PLM in the cloud providing benefits for small to medium-sized companies
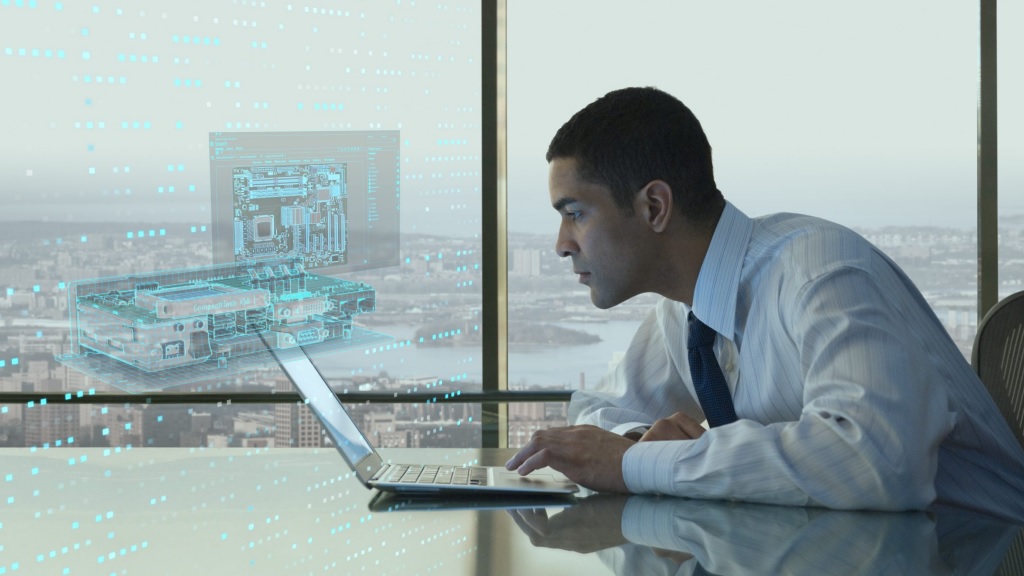
In revisiting our final podcast of the PLM Teamcenter X solution series, we focus on the impact of cloud and PLM on small to medium-sized businesses. We address how the product development process of PLM for the cloud is changing, triggering a structural effect on business operations.
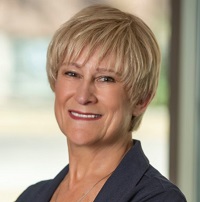
We are privileged to welcome our engineering experts: Mary MacDonald, Global Industry Marketing Leader for small and medium business at Siemens Digital Industries Software, who will interview Tim Yerby, Solution Director for Industrial Machinery at Siemens Digital Industries Software, about the obstacles and benefits of PLM for Components in the cloud for manufacturers.
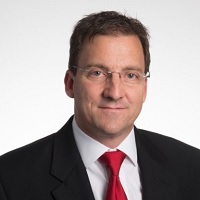
In the last few years, we have witnessed software rapidly improving with more and more capabilities. With these advancements and improvements, there’s always the issue of IT departments, especially in small to medium-sized companies, requiring resources to implement and maintain systems. Larger companies have organizations that support or manage their CAD or PLM system, but smaller to medium-sized companies need the staff or financial structure to address new issues.
The challenge for manufacturers in a rapidly changing landscape
The challenge is finding the right resources to implement and maintain these systems. Indeed, this can be addressed with cloud availability of systems or packaged software with a standard solution that may or may not be customized. If customization is necessary, it’s performed by the users or the department manager; thus, there is no need for IT staff.
Therefore, the first step with cloud and Software-as-a-Service (SaaS) is knowing what works with your current system and CAD data—furthermore, if that data remains the same, you don’t want to change the CAD system to transition to PLM.
So, it’s essential to know whether it will utilize and manage it with the new PLM system and the technical capability to address change management, including the engineering change process. The primary purpose of PLM is to ensure that the organization can use the CAD and bill of material (BOM) data, including the ERP, MRP, and manufacturing system.
The goals of PLM for component manufacturers
A goal of PLM for component manufacturers is to avoid a change in someone’s job function. Conversely, the goal is to remove daily manufacturing barriers and create an efficient process.
Indeed, project timelines are tight in the release process, and if you’re a gear motor manufacturer, a client may need a custom design. However, 80 percent of the bill of materials will be reused. Thus, only 20 percent require customization. However, the manufacturing organization requires delivering the entire BOM, so you must hold off on the 80 percent reuse until the 20 percent is modified for customization, which, unfortunately, is inefficient with tight deadlines.
Agile PLM system for customization
So, an organization’s supply chain needs process and data management that allows the release of 80 percent of the BOM that remains unchanged. Unfortunately, this hybrid release process can cause organizational issues if it’s not an agile PLM system that addresses what is changed/not changed and released/not released – thus requiring managing rolling releases.
“Teamcenter is the gold standard in the industry with respect to PLM management. So, one of the big advantages I see for small to medium businesses is providing this type of technology that may have been previously only available to large enterprises that could afford and support it, or because they needed a large services engagement or customization work to set up for their process. Siemens has now created this type of an industry-standard process,” says Tim Yerby
Therefore, this process helps most customers out of the box, with minimal customization. A significant advantage is that consulting or service costs are lower. As an added benefit, this software engagement can start small, even in just one department. So, it’s not an all-or-nothing investment.
PLM can start with minimal cost
It’s possible to sign up with a specific number of users with a monthly fee, add users along the way, and roll it out across an organization. Indeed, you can build additional modules and continue to grow your organization. Or, if you decide not to use it, turn it off and quit paying. Subsequently, companies can start quickly with low commitment costs and a monthly subscription cost.
“If it saves your team hours of work, then you can go ahead and agree it is working great, then you need to expand it,” says Tim.
PLM for component manufacturers introduces new opportunities to address the daily challenges of small to medium businesses, providing technology and introducing SaaS solutions for substantial innovation.
Siemens Digital Industries Software helps organizations of all sizes digitally transform using software, hardware and services from the Siemens Xcelerator business platform. Siemens’ software and the comprehensive digital twin enable companies to optimize their design, engineering and manufacturing processes to turn today’s ideas into the sustainable products of the future. From chips to entire systems, from product to process, across all industries. Siemens Digital Industries Software – Accelerating transformation.