The future of smart machines and smart industries – ep. 1
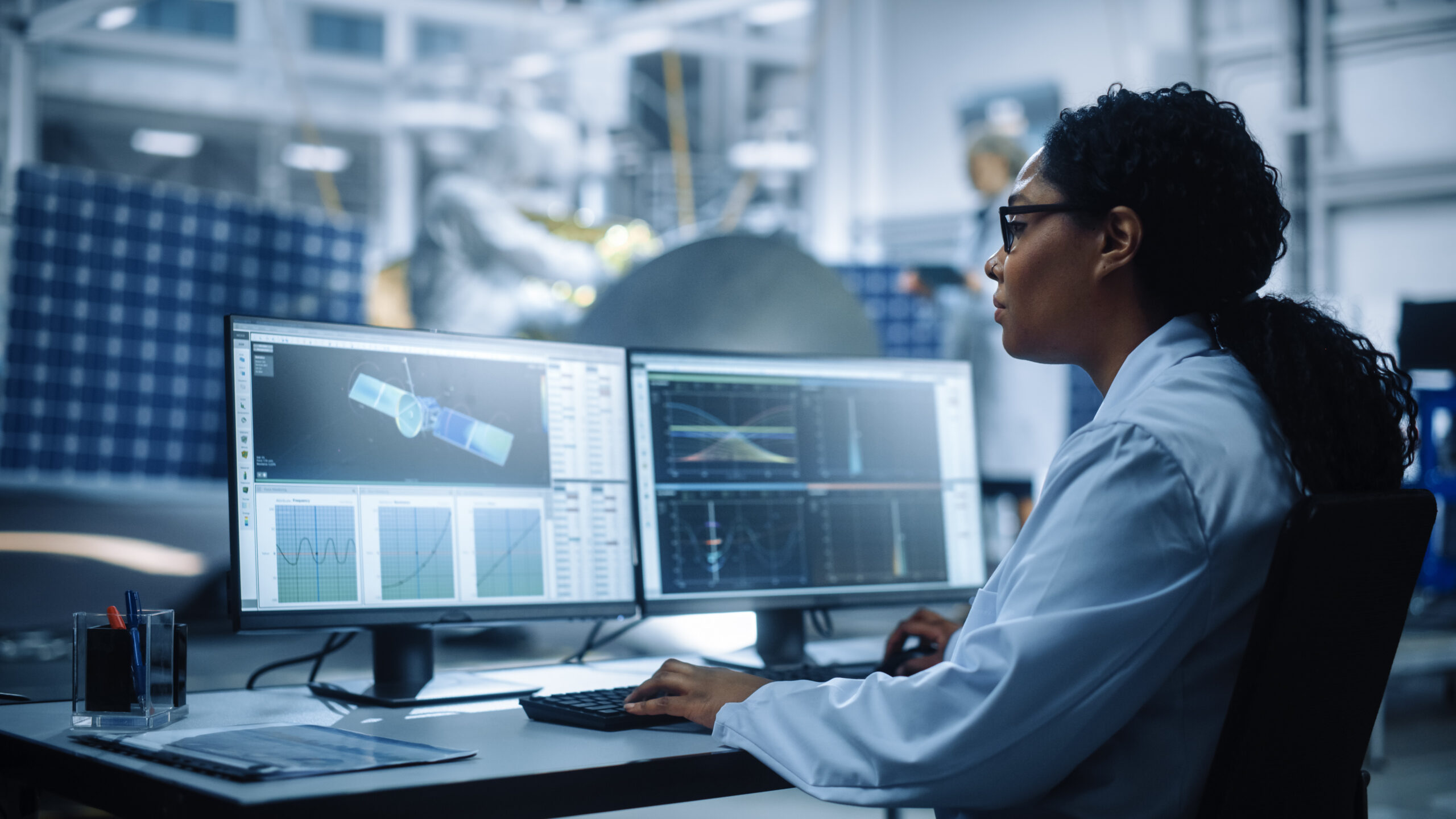
Innovative technologies challenge machine builders daily, spurring them to consider which innovations will have the most significant impact on the market.
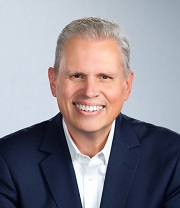
Our engineering experts, Dale Tutt, VP of Industry Strategy; Rahul Garg, VP of Industrial Machinery; and Michael Thomas, SVP of Factory Automation and Head of Production Machines, discuss the trends and challenges in the manufacturing ecosystem today, including technological advances on the horizon, and the role of digitalization in enabling the future of smart manufacturing.
When manufacturers evaluate machine building and manufacturing for efficiency, cost, and time to market, the process must be reduced to individualization of products and quality. Therefore, it’s no surprise that consumers’ current product buying behavior is putting a significant stake in sustainability.
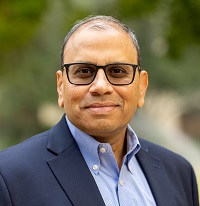
Emerging technologies for new markets in sustainability
Conversely, the landscape of machine builders shows a considerable need for more talent in most countries, both for the companies building machines and for the end customers in manufacturing operations. This situation leads to a challenging endeavor as technologies rapidly advance and change.
