Embracing IT/OT convergence for manufacturing innovation
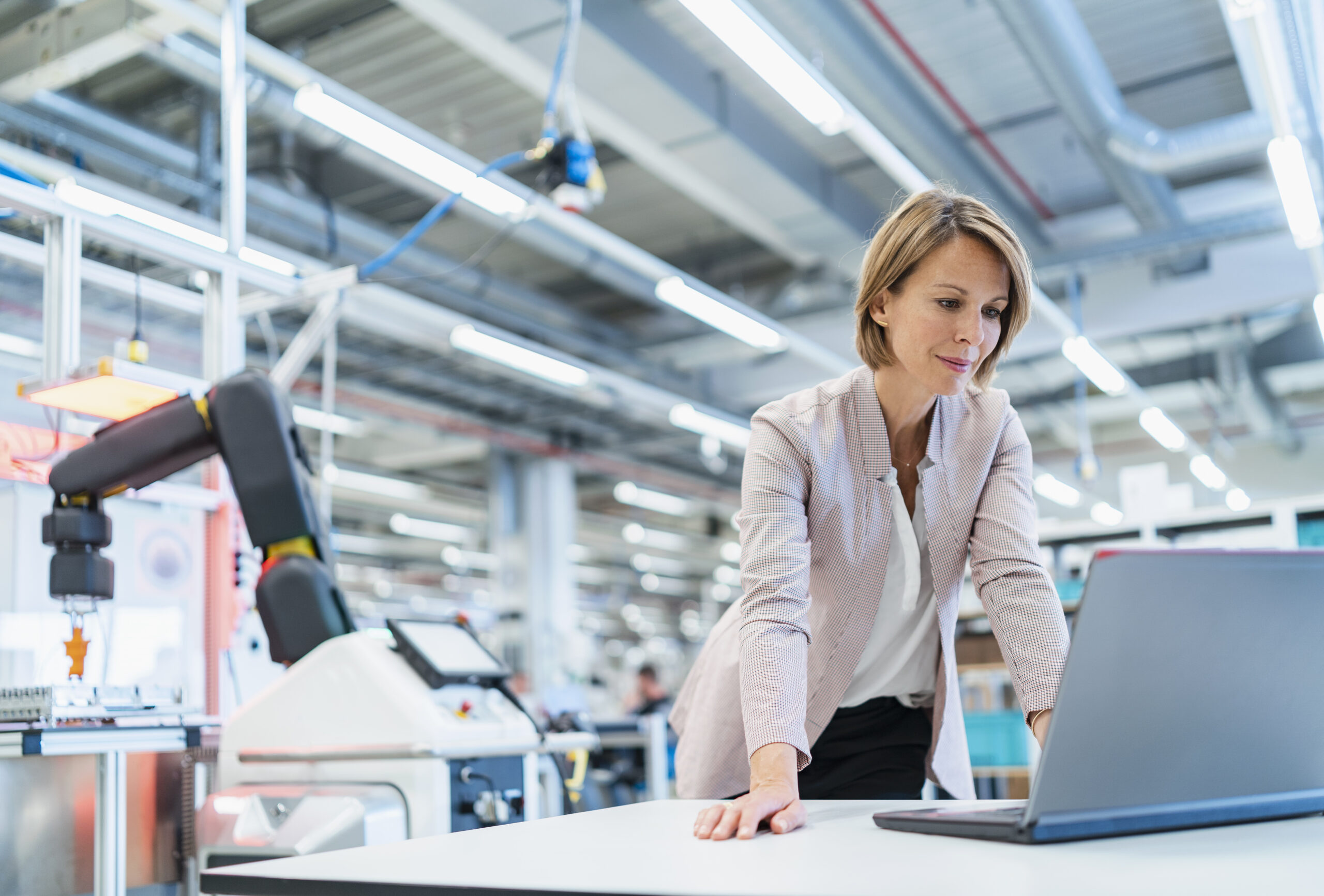
For decades, manufacturing has had to evolve to accommodate a myriad of challenges like labor shortages and supply chain disruptions. Today, these hurdles have only intensified, compounded by the rapid advancements in technology and the increasing demand for faster, superior products that are manufactured with more sustainable processes. With these added pressures, it seems that the industry now stands at a crossroad: either embrace digitalization to innovate and overcome or neglect transformation and risk falling behind in this ever-changing environment.
