforward path to digitalization.
During an episode about advancements in robotics on our Digital Transformation podcast series, Siemens experts Rahul Garg, Vice President for industrial machinery vertical software strategy at Siemens Digital Industries software, and Maximillian Metzner, leader of the module autonomous manufacturing systems for the plant network in Siemens Digital Industries, spoke on how factories can start implementing robots to increase flexibility and improve efficiency all while addressing labor shortages.
Modernizing operations may initially seem intimidating, but through integrating AI and leveraging the digital twin, even brownfields can see impressive gains without much interruption to their existing processes. With the power of the digital twin and AI, implementing advanced robots is an advantageous venture.
The benefits of cobots
Doing things the way they’re always done is no longer enough to manage rising operational costs, production process inefficiencies, and a tight labor market. Manufacturers must ameliorate their existing production environments to stay profitable and competitive; and contrary to popular belief, modernization does not necessarily involve replacing old equipment with shiny, new machines.
Many factories have seen ROI from integrating collaborative robots (cobots), or robots that aid human workers during production. Cobots enable seamless integration between automated and manual systems, even in factories where fully automated systems aren’t feasible, particularly those that rely heavily on manual labor. Using cobots, brownfields can:
- Improve the flexibility and adaptability of their production processes
- Reduce the need for human labor
- Increase operational efficiency and ultimately lower costs
Almost too obviously, achieving a more automated factory starts with a plan. With a solid plan, cobots and other automation features can be more easily incorporated into production lines. To guarantee successful integration of cobots, manufacturers should look to the digital twin.
Simulating success
It is crucial to also test how and where certain processes will work before integrating new machines and processes into brownfield. Utilizing the digital twin for virtual commissioning will provide accurate planning and simulation, reducing errors during implementation.
Virtual commissioning and robot offline programming can significantly reduce the time and effort required to integrate automation systems into existing production environments. Because testing is done virtually, trial runs of potential new systems are cheap and sustainable, especially compared to physical prototypes. On top of that, simulated verification can be completed sometimes within days, making it possible to have more optimized and flexible systems very quickly.
The future of robots
With automated systems completely integrated, factories can begin to implement AI to further their automation capabilities. Recent advancements in AI enable it to complete tasks that were once completely manual. These days, AI can help locate and identify parts as well as determine how the robot should handle them, without the need for programming.
Implementing AI along with cobots and the digital twin can help move your factory into the future. Cobots work as a conduit between manual and automated operations and can be easily introduced into a brownfield environment. Utilizing the simulation capabilities of the digital twin makes cobot integration seamless and hassle-free, enabling a wide range of resource-conserving testing capabilities.
To learn more about increasing your factory’s automation capabilities using cobots, AI, and the digital twin, be sure to check out our podcast in which our experts detail how brownfields can begin on their digital transformation journeys.
Siemens Digital Industries Software helps organizations of all sizes digitally transform using software, hardware and services from the Siemens Xcelerator business platform. Siemens’ software and the comprehensive digital twin enable companies to optimize their design, engineering and manufacturing processes to turn today’s ideas into the sustainable products of the future. From chips to entire systems, from product to process, across all industries. Siemens Digital Industries Software – Accelerating transformation.