Emerging new markets of immobility in sustainability are on the horizon. For example, consider the plastics industry’s substitution of materials. Unfortunately, the number of people who can deal with these challenges is becoming rarer and more limited. As a result, several trends and challenges are manifesting for factories and machine builders, changing the future approach for manufacturers.
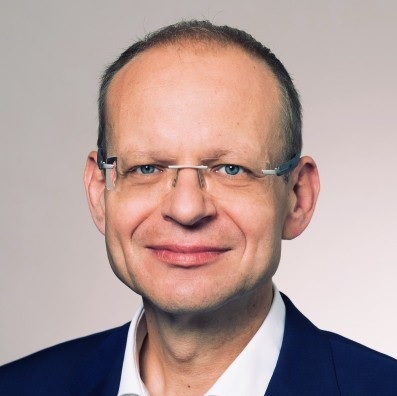
Indeed, workforce challenges are also a significant challenge for our customers. These large manufacturer OEMs and their suppliers attempt to produce products faster, improving yield with less scrap and waste in their production lines. In the current landscape, they must be more flexible so that they can be responsive to the changing demands of their customers.
As these workforce challenges continue, it is crucial to simplify the personnel systems on the shop floor, introducing technologies that make it easier to get online and up and running quickly, possessing a modern look and feel of the entire process and user interface, which is a crucial function to drive greater adoption with the workforce.
Introducing more automation and robotics in the production process
For instance, many companies historically relied on manual labor and struggled with a shortage of technicians. Now they desire to increase automation to help overcome labor shortages. This automation is not merely in their production but in their workflows. Therefore, delivering more information to people on the shop floor requires greater automation, processes, and production.
Most of these challenges correspond to sustainability-related issues in reducing a machine’s energy consumption. Thus, introducing more automation and robotics into the production processes which requires improving operational efficiencies and automation.
A common thread in various industries is immense growth and complexity in companies’ operations. They are changing how they do business and developing the next generation of products. Then, they manufacture those products, affecting many productions processes.
Increasing complexity and customer demand creates a volatile market
Furthermore, complexity affects how factories are managed. They are moving from automated production to adaptive and flexible production facilities, with many automated optimization elements influencing machines. Evaluating machine performance via virtual commissioning before building a prototype is becoming the norm.
Complexity and highly demanding end-customer markets create a volatile market environment with much uncertainty about when to invest. Evaluation is required to lower the risk and become more predictable in the planning and design process and facilities operations.
Factory machines are another significant element, as complexity affects how industrial machinery is designed. There is a desire is to deliver on customer expectations for smart or adaptive manufacturing, to provide equipment that needs to transform the design and engineering process, and to build manufacturing and support processes.
Manufacturers are moving from what was traditionally a sequential process to a more integrated mechatronic-based process where all the multidiscipline engineering activities happen cohesively, with the mechanical, electrical, and automation design processes working continually. This process creates a digital twin of the entire machine, leveraging simulation, and enables the machine buyer, the factory, and the user to evaluate the machine’s overall performance.
Leveraging new technologies to transform internal operations
Therefore, before the commissioning phase, they can evaluate how the machine will work in context with the entire line, making any adjustments virtually before actually cutting a single piece of metal and continuing through the commissioning process.
As a result, this first helps to ensure that what they deliver will meet the customer’s needs. Secondly, it gets it to the customer site quickly, without having any downtime or site operational issues, and from a functional perspective, it can monitor what’s occurring to make any adaptive changes to the equipment.
Consequently, if there are any issues, you can proactively predict potential problems and resolve them before they become more significant. So, these are elements that machine builders want to incorporate into their operational processes to leverage new technologies and capabilities and transform their internal operations.
Additionally, many machine builders are forced to move into new domains, leaving established ones. Thus, when transforming a company like a mid-sized machine builder, they consciously consider the domain’s value and the potential of new areas to enter. In this scenario, the best option is to minimize the risk by quickly adapting to new places they are capable of and educating their people.
During this transformational journey, companies that can adapt to new technologies and utilize the portfolio and the technology available are the most successful ones. So, more and more industry segments are already either in this transformation process or beginning it.
The printing industry is an excellent example of moving into new technologies regarding packaging print and not merely printed media. Also, there is functional printing; for instance, 3D printing takes it from printing 3D pieces to publishing housing properties, which is occurring in the industry domain. However, this field has needed more technological productivity in the last 100 years. Therefore, we are witnessing adjacent new markets because of combining innovations and core automation connected to IT, utilizing AI technologies.
Learn more in the podcast.
Siemens Digital Industries Software helps organizations of all sizes digitally transform using software, hardware and services from the Siemens Xcelerator business platform. Siemens’ software and the comprehensive digital twin enable companies to optimize their design, engineering and manufacturing processes to turn today’s ideas into the sustainable products of the future. From chips to entire systems, from product to process, across all industries. Siemens Digital Industries Software – Accelerating transformation.