In a recent podcast episode, experts Rahul Garg, VP of Industrial Machinery and the SMB program at Siemens Digital Industries Software and Peter Zech Head of Innovation and Digitalization at Siemens’ Bad Neustadt factory, met to discuss one critical way OEMs can embrace digital transformation—IT/OT convergence. In this blog, we’ll reveal insights from their conversation, sharing the challenges, benefits and real-world applications of IT/OT integration.
Why is IT/OT convergence important?
IT/OT convergence refers to the integration of IT systems, which handle data-centric computing, with OT systems, which manage industrial operations. The primary goal is to create a unified and transparent system that enhances data accessibility and improves decision-making across an organization.
So why is this important for manufacturers? Well, one of the main drivers for IT/OT convergence is the need to augment operations by increasing productivity. By adopting IT/OT convergence, manufacturers can gain comprehensive insights into their operations, enabling better performance management, quality control and most importantly, they can ultimately become data-driven organizations.
First the benefits
While IT/OT convergence sounds great in theory, it can be difficult to know where to begin, when to start and what challenges could be encountered along the way. Luckily, Siemens electric motor factory in Bad Neustadt, Germany, serves as a blueprint of the and benefits and challenges of implementing IT/OT convergence.
The factory began their integration journey with a clear focus on improving factory competitiveness and productivity. Initially the factory team built an IT/OT ecosystem capable of addressing use cases from a use case repository covering everything from performance management to sustainability. This required a significant investment in technology and a commitment from management to empower both the team implementing use cases and the end users on the shop floor, ensuring that the factory is strategically gathering and using data to drive productivity.
Here are some ways the use case driven IT OT integration strategy has actively enhanced operations at the Bad Neustadt factory:
- Improved machine utilization: By connecting machines and utilizing both IT and OT data, the factory was able to recognize inefficiencies in machines, allowing them to confidently scrap older, less efficient machines, saving a substantial amount in would-be maintenance costs.
- Transparent energy management. At Bad Neustadt, the factory has been able to generate energy transparency and by implementing data-driven measures to reduce energy usage. This transparency coupled with additional measures like hibernation, weekend shutdowns and more efficient components have been key to significantly reducing the energy consumption of the factory’s production, further exemplifying the power of IT/OT integration.
- Predictive maintenance: By analyzing IT OT system data, the factory can predict machinery failures and perform proactive maintenance. Not only does this approach reduce downtime and minimize the impact on production schedules, but it also leads to smoother operations and increased productivity.
And then the challenges
As much as Bad Neustadt enjoys discussing the advantages they have gained from IT OT integration, there are a few challenges that cannot be overlooked. Organizations looking to undergo IT/OT convergence must learn to navigate these hurdles:
- Building an ecosystem: Creating an integrated IT/OT ecosystem requires substantial effort and investment. Organizations need to build competencies, apply the right technologies and secure commitment from upper leadership. This process is time-consuming and requires a well-thought approach to ensure that the ecosystem can support various use cases beyond initial implementation.
- Creating a unified workforce: Successful IT/OT convergence is not just about technology; it also involves empowering both IT and OT workers. Cultural barriers between workers often hinder the effectiveness of convergence. To overcome this, both training and a mindset shift are essential. This will enable IT and OT to work together and share expertise in their respective fields so that the factory can leverage data insights to optimize processes.
- Addressing cybersecurity: As IT and OT systems converge, cybersecurity becomes a critical concern as integrated systems can be vulnerable if not properly managed. This is where having a unified workforce becomes necessary. With IT OT integration, workers can improve the flow of information and bring real-time insights to issues. By implementing necessary tools and having transparent operations cybersecurity can not only be managed but improved.
The key to competitiveness
Without a doubt, IT/OT convergence is a necessary step for manufacturers looking to stay competitive. By integrating OT and IT technologies, companies can create data driven environments that support better decision-making and operational efficiency. However, this journey and transformation does not happen overnight. Building a supportive ecosystem and breaking down traditional barriers between OT and IT workers is a lengthy process that involves strategy and patience. But as more factories like Bad Neustadt embrace this transformation, the industrial landscape will continue to evolve as the technological landscape advances.
For more IT/OT convergence insights listen to the podcast above or click here.
Siemens Digital Industries Software helps organizations of all sizes digitally transform using software, hardware and services from the Siemens Xcelerator business platform. Siemens’ software and the comprehensive digital twin enable companies to optimize their design, engineering and manufacturing processes to turn today’s ideas into the sustainable products of the future. From chips to entire systems, from product to process, across all industries. Siemens Digital Industries Software – Accelerating transformation.